Aluminum casting molds play a crucial role in the process of aluminum casting. They are used to shape and form molten aluminum into desired objects or components. These molds are typically made from steel or other materials that can withstand high temperatures and pressure.
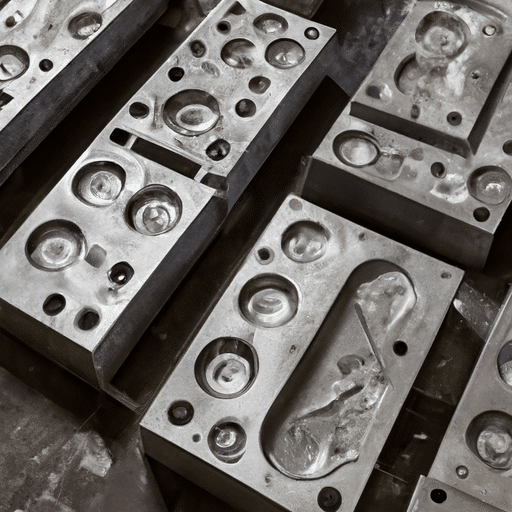
Types of Aluminum Casting Molds
There are several types of aluminum casting molds available, each designed for specific casting methods and applications. Let’s explore some of the common types:
1. Permanent Molds
Permanent molds, also known as metal molds, are made from steel or iron and are designed for repeated use. They are typically used for high-volume production of aluminum parts. The molds have cavities that are precisely machined to create the desired shape of the final product. Permanent molds offer good dimensional accuracy and surface finish.
2. Sand Molds
Sand molds are created by packing a mixture of sand and a binder around a pattern that represents the desired shape of the final product. The pattern is then removed, leaving a cavity in the sand mold. Molten aluminum is poured into the mold, filling the cavity and taking the shape of the pattern. Sand molds are commonly used for low to medium volume production and allow for more complex shapes compared to permanent molds.
3. Die Casting Molds
Die casting molds, also known as dies, are made from steel and are used in the die casting process. Die casting involves injecting molten aluminum into the mold at high pressure to quickly fill the cavity. This results in high production rates and excellent dimensional accuracy. Die casting molds are typically more expensive to produce but offer superior surface finish and tight tolerances.
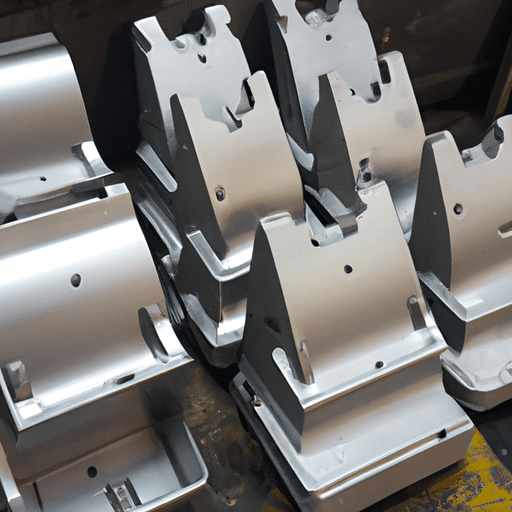
Detailed introduction of aluminum die casting mold
Main components of aluminum die casting mold
Die-casting molds made of aluminum are instruments used in the production of die-cast aluminum alloy components. To facilitate the creation of complicated pieces, these molds often include many different parts. The main elements of aluminum die casting molds are as follows:
- Die foundation: The mould foundation serves as the complete mold’s structural support system, supporting every other part. Typically, it is composed of robust elements like steel to guarantee the mold’s stability and longevity.
- Moving Die: Usually attached to the moveable portion of the die casting machine, the moving die is a movable component of the mold. It encompasses the form of aluminum components, which form their internal structure and outside surface.
- Fixed Die: Usually attached to the fixed portion of the die casting machine, the fixed die is a fixed component of the mold. It shapes the inside contour of the metal component and comprises its internal structure.
- Slides are moveable mould components that are often used to provide extra features to pieces with intricate forms. To make more projections or grooves in the mould, you may adjust the slider in a certain direction.
- Cores: The components used to create voids or holes within a part are called cores. Depending on how the component is designed, they may be permanent or detachable.
- Cooling System: During the die casting process, the cooling system regulates the mold’s temperature to guarantee that the material solidifies as intended. This often involves extra cooling apparatus or cooling water pipelines.
- Sprue and Runner System: Melted aluminum alloy is injected into the mold cavity using the nozzle system. The nozzle, guide channel, and other injection molding-related parts make up the nozzle system.
- Venting System: The air or gas produced as the aluminum alloy fills the mold is extracted using the venting system. By doing this, bubbles and other part flaws are reduced.
The geometry, size, and other specifications of the item being manufactured determine the design and arrangement of these components. Complex systems, aluminum die-casting molds need precise engineering and manufacturing procedures to guarantee the production of aluminum alloy die-cast components of superior quality.
Making of die-cast aluminum molds
Die-cast aluminum mold molding is an intricate and exact process that typically entails the following primary steps:
- Design: The design stage is when the molding process starts. Engineers must plan the mold’s dimensions, shape, and structure in accordance with the specifications for the finished product. This entails taking into account variables including exhaust, cooling, and material flow, among others.
- Material selection: High-strength, very wear-resistant alloy steel is often utilized to manufacture molds. The choice of material is influenced by the component specifications, manufacturing volume, and mold life.
- Processing module: Using the design drawings as a guide, mechanically process the chosen materials. This might include EDM, drilling, milling, CNC machining, and other procedures to create the mold’s numerous components, which include sliders, core pulls, static and moveable molds, and more.
- Assemble the modules that have been processed into a finished mold structure. To guarantee the precision and stability of the mold, make sure that every part is precisely positioned and fitted.
- Heat treatment: To increase the mold’s hardness and resistance to wear, heat treatment is used. Quenching, tempering, and other heat treatment techniques are chosen based on the requirements of the material used to make the mold.
- Surface treatment: To increase the mold’s surface smoothness and corrosion resistance, surface treatment techniques including mirror polishing and electroplating are used on a few critical mold components.
- Processing cooling channels: The efficiency of production and the quality of the aluminum components are increased when the mold’s temperature can be successfully regulated throughout the die-casting process.
- Apply lubrication: Mist the mold surface with lubricant to lower friction, prolong the life of the mold, and guarantee that the aluminum alloy material fills the mould uniformly.
- Testing and debugging: After installing the mold on the die-casting machine, carry out a number of tests. This entails modifying the cooling, exhaust, injection molding, and other systems to guarantee the mold can function correctly and provide aluminum components of superior quality.
In order to guarantee that the final die-cast aluminum mold can fulfill production demands and sustain high-quality component manufacture, the aforementioned procedures are not linear and often call for numerous iterations and revisions.
Benefits of Aluminum Casting Molds
Using aluminum casting molds offers several advantages in the manufacturing process:
1. Design Flexibility
Aluminum casting molds allow for the production of complex shapes and intricate details that may be difficult or costly to achieve using other manufacturing methods. This makes them suitable for a wide range of industries and applications.
2. Cost-Effective Production
Aluminium casting molds can be used for high-volume production, making them a cost-effective option for mass manufacturing. The molds can be designed for efficient cooling and cycle times, further reducing production costs.
3. Excellent Surface Finish
Aluminum casting molds can produce parts with a smooth and uniform surface finish, eliminating the need for additional finishing processes. This saves both time and money in the production process.
4. Material Versatility
Aluminium casting molds can be used with a variety of aluminum alloys, allowing manufacturers to choose the most suitable material for their specific application. This flexibility ensures that the final product meets the required strength, durability, and other performance requirements.
Kesimpulan
Aluminum casting molds are essential tools in the aluminum casting process. Whether it’s permanent molds, sand molds, or die casting molds, each type offers unique benefits and is suitable for different production volumes and requirements. The use of aluminum casting molds enables manufacturers to create complex shapes, achieve cost-effective production, and produce parts with excellent surface finish. With their versatility and efficiency, aluminum casting molds continue to be a popular choice in various industries.
What is the best mold for casting aluminum?
The optimum mold for casting aluminum is determined by a number of parameters, such as the casting project’s particular needs, the part’s complexity, production volume, and financial constraints. The following are a few typical mold kinds for casting aluminum:
Steel Molds:
Advantages: Steel molds are strong, long-lasting, and resistant to high pressure and temperatures. They work well with complicated component geometries and large volume manufacturing.
Cons: Compared to other materials, steel molds typically have a longer manufacturing lead time and may be costly to create.
Cast Iron Molds:
Advantages: Cast iron molds feature superior heat conductivity and are reasonably priced. They work well for production volumes ranging from medium to high.
Cons: It could be difficult to obtain complex component geometries, and they might not be as robust as steel molds.
Graphite Molds:
Advantages: Quick cooling is made possible by the superior heat conductivity of graphite molds. They work well for complex component designs and modest to medium-sized manufacturing runs.
Cons: Graphite molds are prone to wear out over time, particularly with high-volume manufacturing, and are less resilient than steel or cast iron molds.
Sand Molds:
Advantages: Sand molds are economical and appropriate for manufacturing in low to medium quantities. They may be applied to intricate component geometries and are also quite flexible.
Cons: Compared to metal molds, sand molds could not provide the same degree of surface quality and dimensional precision. Usually, they are used in less important applications.
Plaster Molds:
Advantages: Plaster molds are good for small-scale manufacturing and prototyping since they are reasonably priced.
Cons: Their temperature resistance may be limited, and they are not as strong as metal molds.
Investment (Lost Wax) Molds:
Advantages: Investment casting molds can create complex, finely detailed items with a smooth surface. They work well for production volumes ranging from small to medium.
Cons: Compared to other mold types, they might be more costly and time-consuming to make.
The ideal mold selection is determined by the particular needs of the aluminum casting project and is often determined by striking a balance between a number of variables, including cost, production volume, component complexity, and desired quality. Working closely with knowledgeable engineers and mold manufacturers is essential to choose the best mold for the intended use.
What kind of mold is used for aluminum?
When casting aluminum, a variety of mold types are often employed; the selection of one type over another is influenced by several criteria, including the part’s complexity, production volume, economic concerns, and the desired final product quality. The following are a few typical mold kinds for casting aluminum:
1. Molds made of steel:
Steel molds are suited for complicated component geometries and large-volume manufacturing because of their durability and ability to endure high temperatures and pressures.
Benefits include a long lifetime, superior surface polish, and dimensional precision.
Applications: Die casting and permanent mold casting are two common uses for it.
2. Sand Molds:
The process of creating sand molds involves packing sand tightly around a template to create the mold’s interior. They are adaptable for casting a variety of forms and are usually utilized for lower-volume manufacturing.
Benefits include affordability, suitability for intricate forms, and versatility in terms of casting sizes.
Applications: Sand casting is a common process used to produce aluminum castings, particularly bigger pieces.
3. Molds made of graphite:
Graphite molds have strong heat conductivity and are often formed of graphite or a combination of graphite and other materials. Small to medium-sized manufacturing runs are appropriate for them.
Benefits include quick cooling, suitability for complex component designs, and affordability.
Applications: For the casting of more complex and smaller aluminum pieces.
4. Missing Foam Molds:
The process of lost foam casting entails making a foam design that has been covered with refractory material. After that, sand is placed around the foam design, and during casting, molten metal is used to replace the foam.
Benefits include excellent surface quality, less machining needs, and good performance with complicated and near-net-5. 5. shape items.
Applications: Ideal for aluminum castings that call for complex designs and lightweight constructions.
5. Metal or die-casting permanent molds:
Description: Consistent and repeatable aluminum components are produced in large quantities using permanent molds, which are usually composed of steel.
Benefits include rapid production speeds, good dimensional accuracy, and suitability for intricate forms.
Applications: Frequently used in gravity and aluminum die casting procedures.
6. Molds made of ceramic:
Ceramic molds are used for precise casting of complex pieces, and they are constructed from refractory materials.
Benefits include less machining needs, excellent accuracy, and a smooth surface finish.
Applications: Fit for aluminum investment casting.
The particular needs of the casting project will determine the sort of mold to use, and often, a number of considerations may come into play. When choosing the right mold, manufacturers take into account a number of aspects, including the complexity of the item, the volume of production, the cost, and the required quality of the finished aluminum casting.
What is the Mould material for Aluminium casting?
A number of variables, such as the casting procedure, the intended component quality, the volume of production, and economic concerns, influence the choice of mold material for aluminum casting. The following are some typical mold materials for casting aluminum:
Steel:
Aluminum casting is a common use for steel molds, which are often composed of tool steels like H13. They are very durable and resistant to the high pressures and temperatures involved in the casting of aluminum.
Benefits include great heat conductivity, exceptional durability, and suitability for large-scale manufacturing.
Applications: Applied in some sand casting applications as well as die casting and permanent mold casting.
Iron Cast:
Cast iron molds have excellent heat conductivity and are reasonably priced. They work well for less complicated components and medium-volume manufacturing.
Benefits include low cost, excellent heat conductivity, and suitability for permanent mold casting applications as well as sand casting.
Applications: Frequently used in gravity die casting and sand casting.
Graphite:
Graphite dies and molds, which are often composed of graphite mixed with other materials, have a high heat conductivity. Small to medium-sized manufacturing runs are appropriate for them.
Benefits include quick cooling, suitability for complex component designs, and affordability.
Applications: Applied to a number of casting techniques, such as investment casting and die casting.
Ceramic:
Description: Refractory materials like silica, alumina, or zirconia are used to make ceramic molds. Precision casting procedures often employ them.
Benefits include less machining needs, excellent accuracy, and a smooth surface finish.
Applications: Frequently used in aluminum investment casting.
Sand:
Sand molds, fabricated from silica sand or other molding sands, provide both affordability and adaptability. They are often used in production of low to medium volumes.
Benefits include affordability, suitability for intricate forms, and versatility in terms of casting sizes.
Applications: Often used in the sand casting process for different aluminum products.
Plaster:
Plaster molds are a cost-effective solution for small-scale manufacturing and prototypes.
Benefits: Low-cost alternative for prototyping and small volumes.
Applications: When cost is a major factor, used for bespoke or creative casting.
The exact specifications of the casting project, the casting method used, and other elements like component complexity, production volume, and financial considerations all have a role in the mold material selection. To guarantee the manufacturing of high-quality aluminum castings, it is crucial to take into account the mold material’s thermal characteristics, wear resistance, and general durability.
How do you mold and cast aluminum?
There are several phases involved in molding and casting aluminum, and the procedure might change according on the casting technique used. Die casting and sand casting are two popular techniques for casting aluminum. This is a broad synopsis of the procedures:
Sand Casting:
Creating Patterns:
Make a blueprint out of wood, metal, or plastic for the needed portion. The final part’s precise negative form should be represented in the pattern.
Mold Readying:
To create a mold cavity, place the design within a box and cover it with a particular molding sand. For more intricate forms, this mold may be divided into two parts: the cope and the drag.
Elimination of Patterns:
With extreme care, remove the pattern, leaving a hollow in the sand that resembles the required part’s form.
Aluminum Melting:
Heat aluminum to the appropriate temperature in a furnace. Depending on the individual aluminum alloy being utilized, the temperature may change.
Dispensing:
Fill the mold cavity with the molten metal. Let it cool and become solid.
Elimination and Polishing:
Take the casting out of the mold when the metal has hardened. When necessary, carry out finishing procedures like surface treatment or machining to remove any extra material.
Die Casting:
Die Design:
Create a die or mold with two parts that, when closed, will reveal a hollow shaped like the finished product.
Die Production:
Make the die out of steel or other materials. To guarantee accuracy and longevity, the die is machined with precision.
Aluminum Melting:
In a furnace, melt the aluminum alloy to the precise temperature needed for die casting.
Injectable:
Apply intense pressure as you inject the molten metal into the die. In addition to facilitating speedy mold filling, pressure guarantees an exact and precise cast.
Dissipation:
Give the metal in the die time to cool and solidify. The part’s ability to retain its structural integrity depends on the cooling period.
Removal:
Expel the solidified aluminum portion by opening the die. For the next casting, the cycle is then repeated.
Finalizing and Trimming:
Remove any surplus material from the cast component and carry out further finishing procedures as required.
General Advice for Casting Aluminum:
Safety: When handling molten metal, always take the appropriate safety precautions.
Temperature Control: To guarantee correct casting, keep an eye on and regulate the molten aluminum’s temperature.
Metal Preparation: To enhance the casting quality, purge the aluminum of impurities and degas if required.
Tooling Maintenance: To keep molds or dies in excellent shape, check and maintain them on a regular basis.
Remember that the particulars of the procedure could change depending on the tools, supplies, and volume of the product. When working on aluminum casting projects, it’s best to refer to comprehensive casting instructions or speak with knowledgeable experts.