Plastic products are various items, components, or products made of plastic materials. Plastic is an extremely malleable material that comes in many different types and properties, allowing products to be manufactured in a variety of shapes, sizes, and uses.
Injection molding is one ofthe moste commonly used processes for manufacturing plastic products. The plastic is melted through hot melt injection and injected into the mold. After cooling, the product in the desired shape can be obtained. There are a wide variety of plastic products produced by this process. In addition to the common plastic products in daily life, they are also widely used in industrial and medical fields. With the development of science and technology, injection-molded plastic products will have more extensive applications in various fields.
Plastic products of different shapes and types
If divided according to the type of packaging of plastic products, common plastic products include shells, pipes, covers and spare parts. These products are lightweight, convenient, low-cost, and can meet the needs of different industries for product size and geometry.
1. Plastic shell
Plastic housing is one of the most common plastic products made by injection molding. It is characterized by being light and easy to process into different shapes, and can be produced into products of various sizes and geometric shapes, such as mobile phone casings, TV casings, air conditioner casings, etc. Plastic casings are shockproof, waterproof, and anti-corrosive and are widely used in electronics, communications, home appliances, medical, and other fields.
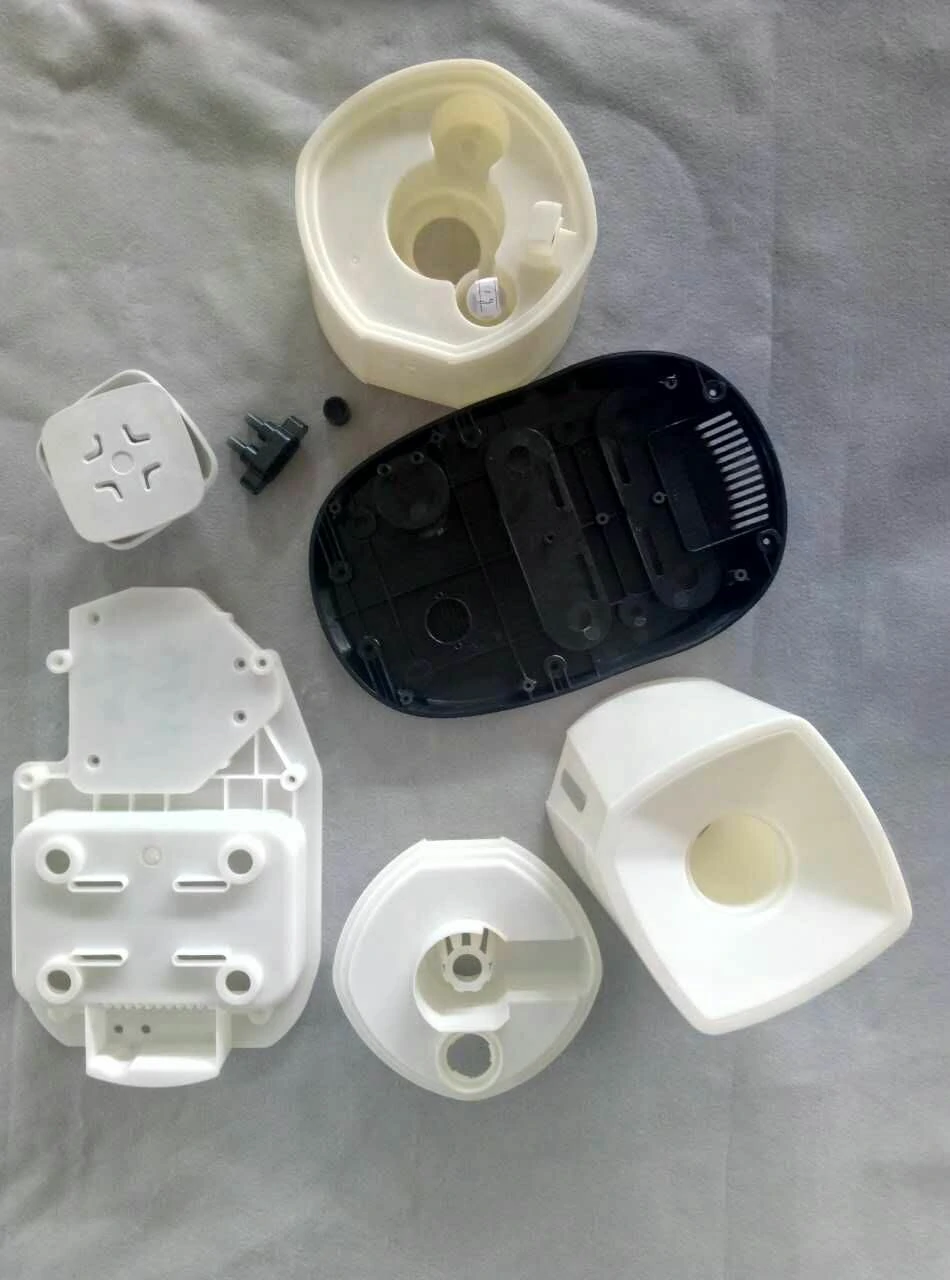
2. Plastic pipes
The injection molding process can produce various types of plastic pipes, including water pipes, gas pipes, sewage pipes, etc., made of PVC, PE, PP, ABS and other materials. These plastic pipes have the characteristics of a long service life, a low price, and convenient construction. They are widely used in construction, municipal administration, the chemical industry, light industry, and other fields.
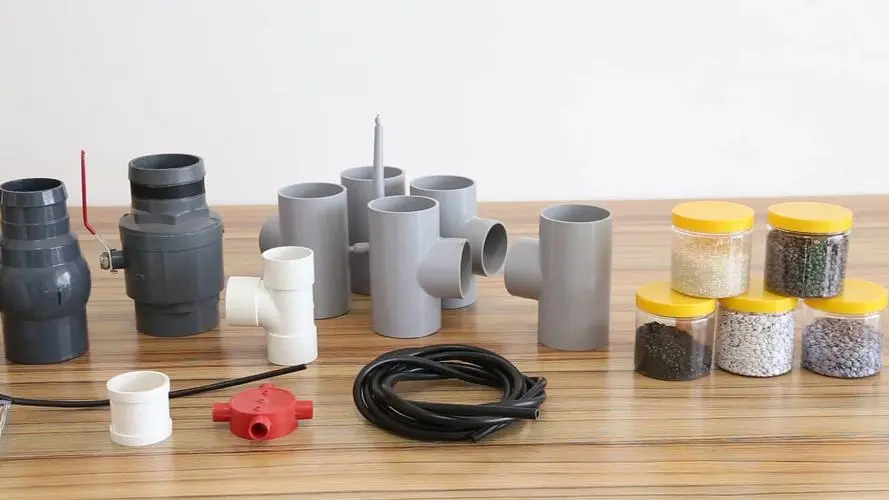
3. Plastic lid
Plastic lids are a common plastic product made by injection molding and are widely used in food, beverage, pharmaceutical, and other industries. It has the advantages of being lightweight, low-cost, and hygienic compared to metal lids, and plastic lids of various sizes and shapes can be customized according to product needs. Plastic lids manufactured by the injection molding process can also be processed with various decorative effects, such as spraying, silk screen, etc.
4. Plastic spare parts
In addition to the above three common plastic products, the injection molding process can also manufacture a variety of plastic parts, such as switches, plugs, sockets, auto parts, etc. These plastic parts have uniform specifications, good processing performance, and low cost, and are widely used in electronics, home appliances, automobiles, and other industries.

Plastic products produced by different injection molding processes
(1) Injection molding
The principle of injection molding is that plastic raw materials are added to the hopper of the injection machine. The raw materials are heated and melted and enter the mold cavity under the high pressure of the injection molding machine. The injection molded product is then hardened and shaped in the mold cavity. Examples of injection molded plastic items:
- Industrial Products
- Kitchen supplies (trash cans, bowls, buckets, pots, cutlery, and various containers)
- Housings for electrical equipment (hair dryers, vacuum cleaners, food mixers, etc.)
- Toys & Games
- Various products for the automotive industry, parts for many other products, etc.

(2) Insert injection molding
The insert is pre-fixed in an appropriate position in the injection mold, and then plastic is injected into the mold. After the mold is opened, the insert is tightly wrapped and embedded in the plastic with cooled and solidified plastic to obtain a product with inserts such as threads and electrodes. Examples of plastic products with insert injection molding:
- Electronics Enclosures: Electronic devices have metal or plastic parts embedded in their enclosures to provide shielding, thermal conductivity, or mechanical support.
- Automotive parts: Automotive light housings, sensor brackets, connectors, etc.
- Medical Devices: Medical devices may contain embedded electronic components or sensors within their housings.
- Home appliances: casings of home appliances such as washing machines, microwave ovens, refrigerators, etc.
- Industrial Equipment: Industrial equipment has electronic components embedded in its control panels or operating components.
- Power Engineering: Components of power engineering equipment, such as plugs, sockets, switches, etc.
- Consumer products: flashlights, remote controls, toys, etc.
- Communications equipment: Communications equipment may have antennas or connecting parts embedded in the housing.
- Aerospace: In aerospace, aircraft components may contain embedded sensors or monitoring devices.
- Electronic accessories: Circuit boards, connectors, sensors, etc. may be embedded in electronic accessories.

(3) Two-color injection molding
Two-color injection molding refers to a molding method that injects two different colors of plastic into the same mold. It can make plastic appear two different colors, and can make plastic parts show regular patterns or irregular moiré-like colors to improve the usability and beauty of plastic parts. Examples of plastic products produced by double-color injection molding:
- Multi-color plastic parts: colorful mobile phone casings, TV remote controls, keyboards, mice, etc.
- Two-color plastic tableware: knives, forks, spoons, bowls, cups, etc. of different colors or materials.
- Car interior parts: Car interior parts, such as dashboards, door panels, seat accessories, etc.
- Medical equipment parts: syringe housings for medical equipment, medical instrument accessories, etc.
- Toys: Manufacture of colorful toys, building blocks, puzzles, etc.
- Electronic product accessories: cell phone cases, headphone cases, chargers, etc.
- Household items: Household items such as vases, decorations, home accessories, etc.
- Industrial Equipment Accessories: Industrial equipment may require accessories in different colors or materials
- Outdoor supplies: multi-color tents, backpacks, kettles, etc.
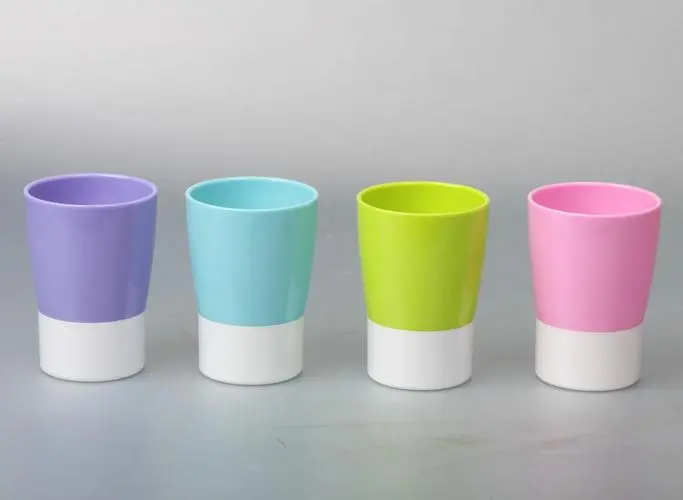
(4) Micro-foam injection molding process
Micro-foam injection molding process is an innovative precision injection molding technology that relies on the expansion of pores to fill the product and completes the molding of the product under low and even pressure. Examples of plastic products produced by micro-foam injection molding process:
- Packaging materials: Lightweight packaging materials, such as foam boxes, protective pads, liners, etc., used to package fragile items such as glass, electronic products, ceramics, etc.
- Insulation: Insulation materials for buildings and cooling equipment such as insulation panels, pipe insulation, roof insulation, etc.
- Automotive interior parts: Manufacture of lightweight interior parts such as instrument panels, door panels, seat cushions, headliners, etc. to reduce vehicle weight and improve insulation properties.
- Toys and Games: Manufactures lightweight toys and games such as flying machines, buoys, swim boards, beach toys, etc.
- Outdoor products: In the outdoor field, microfoam injection molding can be used to make lightweight tents, sleeping bags, mountaineering backpacks, picnic mats, etc.
- Furniture: Manufacture of furniture components such as chair cushions, sofa cushions, mattresses, etc. to provide additional comfort and insulation properties.
- Electronic product casing: In electronic product manufacturing, micro-foam injection molding can be used to manufacture lightweight casings, such as mobile phone casings, tablet computer casings, audio casings, etc.
- Sports goods: Midsoles in sports shoes, racket handles, bicycle seats, etc., can use microfoam injection molding to reduce weight and provide cushioning properties.
- Home Furnishings: Manufacture of household furnishings such as flower pots, trash cans, chair seat cushions, etc.
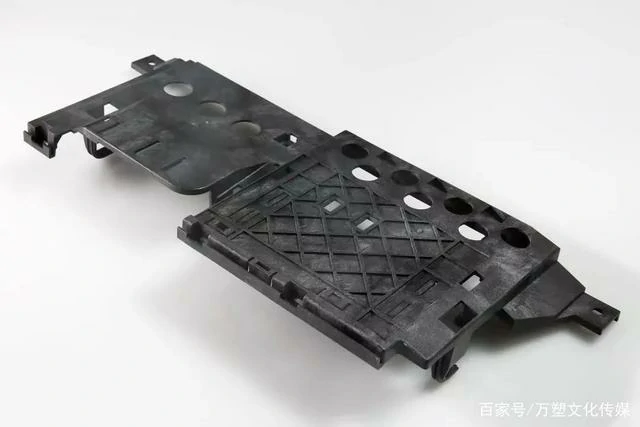
(5) Nano injection molding (NMT)
Nano-injection molding is a high-precision injection molding technology that uses nano-scale particles or additives to improve the performance and characteristics of plastic products. Examples of NMT plastic products:
- Nanocomposites: Create nanocomposites with higher strength and better wear resistance for use in automotive parts, aerospace components, sports gear and more.
- Medical devices: artificial joints, medical instrument casings, medicine dispensers, etc. to improve their biocompatibility and performance.
- Electronic products: Manufacturing of micro electronic product parts, such as micro sensor casings, chip packaging materials, flexible circuits, etc.
- Optical Components: Manufacture of high-precision optical components, such as lenses, lenses, laser components, etc., for use in laser technology, optical communications and imaging equipment.
- Nanoparticle Filters: Used in water purification, air filtration and biomedical applications.
- Battery technology: Li-ion battery separators, battery electrolytes, battery casings, etc.
- Micro fluidic equipment: micro pumps, micro valves, microfluidic chips, etc.
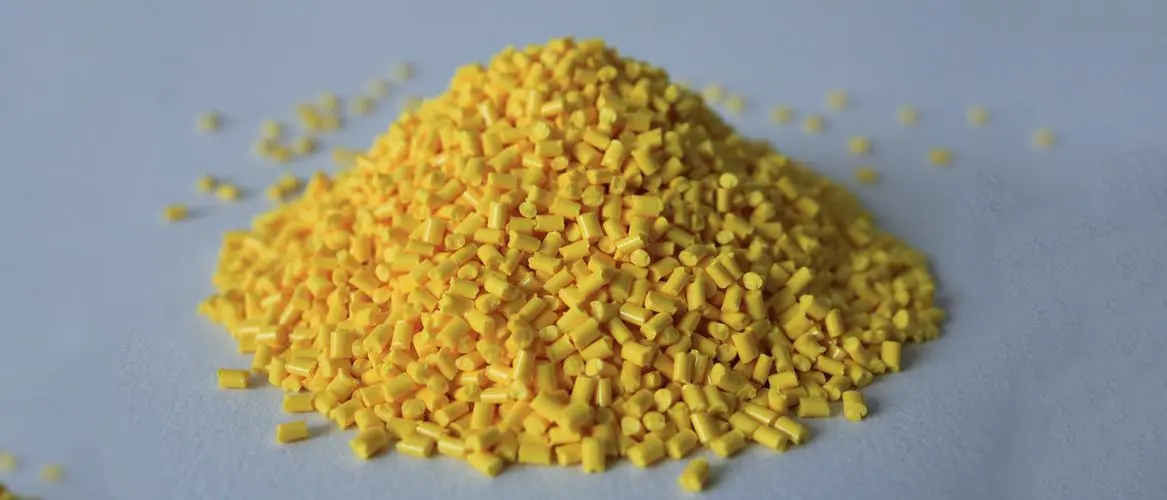
Advantages and Disadvantages of Using Injection Molding to Produce Plastic Products
advantage
- High tolerance repeatability.
- A wide range of materials can be used.
- Low labor cost.
- Minimal waste loss.
- There is no need to continue to perfect the parts after molding.
shortcoming
- Expensive equipment investment.
- Running costs can be high.
- Parts must be designed according to specific molding requirements.
In conclusion
Through the above-mentioned different applications of plastic product types and injection molding process types, we understand which plastic products are made by injection molding.plastic Injection molding products are widely used and can be seen everywhere in our daily lives. Plastic products made by injection molding are also widely used in many industrial equipment, home appliances, and furniture. Injection molding technology has affected our lives. With the development of science and technology, the lightweight and some properties of plastic products are getting closer to metal. I believe that more injection molding products will be used in life in the future.