Spuitgieten van aluminium is een proces waarbij een aluminiumlegering wordt verhit tot een vloeibare toestand en in een spuitgietmatrijs wordt gespoten om af te koelen en te vormen. Het proces biedt voordelen zoals kostenreductie, precisie, efficiëntie en productie op grote schaal. Het materiaalgebruik is hoog en het blanco-gebruik is zelfs 90%, wat de kosten drukt. Toepassingen zijn onder andere auto-industrieelektronica, huishoudelijke apparaten, bouw en decoratie, lucht- en ruimtevaart, militaire en algemene machines. De afgietsels van de aluminiummatrijs hebben uitstekende verenigbaarheid, goede oppervlakteruwheid en hoge dimensionale nauwkeurigheid.
Inleiding
Spuitgieten van aluminium is een proces waarbij een aluminiumlegering wordt verhit tot een vloeibare toestand en vervolgens in een spuitgietmatrijs wordt gespoten om te worden afgekoeld en gevormd. Het spuitgieten van aluminium biedt vele voordelen, zoals kostenreductie, precisie, efficiëntie en productie op grote schaal. Het materiaalgebruik is hoog en het blanco-gebruik is zo hoog als 90%, waardoor de kosten worden verlaagd.
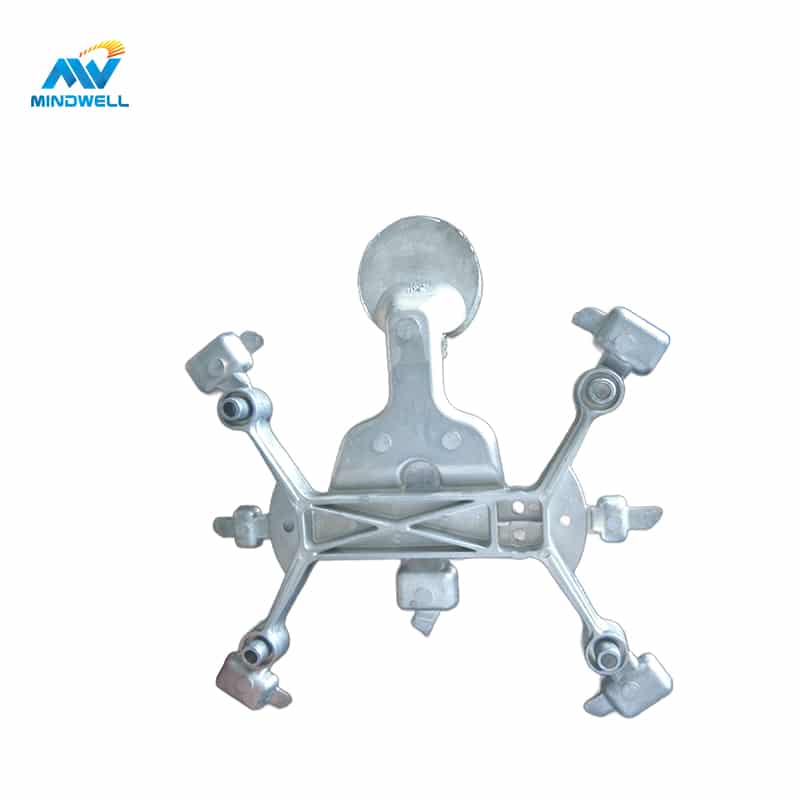
De definitie en het belang van aluminium spuitgieten
Bij het spuitgieten van aluminium wordt een aluminiumlegering verhit tot een vloeibare toestand en vervolgens in een spuitgietmatrijs gespoten, waar het afkoelt en stolt. De voordelen van aluminium spuitgieten ten opzichte van andere productietechnieken zijn een hoog materiaalgebruik, een hoge productiviteit en een hoge productnauwkeurigheid. Aluminium spuitgieten is een andere naam voor aluminium gegoten voorwerpen. Er zijn verschillende toepassingen voor spuitgieten van aluminium, waaronder de productie van apparatuur, elektronica en auto-onderdelen. Gegoten aluminium onderdelen zijn licht, sterk en corrosiebestendig, wat de prestaties en brandstofefficiëntie van een auto aanzienlijk kan verbeteren. Gegoten aluminium onderdelen hebben sterke mechanische eigenschappen en een hoog warmtegeleidingsvermogen, waardoor het product langer meegaat en stabieler blijft. Gegoten aluminium onderdelen zijn hoogwaardige en betrouwbare onderdelen die gebruikt worden bij de productie van machines en die de levensduur en prestaties van apparatuur kunnen verlengen. Als gevolg hiervan is spuitgieten van aluminium uitgebreid ontwikkeld en toegepast in verschillende industrieën. Aangezien nieuwe materialen worden gecreëerd en de moderne productietechnologie aan populariteit blijft winnen, zullen de toepassingsmogelijkheden van het spuitgieten van aluminium zich uitbreiden.
Toepassingsgebieden van aluminium spuitgietwerk
Het spuitgietproces van aluminium wordt op veel gebieden gebruikt. Dit zijn enkele van de belangrijkste domeinen:
- Auto-industrie: Motoronderdelen, remmen, stuurinrichtingen en andere onderdelen zijn enkele van de vele producten in de auto-industrie die aluminium spuitgiettechnologie gebruiken. De sterkte, het lichte gewicht en de thermische geleidbaarheid van aluminiumlegering zorgen ervoor dat het voldoet aan de energie-efficiënte en lichte voertuigvereisten.
- Elektronische en communicatieapparatuur: Componenten voor elektronische en communicatieapparatuur, zoals behuizingen, radiatoren, aansluitingen en stopcontacten, enz. worden gemaakt met de spuitgietmethode van aluminium. Door de sterke elektromagnetische afscherming en thermische geleidbaarheid kan een aluminiumlegering de stabiliteit en prestaties van de apparatuur verbeteren.
- Huishoudelijke apparaten: Het gebied van huishoudelijke apparaten en elektrische apparatuur, waaronder behuizingen voor airconditioners, trommels voor wasmachines, onderdelen voor koelkasten en tv-beugels, is een ander gebied waar de spuitgiettechniek van aluminium op grote schaal wordt gebruikt. Producten gemaakt van aluminiumlegering kunnen hun textuur en esthetiek verbeteren door hun oppervlaktekwaliteit en uiterlijk.
- Bouw- en decoratiesector: Kozijnen, deur- en raamaccessoires, interieurdecoratie-elementen en andere artikelen worden in deze sector vervaardigd met de spuitgietmethode van aluminium. Op het gebied van bouw en decoratie kan een aluminiumlegering voldoen aan criteria voor materiaalsterkte, corrosiebestendigheid en aantrekkelijkheid omdat het licht, weerbestendig en buigzaam is.
- Andere gebieden: De ruimtevaart, militaire sector, algemene machinebouw en andere sectoren maken ook uitgebreid gebruik van de technologie van het spuitgieten van aluminium. Spuitgieten van aluminium kan bijvoorbeeld worden gebruikt om propellers, motoronderdelen, vliegtuigrompen en andere componenten te produceren. Daarnaast kan een verscheidenheid aan onderdelen voor algemene mechanische apparatuur, met inbegrip van onderdelen voor werktuigmachines, pomphuizen, kleppen, drukvaten, enz. worden gemaakt met de spuitgiettechniek van aluminium.
Voordelen en beperkingen van spuitgieten van aluminium
Aluminium spuitgieten heeft de voordelen dat het goedkoop, zeer precies en efficiënt is en dat het ingewikkelde vormen kan produceren. Maar er zijn ook enkele beperkingen waarmee, afhankelijk van de toepassing, zorgvuldig rekening moet worden gehouden.
Voordelen van aluminium spuitgieten:
- Het gesmolten metaal behoudt een grote vloeibaarheid onder hoge druk en hoge snelheid, waardoor diepe holle metalen voorwerpen kunnen worden gemaakt met ingewikkelde geometrieën, duidelijke contouren en dunne wanden.
- Gietstukken van aluminium hebben een uitstekende compatibiliteit, een goede oppervlakteruwheid en een grote maatnauwkeurigheid.
- De kosten kunnen lager uitvallen door de hoge benuttingsgraad van het materiaal en de 90% blanco-benuttingsgraad.
- Uitstekende productiviteit en geschikt voor productie op grote schaal.
- Inlays kunnen worden gebruikt voor specifieke prestatiebehoeften en zijn eenvoudig toe te passen.
- goedkoop. Gieten van aluminium kan de productiekosten verlagen en biedt een eenvoudiger productieproces dan conventionele productietechnieken.
- Het is in staat om enorme hoeveelheden metaalgietwerk te produceren en is extreem herhaalbaar.
- Door zijn grote sterkte kan het materiaal stress verdragen in situaties met hoge belastingen en hoge temperaturen.
- Het oppervlak is eenvoudig te bewerken en te schilderen en coating kan de aantrekkelijkheid, corrosiebestendigheid en duurzaamheid verbeteren.
Spuitgieten van aluminium heeft echter een aantal nadelen.
- Gietstukken zijn niet geschikt voor de productie van kleine series omdat ze vaak gaten en geoxideerde onzuiverheden bevatten.
- Zowel de soorten spuitgietlegeringen als de afmetingen van spuitgietproducten zijn beperkt.
- De matrijzen en apparatuur zijn kostbaar en vereisen een aanzienlijke investering.
- Tijdens het fabricageproces worden afvalmaterialen en uitlaatgassen geproduceerd; deze items moeten worden behandeld om het milieu te beschermen.
- De meeste gegoten aluminium onderdelen zijn dun en bros.
- Aluminium spuitgietwerk is misschien niet de ideale optie voor toepassingen die een hoge mate van sterkte en stijfheid vereisen.
Voorbereiding van grondstoffen

Selectie en kwaliteitscontrole van aluminium blokken
Om de kwaliteit van aluminium spuitgietproducten te garanderen, zijn een aantal voorbereidende stappen nodig, waaronder de selectie van ingots van hoge kwaliteit die voldoen aan de specificaties en een strenge kwaliteitscontrole. Om de kwaliteit en functionaliteit van het afgewerkte product te garanderen, is het ook van vitaal belang om aandacht te besteden aan andere elementen van het aluminium spuitgietproces, zoals het ontwerp van de matrijs, de instellingen van de spuitgietparameters, de nabewerkingsprocedures, enz.
Bij de selectie van aluminium blokken moet rekening worden gehouden met de volgende elementen:
- Aluminiumgehalte: Om de kwaliteit en zuiverheid van de grondstoffen te garanderen, moeten aluminiumblokken minimaal 99,5% aluminium bevatten.
- Gehalte aan onzuiverheid: Het gehalte aan onzuiverheden in aluminium blokken moet voldoen aan alle toepasselijke nationale voorschriften. Om negatieve gevolgen voor de spuitgietprestaties te voorkomen, moet de inhoud van onzuiverheden zoals ijzer, silicium, koper enz. binnen een bepaald bereik blijven.
- De aluminium staaf moet een regelmatige rechthoekige parallellepipedumvorm hebben en vrij zijn van zichtbare fouten in termen van vervorming of deformatie. Er mogen geen gebreken zijn zoals poriën, spleten of slakinsluitsels; het oppervlak moet glad en vlak zijn.
- Dimensionale specificaties: De lengte, breedte en hoogte van aluminium ingots moeten voldoen aan contractspecificaties of toepasselijke nationale normen. De maatnauwkeurigheid van de ingots moet ook voldoen aan de criteria om de stabiliteit en maatnauwkeurigheid van gietstukken te garanderen.
- Grondstofkwaliteitscertificaat: Om de kwaliteit, traceerbaarheid en betrouwbaarheid van de grondstoffen te garanderen, moeten aluminium ingots met dit certificaat worden gebruikt.
De volgende taken moeten worden uitgevoerd voor de kwaliteitscontrole van aluminium ingots:
- Inspectie van binnenkomend materiaal: Controleren of aluminium blokken die de fabriek binnenkomen aan alle criteria voldoen door een kwaliteitsinspectie uit te voeren die zaken omvat als uiterlijke kwaliteit, maatnormen, chemische samenstelling, enz.
- Procesinspectie: Om er zeker van te zijn dat de spuitgietproducten aan de specificaties voldoen, worden ze tijdens het spuitgietproces steekproefsgewijs of grondig onderzocht om de uiterlijke kwaliteit, de correcte afmetingen, de chemische samenstelling enz. van de producten te controleren.
- Omgaan met niet-gekwalificeerde producten: Niet-gekwalificeerde spuitgietproducten of aluminium blokken opsporen en beheren, de oorzaken vaststellen en de juiste maatregelen nemen om herhaling van het probleem te voorkomen.
- Kwaliteitsgegevens bijhouden: Houd ten behoeve van kwaliteitsanalyse en traceerbaarheid de productiedetails en algemene kwaliteitstoestand bij van gietstukken en aluminium ingots.
- Voortdurende verbetering: We optimaliseren voortdurend het productieproces en de grondstofkwaliteit, verbeteren de kwaliteit en stabiliteit van onze producten en identificeren eventuele problemen en verbetermogelijkheden via de bestudering van productieproces- en kwaliteitsgegevens.
Smelten en verwerken van aluminiumlegeringen
- De grondstoffen voorbereiden: Combineer de grondstoffen van de aluminiumlegering, zoals aluminiumbaren, spanen, aluminiumschroot, enz. in een bepaalde verhouding.
Verwarmen en smelten: Om de grondstoffen te smelten, plaats je ze in de oven en verhit je ze tot een hoge temperatuur. Ovens op gas of elektriciteit zijn de meest voorkomende soorten ovens.
Regeling smelttemperatuur: De temperatuur van de oven wordt geregeld, meestal tussen 700 en 900 graden Celsius, gebaseerd op verschillende formules en specificaties van aluminiumlegeringen. - Aanpassing van de samenstelling: Om aan de noodzakelijke prestatiecriteria te voldoen, voeg je de juiste componenten toe aan de aluminiumlegering en pas je de samenstelling aan op basis van de specificaties van het product.
- Behandeling van slak: Tijdens het smeltproces worden sommige onzuiverheden en oxiden gevormd, waardoor slakbehandeling nodig is. Meestal wordt een chemische stof die smeltonzuiverheden kan absorberen en zuiveren gebruikt als slakmiddel.
- Ontgassing: Om de kwaliteit van de aluminiumlegering te verbeteren en gassen tijdens het smeltproces te elimineren, moet een ontgassingsbehandeling snel worden uitgevoerd. Er worden vaak verschillende ontgassingstechnieken gebruikt, zoals de sproei- en stofzuigprocedures.
- Controle van de smelttijd: De kwaliteit van een aluminiumlegering wordt sterk beïnvloed door de smelttijd. De aluminiumlegering zal ongelijkmatig mengen als de smelttijd te kort is en het zal snel oxideren als de smelttijd te lang is. Daarom is controle over de smelttijd nodig.
Aanpassing van de samenstelling en kwaliteitscontrole van aluminiumvloeistof
De prestaties en kwaliteit van het afgewerkte product worden aanzienlijk beïnvloed door de wijziging van de samenstelling en de kwaliteitscontrole van de aluminiumvloeistof, die cruciale stappen zijn in het spuitgietproces van aluminium.
Een essentiële fase in de kwaliteitscontrole van aluminiumvloeistoffen is de wijziging van de samenstelling. Om aan de prestatiecriteria van het product te voldoen, moet de chemische samenstelling van aluminiumvloeistof worden gecontroleerd. De volgende factoren zijn voornamelijk betrokken bij de aanpassing van de samenstelling van aluminiumvloeistof:
- Aluminium element: Met een typisch percentage van meer dan 85%, is aluminium het primaire bestanddeel van de aluminiumlegering van spuitgietwerk. De vloeibaarheid, krimp, warmscheurneiging en mechanische eigenschappen van aluminiumlegeringen worden aanzienlijk beïnvloed door aluminiumelementen. Op basis van de beoogde toepassing en de prestatienormen van het product, moet je de samenstelling en het soort aluminiumelement bepalen.
- Legeringselementen: Naast aluminiumelementen moeten de juiste hoeveelheden legeringselementen, zoals magnesium, zink, koper, enz. worden toegevoegd. De mechanische eigenschappen, corrosiebestendigheid en thermische stabiliteit van aluminiumlegeringen kunnen allemaal worden verbeterd door deze legeringselementen. Kies het juiste type legeringselement en gehalte op basis van de behoeften van de toepassing en prestaties van het product.
- Onzuiverheden: IJzer, silicium en andere onzuiverheden kunnen zich tijdens het smelten met de aluminiumlegering vermengen. Deze onzuiverheidscomponenten hebben invloed op de kwaliteit en de prestaties van de aluminiumlegering. Daarom moet de samenstelling worden gewijzigd om de hoeveelheid onzuivere componenten te elimineren of te verlagen.
Chemische analysetechnieken kunnen worden gebruikt om routinematig de aluminiumvloeistof te detecteren tijdens het aanpassingsproces van de samenstelling om de chemische samenstelling en onzuiverheidsconcentratie te bepalen. De samenstelling van de aluminiumvloeistof wordt gewijzigd in overeenstemming met de testresultaten om te voldoen aan de specificaties van de productprestaties.
Een cruciaal onderdeel bij het veranderen van de samenstelling van de aluminiumvloeistof is kwaliteitscontrole. Om de kwaliteit en zuiverheid van de grondstoffen te garanderen, moet deze strak geregeld worden, te beginnen bij de grondstoffen. Tegelijkertijd moeten variabelen zoals de smelttemperatuur, de duur en het ladingspercentage tijdens de hele operatie worden beheerd om te voorkomen dat de kwaliteit van het gesmolten aluminium afneemt. Om er zeker van te zijn dat de prestaties en kwaliteit van vloeibaar aluminium aan de specificaties voldoen, moet het ook routinematig getest en geëvalueerd worden.
Ontwerp en productie van mallen

Basisprincipes van matrijsontwerp
- Functionaliteit: De matrijs moet de verwachte matrijsfunctie kunnen uitvoeren en garanderen dat de grootte, vorm en nauwkeurigheid van het product voldoen aan de specificaties.
Rationele structuur: De structuur van de mal moet eenvoudig en gemakkelijk te begrijpen zijn, eenvoudig te produceren en in elkaar te zetten, en gemakkelijk te vervangen en te onderhouden tijdens het gebruik. - Stabiliteit: Om gedurende langere tijd een constante productkwaliteit te garanderen, moet de matrijs een uitstekende stabiliteit en duurzaamheid hebben bij herhaald gebruik.
- Veiligheid: Om ongelukken zoals afspatten, barsten, enz. tijdens het gebruik van de mal te voorkomen, moet er tijdens het ontwerp rekening worden gehouden met de veiligheid van de werking.
- Zuinigheid: De productie- en gebruikskosten van de matrijs moeten geminimaliseerd worden terwijl nog steeds aan de functionele en kwaliteitsnormen voldaan wordt.
Selectie en verwerking van matrijsmaterialen
- Materiaalkeuze: Kies materialen met de juiste sterkte, hardheid, slijtvastheid, corrosiebestendigheid en thermische stabiliteit op basis van de eisen van het product en de bedrijfsomstandigheden van de matrijs (temperatuur, druk, wrijving, enz.).
- Warmtebehandeling: Om de mechanische eigenschappen te verbeteren en de levensduur van het matrijsmateriaal te verlengen, past u de juiste warmtebehandeling toe, zoals afschrikken, ontlaten, carboneren, enz.
- Oppervlaktebehandeling: Om de corrosiebestendigheid en oppervlaktekwaliteit van de mal te verhogen, wordt het oppervlak gepolijst, geslepen, geplateerd en krijgt het extra behandelingen.
Processtroom voor het maken van mallen
- Ontwerp van matrijzen: Tekeningen maken en de structuur van de matrijs ontwerpen op basis van de specificaties van het product en de gebruiksomgeving.
- Materiaalvoorbereiding: Verkrijg of produceer de materialen voor de mal en voer de vereiste voorbewerking en inspectie uit.
- Verwerking en productie: Matrijsonderdelen worden geproduceerd met draadsnijden, EDM, mechanische bewerking en andere technieken volgens de specificaties op de tekeningen.
- Montage en foutopsporing: De verwerkte matrijsonderdelen in elkaar zetten, problemen oplossen en de matrijs testen om er zeker van te zijn dat deze naar behoren werkt.
- onderzoek en acceptatie: Voordat de matrijs wordt vrijgegeven voor gebruik, moet deze grondig worden onderzocht om te controleren of hij voldoet aan alle ontwerp- en productcriteria.
Onderhoud en verzorging van schimmels
- Regelmatige inspecties: Voer regelmatig grondige inspecties van matrijzen uit om problemen zoals slijtage, corrosie, scheuren enz. tijdig te identificeren en aan te pakken.
- Reiniging en onderhoud: Om beschadiging van het matrijsoppervlak en achteruitgang van de productkwaliteit te voorkomen, moet je de matrijs schoon houden en regelmatig olie en andere verontreinigingen van het oppervlak verwijderen.
- Smering en onderhoud: Om slijtage te minimaliseren en de levensduur van de mal te verlengen, moet je de bewegende onderdelen van de mal regelmatig oliën.
- Reparatie en vervanging: Om de regelmatige werking van de mal en de kwaliteit van het eindproduct te garanderen, moeten onderdelen van de mal die ernstig versleten of beschadigd zijn, onmiddellijk worden gerepareerd of vervangen.
- Registratiebeheer: Houd het gebruik, de reparaties en het onderhoud van de mal bij, zodat deze in de toekomst beheerd en onderhouden kan worden.
Aluminium spuitgietproces
Aluminium spuitgieten is een proces waarbij vloeibaar aluminium onder hoge druk in een mal wordt gespoten en wordt afgekoeld om aluminium producten met de gewenste vorm en grootte te verkrijgen.
- Vloeibaar aluminium maken: Om vloeibaar aluminium te maken, moeten aluminiumblokken van hogere kwaliteit eerst gesmolten worden tot een gesmolten toestand en dan worden de nodige legeringscomponenten toegevoegd. Om de zuiverheid tijdens dit proces te garanderen, moet de aluminiumvloeistof zuiveringsprocedures doorlopen, waaronder ontgassen en slakverwijdering.
- Kies een spuitgietmachine: Kies een spuitgietmachine die voldoet aan de specificaties voor spuitgietgoederen wat betreft grootte, vorm en precisie. De twee soorten spuitgietmachines zijn de warme kamer en de koude kamer. Kleine, dunwandige voorwerpen kunnen met de eerste worden geproduceerd, terwijl grote, dikwandige voorwerpen met de tweede kunnen worden geproduceerd.
- Installeren en afstellen van spuitgietmatrijzen: Zet de geplande matrijs op de mobiele en permanente matrijzen van de machine. Maak vervolgens de nodige aanpassingen aan de locatie en de openings-/sluitingsslag van de matrijs om een veilige en nauwkeurige passing te garanderen.
- Gieten en vullen: Gesmolten aluminium komt de matrijsholte binnen via de sprue tijdens het spuitgietproces. Het vuleffect van vloeibaar aluminium en de kwaliteit van het eindproduct worden aanzienlijk beïnvloed door de temperatuur en de snelheid van het gieten. Vullen is het proces waarbij de aluminiumvloeistof snel en onder hoge druk de vormholte vult; het spuitgieten gebeurt na een korte periode van stolling.
- Ontvormen en koelen: Na het vullen met aluminiumvloeistof koelt de matrijs af om het spuitgietwerk uit te harden. De grootte en complexiteit van het product bepalen hoe lang het duurt om af te koelen. Het spuitgietwerk wordt uit de mal gehaald door het te openen nadat het een bepaalde hardheid heeft bereikt.
- Screening en kwaliteitsinspectie: Zodra spuitgietonderdelen zijn ontvormd, moeten ze worden getest op kwaliteit, inclusief afmetingen, gewicht en uiterlijk. Het is noodzakelijk om ongekwalificeerde onderdelen te filteren en te verwerken om er zeker van te zijn dat de kwaliteit van het eindproduct voldoet aan de specificaties.
Post-proces
Bijsnijden en verwijderen van sprues
Sprues en overvloeiers zijn belangrijke elementen in het spuitgietproces die gesmolten aluminium in de matrijsholte leiden. Na het spuitgieten zijn deze structuren niet meer nodig. Daarom zijn het snijden en verwijderen van de sprue cruciale bewerkingsprocedures na het spuitgieten.
- Trimming: To ensure that the die casting satisfies the design specifications, cut out any surplus material around the edge using an edge trimmer or punch. Trimming neatens the die cast by getting rid of extra metal.
- Take out the sprue: This is the canal that connects the mould cavity to the gate. These connecting sections have to be taken out after die casting. Manual, mechanical, or laser cutting techniques may all be used for this operation.
Surface treatment technology
Die castings may have surface imperfections including burrs, pores, and bulges. Surface treatment is often necessary to enhance die castings’ look and functionality.
- Polishing: To eliminate surface flaws and smooth the die casting’s surface, use a polishing machine or hand polishing. Additionally, polishing may improve the metal’s appearance and texture.
- Spray coating: Die castings may have a protective coating applied to their surface using spray coating technology to increase wear and corrosion resistance, among other properties. Paint, plastic, and other materials are often sprayed.
- The technique of applying metal or non-metallic materials to die castings’ surfaces is called electroplating. Electroplating is a technique that may be used to generate a coating layer with specific qualities on the die casting surface, such as nickel or chromium plating.
Heat treatment and strengthening process
The methods of heat treatment and strengthening are essential to enhancing die casting performance even more.
- Heat treatment: The interior metallographic structure of the die casting is modified to enhance its mechanical characteristics and stability by heating and cooling it. Annealing, quenching, and other heat treatment procedures are often used.
- Process of strengthening: Using certain techniques, die castings are made harder and more resistant to wear via the process of strengthening. Die castings with surface hardening treatment, for instance, have a harder surface and better wear resistance.
Quality inspection and finished product packaging
To make sure the die-casting components fulfil the specifications, a quality inspection is required after a number of post-processing procedures.
- Quality inspection: use performance testing, dimensional measurement, visual examination, and other methods to thoroughly assess the die castings’ quality. Die castings that are deemed unqualified must be repaired or discarded.
- Final product packaging: To preserve their integrity during storage and transit, qualified die-cast components need to be packaged properly. Appropriate packing materials and techniques, such as wooden boxes, cartons, plastic bags, etc., may be chosen based on the specifications and features of the die-casting components.
Production management and optimization
creation and execution of production schedules
One crucial step in the aluminium die-casting process is the creation of production planning. It entails giving careful thought to factors including raw material availability, manufacturing capability, and market demand. The main procedures for creating and carrying out production plans are as follows:
- Market research and analysis: Gain an understanding of the competitive landscape, product development trends, and market demand via market research, which also serves as a foundation for production plan design.
- Create production plans: Using the information from market research, company strategy objectives, and available resources, create comprehensive short- and long-term production plans.
- Resource scheduling and allocation: To guarantee the manufacturing process moves along smoothly, logically distribute resources like labour, machinery, raw materials, etc. in accordance with the production plan.
- Production scheduling and execution: Work with the production plan to schedule different production links, make sure that the plan is followed, and promptly address issues that arise throughout the production process.
- manufacturing data may be tracked in real time, allowing for the quick identification and resolution of issues with the manufacturing process. Production plans can also be modified to guarantee on-time delivery.
Keeping an eye on things and making adjustments while producing
Real-time monitoring and adjustments to the manufacturing process are necessary to guarantee the stability and quality of aluminium die-casting. The following are some essential tracking and correction steps:
- Equipment status monitoring: Make sure the die-casting machines, moulds, and other pieces of equipment are in good working order by keeping an eye on their operational state in real time using equipment sensors and instruments.
- Process parameter control: Throughout the die-casting process, critical process parameters like temperature, pressure, and time are monitored and managed in real-time to guarantee the stability and precision of the parameters.
- Quality inspection: To make sure that the product quality satisfies requirements, randomly or thoroughly examine die-casting components to look for issues with size, performance, appearance, and other indications.
- Handling of unqualified products: To avoid a recurrence of the issue, examine the reasons behind unqualified die-casting components and promptly modify the manufacturing process.
- Recording and analysis: To analyse and improve the production process, record a variety of data throughout the process, including process parameters, equipment operating parameters, quality inspection findings, etc.
Management and optimisation of production costs
Cost management is essential to the manufacturing process of aluminium die casting. Here are a few ways to save costs:
- Optimise process parameters: By doing so, you may cut down on energy use and raw material waste.
- Boost production efficiency: By enhancing equipment upkeep and boosting equipment utilisation, bolster production efficiency and lower manufacturing expenses per unit of output.
- Lower the scrap rate: Lower the scrap rate by enhancing quality control, optimising manufacturing procedures, and taking other steps that will cut waste.
- Reasonable inventory management and procurement: To prevent waste and backlogs in inventory, correctly buy raw materials based on real production demands. Effective inventory management also lowers the expenses associated with inventories.
- Management of human resources: Allocating resources sensibly, enhancing worker productivity, and cutting labour expenses.
Development and innovation trends in the aluminium die-casting process
The method of die-casting aluminium is always evolving due to the progress of technology and the shifting needs of the market. The following are some potential breakthroughs and development trends:
- Utilisation of novel materials: Create novel aluminium alloy materials to enhance die castings’ mechanical characteristics and resistance to corrosion. Investigate the potential uses of additional metals in the die casting industry concurrently.
- Intelligent production: To achieve automation, informatization, and intelligence of the production process and to enhance production efficiency and product quality, introduce intelligent technologies such as industrial robots, Internet of Things, big data analysis, etc.
- Encouragement of ecologically friendly manufacturing: As environmental consciousness grows, the aluminium die-casting industry’s green growth is pushed to cut down on resource waste and contamination to the environment during production. For instance, actions like recycling garbage and using ecologically friendly release agents are taken.
- Achieving flexibility in customisation and small batch manufacturing requires developing tools and procedures that can swiftly swap out moulds, adapting to changes in market demand, and realising customisation and small batch production.
- Extend application fields: Investigate the potential uses of aluminium die-casting technology in the domains of aerospace, lightweighting cars, new energy, and other areas, and broaden the range of applications for aluminium die-casting components. To gain more precise and thorough information on innovation and development trends, please refer to relevant literature or specialists.
Safety and environmental issues
Risks to safety and precautions to take while die-casting aluminium:
The process of die-casting aluminium may include several safety risks. Corresponding preventative actions must be done in order to guarantee production safety. The following are some typical safety risks and safety measures:
- Burns from high temperatures: Burns from the high-temperature metal liquid used in the die-casting of aluminium are rather common. Wearing the proper protective gear, such as gloves and shoes, and avoiding direct contact with hot metal liquids are examples of precautions.
- Mechanical injury: Pinching, cutting, and other forms of mechanical harm may happen while a die-casting machine is in operation. Strict adherence to operating protocols, the use of gloves and adequate protective gear, and making sure that equipment safety guards are in place are examples of preventive measures.
- Gas and dust: Dangerous gases and dust may be created during the die-casting of aluminium, endangering the health of the workers. Enhanced ventilation, the use of the proper personal protective equipment, and routine environmental cleaning and monitoring are examples of preventative approaches.
- Noise and vibration: The die-casting machine will produce noise and vibration during operation, which may be detrimental to the workers’ comfort and hearing. Controlling noise sources, using silencers, doing regular hearing examinations, and giving employees a pleasant workspace are examples of preventive methods.
- Additional safety risks include those related to electrical safety, operating at heights, etc. It is necessary to take the appropriate precautions, such as routinely inspecting electrical equipment and guaranteeing the working platform’s safety.
Environmental laws and standards for disposing of waste:
In order to guarantee that the manufacturing process satisfies environmental standards, the aluminium die-casting industry must adhere to pertinent environmental rules and waste disposal criteria. The following are some typical laws pertaining to the environment and garbage disposal:
- Pollutant emission control: In order to guarantee that pollutant emissions meet criteria, aluminium die-casting firms are required by both national and municipal environmental protection rules to regulate the emission of waste gas, waste water, and solid waste.
- Waste categorization and treatment: Depending on the kind and nature of the waste, many treatment techniques are used. Sorting recyclable garbage into different categories and delivering it to certified recycling organisations for processing is necessary. Hazardous waste must be sent to certified disposal facilities, and general waste must also be treated correctly in compliance with applicable laws.
- Environmental protection facilities and equipment: To guarantee that pollutants are adequately treated during the production process, aluminium die-casting companies must be outfitted with the appropriate environmental protection facilities and equipment, such as waste water treatment facilities and exhaust gas treatment devices.
- Environmental impact assessment and acceptance: Before being used, newly constructed, remodelled, and extended aluminium die-casting projects must go through an environmental impact assessment and be approved by the environmental protection agency.
- Improvement of employee awareness and training: In order to guarantee that environmental protection regulations are properly applied throughout the production process, aluminium die-casting companies must provide their staff with environmental protection training to raise their level of awareness and sharpen their operational skills.
Green manufacturing techniques, pollution reduction, and energy conservation:
The aluminium die-casting sector may lower energy consumption, cut emissions, and increase resource utilisation efficiency by using a number of green manufacturing and energy-saving techniques. Here are a few potential actions:
- Optimise process parameters: By carefully choosing the die-casting process’s parameters, you may cut down on energy use and raw material waste. For instance, maximising mould design, managing process variables like pressure and temperature, raising die casting certification rates, and lowering scrap rates.
- Energy recycling: To cut down on energy waste, recuperate and repurpose the waste heat from the aluminium die-casting process using waste heat recovery technology. For instance, die-casting moulds are heated or preheated using waste heat from the smelting furnace.
- Employ clean energy: To lessen reliance on fossil fuels, give priority to the use of clean energy in the manufacturing process, such as solar, wind, and other forms of energy.
- Increase equipment efficiency: Through technological advancements and equipment updates, die-casting machines and other manufacturing equipment may operate more efficiently while using less energy and resources. Use energy-saving devices, such as energy-saving lighting and high-efficiency motors, as an example.
- Boost production management: By making sensible preparations for production schedules, streamlining production procedures, and taking other steps, you may cut down on the amount of energy and resources used during production. Concurrently, we will bolster environmental oversight and management throughout the manufacturing process to guarantee that contaminants are efficiently handled and emissions adhere to regulations.
- Encourage the creation of a green supply chain: Aluminium die-casting businesses may work with suppliers to encourage eco-friendly materials and green manufacturing techniques, as well as to collaboratively accomplish sustainable development objectives.
- Innovation and continual improvement: Always look for new methods and tools, enhance and optimise the manufacturing process, increase the effectiveness of resource use, and use less energy. Employees are also urged to take part in creative projects, energy-saving techniques, and emission-reduction strategies in order to collectively support the company’s sustainable growth.
tot besluit
Aluminum die casting is a critical process that involves the selection of high-quality ingots that meet specifications and undergo strict quality control. The smelting and processing of aluminum alloys includes raw material preparation, heating and melting, adjusting melting temperature, composition adjustment, slag treatment, degassing treatment, controlling melting time, etc. Aluminum is a key material in the production of a variety of products, including molds. The process of matrijsontwerp involves selecting and processing materials, ensuring they meet the required specifications, and are appropriately heat treated and surface treated. Aluminum die castings undergo a variety of surface treatment techniques to enhance their appearance and functionality. Die-casting aluminum is a rapidly evolving process that continues to evolve due to technological advances and market demand. The industry is exploring new materials to enhance the mechanical properties and corrosion resistance of die-casting parts. Intelligent production technology is continuously introduced to improve efficiency and product quality. The aluminum die-casting industry is also promoting eco-friendly manufacturing with the aim of reducing resource waste and environmental pollution. The industry is also exploring the application of aluminum die-casting technology in aerospace, automobile lightweighting, and new energy fields.