アルミダイカスト
Aluminum die-casting is a process in which molten aluminum alloy liquid is injected into a mold using high pressure, and then solidified, cooled and other processes are used to obtain aluminum alloy die-casting parts. Aluminum alloy has good fluidity and processability, which is conducive to the production of high-quality aluminum alloy products.
- Aluminum die-casting products have high shape complexity
- Can produce large and small sizes, high strength and lightweight aluminum alloy parts
- The cost is low, the cycle is short, and it can be produced in batches.
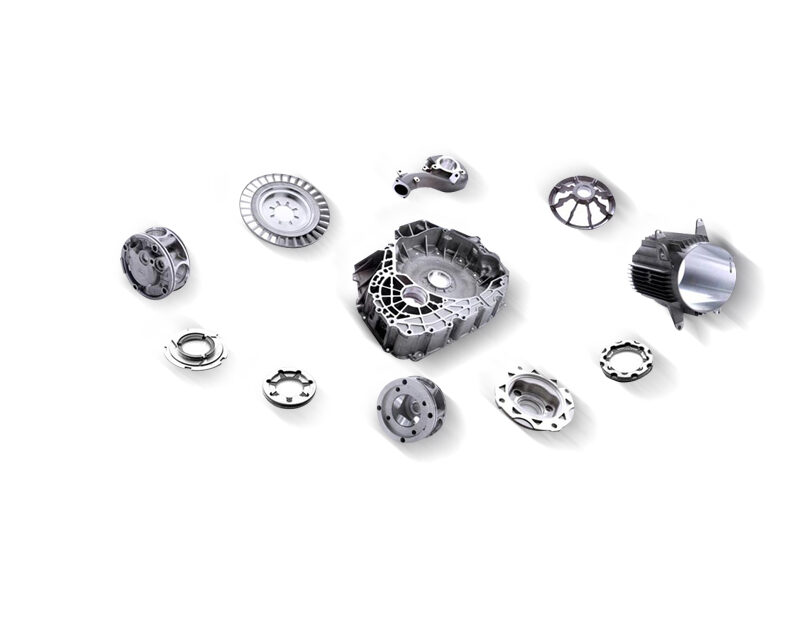
カスタマイズサービス
Our Aluminum Die Casting Process
The process selection of アルミダイキャスト is selected according to the required part design. For example, die casting is more suitable for the production of small and medium-sized and complex aluminum alloy castings. Gravity die casting is more suitable for the production of large and simple aluminum alloy castings. According to the use of parts, we can also carry out subsequent processing and processing of castings to improve the quality and performance of products.

Aluminium High Pressure Die Casting
Liquid aluminum is filled into the die-casting cavity at a high speed under high pressure, and the metal or alloy is solidified under pressure to form a casting method. The commonly used pressure in die casting is 4-500MPa, and the metal filling speed is 0.5-120m/s. Therefore, the filling time of the molten metal is very short, and the cavity can be filled within about 0.01-0.2 seconds (depending on the size of the casting).
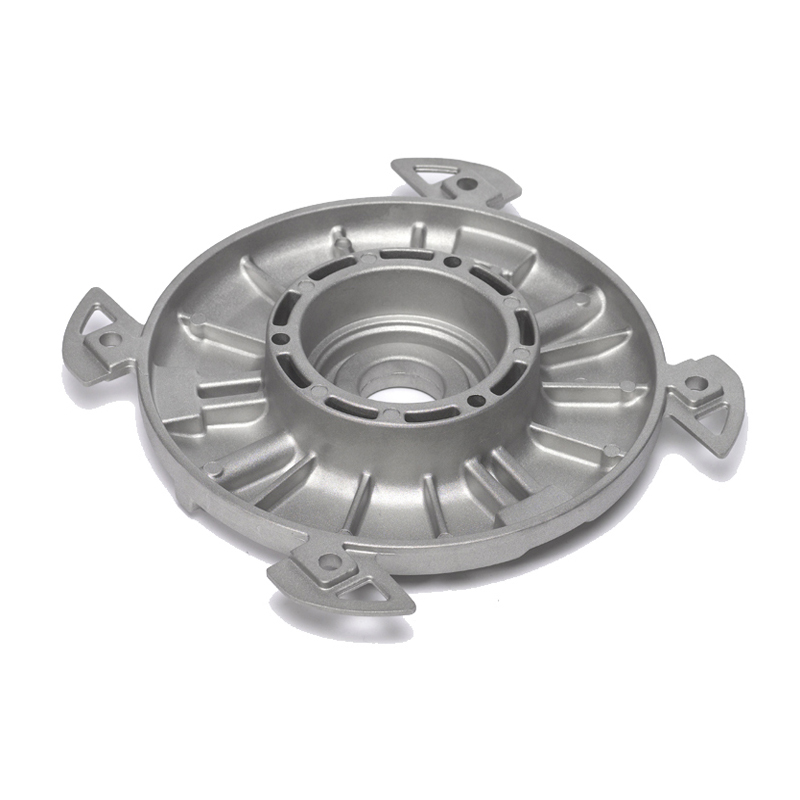
Aluminum Low Pressure Die Casting
Under the action of gas pressure, the aluminum metal liquid rises along the riser pipe into the sprue, enters the cavity through the ingate smoothly, and maintains the gas pressure on the liquid surface in the crucible. until the casting is fully solidified. Then the gas pressure on the liquid surface is released, allowing the unsolidified molten metal in the riser to flow back to the crucible.
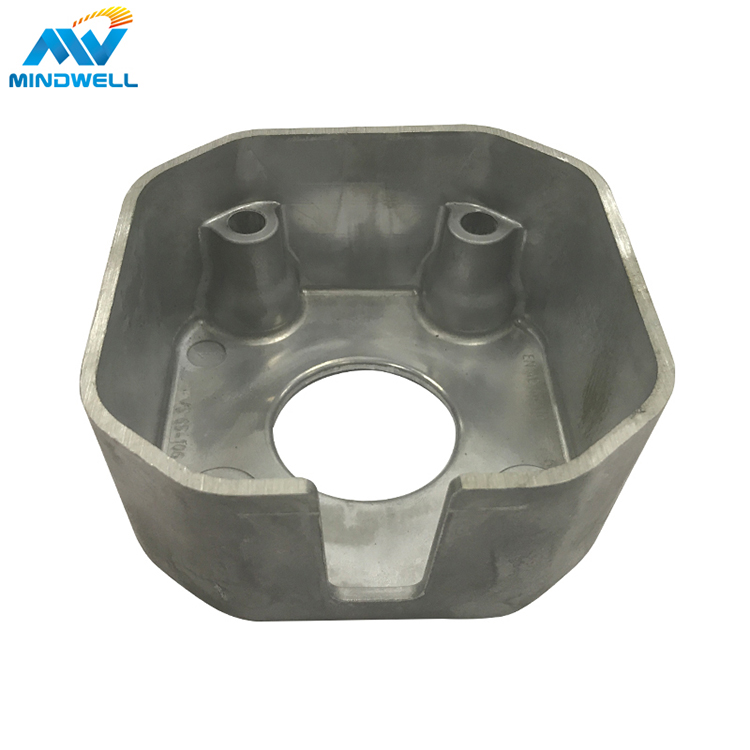
Aluminum gravity die casting
The molten aluminum of gravity casting is generally poured into the gate, and the cavity is filled by the self-weight of the molten metal, exhausted, cooled, and the mold is opened to obtain the sample. Metal mold casting can be divided into vertical manual casting, and inclined casting is now the most widely used metal mold (steel mold) casting.

Aluminum Die Cast Mold
The advantages of aluminum alloy material die-casting molds are high production efficiency, low cost and good product quality. It can manufacture qualified aluminum alloy parts and products in a short time. Aluminum alloy material die-casting mold is an efficient and cost-effective manufacturing tool. It is widely used not only in the automotive, electronics, machinery and other industries, but also in other fields.
How To Choose Aluminum Die Casting Materials
The selection of suitable aluminum alloy material is very important for the production of aluminum alloy die-casting parts. When selecting the steel material of aluminum alloy die-casting mold, the deformation and anti-expansion performance of the material at high temperature should be taken into consideration to ensure the production efficiency and quality of aluminum alloy die-casting mold.
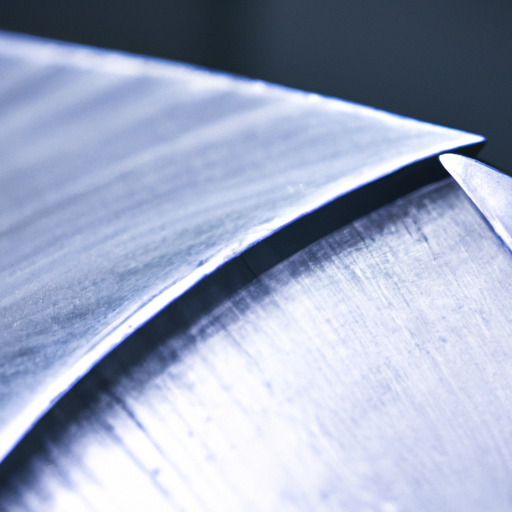
A380
A380 aluminum alloy die-casting is one of the most widely used aluminum alloy materials. It has a perfect combination of casting and mechanical properties; it also has excellent fluidity, air tightness, thermal crack resistance and machinability
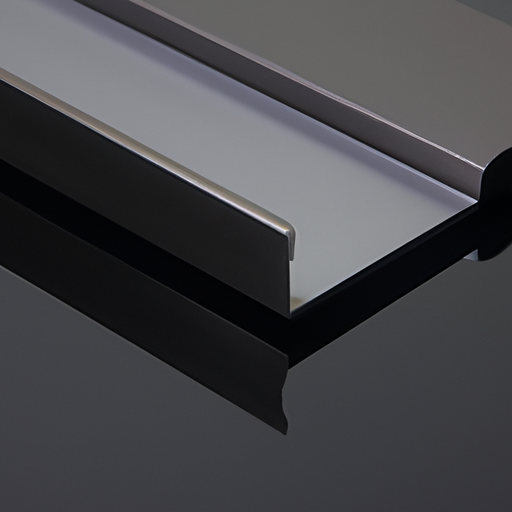
A360
The A360 aluminum alloy material is easy to compression molded. Because of its ease of casting, it is an excellent choice for parts that require complex designs. Its lightweight properties and resistance to corrosion make it an attractive option for products that need a durable but not too heavy.
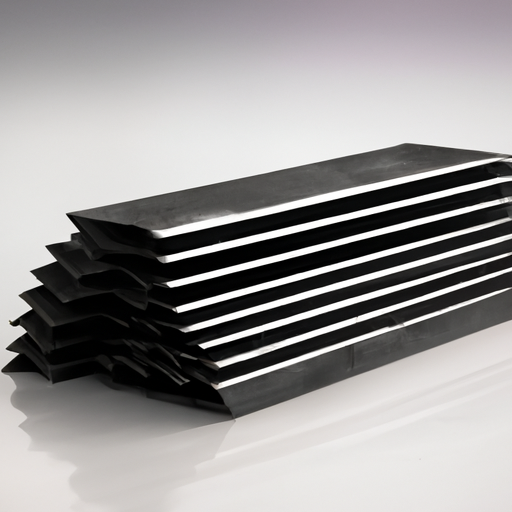
A356
A356 casting offers several advantages including cost-effectiveness, flexibility and excellent mechanical properties. It also has a good surface finish, which can produce high-quality parts that require less secondary operations. A356 becomes the perfect material for marine industry applications.

ADC12
ADC12 aluminum alloy material is an aluminum-silicon alloy with good castability, mechanical properties and corrosion resistance, and is widely used in the fields of automobiles, motorcycles, electrical appliances, mechanical equipment and so on.
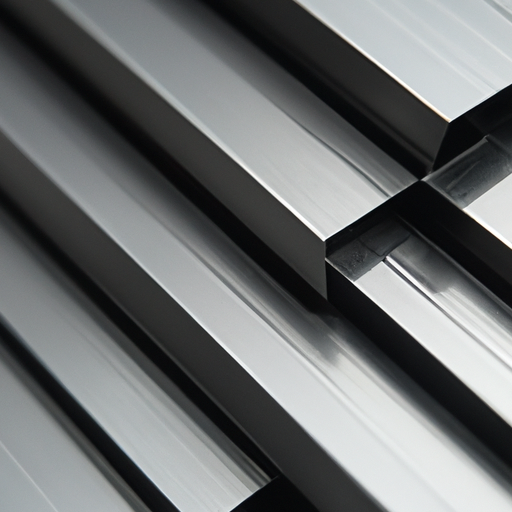
ADC10
ADC10 aluminum alloy material is a versatile and cost-effective material that can also be used in harsh environments due to its excellent corrosion resistance. ADC10 alloy material is also light weight and ductile, which makes it easy to machine and weld.

A413
A413 is an aluminum alloy with high silicon content, typically around 12%, and its excellent strength-to-weight ratio, corrosion resistance and good machinability make it an excellent choice for highly complex parts requiring intricate details.
Mindwell is an aluminum die-casting manufacturer that integrates mold opening, die-casting and processing. The company has experienced technical staff, excellent die-casting processing equipment, is an aluminum alloy die-casting manufacturer with advantages in the field.
Hot chamber die casting machine
The hot chamber die casting machine is a process in which metal materials are heated to a liquid state and then injected into a mold to form the desired product under high pressure. Hot chamber die-casting machines are usually suitable for situations where production needs are large and can achieve continuous production. Since aluminum alloys are prone to oxidation, the hot chamber die-casting machine needs to add protective gas during production to protect the service life of the aluminum alloy and mold, but the production cost is also relatively high.
Cold chamber die casting machine
The cold chamber die casting machine adopts a “pre-casting” manufacturing process, which first heats the metal material to a liquid state, then pours it into a pre-casting furnace for casting, and finally uses water cooling to form the desired product. Cold chamber die casting machines are generally suitable for situations where the production demand is small, and are usually used when the structure of the product produced is more complex. Compared with hot chamber die casting machines, its production cost is lower, but there is also the problem of relatively low production efficiency.
Which type of aluminum alloy die casting machine to choose needs to be selected according to specific production needs. If large-scale, efficient, continuous production is required, a hot chamber die-casting machine is usually chosen; and if small, low-cost production is required, a cold-chamber die-casting machine is usually selected.

Parameter setting
When performing die-casting molding, it is necessary to select the appropriate temperature, pressure and speed for processing according to different product materials and shapes. In addition, factors such as the physical and chemical properties of the molten aluminum alloy, cooling of the mold, etc. also need to be considered. Finally, post-processing of the product is required, including deburring, grinding, spraying and other steps to achieve the expected appearance and functional effects.
Mold making
Mold making is one of the most complex and time-consuming aspects of aluminum alloy die casting. The quality of molds directly affects the accuracy and surface finish of products. Therefore, precise control of materials, processing techniques, dimensions and deviations is required during the manufacturing process. At the same time, strict inspection and testing are also needed to ensure the quality and stability of the mold.
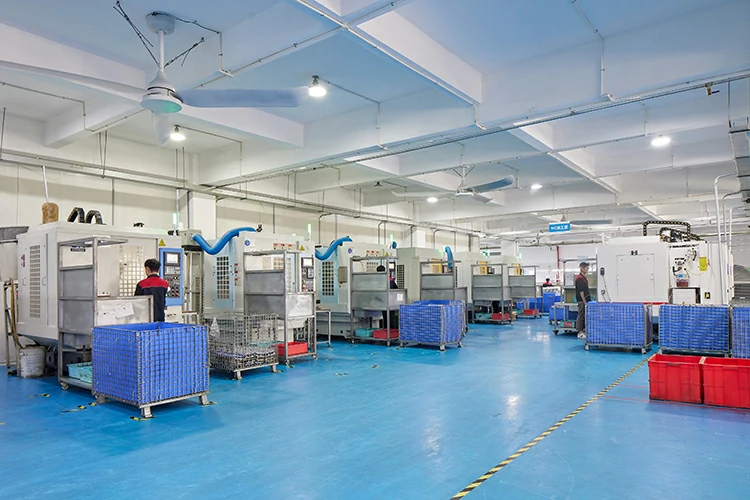
Get Started Now with Custom Aluminum Die Casting According to Your Needs!
Surface Finishes of Aluminum Die Casting
The surface treatment of die castings is to improve the surface state of die castings, thicken the surface oxide film or form a new surface mold, so as to improve the corrosion resistance, decoration or other required characteristics of the surface of die castings.
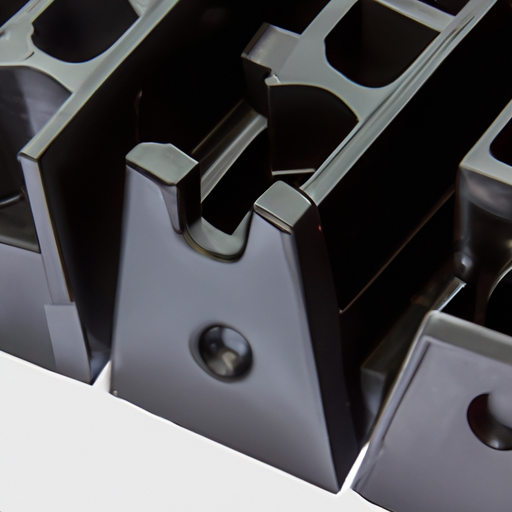
Commonly used surface treatment methods for die castings include chemical conversion treatment, anodic oxidation treatment, electroplating and coating, etc. In order to obtain satisfactory surface treatment effects, die castings need to be pretreated before treatment, including mechanical pretreatment (grinding, polishing, sandblasting, etc.) and chemical pretreatment (degreasing, pickling and alkali cleaning)
Common surface treatment processes for aluminum alloy die castings are as follows:
- Phosphating of aluminum
- Alkaline electrolytic polishing process for aluminu
- Environmentally friendly chemical polishing of aluminum and aluminum alloys
- Electrochemical surface strengthening of aluminum and its alloys
- Surface oxidation treatment technology of YL112 aluminum alloy
Related Aluminum Die Casting Products
Application of Aluminum Die Casting
Aluminum alloy die-casting products are currently mainly used in auto parts, electronic casings, communications, motors, aviation, ships, home appliances, furniture accessories, digital casings, handicrafts, security product casings, LED lighting (lampshades) and some new energy industries
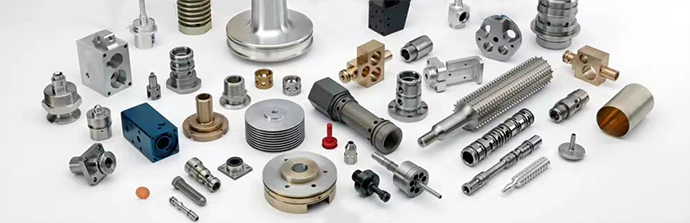
Advantages of choosing MindWell Custom Aluminum Die Casting
Through advanced die-casting technology, MindWell custom-manufactures aluminum die-casting parts of various highly accurate shapes and sizes, providing various complex design requirements, including detailed structures and precise dimensional control
Leading aluminum die casting manufacturer in China
- Mindwell has a team of engineers with strong skills and rich experience.
- Strict 6S management, adopting international production management model, establishing and improving operating standards for each process.
- More than a dozen sets of advanced processing equipment.
- Project management and ERP systems ensure delivery on time.
- Enhance lean manufacturing and optimize supply chain collaboration to reduce costs
- Provide one-stop service from accessory design to finished product packaging and shipment
Aluminum alloy die casting process flow
The process flow of aluminum alloy die-casting is generally divided into five steps, among which casting design and mold manufacturing are the key links:
- Casting design
- Mold making
- Smelting aluminum alloy
- Die casting
- Post-processing
- Assembling and packaging

ABOUT US
Mindwell - Professional custom aluminum die-casting service manufacturer in China
As a professional manufacturer of aluminum alloy die-casting parts in China, Mindwell always adheres to the service concept of “long-term cooperation” and insists on providing customers with high-quality, high-performance aluminum alloy die-casting products from the customer’s perspective.
Truly meet customer customization needs
Mindwell provides customized services. Based on the customer’s parts usage needs, it fully considers the actual use of customized aluminum die-casting parts in all aspects of product design, material selection, production, and manufacturing, and focuses on understanding the special requirements of the customer’s industry, so as to make To produce aluminum alloy die-casting products that are more suitable for customer needs. This allows customers to enjoy high-quality, high-performance products while also receiving more intelligent and personalized services.
Strong technical strength
Mindwell is equipped with advanced die-casting equipment and testing equipment and has established close technical cooperation relationships with professional quality inspection institutions, constantly accumulating and precipitating technical strength. At the same time, Mindwell has a professional technical team, each technician has rich experience and superb skills and can provide customers with all-round, one-stop technical support and services. As a result, the company has always been in a leading position among China’s aluminum alloy die-casting manufacturers.
Strict quality control
Aluminum alloy die castings are complex components with high strength, high toughness, and high precision. Their quality directly affects customers’ product performance, safety, market competitiveness, and other aspects. Therefore, Mindwell Company strictly controls every step of the production process, from raw material procurement, inspection, and warehousing, to the production process, to shipping inspection. Every step is carefully and scientifically monitored to ensure that the products are shipped out of the factory. Quality meets customer expectations.
Comprehensive service system
Under the concept of customer first, Mindwell has established a comprehensive pre-sales, sales, and after-sales service system. In the pre-sales stage, the company fully communicates with customers, understands their needs, and solves their actual needs through technical support, sample production, mold development, etc.; in the mid-sales stage, the company assigns professional account managers to each customer to follow up with them throughout the process. orders and timely feedback on order progress; during the after-sales stage, the company promptly follows up on customer complaints based on customer feedback, handles customer issues in a timely manner, and ensures customer satisfaction and loyalty.
Continuous innovation replaces backwardness and elimination
In the context of increasingly fierce competition in the global market, what competes with each other is scientific and technological strength and innovation capabilities. Aluminum alloy die-casting products have always been in a leading position in the market due to their high efficiency, strength, and quality. Mindwell pays attention to new market trends in every aspect, from equipment updates, and staff training, to the development of new materials, and follows up on the latest technology and material changes to obtain new technologies and new quality upgrades.
As an aluminum alloy die-casting manufacturer that pays attention to customer needs and emphasizes service details, Mindwell stands out among many competitors with its high-quality products, excellent technology, strict quality control, and comprehensive services, and has won the trust of customers. and support. In the future development, Mindwell company will continue to improve the level of products and services. If you are considering customizing aluminum die-casting products, please contact us directly. You can also send us drawings.


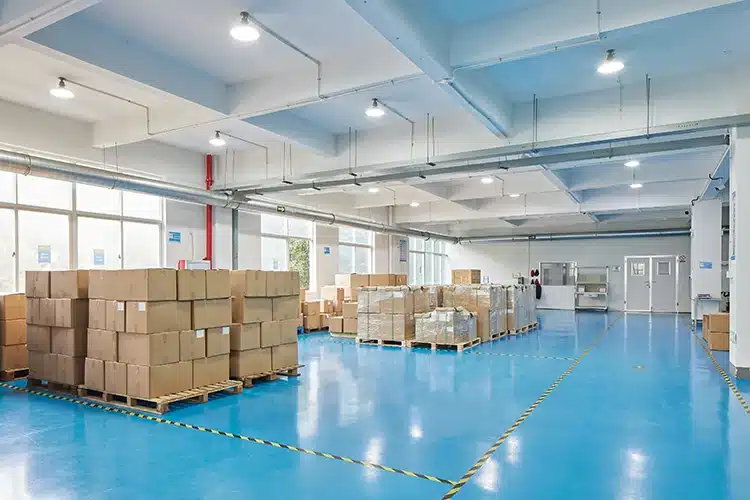
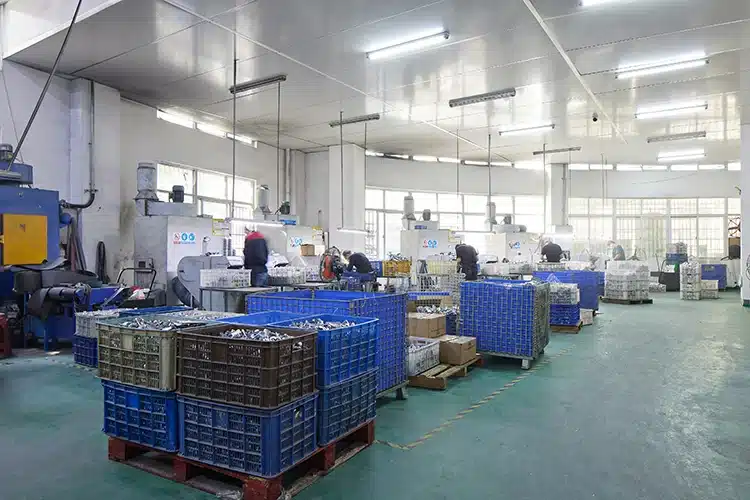
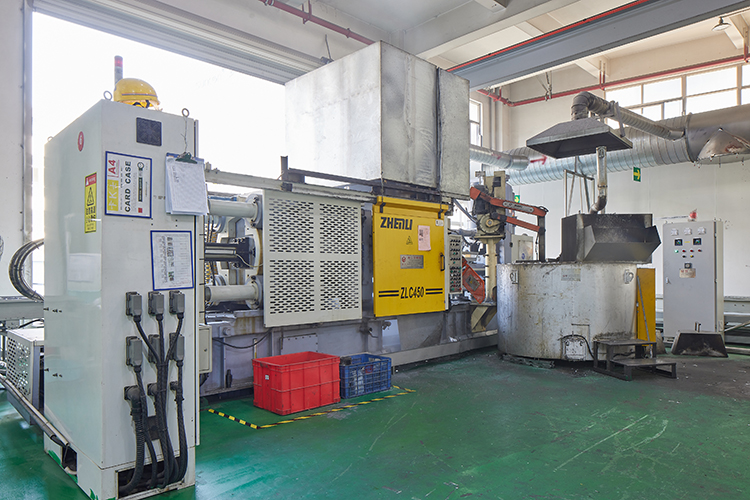



Aluminum die casting related FAQs
As a professional aluminum die-casting manufacturer in China, Mindwell has rich experience and ideas in innovation and research and development in the aluminum die-casting industry, which we share with you here.
What is aluminum die casting?
The aluminum alloy die-casting process is an efficient and precision casting process that injects high-temperature, high-pressure liquid metal into the casting mold to quickly cool it and form aluminum alloy parts with good mechanical properties and surface quality.
For aluminum castings, there are three main casting processes:
- pressure casting
- gravity casting
- Extrusion casting
The whole casting process can be summarized into the following steps:
- Aluminum/aluminum alloy melting
- model making
- Casting solidifies
- molding
- Clean.
Three aluminum casting processes are introduced below:
- Pressure casting, referred to as die casting, refers to the process of instantly injecting molten aluminum or aluminum alloy into the casting cavity of a mold under the action of external forces other than gravity. Pressure casting can be further subdivided into vacuum casting, centrifugal casting, low-pressure casting, pressure casting, and casting that relies on the pressure of the die-casting machine.
- Gravity casting refers to the process in which molten aluminum or aluminum alloy flows into the casting cavity of the mold by its own gravity. Gravity casting can be refined into the sand casting process and hard mold casting process.The sand casting process is very suitable for single-piece or mass production of aluminum castings because the mold materials used are cheap and easy to obtain, and the process method is relatively simple. Therefore, it can be said to be the “basic operation” in the aluminum casting manufacturing process.The hard mold casting process is also called the metal mold casting process. It is a process in which liquid aluminum or liquid aluminum alloy is injected into the metal casting mold and the casting is obtained after cooling and solidification. Metal molds are usually made of higher-strength aluminum alloys or other hard metals and can be used repeatedly. The entire process can be understood as injection molding.
- The squeeze casting process is also called the liquid die forging process. The specific process is to pour aluminum or aluminum alloy in the molten state directly into the open mold, and then seal the mold to allow the liquid aluminum or aluminum alloy to flow into the mold. The flow is filled to the shape outside the mold, and then high pressure is applied to the mold to cause plastic deformation of the solidified aluminum/aluminum alloy in the mold. The unsolidified aluminum/aluminum alloy will undergo high-pressure solidification while undergoing isostatic pressure and finally form aluminum/aluminum alloy castings.
For now, the above manufacturing processes for aluminum castings are the most commonly used in the industry and are relatively low-cost. In addition to the above-mentioned, there are also ceramic casting, plaster casting, and other technologies.
In addition, when aluminum castings are manufactured, the surface of the mold cavity used has a high smoothness and is also sprayed with a refractory coating made of refractory materials and high-temperature adhesives, so the surface of the aluminum castings produced is also very smooth and flat. , superior to other ordinary metal castings. This also gives aluminum castings a very significant advantage – the surface is smooth and the castings are high-precision, so the workload can be reduced during processing operations, but at the same time, there is not much machining allowance for those small and precise parts. The aluminum/aluminum alloy castings produced in this way do not require machining and can be used simply by grinding and polishing the remaining parts, which greatly saves processing time and labor costs, and also saves a lot of pure aluminum/aluminum alloy raw materials.
What is the best aluminum for die casting?
Die-cast aluminum alloy is a cast aluminum alloy material, which is characterized by good fluidity, low price, corrosion resistance, low density, easy to oxidize, easy to corrode, easy to produce pores, low melting point, etc. The aluminum alloy material of each model is also different.
A356 has the highest conductivity, and the lowest is A380 and ADC12.
A380 and ADC12 have the highest tensile limit, while A356 has the lowest
A360 has the best yield strength
LM5 has the highest elongation rate
ADC12 performs well in all aspects, is relatively balanced, has no outstanding features and has no shortcomings. It is a material commonly used in the cast aluminum industry. 80% of MINDWELL’s products use ADC12. The products produced by this material have strong bearing capacity and mechanical strength. It has high performance, good cutting performance, good demoulding performance, high casting pass rate, is especially friendly to thin-walled parts, and can meet the requirements of high-performance aluminum alloy die castings.
How much does aluminium die casting cost?
The cost of aluminum die castings mainly includes the following parts:
- Aluminum alloy material cost: Depending on the size and weight of the die-casting, a certain amount of aluminum alloy material needs to be consumed. This cost is related to factors such as the model, quality, and market price of the aluminum alloy.
- Mold making costs: Aluminum die-casting molds require sophisticated design and production, so the cost of this part is relatively high.
- Die casting processing costs: including die casting, cooling, demoulding, trimming and other processes.
- Other costs: including equipment depreciation, management costs, transportation costs, etc.
Taking into consideration the above expenses, the cost of aluminum die-casting parts will vary depending on factors such as model, specification, material, etc. Generally speaking, the cost of aluminum die-casting parts ranges from tens to hundreds of yuan. The specific cost needs to be calculated based on actual conditions and specific production processes.
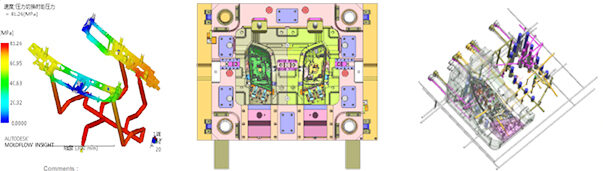
Aluminum alloy die casting design guide
The reasonableness of the design of die casting is related to the entire die casting molding process, in the design of die casting, should give full consideration to the structural characteristics of the die casting, die casting process requirements, try to minimize the occurrence of defects of the design of die casting in the die casting molding process, in order to the optimal design scheme to maximize the improvement of the quality of the die casting.
Reasonable design die casting wall thickness
- Aluminum alloy die-casting structure design should give full consideration to wall thickness, wall thickness is of special significance in the die-casting process, wall thickness, and the whole process specification have a close relationship, such as the calculation of filling time, the selection of the speed of the inner gate, the calculation of solidification time, the analysis of the mold temperature gradient, the role of the pressure (the final pressure), the length of time to stay in the mold, casting ejector temperature and operating efficiency;
- Designing the wall thickness too thick will result in external surface defects such as shrinkage holes, sand holes, air holes, coarse internal grains, etc., which will make the mechanical properties decrease and the quality of the part increase resulting in higher costs;
- Design wall thickness is too thin will cause poor filling of aluminum liquid, and molding difficulties, so the aluminum alloy dissolution is not good, easy to appear casting surface filling difficulties, lack of material and other defects, and the die casting process brings difficulties;
- Die casting with the increase of air holes, internal air holes, shrinkage holes, and other defects, so in order to ensure that the casting has enough strength and stiffness under the premise, should try to reduce the casting wall thickness and keep the cross-section of the thickness of uniformity.
Reasonable design of die-casting reinforcement
For large plane or thin wall die casting, its strength, and rigidity are poor, and easy to deform, then the use of a reinforcing bar can effectively prevent the die casting shrinkage, and fracture, eliminate deformation, enhance the strength and rigidity of the die casting, for too high columns, tables and other structures, can use reinforcing bar to improve the distribution of stress conditions, to prevent the root of the fracture, and at the same time reinforcing bar can assist in the flow of melted metal to improve the casting of the filler performance.
Reinforcement of the root thickness is not greater than the thickness of the wall here, the general thickness is designed for 0.8 ~ 2.0mm; reinforcement of the mold release slope is generally designed for 1 ° ~ 3 °, the higher the design of the mold release slope is smaller; reinforcement of the root need to add rounded corners, in order to avoid sharp changes in the cross-section of the part, and at the same time to assist in the flow of molten metal to reduce stress concentration in the parts, to enhance the strength of the parts, rounded corners are generally close to the wall thickness here; Reinforcement height is generally not more than 5 times its thickness, reinforcement thickness is generally required to be uniform, if the design is too thin, reinforcement itself is easy to fracture, if too thick, it is easy to produce depression, porosity, and other defects.
Reasonable design die-casting mold slope
The role of die casting mold slope is to reduce the casting and mold cavity friction, easy to take out the casting; Ensure that the die-casting surface is not strained, and at the same time extend the life of the mold. Die casting slope and the height of the die casting, the greater the height, the smaller the slope of the mold. In general, the outer surface of the die-casting mold out of the slope for the inner cavity out of the mold slope of about 1/2, but in the actual design, can be die-casting inside and outside the surface of the mold out of the slope design for the same, in order to maintain a uniform wall thickness, simplify the structural design.
Reasonable design processing allowance
Die casting design should try to avoid machining, machining will destroy the surface of the parts of the dense layer, affecting the mechanical properties of the parts; will make the die casting of the internal pores exposed, affecting the surface quality, but also increase the cost of parts. Die casting can’t avoid machining, one should try to avoid the design of large cutting amounts, and structural design as much as possible to facilitate the machine or reduce the machine area, to reduce the cost of the machine.
Die casting on the part of the higher dimensional accuracy requirements, or some plane surface roughness requirements, die casting process is difficult to meet the requirements, this time it is necessary to carry out subsequent processing, on this part of the structure, the design should try to reserve machining allowance. Die casting surface strength, hardness than the internal high, machining should pay attention to retain the surface of the densification, so the machining allowance can not be excessive allowance, machine plus too much is likely to produce porosity and external surface defects.
Aluminum alloy die casting spraying design
Die casting surface coating design generally uses a powder spraying process, the principle of electrostatic powder spraying: mainly through the electrode will paint polarization, and then the object to be sprayed with the opposite charge, in the electric field force under the action of the powder uniformly attached to the surface of the object. Powder spraying process features: powder electrostatic spraying does not cause air pollution, powder can be recycled to reduce the cost of material consumption, film performance acid, alkali, corrosion resistance is good.
お見積もり
射出成形のお見積もりは無料です。