Le moulage sous pression de l'aluminium est un processus dans lequel l'alliage d'aluminium est chauffé à l'état liquide et injecté dans un moule de moulage sous pression pour être refroidi et formé. Ce procédé offre des avantages tels que la réduction des coûts, la précision, l'efficacité et la fabrication à grande échelle. Le taux d'utilisation des matériaux est élevé et le taux d'utilisation des ébauches peut atteindre 90%, ce qui permet de réduire les coûts. Les applications sont les suivantes industrie automobileLes pièces moulées sous pression en aluminium peuvent être utilisées dans les domaines suivants : industrie, électronique, appareils ménagers, construction et décoration, aérospatiale, militaire et machines générales. Les pièces moulées sous pression en aluminium ont une excellente compatibilité, une bonne rugosité de surface et une grande précision dimensionnelle.
Introduction
Le moulage sous pression de l'aluminium est un processus dans lequel l'alliage d'aluminium est chauffé à l'état liquide, puis injecté dans un moule de moulage sous pression pour être refroidi et formé. Le moulage sous pression de l'aluminium offre de nombreux avantages, notamment la réduction des coûts, la précision, l'efficacité et la fabrication à grande échelle. Le taux d'utilisation des matériaux est élevé, et le taux d'utilisation des ébauches peut atteindre 90%, ce qui permet de réduire les coûts.
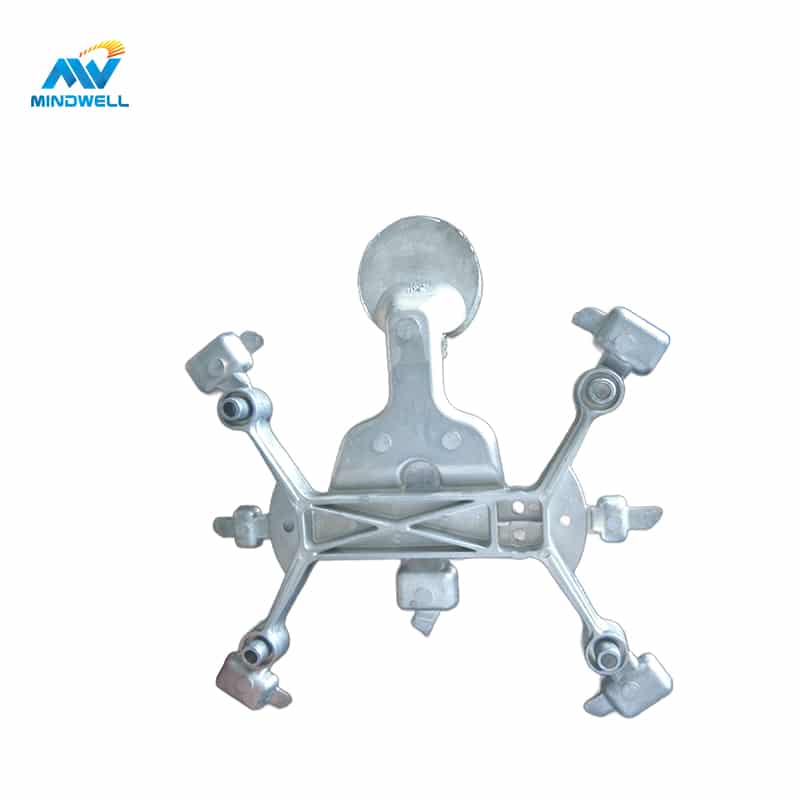
La définition et l'importance du moulage sous pression de l'aluminium
La méthode de moulage sous pression de l'aluminium consiste à chauffer un alliage d'aluminium jusqu'à ce qu'il devienne liquide, puis à l'injecter dans un moule de moulage sous pression, où il refroidit et se solidifie. Les avantages du moulage sous pression de l'aluminium par rapport à d'autres techniques de production sont une utilisation élevée des matériaux, une productivité élevée et une grande précision du produit. Le moulage sous pression de l'aluminium est un autre nom pour les articles moulés sous pression en aluminium. Le moulage sous pression de l'aluminium a plusieurs utilisations, notamment la production d'équipements, d'appareils électroniques et de composants automobiles. Les composants en aluminium moulé sous pression sont légers, solides et résistants à la corrosion, ce qui permet d'améliorer considérablement les performances et le rendement énergétique d'une automobile. Les composants en aluminium moulé sous pression présentent de solides propriétés mécaniques et une conductivité thermique élevée, ce qui contribue à prolonger la durée de vie et la stabilité du produit. Les pièces moulées sous pression en aluminium sont des composants fiables et de haute qualité utilisés dans la fabrication de machines qui peuvent prolonger la durée de vie et les performances de l'équipement. Par conséquent, le moulage sous pression de l'aluminium a été largement développé et utilisé dans une variété d'industries. Avec la création de nouveaux matériaux et la popularité croissante des technologies de fabrication contemporaines, les possibilités d'application du moulage sous pression de l'aluminium ne cesseront de s'étendre.
Domaines d'application du moulage sous pression de l'aluminium
Le procédé de moulage sous pression de l'aluminium est utilisé dans de nombreux domaines. Voici quelques-uns des principaux domaines :
- Industrie automobile : Les pièces de moteur, les freins, les mécanismes de direction et d'autres composants font partie des nombreux produits de l'industrie automobile qui font appel à la technologie du moulage sous pression de l'aluminium. La résistance, la légèreté et la conductivité thermique de l'alliage d'aluminium lui permettent de répondre aux exigences d'efficacité énergétique et de légèreté des véhicules.
- Équipements électroniques et de communication : Les composants des équipements électroniques et de communication, tels que les boîtiers, les radiateurs, les connexions et les prises, etc., sont fabriqués en utilisant la méthode de moulage sous pression de l'aluminium. Grâce à sa forte protection électromagnétique et à sa conductivité thermique, l'alliage d'aluminium peut améliorer la stabilité et les performances de l'équipement.
- Appareils ménagers : Le domaine des appareils électroménagers et de l'équipement électrique, y compris les boîtiers de climatiseurs, les tambours de machines à laver, les composants de réfrigérateurs et les supports de télévision, est un autre domaine dans lequel la technique de moulage sous pression de l'aluminium est largement utilisée. La texture et l'esthétique des produits en alliage d'aluminium peuvent être améliorées par la qualité et l'aspect de leur surface.
- Secteur de la construction et de la décoration : Dans ce secteur, les cadres de fenêtres, les accessoires de portes et de fenêtres, les éléments de décoration intérieure et d'autres articles sont fabriqués à l'aide de la méthode de moulage sous pression de l'aluminium. Dans les domaines de la construction et de la décoration, l'alliage d'aluminium peut satisfaire aux critères de solidité du matériau, de résistance à la corrosion et d'attractivité, car il est léger, résistant aux intempéries et malléable.
- Autres domaines : L'aérospatiale, l'armée, la machinerie générale et d'autres domaines font également un usage intensif de la technologie du moulage sous pression de l'aluminium. Par exemple, le moulage sous pression de l'aluminium peut être utilisé pour produire des hélices, des pièces de moteur, des coques d'avion et d'autres composants. En outre, la technique de moulage sous pression de l'aluminium permet de fabriquer divers composants d'équipements mécaniques généraux, notamment des pièces de machines-outils, des corps de pompes, des vannes, des réservoirs sous pression, etc.
Avantages et limites du moulage sous pression de l'aluminium
Le moulage sous pression de l'aluminium présente l'avantage d'être peu coûteux, très précis, efficace et capable de produire des formes compliquées. Mais il existe aussi certaines restrictions qui, selon l'application, doivent être soigneusement prises en compte.
Avantages du moulage sous pression de l'aluminium :
- Le métal en fusion conserve une grande fluidité sous haute pression et à grande vitesse, ce qui permet de fabriquer des objets métalliques creux et profonds présentant des géométries complexes, des contours clairs et des parois minces.
- Les pièces moulées sous pression en aluminium présentent une excellente compatibilité, une bonne rugosité de surface et une grande précision dimensionnelle.
- Les coûts peuvent être réduits en raison du taux élevé d'utilisation des matériaux et du taux d'utilisation des ébauches 90%.
- Excellente productivité et adaptée à la fabrication à grande échelle.
- Les incrustations peuvent être utilisées pour répondre à des besoins de performance spécifiques et sont simples à mettre en œuvre.
- peu coûteux. Le moulage sous pression de l'aluminium peut réduire les coûts de production et offre un processus de fabrication plus simple que les techniques de fabrication conventionnelles.
- Elle est capable de produire de grands volumes de pièces métalliques coulées et est extrêmement reproductible.
- Grâce à sa grande résistance, le matériau est capable de supporter des contraintes dans des situations où les charges et les températures sont élevées.
- La surface est facile à travailler et à peindre, et le revêtement peut améliorer son attrait, sa résistance à la corrosion et sa durabilité.
Le moulage sous pression de l'aluminium présente toutefois plusieurs inconvénients.
- Les pièces moulées sous pression ne conviennent pas à la fabrication de petits lots car elles présentent souvent des trous et des impuretés oxydées.
- Les types d'alliages de moulage sous pression et les tailles des pièces moulées sous pression sont limités.
- Les moules et l'équipement sont coûteux et nécessitent un investissement important.
- Au cours du processus de fabrication, des déchets et des gaz d'échappement sont produits ; ces éléments doivent être traités pour la protection de l'environnement.
- La plupart des composants en aluminium moulé sous pression sont minces et fragiles.
- Le moulage sous pression de l'aluminium n'est peut-être pas l'option idéale pour les applications nécessitant un niveau élevé de résistance et de rigidité.
Préparation des matières premières

Sélection et contrôle de la qualité des lingots d'aluminium
Garantir la qualité des produits moulés sous pression en aluminium nécessite un certain nombre de préliminaires, notamment la sélection de lingots de haute qualité répondant aux spécifications et un contrôle de qualité rigoureux. Pour garantir la qualité et la fonctionnalité du produit fini, il est également essentiel de prêter attention à d'autres éléments du processus de moulage sous pression de l'aluminium, tels que la conception du moule, le réglage des paramètres de moulage sous pression, les procédures de post-traitement, etc.
Les éléments suivants doivent être pris en compte lors de la sélection des lingots d'aluminium :
- Teneur en aluminium : Pour garantir la qualité et la pureté des matières premières, les lingots d'aluminium doivent avoir une teneur minimale en aluminium de 99,5%.
- Teneur en impuretés : La teneur en impuretés des lingots d'aluminium doit être conforme à toutes les réglementations nationales applicables. Pour éviter tout impact négatif sur les performances du moulage sous pression, la teneur en éléments impurs tels que le fer, le silicium, le cuivre, etc. doit être maintenue dans une certaine fourchette.
- Le lingot d'aluminium doit avoir une forme régulière de parallélépipède rectangle et être exempt de tout défaut visible en termes de distorsion ou de déformation. Il ne doit pas présenter de défauts tels que des pores, des fissures ou des inclusions de scories ; la surface doit être lisse et plane.
- Spécifications dimensionnelles : La longueur, la largeur et la hauteur des lingots d'aluminium doivent être conformes aux spécifications contractuelles ou aux normes nationales applicables. La précision dimensionnelle des lingots doit également répondre aux critères garantissant la stabilité et la précision dimensionnelle des pièces moulées sous pression.
- Certificat de qualité de la matière première : Pour garantir la qualité, la traçabilité et la fiabilité des matières premières, il convient d'utiliser des lingots d'aluminium munis de ce certificat.
Les tâches suivantes doivent être accomplies pour le contrôle de la qualité des lingots d'aluminium :
- Inspection des matériaux entrants : Vérifier que les lingots d'aluminium entrant dans l'usine répondent à tous les critères en effectuant une inspection de la qualité qui couvre des aspects tels que l'apparence, les normes dimensionnelles, la composition chimique, etc.
- Inspection du processus : Pour s'assurer que les pièces moulées sous pression sont conformes aux spécifications, elles sont examinées de manière aléatoire ou approfondie au cours du processus de moulage sous pression afin de vérifier la qualité de l'aspect des pièces, l'exactitude des dimensions, la composition chimique, etc.
- Traitement des produits non qualifiés : Retrouver et gérer les pièces coulées sous pression ou les lingots d'aluminium non qualifiés, identifier les causes et prendre les mesures appropriées pour éviter que le problème ne se reproduise.
- Tenir des registres de qualité : À des fins d'analyse de la qualité et de traçabilité, gardez une trace des détails de fabrication et de l'état général de la qualité des pièces moulées sous pression et des lingots d'aluminium.
- Amélioration continue : Nous optimisons en permanence le processus de fabrication et la qualité des matières premières, nous améliorons la qualité et la stabilité de nos produits et nous identifions les problèmes et les possibilités d'amélioration grâce à l'étude du processus de production et des données sur la qualité.
Fusion et traitement des alliages d'aluminium
- Préparation des matières premières : Combiner les matières premières de l'alliage d'aluminium, telles que les lingots d'aluminium, les copeaux, les déchets d'aluminium, etc. dans un certain rapport.
Chauffage et fusion : Pour faire fondre les matières premières, il faut les placer dans le four et les chauffer à haute température. Les fours à gaz ou à résistance électrique sont les plus courants.
Contrôle de la température de fusion : La température du four est régulée, généralement entre 700 et 900 degrés Celsius, en fonction des différentes formules et spécifications des alliages d'aluminium. - Ajustement de la composition : Pour répondre aux critères de performance nécessaires, il faut ajouter les composants appropriés à l'alliage d'aluminium et apporter les modifications nécessaires à sa composition en fonction des spécifications du produit.
- Traitement des scories : Certaines impuretés et certains oxydes se forment au cours du processus de fusion, ce qui nécessite un traitement du laitier. En général, un produit chimique capable d'absorber et de purifier les impuretés de la fonte est utilisé comme agent de scorification.
- Traitement de dégazage : Pour améliorer la qualité de l'alliage d'aluminium et éliminer les gaz pendant le processus de fusion, le traitement de dégazage doit être effectué rapidement. Plusieurs techniques de dégazage sont souvent utilisées, telles que les procédures de pulvérisation et d'aspiration.
- Contrôle du temps de fusion : La qualité d'un alliage d'aluminium est fortement influencée par son temps de fusion. L'alliage d'aluminium se mélangera de manière inégale si la période de fusion est trop courte, et il s'oxydera rapidement si la durée de fusion est trop longue. Il est donc nécessaire de contrôler le temps de fusion.
Ajustement de la composition et contrôle de la qualité de l'aluminium liquide
Les performances et la qualité du produit fini sont fortement influencées par la modification de la composition et le contrôle de la qualité de l'aluminium liquide, qui sont des étapes cruciales du processus de moulage sous pression de l'aluminium.
La modification de la composition est une étape essentielle du contrôle de la qualité des liquides d'aluminium. Pour atteindre les critères de performance du produit, la composition chimique de l'aluminium liquide doit être contrôlée. Les facteurs suivants sont principalement impliqués dans l'ajustement de la composition de l'aluminium liquide :
- Élément d'aluminium : Avec un pourcentage typique de plus de 85%, l'aluminium est le principal constituant de l'alliage d'aluminium moulé sous pression. La fluidité, le retrait, la propension à la fissuration à chaud et les caractéristiques mécaniques des alliages d'aluminium sont fortement influencés par les éléments d'aluminium. En fonction de l'application prévue et des normes de performance du produit, il convient de vérifier la composition et le type de l'élément d'aluminium.
- Éléments d'alliage : Des proportions appropriées d'éléments d'alliage, tels que le magnésium, le zinc, le cuivre, etc., doivent être ajoutées aux éléments d'aluminium. Les caractéristiques mécaniques, la résistance à la corrosion et la stabilité thermique des alliages d'aluminium peuvent être améliorées par ces éléments d'alliage. Choisissez le bon type d'élément d'alliage et la bonne teneur en fonction des besoins de l'application et des performances du produit.
- Éléments d'impureté : Le fer, le silicium et d'autres impuretés peuvent être mélangés à l'alliage d'aluminium lors de sa fusion. Ces impuretés ont un impact sur la qualité et les performances de l'alliage d'aluminium. Par conséquent, afin d'éliminer ou de réduire la quantité d'éléments impurs, la composition doit être modifiée.
Des techniques d'analyse chimique peuvent être utilisées pour détecter systématiquement le liquide d'aluminium pendant le processus d'ajustement de la composition afin de déterminer sa composition chimique et sa concentration en impuretés. La composition de l'aluminium liquide est modifiée en fonction des résultats des tests afin de satisfaire aux spécifications de performance du produit.
Le contrôle de la qualité est un élément essentiel pour modifier la composition du liquide d'aluminium. Pour garantir la qualité et la pureté des matières premières, il doit être étroitement réglementé en commençant par les matières premières. Simultanément, des variables telles que la température de fusion, la durée et le pourcentage de charge doivent être gérées tout au long de l'opération afin d'éviter que la qualité de l'aluminium fondu ne diminue. Pour s'assurer que les performances et la qualité de l'aluminium liquide répondent aux spécifications, il faut également le soumettre à des tests et à des évaluations de routine.
Conception et fabrication de moules

Principes de base de la conception des moules
- Fonctionnalité : Le moule doit pouvoir accomplir la fonction de moulage prévue et garantir que la taille, la forme et la précision du produit sont conformes aux spécifications.
Structure rationnelle : La structure du moule doit être simple et facile à comprendre, simple à produire et à assembler, et facile à remplacer et à entretenir en cours d'utilisation. - Stabilité : Pour garantir une qualité constante du produit sur une longue période, le moule doit présenter une excellente stabilité et une grande durabilité en cas d'utilisation répétée.
- Sécurité : Afin d'éviter les accidents tels que les éclats, les fissures, etc. lors de l'utilisation du moule, la sécurité de l'opération doit être prise en compte lors de la conception.
- L'économie : Les coûts de fabrication et d'utilisation du moule doivent être réduits au minimum tout en respectant les normes fonctionnelles et de qualité.
Sélection et traitement des matériaux de moulage
- Sélection des matériaux : Choisir des matériaux présentant la solidité, la dureté, la résistance à l'usure, la résistance à la corrosion et la stabilité thermique adéquates en fonction des exigences du produit et des conditions de fonctionnement du moule (température, pression, frottement, etc.).
- Traitement thermique : Pour améliorer les qualités mécaniques et prolonger la durée de vie du matériau du moule, il convient d'appliquer le traitement thermique approprié, tel que la trempe, le revenu, la cémentation, etc.
- Traitement de surface : Pour améliorer la résistance à la corrosion et la qualité de la surface du moule, celle-ci est polie, rectifiée, plaquée et soumise à d'autres traitements.
Processus de fabrication des moules
- Conception du moule : Créer des dessins et concevoir la structure du moule en fonction des spécifications du produit et de l'environnement d'exploitation.
- Préparation des matériaux : Obtenir ou produire les matériaux du moule et effectuer le prétraitement et l'inspection nécessaires.
- Traitement et fabrication : Les pièces du moule sont produites par découpage au fil, par électroérosion, par traitement mécanique et par d'autres techniques, conformément aux spécifications indiquées dans les dessins.
- Assemblage et débogage : Assembler les composants du moule traité, dépanner et tester le moule pour s'assurer qu'il fonctionne comme il se doit.
- examen et acceptation : Avant d'autoriser l'utilisation du moule, il convient de procéder à un examen approfondi pour s'assurer qu'il satisfait à tous les critères de conception et de production.
Entretien et maintenance des moules
- Inspections fréquentes : Effectuer fréquemment des inspections approfondies des moules afin d'identifier et de résoudre rapidement tout problème d'usure, de corrosion, de fissure, etc.
- Nettoyage et entretien : Pour éviter d'endommager la surface du moule et de détériorer la qualité du produit, il convient de maintenir le moule propre et d'éliminer régulièrement l'huile et les autres polluants de sa surface.
- Lubrification et entretien : Pour minimiser l'usure et prolonger la durée de vie du moule, il convient de lubrifier régulièrement les éléments mobiles du moule.
- Réparation et remplacement : Pour garantir le fonctionnement régulier du moule et la qualité du produit final, il convient de réparer ou de remplacer rapidement les composants du moule qui sont gravement usés ou endommagés.
- Gestion des dossiers : Gardez une trace de l'utilisation, des réparations et de l'entretien du moule afin de pouvoir le gérer et l'entretenir à l'avenir.
Procédé de moulage sous pression de l'aluminium
Le moulage sous pression de l'aluminium est un processus au cours duquel de l'aluminium liquide est injecté dans un moule sous haute pression et refroidi pour obtenir des produits en aluminium de la forme et de la taille souhaitées.
- Fabrication de l'aluminium liquide : Pour fabriquer de l'aluminium liquide, il faut d'abord faire fondre des lingots d'aluminium de qualité supérieure, puis ajouter les composants d'alliage nécessaires. Pour garantir sa pureté tout au long de ce processus, l'aluminium liquide doit être soumis à des procédures de purification, notamment le dégazage et l'élimination des scories.
- Choisir une machine de coulée sous pression : Choisissez une machine de moulage sous pression qui répond aux spécifications des produits moulés sous pression en termes de taille, de forme et de précision. Les deux types de machines de coulée sous pression sont la chambre chaude et la chambre froide. La première permet de produire des objets de petite taille et à parois minces, tandis que la seconde permet de produire des objets de grande taille et à parois épaisses.
- Installation et réglage des moules de coulée sous pression : Établir le moule prévu sur les moules mobiles et permanents de la machine. Il faut ensuite procéder aux ajustements nécessaires de l'emplacement du moule et de la course d'ouverture/fermeture pour garantir un ajustement sûr et précis.
- Coulée et remplissage : L'aluminium fondu pénètre dans la cavité du moule par la carotte pendant le processus de coulée sous pression. L'effet de remplissage de l'aluminium liquide et la qualité du produit final sont fortement influencés par la température et la vitesse de la coulée. Le remplissage est le processus par lequel l'aluminium liquide remplit rapidement et sous haute pression la cavité du moule ; la coulée sous pression est réalisée après une brève période de solidification.
- Démoulage et refroidissement : Une fois le remplissage d'aluminium liquide terminé, le moule se refroidit pour durcir la pièce moulée sous pression. La taille et la complexité du produit déterminent la durée du refroidissement. La pièce moulée est démoulée en l'ouvrant lorsqu'elle a atteint une certaine dureté.
- Contrôle et inspection de la qualité : Une fois démoulés, les composants de moulage sous pression doivent être soumis à des tests de qualité, notamment en ce qui concerne les dimensions, le poids et l'apparence. Il est nécessaire de filtrer et de traiter les éléments non qualifiés afin de s'assurer que la qualité du produit fini est conforme aux spécifications.
Processus de post-traitement
Découpage et retrait des carottes
Les carottes et les débordements sont des éléments importants du processus de moulage sous pression qui dirigent l'aluminium fondu dans la cavité du moule. Une fois la pièce moulée sous pression créée, ces structures ne sont plus nécessaires. Par conséquent, le découpage et l'enlèvement des carottes sont des procédures cruciales de traitement après le moulage sous pression.
- Découpage : Pour s'assurer que le moulage sous pression répond aux spécifications de conception, il faut découper tout matériau excédentaire autour du bord à l'aide d'un coupe-bordures ou d'un poinçon. Le rognage permet d'obtenir un moulage sous pression plus net en éliminant le métal excédentaire.
- Retirer la carotte : il s'agit du canal qui relie la cavité du moule à la porte. Ces sections de liaison doivent être retirées après le moulage sous pression. Des techniques manuelles, mécaniques ou de découpe au laser peuvent être utilisées pour cette opération.
Technologie de traitement de surface
Les pièces moulées sous pression peuvent présenter des imperfections de surface, notamment des bavures, des pores et des renflements. Un traitement de surface est souvent nécessaire pour améliorer l'aspect et la fonctionnalité des pièces moulées sous pression.
- Polishing: To eliminate surface flaws and smooth the die casting’s surface, use a polishing machine or hand polishing. Additionally, polishing may improve the metal’s appearance and texture.
- Spray coating: Die castings may have a protective coating applied to their surface using spray coating technology to increase wear and corrosion resistance, among other properties. Paint, plastic, and other materials are often sprayed.
- The technique of applying metal or non-metallic materials to die castings’ surfaces is called electroplating. Electroplating is a technique that may be used to generate a coating layer with specific qualities on the die casting surface, such as nickel or chromium plating.
Heat treatment and strengthening process
The methods of heat treatment and strengthening are essential to enhancing die casting performance even more.
- Heat treatment: The interior metallographic structure of the die casting is modified to enhance its mechanical characteristics and stability by heating and cooling it. Annealing, quenching, and other heat treatment procedures are often used.
- Process of strengthening: Using certain techniques, die castings are made harder and more resistant to wear via the process of strengthening. Die castings with surface hardening treatment, for instance, have a harder surface and better wear resistance.
Quality inspection and finished product packaging
To make sure the die-casting components fulfil the specifications, a quality inspection is required after a number of post-processing procedures.
- Quality inspection: use performance testing, dimensional measurement, visual examination, and other methods to thoroughly assess the die castings’ quality. Die castings that are deemed unqualified must be repaired or discarded.
- Final product packaging: To preserve their integrity during storage and transit, qualified die-cast components need to be packaged properly. Appropriate packing materials and techniques, such as wooden boxes, cartons, plastic bags, etc., may be chosen based on the specifications and features of the die-casting components.
Production management and optimization
creation and execution of production schedules
One crucial step in the aluminium die-casting process is the creation of production planning. It entails giving careful thought to factors including raw material availability, manufacturing capability, and market demand. The main procedures for creating and carrying out production plans are as follows:
- Market research and analysis: Gain an understanding of the competitive landscape, product development trends, and market demand via market research, which also serves as a foundation for production plan design.
- Create production plans: Using the information from market research, company strategy objectives, and available resources, create comprehensive short- and long-term production plans.
- Resource scheduling and allocation: To guarantee the manufacturing process moves along smoothly, logically distribute resources like labour, machinery, raw materials, etc. in accordance with the production plan.
- Production scheduling and execution: Work with the production plan to schedule different production links, make sure that the plan is followed, and promptly address issues that arise throughout the production process.
- manufacturing data may be tracked in real time, allowing for the quick identification and resolution of issues with the manufacturing process. Production plans can also be modified to guarantee on-time delivery.
Keeping an eye on things and making adjustments while producing
Real-time monitoring and adjustments to the manufacturing process are necessary to guarantee the stability and quality of aluminium die-casting. The following are some essential tracking and correction steps:
- Equipment status monitoring: Make sure the die-casting machines, moulds, and other pieces of equipment are in good working order by keeping an eye on their operational state in real time using equipment sensors and instruments.
- Process parameter control: Throughout the die-casting process, critical process parameters like temperature, pressure, and time are monitored and managed in real-time to guarantee the stability and precision of the parameters.
- Quality inspection: To make sure that the product quality satisfies requirements, randomly or thoroughly examine die-casting components to look for issues with size, performance, appearance, and other indications.
- Handling of unqualified products: To avoid a recurrence of the issue, examine the reasons behind unqualified die-casting components and promptly modify the manufacturing process.
- Recording and analysis: To analyse and improve the production process, record a variety of data throughout the process, including process parameters, equipment operating parameters, quality inspection findings, etc.
Management and optimisation of production costs
Cost management is essential to the manufacturing process of aluminium die casting. Here are a few ways to save costs:
- Optimise process parameters: By doing so, you may cut down on energy use and raw material waste.
- Boost production efficiency: By enhancing equipment upkeep and boosting equipment utilisation, bolster production efficiency and lower manufacturing expenses per unit of output.
- Lower the scrap rate: Lower the scrap rate by enhancing quality control, optimising manufacturing procedures, and taking other steps that will cut waste.
- Reasonable inventory management and procurement: To prevent waste and backlogs in inventory, correctly buy raw materials based on real production demands. Effective inventory management also lowers the expenses associated with inventories.
- Management of human resources: Allocating resources sensibly, enhancing worker productivity, and cutting labour expenses.
Development and innovation trends in the aluminium die-casting process
The method of die-casting aluminium is always evolving due to the progress of technology and the shifting needs of the market. The following are some potential breakthroughs and development trends:
- Utilisation of novel materials: Create novel aluminium alloy materials to enhance die castings’ mechanical characteristics and resistance to corrosion. Investigate the potential uses of additional metals in the die casting industry concurrently.
- Intelligent production: To achieve automation, informatization, and intelligence of the production process and to enhance production efficiency and product quality, introduce intelligent technologies such as industrial robots, Internet of Things, big data analysis, etc.
- Encouragement of ecologically friendly manufacturing: As environmental consciousness grows, the aluminium die-casting industry’s green growth is pushed to cut down on resource waste and contamination to the environment during production. For instance, actions like recycling garbage and using ecologically friendly release agents are taken.
- Achieving flexibility in customisation and small batch manufacturing requires developing tools and procedures that can swiftly swap out moulds, adapting to changes in market demand, and realising customisation and small batch production.
- Extend application fields: Investigate the potential uses of aluminium die-casting technology in the domains of aerospace, lightweighting cars, new energy, and other areas, and broaden the range of applications for aluminium die-casting components. To gain more precise and thorough information on innovation and development trends, please refer to relevant literature or specialists.
Safety and environmental issues
Risks to safety and precautions to take while die-casting aluminium:
The process of die-casting aluminium may include several safety risks. Corresponding preventative actions must be done in order to guarantee production safety. The following are some typical safety risks and safety measures:
- Burns from high temperatures: Burns from the high-temperature metal liquid used in the die-casting of aluminium are rather common. Wearing the proper protective gear, such as gloves and shoes, and avoiding direct contact with hot metal liquids are examples of precautions.
- Mechanical injury: Pinching, cutting, and other forms of mechanical harm may happen while a die-casting machine is in operation. Strict adherence to operating protocols, the use of gloves and adequate protective gear, and making sure that equipment safety guards are in place are examples of preventive measures.
- Gas and dust: Dangerous gases and dust may be created during the die-casting of aluminium, endangering the health of the workers. Enhanced ventilation, the use of the proper personal protective equipment, and routine environmental cleaning and monitoring are examples of preventative approaches.
- Noise and vibration: The die-casting machine will produce noise and vibration during operation, which may be detrimental to the workers’ comfort and hearing. Controlling noise sources, using silencers, doing regular hearing examinations, and giving employees a pleasant workspace are examples of preventive methods.
- Additional safety risks include those related to electrical safety, operating at heights, etc. It is necessary to take the appropriate precautions, such as routinely inspecting electrical equipment and guaranteeing the working platform’s safety.
Environmental laws and standards for disposing of waste:
In order to guarantee that the manufacturing process satisfies environmental standards, the aluminium die-casting industry must adhere to pertinent environmental rules and waste disposal criteria. The following are some typical laws pertaining to the environment and garbage disposal:
- Pollutant emission control: In order to guarantee that pollutant emissions meet criteria, aluminium die-casting firms are required by both national and municipal environmental protection rules to regulate the emission of waste gas, waste water, and solid waste.
- Waste categorization and treatment: Depending on the kind and nature of the waste, many treatment techniques are used. Sorting recyclable garbage into different categories and delivering it to certified recycling organisations for processing is necessary. Hazardous waste must be sent to certified disposal facilities, and general waste must also be treated correctly in compliance with applicable laws.
- Environmental protection facilities and equipment: To guarantee that pollutants are adequately treated during the production process, aluminium die-casting companies must be outfitted with the appropriate environmental protection facilities and equipment, such as waste water treatment facilities and exhaust gas treatment devices.
- Environmental impact assessment and acceptance: Before being used, newly constructed, remodelled, and extended aluminium die-casting projects must go through an environmental impact assessment and be approved by the environmental protection agency.
- Improvement of employee awareness and training: In order to guarantee that environmental protection regulations are properly applied throughout the production process, aluminium die-casting companies must provide their staff with environmental protection training to raise their level of awareness and sharpen their operational skills.
Green manufacturing techniques, pollution reduction, and energy conservation:
The aluminium die-casting sector may lower energy consumption, cut emissions, and increase resource utilisation efficiency by using a number of green manufacturing and energy-saving techniques. Here are a few potential actions:
- Optimise process parameters: By carefully choosing the die-casting process’s parameters, you may cut down on energy use and raw material waste. For instance, maximising mould design, managing process variables like pressure and temperature, raising die casting certification rates, and lowering scrap rates.
- Energy recycling: To cut down on energy waste, recuperate and repurpose the waste heat from the aluminium die-casting process using waste heat recovery technology. For instance, die-casting moulds are heated or preheated using waste heat from the smelting furnace.
- Employ clean energy: To lessen reliance on fossil fuels, give priority to the use of clean energy in the manufacturing process, such as solar, wind, and other forms of energy.
- Increase equipment efficiency: Through technological advancements and equipment updates, die-casting machines and other manufacturing equipment may operate more efficiently while using less energy and resources. Use energy-saving devices, such as energy-saving lighting and high-efficiency motors, as an example.
- Boost production management: By making sensible preparations for production schedules, streamlining production procedures, and taking other steps, you may cut down on the amount of energy and resources used during production. Concurrently, we will bolster environmental oversight and management throughout the manufacturing process to guarantee that contaminants are efficiently handled and emissions adhere to regulations.
- Encourage the creation of a green supply chain: Aluminium die-casting businesses may work with suppliers to encourage eco-friendly materials and green manufacturing techniques, as well as to collaboratively accomplish sustainable development objectives.
- Innovation and continual improvement: Always look for new methods and tools, enhance and optimise the manufacturing process, increase the effectiveness of resource use, and use less energy. Employees are also urged to take part in creative projects, energy-saving techniques, and emission-reduction strategies in order to collectively support the company’s sustainable growth.
en conclusion
Aluminum die casting is a critical process that involves the selection of high-quality ingots that meet specifications and undergo strict quality control. The smelting and processing of aluminum alloys includes raw material preparation, heating and melting, adjusting melting temperature, composition adjustment, slag treatment, degassing treatment, controlling melting time, etc. Aluminum is a key material in the production of a variety of products, including molds. The process of conception de moules involves selecting and processing materials, ensuring they meet the required specifications, and are appropriately heat treated and surface treated. Aluminum die castings undergo a variety of surface treatment techniques to enhance their appearance and functionality. Die-casting aluminum is a rapidly evolving process that continues to evolve due to technological advances and market demand. The industry is exploring new materials to enhance the mechanical properties and corrosion resistance of die-casting parts. Intelligent production technology is continuously introduced to improve efficiency and product quality. The aluminum die-casting industry is also promoting eco-friendly manufacturing with the aim of reducing resource waste and environmental pollution. The industry is also exploring the application of aluminum die-casting technology in aerospace, automobile lightweighting, and new energy fields.