The automotive industry is facing a revolution in technology and design aimed at improving vehicle performance and easing fuel consumption while reducing emissions and environmental impact. On this evolutionary path, aluminum die castings are at the forefront, providing automakers with unlimited room for innovation. MINDWELL is a professional aluminum die-casting manufacturer. This article will explore the manufacturing process of aluminum die-casting parts, their wide range of applications, and how they will shape future automotive design.
Aluminum die casting technology
Aluminum die-casting is a modern manufacturing process that allows aluminum alloys to be heated to a liquid state and then injected into a precise mold. The aluminum alloy then cools and forms the required parts, which feature complex geometries and superior strength. Key advantages of aluminum die-casting technology include high precision, speed, material strength, and lightweight design.
Additionally, the choice of aluminum alloy is critical during the manufacturing process, as different alloys can provide different properties to suit different automotive applications.
Applications in the automotive industry
Aluminum die castings have a wide variety of applications in the automotive industry, including but not limited to:
- Body and chassis components: Aluminum alloys are widely used in automobile body and chassis components, such as suspension brackets, frame components, chassis covers, etc. The use of these parts reduces vehicle weight and improves fuel efficiency while maintaining strength and durability.
- Engine and Powertrain Components: Aluminum die castings play a key role in automotive engines and powertrains. This includes critical components such as radiators, oil pans, manifolds, and more. They are designed and manufactured with high precision to ensure engine performance and efficiency.
- Interior and exterior design: In addition to mechanical parts, aluminum die-casting also plays a role in the interior and exterior design of cars. Parts such as engine hoods, door handles, and dashboard brackets are manufactured using aluminum die-casting technology, which not only provides aesthetics but also lightweight and reliability.
These applications demonstrate how versatile and critical aluminum die castings are in automotive design. The use of aluminum die castings has fueled the automotive industry and has a positive impact on vehicle performance, efficiency, and sustainability. In addition to the aluminum die-cast parts mentioned above, our company also customizes the automotive aluminum die-cast parts required by customers.
Advantages and benefits
Aluminum die castings offer many advantages and benefits in automotive manufacturing, some of which include:
- Light weight and high strength: Aluminum alloys play a key role in lightweight design in car manufacturing. It is lighter than steel while offering excellent strength, which can reduce overall vehicle weight, increase fuel efficiency, and provide better performance.
- Corrosion resistance and wear resistance: Aluminum alloys have corrosion resistance and wear resistance, allowing them to operate in various harsh conditions, reducing corrosion and wear of parts and extending the service life of parts.
- Manufacturing Efficiency and Cost Effectiveness: Aluminum die casting technology is fast and efficient, reducing manufacturing costs. This is because it can produce parts in bulk, reducing waste in the manufacturing process and improving production efficiency.
- Sustainability and environmental benefits: Aluminum is a recyclable material that helps reduce resource waste. At the same time, due to the adoption of lightweight design, aluminum die-cast parts can reduce the fuel consumption of the entire vehicle, reduce emissions, and help protect the environment.
These advantages make aluminum die-casting technology the first choice for car manufacturers, driving innovation in car design and manufacturing.
design & engineering
The success of automotive aluminum die castings is closely tied to design and engineering. Making these parts requires
Precise design, structural analysis, and simulation. During the engineering verification and testing phase, it is ensured that components can meet the performance and safety standards required to meet the requirements of the automotive industry.
Actual case studies
Let’s take a look at some of our company’s automotive aluminum die-casting case studies to see how Mindwell uses aluminum die-casting to improve vehicle performance and fuel efficiency. For example, the car radiator we made is a successful case, and there are also some other aluminum die-cast parts.The picture below is an aluminum die-cast heat sink:
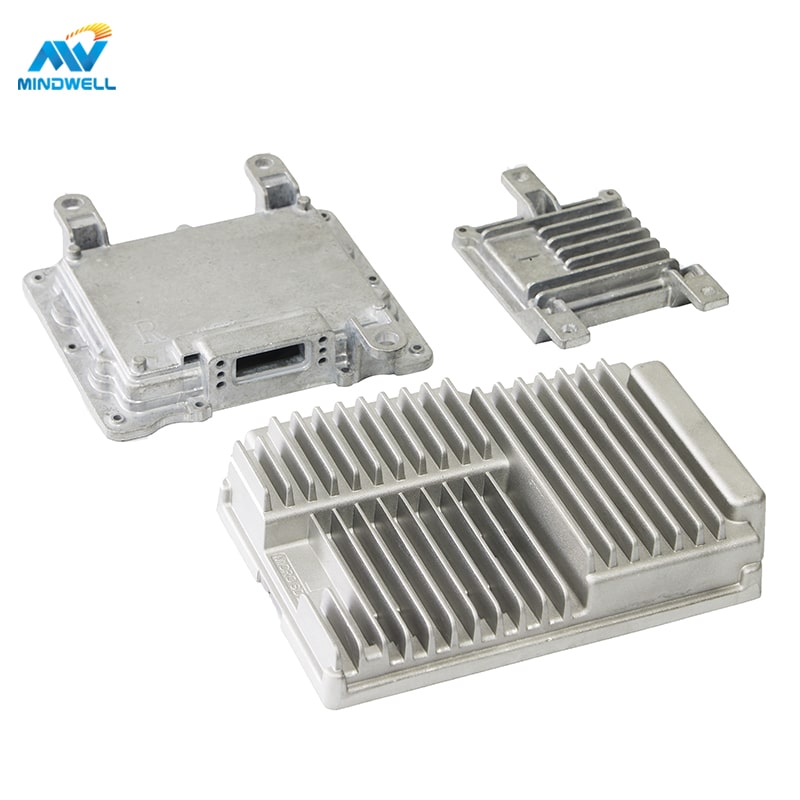
Challenges and future trends
While aluminum die castings offer many advantages in automotive manufacturing, they also come with some challenges. Some of these challenges include sustainability issues such as material recycling and energy consumption, as well as ever-changing regulations and safety standards. However, future trends show that aluminum die-casting technology will continue to develop and innovate. Digital manufacturing, lightweight design and more advanced alloys will drive further advancements in this technology, improving vehicle performance, efficiency and sustainability.
Conclusione
Aluminum die casting has become the core technology of modern automobile manufacturing, and its widespread application has improved automobile performance, reduced fuel consumption, and reduced automobile emissions and environmental impact. In the future, we can expect to see more innovations and developments, allowing aluminum die-casting technology to continue to play a key role in automotive design and manufacturing. This technology has exciting prospects and is expected to bring more breakthroughs and improvements to the automobile industry.