matériaux de moulage sous pression
Nous fournissons des services de moulage sous pression sur mesure dans une variété de matériaux, et nous pouvons choisir le matériau le plus approprié en fonction de l'utilisation du produit du client et des exigences de conception. Par exemple, si une résistance aux températures élevées ou à l'usure est requise, différents matériaux peuvent être sélectionnés.
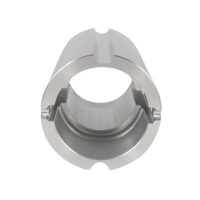
Moulage sous pression d'aluminium
En raison de ses caractéristiques, l'aluminium est actuellement le matériau de moulage sous pression le plus couramment utilisé et peut être largement employé dans diverses industries. Presque toutes les pièces moulées sous pression peuvent être réalisées en aluminium.
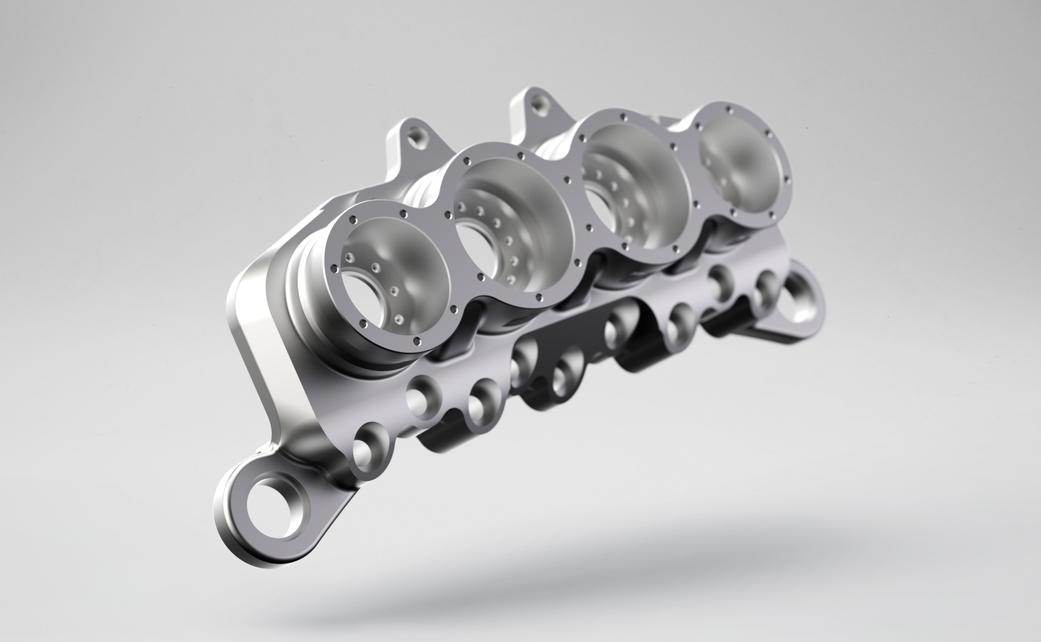
Moulage sous pression d'alliages d'aluminium
Parfois, lorsque l'aluminium pur ne peut répondre aux exigences de production, d'autres matières premières métalliques sont généralement ajoutées à l'aluminium pour en améliorer la stabilité ou la dureté, etc. Ces matériaux d'aluminium ajoutés à des matières premières métalliques sont collectivement appelés alliages d'aluminium.
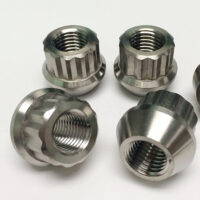
Moulage sous pression d'alliages de zinc
L'alliage de zinc est un métal dont la matière première est le zinc et dont les autres composants sont le cuivre, l'aluminium, le magnésium, etc. Il présente une bonne résistance à la corrosion et de bonnes propriétés mécaniques.
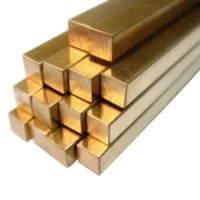
Moulage sous pression du laiton
Le matériau de moulage sous pression en laiton est un alliage de cuivre et de zinc, généralement composé de 60-90% de cuivre et de 10-40% de zinc. Il présente généralement une bonne aptitude au traitement, une résistance élevée à la corrosion et une bonne conductivité électrique. En raison de sa bonne coulabilité et formabilité, il peut être utilisé dans une variété d'applications, y compris certaines pièces de machines, tuyaux, joints, valves, écrous et boulons, etc.
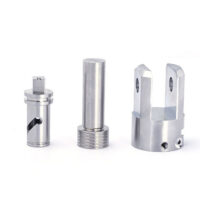
Pièces moulées en acier inoxydable
L'acier inoxydable présente les caractéristiques suivantes : résistance à la corrosion, résistance aux températures élevées, grande solidité et bonnes performances de traitement. Les matériaux les plus courants pour le moulage sous pression de l'acier inoxydable sont l'acier inoxydable 316L, l'acier inoxydable 304, l'acier inoxydable 410 et l'acier inoxydable 17-4PH. Ces matériaux sont couramment utilisés dans la fabrication de composants et d'éléments pour l'automobile, d'équipements médicaux, de moules, etc.
Comment choisir le matériau pour le moulage sous pression ?
Chez MindWell, les matériaux couramment utilisés pour le moulage sous pression sont l'alliage de zinc, l'alliage d'aluminium, l'alliage de magnésium, l'alliage de cuivre, etc. et peuvent également être personnalisés en fonction de vos besoins. Vous pouvez nous faire part de vos exigences spécifiques en matière de matériaux pour les pièces personnalisées, ou vous pouvez prendre en compte les aspects suivants lors du choix des matériaux :
- Propriétés mécaniques : résistance à la traction, limite d'élasticité, dureté, ténacité, etc. Il est nécessaire de sélectionner les propriétés mécaniques appropriées en fonction de l'environnement d'utilisation réel.
- Résistance à la chaleur : S'il doit être utilisé dans un environnement à haute température, il est nécessaire de choisir un matériau résistant à cette température.
- Résistance à la corrosion : S'il doit être utilisé dans un environnement corrosif, il est nécessaire de choisir un matériau résistant à la corrosion.
- Performance de traitement : y compris la performance du traitement thermique, la performance de la coulée, la performance du traitement, etc.
- Le coût : Des matériaux différents ont des prix différents, et il est nécessaire de choisir des matériaux avec des coûts appropriés en fonction de la situation réelle.