Aluminiumgussformen spielen eine entscheidende Rolle im Prozess des Aluminiumgusses. Sie werden verwendet, um geschmolzenes Aluminium zu den gewünschten Objekten oder Komponenten zu formen und zu gestalten. Diese Formen werden in der Regel aus Stahl oder anderen Materialien hergestellt, die hohen Temperaturen und Druck standhalten können.
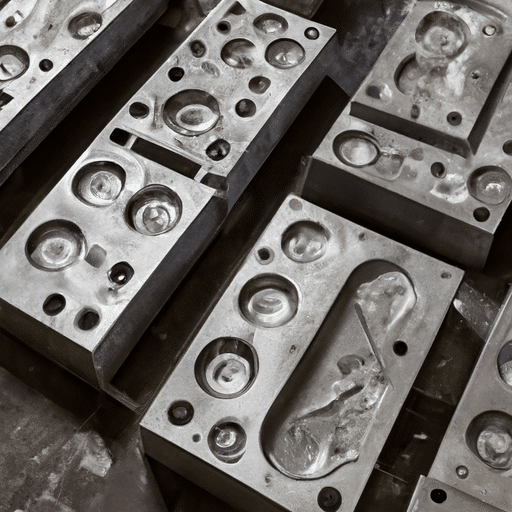
Arten von Aluminium-Gussformen
Es gibt verschiedene Arten von Aluminiumgießformen, die jeweils für bestimmte Gießverfahren und Anwendungen ausgelegt sind. Sehen wir uns einige der gängigen Typen an:
1. Dauerhafte Schimmelpilze
Dauerformen, auch Metallformen genannt, werden aus Stahl oder Eisen hergestellt und sind für den wiederholten Einsatz konzipiert. Sie werden in der Regel für die Großserienproduktion von Aluminiumteilen verwendet. Die Formen haben Hohlräume, die präzise bearbeitet werden, um die gewünschte Form des Endprodukts zu erzeugen. Kokillen bieten eine gute Maßhaltigkeit und Oberflächengüte.
2. Sand-Formen
Sandformen werden hergestellt, indem ein Gemisch aus Sand und einem Bindemittel um ein Muster gepackt wird, das die gewünschte Form des Endprodukts darstellt. Das Modell wird dann entfernt, wobei ein Hohlraum in der Sandform zurückbleibt. Geschmolzenes Aluminium wird in die Form gegossen, füllt den Hohlraum und nimmt die Form des Modells an. Sandformen werden in der Regel für kleine bis mittlere Produktionsmengen verwendet und ermöglichen im Vergleich zu Dauerformen komplexere Formen.
3. Druckgußformen
Druckgussformen, auch Kokillen genannt, werden aus Stahl hergestellt und im Druckgussverfahren verwendet. Beim Druckguss wird geschmolzenes Aluminium mit hohem Druck in die Form gespritzt, um den Hohlraum schnell zu füllen. Dies führt zu hohen Produktionsraten und ausgezeichneter Maßgenauigkeit. Druckgussformen sind in der Regel teurer in der Herstellung, bieten aber eine hervorragende Oberflächengüte und enge Toleranzen.
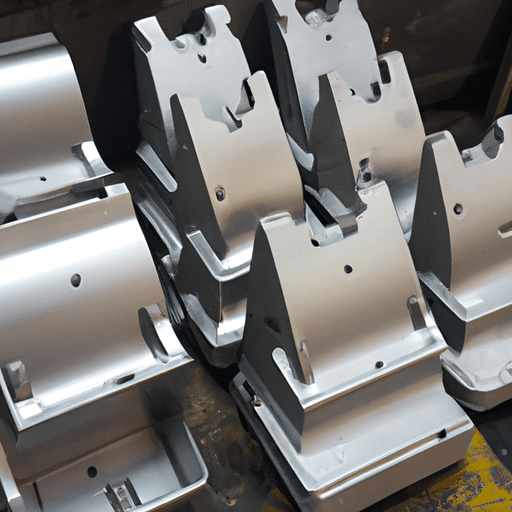
Detaillierte Einführung der Aluminium-Druckgussform
Hauptbestandteile einer Aluminium-Druckgussform
Druckgussformen aus Aluminium sind Instrumente, die bei der Herstellung von Teilen aus Aluminiumdruckgusslegierungen verwendet werden. Um die Herstellung komplizierter Teile zu erleichtern, bestehen diese Formen oft aus vielen verschiedenen Teilen. Die Hauptelemente von Aluminiumdruckgussformen sind wie folgt:
- Das Fundament der Form: Das Formfundament dient als strukturelles Stützsystem der gesamten Form, das alle anderen Teile trägt. In der Regel besteht es aus robusten Elementen wie Stahl, um die Stabilität und Langlebigkeit der Form zu gewährleisten.
- Bewegliche Form: Die bewegliche Form ist in der Regel am beweglichen Teil der Druckgussmaschine angebracht und ist ein beweglicher Bestandteil der Form. Sie umfasst die Form von Aluminiumkomponenten, die ihre innere Struktur und äußere Oberfläche bilden.
- Feste Form: Die feste Form ist in der Regel am festen Teil der Druckgussmaschine angebracht und ist ein fester Bestandteil der Form. Sie formt die Innenkontur des Metallteils und umfasst dessen innere Struktur.
- Schieber sind bewegliche Formteile, die häufig verwendet werden, um Teilen mit komplizierten Formen zusätzliche Merkmale zu verleihen. Um mehr Vorsprünge oder Rillen in der Form zu erzeugen, können Sie den Schieber in eine bestimmte Richtung verstellen.
- Kerne: Die Komponenten, die zur Schaffung von Hohlräumen oder Löchern in einem Teil verwendet werden, nennt man Kerne. Je nachdem, wie das Bauteil konstruiert ist, können sie dauerhaft oder abnehmbar sein.
- Kühlsystem: Während des Druckgussverfahrens reguliert das Kühlsystem die Temperatur der Form, um zu gewährleisten, dass das Material wie vorgesehen erstarrt. Dazu sind oft zusätzliche Kühlvorrichtungen oder Kühlwasserleitungen erforderlich.
- Anguss- und Angusskanalsystem: Die geschmolzene Aluminiumlegierung wird mit Hilfe des Düsensystems in den Formhohlraum eingespritzt. Die Düse, der Führungskanal und andere spritzgussbezogene Teile bilden das Düsensystem.
- Entlüftungssystem: Die Luft oder das Gas, das beim Füllen der Form mit der Aluminiumlegierung entsteht, wird mit Hilfe des Entlüftungssystems abgesaugt. Auf diese Weise werden Blasen und andere Mängel an den Teilen reduziert.
Die Geometrie, die Größe und andere Spezifikationen des herzustellenden Artikels bestimmen das Design und die Anordnung dieser Komponenten. Komplexe Systeme, Aluminiumdruckgussformen benötigen präzise Konstruktions- und Fertigungsverfahren, um die Herstellung von Druckgussbauteilen aus Aluminiumlegierungen von höchster Qualität zu gewährleisten.
Herstellung von Formen für Aluminiumdruckguss
Das Formen von Aluminiumdruckguss ist ein komplizierter und genauer Prozess, der in der Regel die folgenden Hauptschritte umfasst:
- Entwurf: In der Konstruktionsphase beginnt der Formgebungsprozess. Die Ingenieure müssen die Abmessungen, die Form und die Struktur der Form in Übereinstimmung mit den Spezifikationen für das Endprodukt planen. Dabei müssen unter anderem Variablen wie Entlüftung, Kühlung und Materialfluss berücksichtigt werden.
- Auswahl des Materials: Zur Herstellung von Formen wird häufig hochfester, sehr verschleißfester legierter Stahl verwendet. Die Wahl des Materials hängt von den Komponentenspezifikationen, dem Fertigungsvolumen und der Lebensdauer der Form ab.
- Modul Verarbeitung: Anhand der Konstruktionszeichnungen werden die ausgewählten Materialien mechanisch bearbeitet. Dies kann Erodieren, Bohren, Fräsen, CNC-Bearbeitung und andere Verfahren umfassen, um die zahlreichen Komponenten der Form herzustellen, darunter Schieber, Kernzüge, statische und bewegliche Formen und mehr.
- Bauen Sie die bearbeiteten Module zu einer fertigen Formstruktur zusammen. Um die Präzision und Stabilität der Form zu gewährleisten, ist darauf zu achten, dass jedes Teil genau positioniert und eingepasst ist.
- Wärmebehandlung: Um die Härte und Verschleißfestigkeit der Form zu erhöhen, wird eine Wärmebehandlung durchgeführt. Abschrecken, Anlassen und andere Wärmebehandlungsverfahren werden je nach den Anforderungen des für die Herstellung der Form verwendeten Materials ausgewählt.
- Oberflächenbehandlung: Um die Oberflächenglätte und die Korrosionsbeständigkeit der Form zu verbessern, werden bei einigen kritischen Formteilen Oberflächenbehandlungsverfahren wie Spiegelpolieren und Galvanisieren eingesetzt.
- Verarbeitung von Kühlkanälen: Die Effizienz der Produktion und die Qualität der Aluminiumbauteile werden erhöht, wenn die Temperatur der Form während des gesamten Druckgussprozesses erfolgreich reguliert werden kann.
- Schmierung auftragen: Besprühen Sie die Oberfläche der Form mit Schmiermittel, um die Reibung zu verringern, die Lebensdauer der Form zu verlängern und zu gewährleisten, dass das Material aus der Aluminiumlegierung die Form gleichmäßig ausfüllt.
- Prüfung und Fehlerbehebung: Nach der Installation der Form auf der Druckgießmaschine werden eine Reihe von Tests durchgeführt. Dabei werden die Kühlung, die Absaugung, das Spritzgießen und andere Systeme modifiziert, um zu gewährleisten, dass die Form korrekt funktioniert und Aluminiumteile von höchster Qualität liefert.
Um zu gewährleisten, dass die endgültige Aluminiumdruckgussform die Produktionsanforderungen erfüllt und eine qualitativ hochwertige Bauteilfertigung gewährleistet, sind die oben genannten Verfahren nicht linear und erfordern oft zahlreiche Iterationen und Überarbeitungen.
Vorteile von Aluminium-Gussformen
Die Verwendung von Aluminiumgussformen bietet mehrere Vorteile im Herstellungsprozess:
1. Flexibilität bei der Gestaltung
Aluminiumgussformen ermöglichen die Herstellung komplexer Formen und komplizierter Details, die mit anderen Herstellungsverfahren nur schwer oder nur mit hohem Aufwand zu realisieren sind. Dadurch sind sie für eine Vielzahl von Branchen und Anwendungen geeignet.
2. Kosteneffiziente Produktion
Aluminiumgießformen können für die Großserienproduktion verwendet werden und sind damit eine kostengünstige Option für die Massenproduktion. Die Formen können für effiziente Kühlung und Zykluszeiten ausgelegt werden, was die Produktionskosten weiter senkt.
3. Ausgezeichnete Oberflächengüte
Mit Aluminiumgussformen können Teile mit einer glatten und gleichmäßigen Oberfläche hergestellt werden, so dass keine zusätzlichen Nachbearbeitungsprozesse erforderlich sind. Dies spart sowohl Zeit als auch Geld im Produktionsprozess.
4. Material Vielseitigkeit
Aluminiumgussformen können mit einer Vielzahl von Aluminiumlegierungen verwendet werden, so dass die Hersteller das für ihre spezifische Anwendung am besten geeignete Material auswählen können. Diese Flexibilität gewährleistet, dass das Endprodukt die erforderliche Festigkeit, Haltbarkeit und andere Leistungsanforderungen erfüllt.
Schlussfolgerung
Aluminiumgussformen sind wichtige Werkzeuge im Aluminiumgussverfahren. Ob Kokillen, Sandformen oder Druckgussformen, jeder Typ bietet einzigartige Vorteile und ist für unterschiedliche Produktionsmengen und Anforderungen geeignet. Der Einsatz von Aluminiumgussformen ermöglicht Herstellern die Herstellung komplexer Formen, eine kostengünstige Produktion und die Herstellung von Teilen mit hervorragender Oberflächengüte. Aufgrund ihrer Vielseitigkeit und Effizienz sind Aluminiumgussformen in verschiedenen Branchen nach wie vor eine beliebte Wahl.
Was ist die beste Form für das Gießen von Aluminium?
Die optimale Form für das Gießen von Aluminium wird durch eine Reihe von Parametern bestimmt, wie z. B. die besonderen Anforderungen des Gießprojekts, die Komplexität des Teils, das Produktionsvolumen und die finanziellen Zwänge. Im Folgenden werden einige typische Formen für das Gießen von Aluminium vorgestellt:
Steel Molds:
Advantages: Steel molds are strong, long-lasting, and resistant to high pressure and temperatures. They work well with complicated component geometries and large volume manufacturing.
Cons: Compared to other materials, steel molds typically have a longer manufacturing lead time and may be costly to create.
Cast Iron Molds:
Advantages: Cast iron molds feature superior heat conductivity and are reasonably priced. They work well for production volumes ranging from medium to high.
Cons: It could be difficult to obtain complex component geometries, and they might not be as robust as steel molds.
Graphite Molds:
Advantages: Quick cooling is made possible by the superior heat conductivity of graphite molds. They work well for complex component designs and modest to medium-sized manufacturing runs.
Cons: Graphite molds are prone to wear out over time, particularly with high-volume manufacturing, and are less resilient than steel or cast iron molds.
Sand Molds:
Advantages: Sand molds are economical and appropriate for manufacturing in low to medium quantities. They may be applied to intricate component geometries and are also quite flexible.
Cons: Compared to metal molds, sand molds could not provide the same degree of surface quality and dimensional precision. Usually, they are used in less important applications.
Plaster Molds:
Advantages: Plaster molds are good for small-scale manufacturing and prototyping since they are reasonably priced.
Cons: Their temperature resistance may be limited, and they are not as strong as metal molds.
Investment (Lost Wax) Molds:
Advantages: Investment casting molds can create complex, finely detailed items with a smooth surface. They work well for production volumes ranging from small to medium.
Cons: Compared to other mold types, they might be more costly and time-consuming to make.
The ideal mold selection is determined by the particular needs of the aluminum casting project and is often determined by striking a balance between a number of variables, including cost, production volume, component complexity, and desired quality. Working closely with knowledgeable engineers and mold manufacturers is essential to choose the best mold for the intended use.
What kind of mold is used for aluminum?
When casting aluminum, a variety of mold types are often employed; the selection of one type over another is influenced by several criteria, including the part’s complexity, production volume, economic concerns, and the desired final product quality. The following are a few typical mold kinds for casting aluminum:
1. Molds made of steel:
Steel molds are suited for complicated component geometries and large-volume manufacturing because of their durability and ability to endure high temperatures and pressures.
Benefits include a long lifetime, superior surface polish, and dimensional precision.
Applications: Die casting and permanent mold casting are two common uses for it.
2. Sand Molds:
The process of creating sand molds involves packing sand tightly around a template to create the mold’s interior. They are adaptable for casting a variety of forms and are usually utilized for lower-volume manufacturing.
Benefits include affordability, suitability for intricate forms, and versatility in terms of casting sizes.
Applications: Sand casting is a common process used to produce aluminum castings, particularly bigger pieces.
3. Molds made of graphite:
Graphite molds have strong heat conductivity and are often formed of graphite or a combination of graphite and other materials. Small to medium-sized manufacturing runs are appropriate for them.
Benefits include quick cooling, suitability for complex component designs, and affordability.
Applications: For the casting of more complex and smaller aluminum pieces.
4. Missing Foam Molds:
The process of lost foam casting entails making a foam design that has been covered with refractory material. After that, sand is placed around the foam design, and during casting, molten metal is used to replace the foam.
Benefits include excellent surface quality, less machining needs, and good performance with complicated and near-net-5. 5. shape items.
Applications: Ideal for aluminum castings that call for complex designs and lightweight constructions.
5. Metal or die-casting permanent molds:
Description: Consistent and repeatable aluminum components are produced in large quantities using permanent molds, which are usually composed of steel.
Benefits include rapid production speeds, good dimensional accuracy, and suitability for intricate forms.
Applications: Frequently used in gravity and aluminum die casting procedures.
6. Molds made of ceramic:
Ceramic molds are used for precise casting of complex pieces, and they are constructed from refractory materials.
Benefits include less machining needs, excellent accuracy, and a smooth surface finish.
Applications: Fit for aluminum investment casting.
The particular needs of the casting project will determine the sort of mold to use, and often, a number of considerations may come into play. When choosing the right mold, manufacturers take into account a number of aspects, including the complexity of the item, the volume of production, the cost, and the required quality of the finished aluminum casting.
What is the Mould material for Aluminium casting?
A number of variables, such as the casting procedure, the intended component quality, the volume of production, and economic concerns, influence the choice of mold material for aluminum casting. The following are some typical mold materials for casting aluminum:
Steel:
Aluminum casting is a common use for steel molds, which are often composed of tool steels like H13. They are very durable and resistant to the high pressures and temperatures involved in the casting of aluminum.
Benefits include great heat conductivity, exceptional durability, and suitability for large-scale manufacturing.
Applications: Applied in some sand casting applications as well as die casting and permanent mold casting.
Iron Cast:
Cast iron molds have excellent heat conductivity and are reasonably priced. They work well for less complicated components and medium-volume manufacturing.
Benefits include low cost, excellent heat conductivity, and suitability for permanent mold casting applications as well as sand casting.
Applications: Frequently used in gravity die casting and sand casting.
Graphite:
Graphite dies and molds, which are often composed of graphite mixed with other materials, have a high heat conductivity. Small to medium-sized manufacturing runs are appropriate for them.
Benefits include quick cooling, suitability for complex component designs, and affordability.
Applications: Applied to a number of casting techniques, such as investment casting and die casting.
Ceramic:
Description: Refractory materials like silica, alumina, or zirconia are used to make ceramic molds. Precision casting procedures often employ them.
Benefits include less machining needs, excellent accuracy, and a smooth surface finish.
Applications: Frequently used in aluminum investment casting.
Sand:
Sand molds, fabricated from silica sand or other molding sands, provide both affordability and adaptability. They are often used in production of low to medium volumes.
Benefits include affordability, suitability for intricate forms, and versatility in terms of casting sizes.
Applications: Often used in the sand casting process for different aluminum products.
Plaster:
Plaster molds are a cost-effective solution for small-scale manufacturing and prototypes.
Benefits: Low-cost alternative for prototyping and small volumes.
Applications: When cost is a major factor, used for bespoke or creative casting.
The exact specifications of the casting project, the casting method used, and other elements like component complexity, production volume, and financial considerations all have a role in the mold material selection. To guarantee the manufacturing of high-quality aluminum castings, it is crucial to take into account the mold material’s thermal characteristics, wear resistance, and general durability.
How do you mold and cast aluminum?
There are several phases involved in molding and casting aluminum, and the procedure might change according on the casting technique used. Die casting and sand casting are two popular techniques for casting aluminum. This is a broad synopsis of the procedures:
Sand Casting:
Creating Patterns:
Make a blueprint out of wood, metal, or plastic for the needed portion. The final part’s precise negative form should be represented in the pattern.
Mold Readying:
To create a mold cavity, place the design within a box and cover it with a particular molding sand. For more intricate forms, this mold may be divided into two parts: the cope and the drag.
Elimination of Patterns:
With extreme care, remove the pattern, leaving a hollow in the sand that resembles the required part’s form.
Aluminum Melting:
Heat aluminum to the appropriate temperature in a furnace. Depending on the individual aluminum alloy being utilized, the temperature may change.
Dispensing:
Fill the mold cavity with the molten metal. Let it cool and become solid.
Elimination and Polishing:
Take the casting out of the mold when the metal has hardened. When necessary, carry out finishing procedures like surface treatment or machining to remove any extra material.
Die Casting:
Die Design:
Create a die or mold with two parts that, when closed, will reveal a hollow shaped like the finished product.
Die Production:
Make the die out of steel or other materials. To guarantee accuracy and longevity, the die is machined with precision.
Aluminum Melting:
In a furnace, melt the aluminum alloy to the precise temperature needed for die casting.
Injectable:
Apply intense pressure as you inject the molten metal into the die. In addition to facilitating speedy mold filling, pressure guarantees an exact and precise cast.
Dissipation:
Give the metal in the die time to cool and solidify. The part’s ability to retain its structural integrity depends on the cooling period.
Removal:
Expel the solidified aluminum portion by opening the die. For the next casting, the cycle is then repeated.
Finalizing and Trimming:
Remove any surplus material from the cast component and carry out further finishing procedures as required.
General Advice for Casting Aluminum:
Safety: When handling molten metal, always take the appropriate safety precautions.
Temperature Control: To guarantee correct casting, keep an eye on and regulate the molten aluminum’s temperature.
Metal Preparation: To enhance the casting quality, purge the aluminum of impurities and degas if required.
Tooling Maintenance: To keep molds or dies in excellent shape, check and maintain them on a regular basis.
Remember that the particulars of the procedure could change depending on the tools, supplies, and volume of the product. When working on aluminum casting projects, it’s best to refer to comprehensive casting instructions or speak with knowledgeable experts.