Introduction
Dans le monde complexe de la fabrication, pièces en aluminium moulé sous pression sont parmi les plus utilisées, car elles allient résistance, précision et polyvalence. Cet article se penche sur les détails complexes des pièces en aluminium moulées sous pression, en explorant leurs processus de fabrication, leurs applications dans tous les secteurs et les avantages indéniables qu'elles apportent à la production moderne.
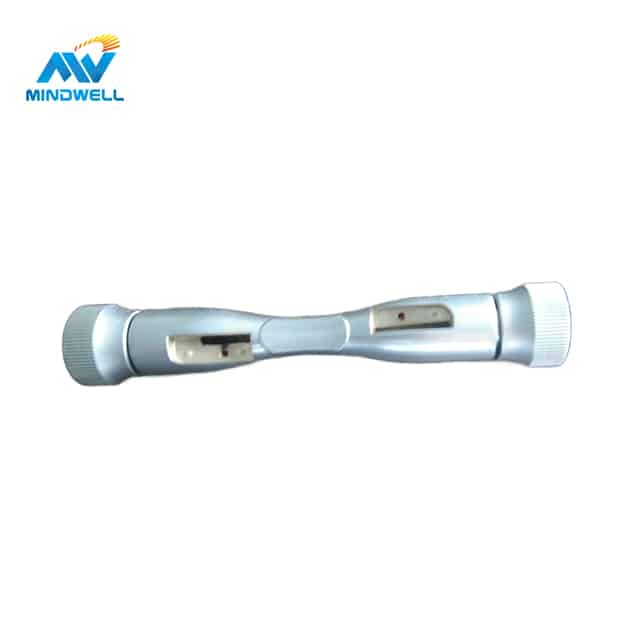
1. créer des miracles
Production de pièces en aluminium moulé sous pression
L'art qui se cache derrière les pièces en aluminium moulé sous pression implique un processus de production minutieux. De la sélection des matériaux aux techniques de moulage avancées, chaque étape contribue à créer des pièces d'une qualité inégalée.
- Le choix des matériaux est essentiel. L'aluminium est un métal léger, très résistant, qui présente une bonne conductivité électrique et une bonne résistance à la corrosion. Au cours du processus de moulage sous pression, la sélection d'alliages d'aluminium de haute qualité peut garantir les propriétés mécaniques et la durabilité des pièces. Dans le même temps, les alliages d'aluminium appropriés peuvent également offrir de bonnes propriétés de moulage, y compris la fluidité, le retrait et l'étanchéité à l'air.
- Conception du moule et la fabrication. Le moule est un outil essentiel pour le formage des pièces en aluminium moulé sous pression. Sa qualité et sa conception ont un impact décisif sur la forme, la taille et la qualité de la surface de la pièce. Au cours de l'étape de fabrication de moules Dans le cadre du processus de fabrication des moules, des facteurs tels que la géométrie, la précision dimensionnelle, l'état de surface et l'emboutissage de la pièce doivent être pris en considération. Parallèlement, afin de garantir l'efficacité de la production et de réduire les coûts, la conception des moules doit également prendre en compte le remplacement et la réparation des pièces d'usure.
- Au cours du processus de moulage sous pression, l'alliage d'aluminium en fusion est injecté dans le moule sous haute pression, puis refroidi et démoulé pour obtenir des pièces en aluminium moulées sous pression. Dans ce processus, le contrôle de la pression, de la température et du temps est vital. Une pression trop élevée peut endommager le moule, tandis qu'une pression trop faible peut entraîner des défauts tels que des soufflures dans la pièce. Parallèlement, le contrôle de la température et du temps affecte aussi directement la vitesse de refroidissement, la vitesse de retrait et la distribution des contraintes internes de la pièce.
- Enfin, le traitement ultérieur des pièces en aluminium moulé sous pression est également essentiel. Il comprend des étapes telles que l'ébavurage, le polissage et la peinture par pulvérisation. Ces traitements peuvent non seulement améliorer l'apparence des pièces, mais aussi leur résistance à la corrosion et à l'usure.
En bref, le processus de production de pièces en aluminium moulées sous pression est un processus détaillé et complexe, et chaque maillon a un impact important sur la qualité des pièces. En sélectionnant les bons matériaux, en concevant et en fabriquant des moules de haute qualité, en contrôlant précisément le processus de moulage sous pression et le post-traitement, nous pouvons créer des pièces en aluminium moulé sous pression d'une qualité inégalée.
CAO de pointe
La technologie avancée de conception assistée par ordinateur (CAO) joue un rôle crucial dans la précision du processus de moulage. Cette technologie permet de transformer des conceptions complexes en pièces d'aluminium tangibles et de haute qualité en utilisant des logiciels spécialisés dans les domaines suivants conception de produits, la simulation et l'analyse.
Tout d'abord, la technologie CAO permet de réaliser des prototypes et des simulations pendant la phase de conception afin de tester la faisabilité et les performances de la conception. En testant les conceptions dans un environnement informatique, il est possible de prévoir et de résoudre les éventuels problèmes de fabrication, tels que l'écoulement du moule, la formation de pores et l'ajustement de l'assemblage des pièces. Cette conception prédictive améliore considérablement l'efficacité de la production et réduit les coûts de production, tout en garantissant la précision et la qualité du produit.
Deuxièmement, la technologie CAO permet de contrôler avec précision le processus de fabrication des moules. En utilisant les données précises du modèle CAO, il est possible de fabriquer des moules avec des détails plus fins et des dimensions plus précises. Dans le même temps, la technologie CAO peut également effectuer une analyse des contraintes sur le moule afin de prévenir les problèmes potentiels tels que les fissures au cours du processus de moulage sous pression. Ce processus précis de fabrication des moules garantit la précision des dimensions et des formes des pièces, ce qui permet aux pièces d'aluminium produites de répondre à des exigences de qualité strictes.
En outre, la technologie CAO permet également d'effectuer des simulations et des optimisations au cours du processus de moulage sous pression. En simulant le processus de moulage sous pression dans un environnement informatique, les paramètres de moulage sous pression tels que le flux de métal, le taux de refroidissement du moule et la distribution de la pression peuvent être prédits et optimisés avec précision. Cette optimisation par simulation maximise l'efficacité de la production tout en maintenant la qualité et les performances des pièces.
Enfin, la technologie CAO peut également être utilisée pour contrôler et optimiser le processus de production. À l'aide de capteurs et d'équipements de surveillance, les données du processus de production peuvent être obtenues en temps réel, puis comparées et analysées avec les modèles de CAO. Ce type de contrôle permet de détecter et de résoudre rapidement les problèmes potentiels. En même temps, la conception peut être ajustée et optimisée sur la base des conditions de production réelles afin de répondre à la demande du marché.
En conclusion, la technologie avancée de conception assistée par ordinateur (CAO) joue un rôle clé dans la précision du processus de moulage. En réalisant des prototypes et des simulations pendant la phase de conception, en contrôlant avec précision le processus de fabrication du moule, en simulant et en optimisant le processus de moulage sous pression, et en contrôlant et en optimisant le processus de production, la technologie de la CAO permet de réaliser des conceptions complexes de composants en aluminium et de les produire avec une qualité et une précision élevées. Pièces en aluminium. L'application de cette technologie permet non seulement d'améliorer l'efficacité de la production et de réduire les coûts de production, mais aussi de multiplier les possibilités de production de composants en aluminium.
Contrôle de la température et de la pression
Dans le processus de moulage sous pression, le contrôle précis de la température et de la pression est extrêmement important. Elles sont non seulement essentielles pour garantir l'intégrité structurelle de la pièce, mais jouent également un rôle décisif dans l'amélioration de la résistance et de la finition de la surface de la pièce.
- Contrôle de la température. Au cours du processus de moulage sous pression d'un alliage d'aluminium, un contrôle approprié de la température peut garantir la fluidité de l'aluminium en fusion et réduire l'apparition de défauts internes dans le moulage. Dihui Die Casting s'appuie sur un équipement de contrôle de la température avancé pour contrôler et surveiller la température de coulée en temps réel. Typiquement, la température de fusion de l'alliage d'aluminium est 650℃-710℃, tandis que la température du moule est habituellement entre 150℃-250℃. En fonctionnement réel, les températures du moule et du four peuvent être contrôlées avec précision pour s'assurer que la température de chaque coulée répond aux exigences de la norme.
- Le contrôle de la pression est également un facteur critique dans le processus de moulage sous pression. Une pression appropriée permet de s'assurer que le métal remplit entièrement chaque détail du moule et d'éviter les problèmes tels que les pores et les défauts. Le réglage précis de la pression permet d'assurer la cohérence et l'intégrité des pièces et d'améliorer la précision et la stabilité du moulage. Au cours du processus de moulage sous pression, la taille et le temps d'action de la pression ont un impact significatif sur la qualité et la performance du moulage.
- Grâce à un contrôle précis de la température et de la pression, l'intégrité structurelle des pièces coulées est assurée. Cela signifie que chaque pièce moulée aura la forme, la taille et les détails internes prévus. En outre, ces contrôles améliorent la résistance de la pièce moulée. Comme le métal s'écoule plus uniformément sous haute pression et que les défauts internes sont réduits, la résistance globale de la pièce moulée est améliorée.
- Enfin, un contrôle précis de la température et de la pression peut également améliorer l'état de surface de vos pièces moulées. Au cours du processus de moulage sous pression, des conditions de température et de pression appropriées permettent de réduire la rugosité de la surface du moule, ce qui rend la surface de la pièce moulée plus lisse. En outre, en contrôlant le débit et le mode de remplissage du métal, il est possible de réduire les défauts de surface tels que les pores et les fermetures à froid, ce qui améliore encore la qualité de la surface de la pièce moulée.
En résumé, un contrôle précis de la température et de la pression joue un rôle extrêmement important dans le processus de moulage sous pression. Elles garantissent non seulement l'intégrité structurelle et la résistance du moulage, mais améliorent également la finition de la surface du moulage. Des pièces moulées en alliage d'aluminium de haute qualité peuvent être produites en utilisant un équipement de contrôle de la température avancé et une régulation précise de la pression.

2. Application interprofessionnelle
Favoriser l'innovation dans le secteur automobile
Dans le secteur automobile, les pièces en aluminium moulées sous pression jouent un rôle essentiel dans la conception légère, l'efficacité énergétique et l'intégrité structurelle des véhicules modernes.
- Pensons à la conception légère. Les constructeurs automobiles modernes s'efforcent de réduire le poids de leurs véhicules en utilisant des matériaux légers et des conceptions optimisées pour améliorer le rendement énergétique et les performances. Les pièces en aluminium moulé sous pression sont un facteur clé pour atteindre cet objectif en raison de leur grande résistance et de leur légèreté. Par exemple, l'utilisation de capots, d'ailes, de portes, de cadres de portes et d'autres composants en aluminium réduit considérablement le poids du véhicule tout en conservant la résistance et la rigidité requises. En outre, la légèreté de la conception confère à la voiture une meilleure contrôlabilité et une plus grande vitesse de réaction, ce qui améliore l'expérience de conduite.
- Les pièces en aluminium moulé sous pression jouent également un rôle majeur dans l'amélioration du rendement énergétique. L'aluminium étant moins dense, l'utilisation de pièces en aluminium permet de réduire le poids total du véhicule, ce qui allège la charge sur le moteur et améliore le rendement énergétique. Une étude a montré que pour chaque 100 kilogrammes de poids de véhicule en moins, la consommation de carburant peut être réduite d'environ 7%. Par conséquent, les pièces en aluminium moulées sous pression sont d'une grande importance pour la promotion de la protection de l'environnement.
- Les pièces en aluminium moulé sous pression sont également essentielles au maintien et à l'amélioration de l'intégrité structurelle de votre véhicule. L'aluminium est un matériau à haute résistance et à haute rigidité qui peut résister aux chocs extérieurs et à la corrosion. Dans les structures automobiles, les pièces en aluminium moulé sous pression telles que les composants du châssis, du moteur, du système de freinage, etc. peuvent améliorer la résistance structurelle et la durabilité de la carrosserie. En outre, en raison de la conductivité thermique élevée de l'aluminium, les composants tels que les radiateurs en aluminium permettent d'évacuer rapidement la chaleur vers la surface du véhicule, d'améliorer l'efficacité de la dissipation thermique et d'assurer le fonctionnement stable du moteur et du système de freinage.
Les pièces en aluminium moulé sous pression jouent un rôle de plus en plus important dans l'industrie automobile. Non seulement elles permettent de concevoir des véhicules légers et d'améliorer le rendement énergétique, mais elles renforcent également l'intégrité structurelle de la voiture. Par ailleurs, le processus de fabrication des pièces moulées sous pression en aluminium est relativement respectueux de l'environnement et répond aux exigences du développement durable. Avec les progrès technologiques et la demande croissante de protection de l'environnement, les perspectives d'application des pièces en aluminium moulées sous pression dans l'industrie automobile future seront plus larges.
Possibilités d'éclairage dans le monde de l'électronique
Dans le monde de l'électronique, les composants en aluminium moulé sous pression ont un impact large et profond sur les applications de dissipation thermique efficaces. Qu'il s'agisse de smartphones, de tablettes, d'ordinateurs portables ou de divers produits électroniques industriels, les composants en aluminium moulé sous pression jouent un rôle clé.
Commençons par le smartphone. Les performances et la stabilité d'un smartphone dépendent en grande partie de la conception de ses composants électroniques internes et de son système de refroidissement. Les composants en aluminium moulé sous pression jouent un rôle essentiel à cet égard. La conductivité thermique élevée de l'aluminium et ses propriétés de légèreté en font un matériau idéal pour les systèmes de refroidissement des téléphones portables. Les pièces en aluminium moulé sous pression conçues avec précision, telles que les radiateurs, les boîtiers, etc., peuvent conduire efficacement la chaleur de l'intérieur du téléphone vers l'extérieur, ce qui garantit la stabilité et la fiabilité du téléphone lors d'un fonctionnement à forte charge.
Outre les smartphones, les composants en aluminium moulé sous pression sont également importants pour les applications de dissipation thermique dans d'autres produits électroniques tels que les tablettes et les ordinateurs portables. Les structures internes de ces appareils sont plus complexes et des systèmes de refroidissement efficaces sont essentiels pour maintenir des performances et une stabilité élevées. Les composants en aluminium moulé sous pression peuvent répondre aux besoins de légèreté, de résistance élevée et de dissipation thermique efficace de ces appareils, et sont donc largement utilisés dans la conception de ces appareils.
En outre, les composants en aluminium moulé sous pression sont de plus en plus utilisés dans les équipements électroniques industriels. Les équipements électroniques industriels ont généralement une puissance plus élevée et des circuits plus complexes, de sorte que les exigences en matière de systèmes de refroidissement sont également plus strictes. Les pièces en aluminium moulé sous pression offrent une grande résistance, une conductivité thermique élevée et des solutions légères, ce qui permet à ces appareils de maintenir des performances stables dans des environnements d'exploitation difficiles.
Dans l'ensemble, les composants en aluminium moulé sous pression jouent un rôle clé dans le refroidissement efficace des appareils électroniques. Des smartphones à l'électronique industrielle, les composants en aluminium moulé sous pression ont une large gamme d'applications et un impact considérable. Comme la technologie électronique continue de progresser et que les exigences en matière de dissipation de la chaleur continuent d'augmenter, les composants en aluminium moulé sous pression continueront de jouer un rôle important dans la conception et la fabrication des futurs appareils électroniques.
3. Avantages et innovation
Rapport résistance/poids
The excellent strength-to-weight ratio of die-cast aluminum parts is due to some of the unique physical and mechanical properties of the aluminum itself, as well as the advantages of the die-casting process. This property makes die-cast aluminum components the first choice for many industries that require lightweight yet strong components.
- Aluminum is a light metal with a relatively low density. This allows the aluminum parts to be relatively light in weight yet retain adequate strength. Aluminum’s strength to weight ratio is superior to that of many other metals, such as steel and copper. This means that for the same weight, aluminum offers greater strength, allowing aluminum parts to perform exceptionally well when withstanding loads and stresses.
- The die casting process plays a key role in achieving a high strength to weight ratio. Die casting is a high-pressure molding process that applies high pressure in a mold to inject molten aluminum alloy into the mold cavity and form the part after cooling. Due to the high pressure and rapid cooling during die casting, aluminum alloys are able to form a dense microstructure that increases the strength and hardness of the part. Additionally, the die-casting process enables the design of complex shapes and thin-walled structures, further reducing component weight while maintaining the required strength and stiffness.
- The composition and heat treatment process of the aluminum alloy also have a significant impact on the strength-to-weight ratio. By adding alloying elements and carrying out appropriate heat treatment, the mechanical properties and microstructure of aluminum alloys can be adjusted to further improve their strength and hardness. This enables die-cast aluminum components to perform exceptionally well in a variety of application conditions.
- Combined with the above factors, the strength-to-weight ratio of die-cast aluminum components makes them the preferred choice for many industries. In the aerospace sector, for example, weight reduction is critical to improving fuel efficiency and flight performance. Die-cast aluminum components play an important role in the manufacture of structural parts and casings in spacecraft such as aircraft, satellites and rockets. In the automotive industry, die-cast aluminum components are used to make vehicle bodies, engine parts, and suspension systems to reduce vehicle weight and improve fuel efficiency. In addition, die-cast aluminum components are also widely used in areas such as electronics, power tools, and sporting goods.
The excellent strength-to-weight ratio of die-cast aluminum components is the result of a combination of the lightweight properties of aluminum, the advantages of the die-casting process, and the control of the alloy composition and heat treatment process. This characteristic makes die-cast aluminum parts the first choice for critical industries that require lightweight yet strong components.
Unleash complex designs
Die casting is an advanced manufacturing process capable of producing aluminum parts with complex geometries, thin-walled structures and high quality. Here are just a few of the ways die-casting technology offers design freedom and meets modern, evolving design requirements:
- Complex geometries: Die casting technology can produce aluminum parts with complex geometries, such as parts with fine features, projections and grooves. This degree of design freedom allows designers to innovate in the structure and appearance of parts and realize more complex design concepts.
- Thin-wall structure: Die-casting technology can realize the design of thin-wall structure, and the wall thickness of parts can be very thin, reaching the millimeter level. This thin-walled design can significantly reduce the weight of the part while maintaining adequate strength and stiffness. This degree of design freedom is very important for modern products, especially for applications such as automotive, electronics and aerospace that require lightweighting and energy conservation.
- High-quality surface: Die-casting technology can produce high-quality aluminum parts with smooth, flat surfaces and no obvious flaws and defects. This high-quality surface enhances the look and feel of your product, while also improving its longevity and reliability.
- Good Mechanical Properties: Die-cast aluminum parts have mechanical properties such as high strength, high hardness and good wear resistance. These properties can meet the requirements for high strength, lightweight and durability of modern products.
- Diverse material selection: Die-casting technology can use different types of aluminum alloys as raw materials. These aluminum alloys have different mechanical properties and chemical compositions and can be selected according to design requirements. This diversity of material options allows designers to use suitable aluminum alloy materials in different application areas.
In summary, the design freedom and ability to meet modern and evolving design requirements that die-casting technology offers make it an important manufacturing process in modern manufacturing. By leveraging die-casting technology, designers can innovate and design more freely to achieve more complex, lightweight and high-quality product designs.
time and cost efficient
In the competitive landscape of the manufacturing industry, time is indeed money. Production cycles for die-cast aluminum parts surpass traditional methods, providing companies with a competitive advantage and faster time to market. Let’s delve deeper into this issue:
- Optimization of production cycle: Die-casting technology has efficient production capacity and can complete the production of a large number of parts in a short time. The die-casting process allows more products to be manufactured in less time than traditional machining or forging processes. This optimization of the production cycle saves valuable manufacturing time for companies and speeds up product launch.
- Reduce manufacturing links: Die-casting technology can achieve integrated manufacturing, that is, the entire manufacturing process from raw materials to final parts can be completed in one device. This kind of integrated manufacturing reduces links and transportation time in the production process, reducing the manufacturing cycle.
- Rapid prototyping: Die-casting technology allows rapid production of prototype parts, allowing designers and engineers to test and validate products at an early stage. This rapid prototyping capability greatly shortens the product development cycle and accelerates the speed of products to market.
- Customized production: Die-casting technology can realize customized production, producing parts of different specifications and shapes according to customer needs. This customized production capability provides companies with more market opportunities, meets the special needs of customers, and further improves the speed of products to market.
- Efficient supply chain management: Die-casting technology can make supply chains more efficient and flexible. Because die-cast aluminum parts are consistent and standardized, companies can more easily conduct inventory management and logistics distribution, reducing supply chain management costs.
Taken together, the production cycle of pièces en aluminium moulé sous pression exceeds traditional methods, providing companies with a competitive advantage and faster time to market. By optimizing production cycles, reducing manufacturing links, rapid prototyping, customized production and efficient supply chain management, die-casting technology brings higher production efficiency and faster response speed to companies, meeting the needs of modern manufacturing.
4.FAQ
Are die-cast aluminum parts suitable for high-stress applications?
Yes, die-cast aluminum parts perform well in high-stress applications due to their superior strength-to-weight ratio and structural integrity.
Can these components be recycled?
Absolutely. Die-cast aluminum parts are highly recyclable, contributing to sustainable and eco-friendly manufacturing practices.
How does temperature and pressure control affect the quality of die castings?
Precise temperature and pressure control ensures thorough mold filling, minimizing defects and improving part structural integrity and surface finish.
Which industries benefit most from die-cast aluminum parts?
The aerospace, automotive, electronics, and renewable energy industries are major beneficiaries, leveraging the versatility and strength of these parts.
What finishing options are available for die cast aluminum parts?
Common surface treatment options include anodizing and powder coating, which not only provide aesthetics but also provide additional protection against corrosion.
How do die-cast aluminum parts contribute to sustainability?
Their recyclability, light weight and energy efficiency of production contribute to the overall sustainability of die-cast aluminum parts.
Conclusion: Shaping the Future
In conclusion, die-cast aluminum parts are the backbone of modern manufacturing innovation. Its diverse applications and unrivaled advantages make it a cornerstone of various industries. As technology advances, so does the influence of die-cast aluminum parts, shaping the future of manufacturing with strength, precision and sustainability.