アルミダイキャスト製ヒートシンク
The heat sinks designed and customized by our company are made of aluminum. Aluminum is the most suitable for heat sinks because aluminum material has high hardness and good heat dissipation properties, which meets the application requirements of heat sinks.
At Mindwell, in addition to producing and manufacturing aluminum die-cast parts, we can also provide product design and molds. Our designers will design many holes and fins according to the application of the heat sink to increase the surface area, or use wavy shapes to improve the flow diversion effect. Heat sink applications in different industries such as automobiles and LED lights can be customized according to needs. Below we will introduce the die-cast heat sink information in detail.

PRECISION MANUFACTURER
Die Cast Heat Sink Manufacturing Process
The production process of die-casting heat sinks is to melt aluminum alloy or copper alloy and pour it into a mold, and then pour the hot liquid into the mold through pressure to form a three-dimensional structure with multiple heat sinks. Compared with other radiators, die-cast aluminum radiators have the advantages of stable structure, high strength, and high heat dissipation efficiency.
Aluminum die-cast heat sink manufacturing process:
- Aluminum ingot smelting
- Mold making
- Install mold
- Die casting
- demoulding
- Secondary processing
- Package


Material advantages
heat sink Aluminum Material
At Mindwell, we use high-quality aluminum alloy materials to customize die-cast heat sinks. The aluminum material itself has the characteristics of good corrosion resistance, high strength, light weight, etc., and has good thermal conductivity and heat dissipation performance.
In heat sink applications, the shape and size of aluminum heat sinks can be customized and processed according to different application scenarios.
Advantages of Die-Cast Heat Sinks
There are several benefits to using die-cast heat sinks for effectively controlling the heat produced by electrical components. The following is a summary of the main advantages that make die-cast heat sinks the recommended option:
- High thermal conductivity:Die-cast heat sinks are crafted from materials with excellent thermal conductivity, such as aluminum alloy. This allows for the swift transfer of heat to the heat sink, effectively drawing heat away from electronic components and helping to maintain optimal operating temperatures.
- Complex Geometric Shapes:The inherent processing properties of aluminum alloy materials, coupled with the die-casting process, allow for the creation of intricate geometric shapes. This flexibility enhances air flow and surface area, thereby boosting the overall heat dissipation performance of die -cast aluminum heat sinks.
- Precision and Uniformity:Die casting is a precise manufacturing technique that guarantees reliable heat sink manufacture. Maintaining uniform thermal performance over a wide range of heat sinks depends on this consistency.
- Efficient Production of Series:Die casting turns out to be an economical way to produce heat sinks in large quantities. It is appropriate for large-scale manufacturing because of its effective and quick production capabilities, which eventually lower unit costs.
- Excellent Surface Treatment Options:Completed die-cast heat sinks are easily polished to improve their appearance and offer further weather resistance. Additional methods for improving corrosion resistance include painting, powder coating, and anodizing.
- Lightweight: Because heat sinks are made of lightweight materials (die cast aluminum and zinc alloys), they are appropriate for uses where weight is an issue (automotive or aerospace, for example).
- Sufficient Electrical Conductivity: Aluminum is one of the materials that heat sinks are made of, and it has strong electrical conductivity. Applications requiring efficient electrical grounding or conductivity benefit from this feature.
- Durability and Longevity: Die casting materials, such zinc and aluminum alloys, are renowned for their sturdiness and resistance to corrosion. heat sinks have a longer lifetime due in part to their durability, which guarantees dependable performance.
- Customization Possibilities: Die casting allows for the customization of heat sink designs to meet specific thermal requirements. Engineers are able to modify the fin design, size, and shape to meet the specific thermal requirements of a given application.
To sum up, die-cast heat sinks combine durability, cost-effectiveness, design freedom, and thermal efficiency in a seamless manner. Because of these benefits, they are a well-liked option for several electrical gadgets and uses where efficient heat control is essential.
Extrusion aluminum VS die cast heat sink
Extrusion and die-casting are two different manufacturing processes for creating heat sinks, each with its own set of characteristics and advantages. Let’s compare extrusion aluminum and die-cast heat sinks:
Extrusion Aluminum Heat Sink:
1. Manufacturing Process:
- Process: Extrusion involves forcing aluminum through a shaped opening (die) to create a continuous profile. The profile is then cut to the desired length.
- Flexibility: Extrusion allows for the creation of long, continuous profiles with a consistent cross-section.
2. Design Flexibility:
- Complexity: Limited compared to die casting. Extruded heat sinks are typically simpler in design and have fewer intricate features.
- Customization: Extruded profiles can be customized to some extent, but the options are more constrained.
3. Thermal Performance:
- Thermal Conductivity: Good thermal conductivity, but not as high as some die-cast materials.
Surface Area: Effective for creating larger surface areas for heat dissipation.
4. Cost:
- Production Cost: Extrusion is generally a cost-effective process, especially for simpler designs and smaller quantities.
- Tooling Cost: Tooling costs are often lower compared to die casting.
5. Surface Finish:
- Finish: Extruded heat sinks may have a rougher surface finish compared to die-cast heat sinks.
- Surface Treatment: Anodizing or other surface treatments can be applied for improved aesthetics and corrosion resistance.
Die-Cast Heat Sink:
1. Manufacturing Process:
- Process: Die casting involves injecting molten metal into a mold cavity under high pressure. This process allows for complex shapes with fine details.
- Complexity: well-suited for intricate and complex designs with fine details.
2. Design Flexibility:
- Complexity: highly flexible. Die casting allows for intricate fins, variable thickness, and other detailed features.
- Customization: There are more options for customization, making it suitable for a wide range of design requirements.
3. Thermal Performance:
- Thermal Conductivity: Excellent thermal conductivity, especially with materials like aluminum and copper.
- Surface Area: Can be optimized for efficient heat dissipation in compact spaces.
4. Cost:
- Production Cost: Die casting can be cost-effective for large quantities and complex designs.
- Tooling Cost: Initial tooling costs are higher compared to extrusion.
5. Surface Finish:
- Finish: generally smoother surface finish compared to extrusion.
- Surface Treatment: Can be treated for improved aesthetics, corrosion resistance, and other functional properties.
Conclusion:
1.Application Considerations:
- Extrusion is suitable for simpler designs and when cost-effectiveness is a primary concern.
- Die casting is ideal for complex designs, high quantities, and when thermal performance is critical.
2.Design Flexibility:
- Extrusion is limited in complexity.
- Die casting offers more design flexibility and intricate detailing.
3.Cost:
- Extrusion is cost-effective for simpler designs and smaller quantities.
- Die casting can be cost-effective for large quantities and complex designs over the long term.
Ultimately, the choice between extrusion aluminum and die-cast heat sinks depends on specific application requirements, design complexity, and budget considerations.

Get Started Now with Custom Die Casting Heat Sink According to Your Needs!
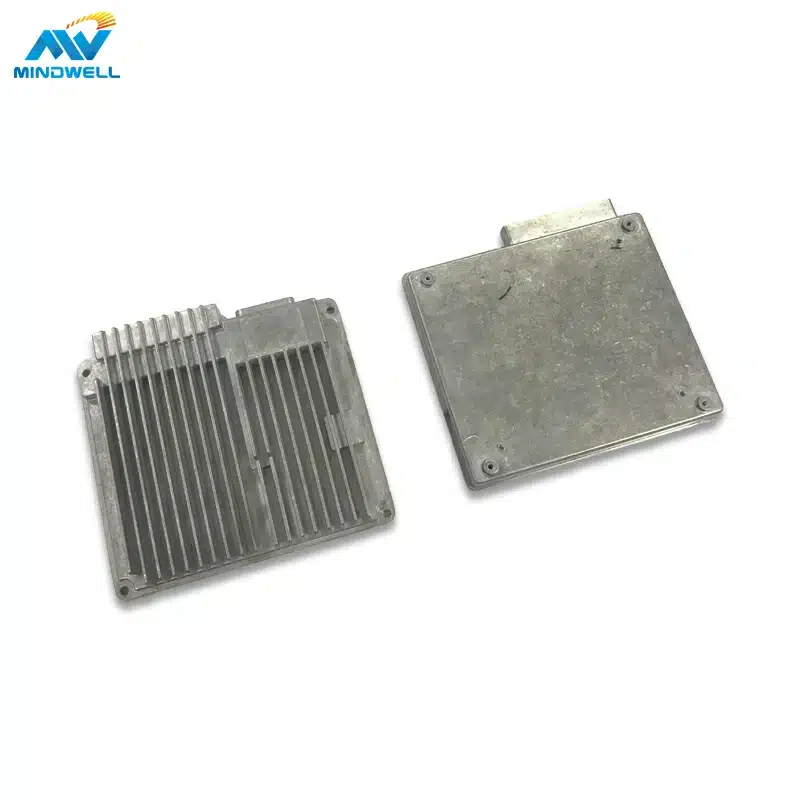
aluminum heatsink Applications
aluminum die-casting heat sinks are mainly used in occasions that require heat dissipation. Due to its fine manufacturing process and flexible shape design, heat sinks of different shapes and sizes can be made according to different requirements, and have a wide range of applications. .
Aluminum die-casting heat sinks are mainly used in electronic equipment, automobile engines, LED lights and other fields that require heat dissipation, and the heat dissipation effect is very good. Due to its flexible shape design and fine manufacturing process, heat sinks of different shapes and sizes can be made according to different requirements, so it has a wide range of applications.
About US
A reliable heat sink die casting manufacturer: Mindwell
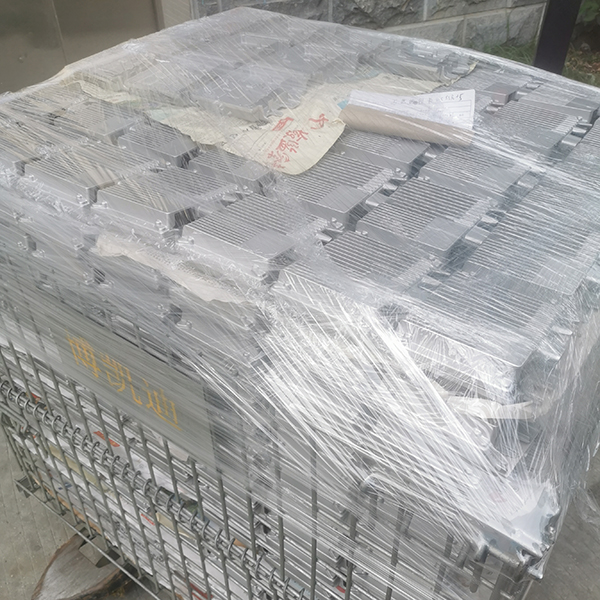
Mindwell is a company specializing in the design and production of aluminum alloy, zinc alloy die-casting parts, and aluminum profile processing parts. It provides a full range of production services from the design and development of molds to the forming, post-processing, and surface treatment of die-casting products. The products are mainly used in electronic appliances, automobile and motorcycle accessories, furniture and bathrooms, power tools, medical machinery and other industries, and are exported to Europe, America and Southeast Asian countries.
Mindwell was founded in 2010. It has many years of experience in R&D and production management. It uses technology and management innovation as a means to continuously improve services and continuously reduce costs to seek development. Regardless of the size of the customer, our company will continue to do so. Provide customers with precise die-casting process solutions, and also undertake OEM and ODM cooperation.
The company’s production workshop consists of a mold department, a die-casting department, a processing department, a CNC department, etc., with a total of 12 professional mold design engineers, die-casting adjusters, and CNC programmers. The company’s equipment is complete. The mold department is equipped with various types of machines such as CNC, precision engraving machines (CNC), CNC lathes, lathes, milling machines, and spark machines. The die-casting department has hot and cold chamber die-casting machines, with capacities of 800 tons, 700 tons, 500 tons, 300 tons, 280 tons, and 160 tons respectively. Magnesium alloys, aluminum alloys, and zinc alloys can all be produced by die casting. There are also CNC lathes. The post-processing department currently has several equipments including drilling machines, tapping machines, sanding machines, polishing machines, wire drawing machines, sandblasting machines, roller machines, grinders, punching machines, etc. The quality control department is equipped with a three-dimensional measuring instrument, a salt spray testing machine, a vacuum detector, a balance detector, and more than 100 other measuring instruments.
お見積もり
射出成形のお見積もりは無料です。
よくある質問
Mindwell has been providing aluminum die-casting services in Xiamen for more than ten years. We have extensive experience in customizing die-cast heat sink developers. If you are considering customizing aluminum die-casting services or have any questions about aluminum die-casting, please feel free to contact us. Talk to us, contact us directly and our engineers will communicate with you.
Aluminum heat sink housing are various shells made of aluminum alloy. They are highly flexible and can be cut to any length. The convenience is unmatched by other types of shells. And aluminum is a material with good thermal conductivity, so it has Very good heat dissipation.
Aluminum material selection for heat sinks
In the current market, the main material used for aluminum housing products is aluminum alloy. Aluminum alloy has good thermal conductivity and is strong and durable. Of course, the base made of aluminum alloy can better absorb and dissipate heat.
6063 aluminum profile heat sink technology:
Aluminum profile extrusion manufacturers develop corresponding molds to heat the aluminum ingot to a certain temperature to change its physical shape to obtain aluminum heat sink materials.
Then after coming out of the mold, we get the various types of heat sink profiles we want; then we can cut, groove, polish, deburr, clean, and surface them before they can be used.
6063 aluminum profile heat sink principle:
First: 6063 aluminum profile heat sink has very strong thermal conductivity
Aluminum has strong thermal conductivity and can very well help electronic products dissipate heat. As far as the aluminum profile heat sink material is concerned, the thermal conductivity of each material is different. They are arranged from high to low according to the thermal conductivity. differences are:
Copper, aluminum, steel. However, if silver is used as a heat sink, it will be too expensive, so the best solution is to use copper. Although aluminum is much cheaper, its thermal conductivity is obviously not as good as copper (about 50% of that of copper) ).
The commonly used materials for aluminum profile heat sink are copper and aluminum alloys, both of which have their own advantages and disadvantages. Copper has good thermal conductivity, but is more expensive, difficult to process, overweight, has small heat capacity, and is easily oxidized.
Aluminum is too soft and cannot be used directly. Only the aluminum alloy used can provide sufficient hardness. The advantages of aluminum alloy are low price and light weight, but its thermal conductivity is much worse than copper. Some heat sink have different Take the long answer and embed a copper plate on the aluminum alloy radiator base. This can not only take care of the price issue, but also ensure the quality of heat dissipation.
Second: The density of 6063 aluminum profile heat sink is smaller and easier to process into other parts.
Simple installation and convenient maintenance. Since aluminum alloy has low density and can be made into parts of various shapes and specifications, the cross-section of this kind of aluminum profile radiator is large and regular, and product assembly and surface treatment can be carried out in one step.
The steps are in place and can be installed directly at the construction site, saving large installation costs and making maintenance more convenient.
Third: 6063 aluminum radiator has strong plasticity
The 6063 aluminum radiator can be subjected to various surface treatments, with many colors and varieties, and no solder joints. It is highly decorative, beautiful and durable, and can meet people’s personalized requirements. Yongyu Metal can also process sandblasting, drawing, polishing
Light, surface anodizing, hard oxidation and other processing techniques can produce more beautiful aluminum radiators.
Radiators made of 6063 aluminum profiles have strong thermal conductivity, low density and low price, so they are loved by major manufacturers.
Other functions of aluminum alloy heat sink:
- Anti-electromagnetic radiation: The solid shell protects the board, power supply and storage equipment, and can prevent pressure, impact, and dust. It can also perform the function of preventing electromagnetic interference and radiation, and shielding electromagnetic radiation.
- Low density: The density of the aluminum alloy shell is very small. The container is easy to make and can be used as a mobile phone shell and charging shell. It is also very wear-resistant and anti-corrosion. A dense aluminum Oxide film is easily formed on the surface of the aluminum alloy shell to prevent nutrient growth.
- Storage devices: It can provide space for power supplies, motherboards, various expansion boards, floppy disk drives, optical disk drives, hard disk drives and other storage devices, and is connected through supports, brackets, various screws or clips inside the chassis . The components securely fix these parts inside the chassis to form an intensive whole.
- High strength: The aluminum alloy shell can effectively improve the hardness of the aluminum shell after aging treatment. The aluminum profile shell after rough surface treatment not only takes into account the heat dissipation performance, but also takes into account the appearance.
- Light weight. Only one-third the weight of a cast iron radiator with the same heat dissipation. Light weight, easy to install and carry. When the heat dissipation is the same, its weight is only one-tenth that of a cast iron radiator, one-sixth that of a steel radiator and one-third that of a copper radiator, which can greatly save transportation costs, reduce labor intensity, and save Install time.
- Safe and reliable. Safe and reliable, high thermal efficiency, good thermal conductivity, energy-saving and environmentally friendly, and long service life.
- Corrosion resistance. The surface of the aluminum die-cast heat sink is degreased, oxidized and then spray-coated to ensure that the coating will not fall off for a long time and is impact resistant. A thick oxide film can be formed on the surface of aluminum alloy materials and can be used for heating water with pH ≤ 9 or for long-term use in automobile water tanks. Aluminum heat sinks with special surface treatment can be used in various pH~12. This material is used for a long time.
- Beautiful. The aluminum die-cast heat sink has a simple, beautiful, elegant yet fashionable design, is small in size, light in weight, and easy to install, inheriting the excellent European radiator production technology. Cooling fins are available in a variety of surface finishes. It has a variety of patterns and colors, no solder joints, strong decoration, beautiful and durable, and can meet people’s personalized requirements.
- Wide application. Widely used in automobiles, LED, etc., mechanical equipment, electronic equipment, motor body shells and other industries.
- Dimensions are variable. Beautiful appearance, flexible size. It can be an artistic shape, or it can be customized according to the special requirements of special rooms and users to show your personality; it is easy to match and coordinate with the room, making it a perfect home decoration product.
- High strength. Die-cast aluminum radiators have high overall strength and high working pressure, so they are suitable for high-rise buildings because the specific strength and specific stiffness of aluminum alloys are much higher than those of copper, cast iron and steel. Even though it is thin, it can withstand sufficient pressure, bending force, traction and impact force, and will not be damaged during handling, installation and use.
- Easy to install. Module combination, easy to install. Due to the low density of aluminum alloy, it can be processed into parts of various shapes and specifications. This kind of aluminum radiator has a large and regular cross-section. The product assembly and surface treatment can be done in one step. It can be installed directly at the construction site, saving a lot of installation costs. Maintenance is also very convenient and cheap.
- Energy saving and consumption reduction, low cost of use. When the center distance of the radiator inlet and outlet is the same as the heat conduction temperature, the aluminum radiator is 2.5 times more dispersed than the cast iron radiator, and cannot be heated due to its beautiful appearance. It can reduce heat loss by more than 30 inches and reduce costs by 10 inches. Although the cooling effect of the above aluminum radiator is slightly not as good as that of the copper radiator, the weight can be greatly reduced. Since the price of aluminum is only 1/3 of the price of copper, it can greatly reduce costs.
Aluminum die-cast heat sinks are widely used in automotive engines, electronic equipment, industrial machinery and other fields. For example, the radiator on a car engine needs to use aluminum die-casting fins to dissipate heat to ensure the normal operation of the engine.
The manufacturing process of aluminum die-casting heat sink mainly includes the following steps:
- – Design heat sink structure, determine materials and specifications;
- – Make heat sink mold;
- – Melt the aluminum alloy material and press it into the heat sink mold through a die-casting machine, allowing it to cool and harden;
- – Surface treatment of aluminum die-cast heat sinks, such as oxidation treatment, painting, etc.
- – Product quality: MindWell (hereinafter referred to as MNW) conducts strict quality control of products and is a reliable supplier of aluminum die-casting heat sinks;
- – Support service: MNW has good after-sales service and technical support, and can solve problems for customers in time;
- – Cost control: provide you with reasonable product prices and preferential policies to effectively control costs;
- – Innovation ability: The company has many years of production experience and engineering team, and has research and development capabilities, which can provide customers with novel and competitive heat sink products.
The maintenance and maintenance of aluminum die-casting heat sinks mainly need to pay attention to the following items:
- – Regularly check the working status and thermal efficiency of the radiator, and replace the radiator in time;
- – Clean the radiator to ensure its cooling effect, you can use professional cleaning tools;
- – Regularly check whether the installation and bracket of the radiator are loose or fall off;
- – Avoid using the radiator in high temperature, humid or dusty environment.
When designing an aluminum die-cast heat sink enclosure, engineers usually consider the following aspects: enclosure size, heat dissipation power, fan configuration, and installation method.
- Housing size is very important. It needs to be determined based on the size and number of cooling elements. The size of the casing will directly affect the cooling capacity of the radiator. If it is too small, it will result in insufficient heat dissipation, and if it is too large, it will waste materials and costs.
- The heat dissipation power is an important consideration for aluminum die-casting heat sinks. The amount of heat dissipation power is closely related to the heat dissipation power of the internal heat dissipation components and the working status of the fan. Therefore, when designing the casing, sufficient space for heat dissipation and sufficient air flow must be ensured to ensure the heat dissipation effect.
- Fan configuration is another important factor to consider when designing an aluminum die-cast heat sink. It is necessary to ensure that air can flow through the entire radiator, taking into account noise and power consumption.
- The installation method is the last important factor in aluminum die-casting heat sink design. Different installation methods will affect the heat dissipation effect and practicality of the radiator. By choosing the correct installation method, the radiator can be more stable and reliable in operation, and can also be more conveniently maintained and replaced.
In short, aluminum die-cast heat sink is one of the important parts of the radiator, and its design plays a very important role in the performance and practicality of the radiator. Through reasonable size design, cooling power calculation, fan configuration and excellent installation methods, users can be provided with more efficient, safe and reliable cooling solutions.