CNC aluminum parts refer to aluminum parts made using computer numerical control (CNC) machining technology. CNC machining is a modern manufacturing method based on computer numerical control technology that can produce aluminum parts of various shapes and sizes with high precision and efficiency.
CNC aluminum parts have wide applications in many fields, such as aerospace, automotive, electronics, medical equipment, etc. These parts usually require high precision, high strength, and lightweight characteristics to adapt to different application scenarios. CNC processing technology can meet these requirements and be able to process aluminum materials into various complex shapes and structures.
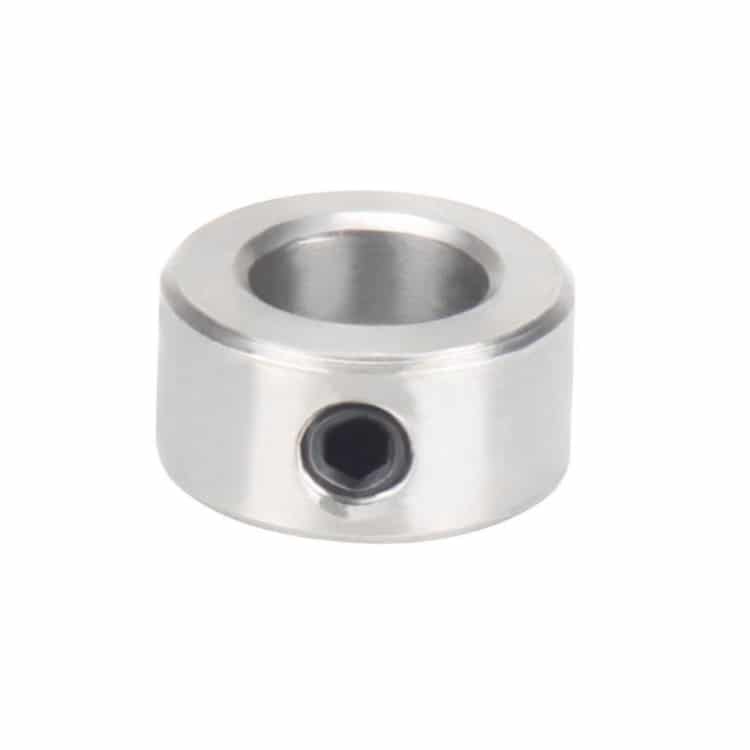
The process of customizing CNC aluminum parts
Principles of CNC machining of aluminum
Aluminum CNC machining is a technology that uses a computer control system to perform CNC machining of aluminum materials. It writes processing programs, inputs processing and parameters into the computer, and then controls the machine tool through the computer control system so that it can process according to the predetermined path, speed and processing depth. Aluminum CNC processing technology has the characteristics of high precision, high efficiency, high stability and high flexibility.
Manufacturing process of custom CNC aluminum parts
- Design and Modeling: We use Computer Aided Design (CAD) software for part design and modeling. Designers can design the shape, size and structure of parts according to needs, and create digital models.
- Material preparation: Cut the required aluminum materials into appropriate sizes and shapes, and perform necessary surface treatments, such as cleaning, polishing, etc.
- CNC processing: Import digital models into CNC machining centers for automated processing. The machining center can perform precise cutting, drilling, milling and other operations based on the model to achieve high-precision processing.
- Inspection and quality control: Conduct quality inspection on the processed CNC aluminum parts to ensure that they meet the design and usage requirements.
- Assembly and use: Assemble the CNC aluminum parts into the corresponding products and perform necessary use testing and maintenance.
In summary, CNC aluminum parts are an advanced manufacturing method that enables high-precision, high-efficiency, and lightweight parts manufacturing. The CNC aluminum parts we manufacture have a wide range of applications in many fields.
What should we pay special attention to when processing CNC precision parts?
When processing CNC precision parts, there are some important precautions that require special attention:
Design and drawing preparation:
Ensure design drawings are accurate and contain all necessary dimensions, tolerances and surface requirements.
Design part shapes and structures rationally, considering limitations and challenges that may arise during processing.
wybór materiału:
Choose appropriate materials based on the function and requirements of the part. Different materials have different mechanical properties and processing characteristics, which need to be selected according to the actual situation.
Tool selection and cutting parameters:
Select appropriate tool types, tool sizes and cutting parameters based on material type, part shape and processing requirements.
Pay attention to the settings of parameters such as cutting speed, feed rate, and cutting depth to ensure processing quality and tool life.
Clamping and positioning:
Choose the appropriate fixture and positioning method to ensure the stability and accuracy of the parts during processing.
Avoid excessive or uneven clamping force, which may cause deformation or affect processing accuracy.
Processing sequence and process planning:
Properly plan the processing sequence to avoid increased difficulty in subsequent processing due to residual stress or deformation during processing.
According to the characteristics and requirements of the parts, select the appropriate processing technology, such as milling, drilling, thread processing, etc.
Processing monitoring and quality inspection:
During the machining process, the machining status is monitored in a timely manner and the cutting conditions and surface quality are observed.
Carry out necessary dimensional measurements and surface inspections to ensure that the processing accuracy and quality meet the requirements.
Tool management and maintenance:
Check and replace cutting tools regularly to maintain processing quality and tool life.
Pay attention to the cleaning, lubrication and storage of knives to prevent damage or rust.
Safety Precautions:
Observe safe operating procedures and wear personal protective equipment to ensure the safety of operators.
Ensure that machine tools and equipment are in normal working order and perform regular maintenance and inspections.
What three elements must be included in the CNC aluminum parts processing program?
The three elements of the CNC aluminum parts processing program include: design, processing technology and quality control.
First, design is the basis of the CNC aluminum parts machining program. Design factors include the shape, size, material, etc. of parts. During the design process, it is necessary to consider the functional requirements, assembly requirements and cooperation with other parts of the parts. The designer also needs to use CAD software for drawing to ensure the accuracy and feasibility of the design.
Secondly, the machining process is the core of the CNC aluminum parts processing program. The machining process includes selecting appropriate machine tools, cutting tools, and cutting parameters. During the processing process, it is necessary to select the appropriate processing method according to the shape and material properties of the part, such as turning, milling, drilling, etc. At the same time, it is also necessary to determine the processing parameters such as cutting speed, feed speed and cutting depth to ensure the accuracy and surface quality of the parts.
Finally, quality control is an important part of the CNC aluminum parts machining procedure. Quality control includes inspection of raw materials, monitoring of processing and inspection of final products. During the processing, regular maintenance and upkeep of processing equipment is required to ensure its normal operation. At the same time, measuring tools need to be used to inspect the size and surface quality of the parts to ensure that the parts meet the design requirements. If problems are found, the processing technology needs to be adjusted in a timely manner to improve product quality.
To sum up, the three elements of the CNC aluminum parts processing program include design, processing technology and quality control. These elements are interrelated and are indispensable. Only on the basis of doing well in these three aspects can high-quality CNC aluminum parts processing be achieved.
Cutting parameters for CNC machining of aluminum materials
The cutting parameters of CNC machining of aluminum mainly include cutting speed, feed speed and cutting depth. The selection of these parameters directly affects the processing quality and efficiency, so reasonable settings should be made based on the specific situation. Cutting speed: Cutting speed refers to the length of aluminum material cut by the cutting tool per unit time. For aluminum materials, the cutting speed is generally high, usually between 100-300m/min. If the cutting speed is too low, the cutting force will increase and the tool wear will accelerate. If the cutting speed is too high, the surface roughness of the aluminum material will increase, and even burrs and other problems will occur.
- Feed speed: The feed speed refers to the distance the cutting tool moves to the aluminum material per unit time. Feed speed is generally low, usually between 0.05-0.5mm/r. If the feed rate is too low, the processing efficiency will be low, and if the feed rate is too high, the surface roughness of the aluminum material will increase.
- Depth of cut: Depth of cut refers to the distance between the cutting tool and the surface of the aluminum material during each cut. The depth of cut should be determined based on the hardness of the aluminum, the size and material of the tool, and other factors. Generally speaking, the cutting depth should not be too large, so as not to cause a decrease in processing accuracy or accelerated tool wear.
In short, the cutting parameters for CNC machining of aluminum need to be reasonably set according to specific conditions to ensure processing efficiency and processing quality. When setting cutting parameters, the characteristics and processing requirements of aluminum should be fully considered, and continuous adjustments and optimizations should be made to improve processing efficiency and quality.
The precision of CNC machined parts
The precision of CNC machined aluminum parts can reach a very high level, often to a few microns (μm) or even smaller. Here are some common precision requirements for CNC machined aluminum parts:
- Dimensional accuracy:CNC machining can achieve high dimensional accuracy, typically achieving tolerance requirements of ±0.01mm or less. This means that the dimensions of the machined part are very close to the dimensions on the design drawing.
- Surface roughness:CNC machining can control the surface roughness of parts to meet specific requirements. Surface roughness Ra 0.8μm or less can usually be achieved, and sometimes even Ra 0.4μm or less can be achieved.
- Parallelism and perpendicularity:CNC machining can ensure the parallelism and perpendicularity of parts and ensure that the relationship between the various surfaces of the parts meets the requirements. Parallelism and verticality requirements within 0.02mm can usually be achieved.
- Aperture accuracy:CNC machining can achieve high-precision aperture processing, including drilling, reaming, etc. It is usually possible to achieve H7 level aperture accuracy, that is, the aperture is very close to the size required by the design.
It should be noted that actual accuracy requirements depend on specific part design and processing requirements. Different materials, shapes and processing methods may affect accuracy. In addition, factors such as the performance of the machine tool, tool quality and processing environment also need to be considered.
Application of CNC machining technology in aluminum alloy parts processing
- Design and processing of parts
CNC processing technology can be programmed according to the design requirements of the parts to process aluminum alloy parts.
Various complex-shaped parts, such as curved surface parts, aperture parts, etc., can be processed through CNC processing equipment to meet the needs of different industries.
- Processing optimization
CNC machining technology can improve processing efficiency and quality through optimized processing.
By optimizing parameters such as cutting tools, cutting speed and feed speed, cutting time and cutting force can be reduced, and processing efficiency and surface quality of parts can be improved.
- Inspection and measurement of parts
CNC processing technology can detect and measure parts through the measuring device that comes with the processing equipment.
The size and shape of the parts can be monitored in real time through the measuring device, thereby ensuring the quality and accuracy of the parts.
- Repair and modification of parts
CNC processing technology can realize the repair and modification of aluminum alloy parts.
Damaged parts can be repaired through CNC processing equipment, or old parts can be transformed, thereby improving the service life and performance of the parts.
What are the precision machining surface treatment methods of CNC aluminum products?
After precision machining of CNC aluminum products, in order to improve their surface quality and corrosion resistance, surface treatment is required. Common surface treatment methods include anodizing, electrophoretic coating, sandblasting, polishing, etc.
- Anodizing: Anodizing is a common surface treatment method that can form a dense and uniform oxide film on the surface of aluminum products to improve the corrosion resistance and surface hardness of aluminum products. At the same time, anodizing can also change the color of aluminum products through dyeing and enhance their beauty.
- Electrophoretic coating: Electrophoretic coating is a method of attaching paint to the surface of aluminum products, which can form a uniform and dense coating to improve the corrosion resistance and surface quality of aluminum products. Different coatings can be used for electrophoretic coating, such as polyester, epoxy, acrylic, etc.
- Sandblasting: Sandblasting is a method of mechanical surface processing. It can polish the surface of aluminum products by spraying abrasives at a high speed to remove surface burrs and stains, thereby improving its surface finish and aesthetics.
- Polishing: Polishing is a method of grinding and polishing the surface of aluminum products to remove surface burrs and stains and improve its surface finish and brightness. At the same time, polishing can also change the surface morphology and texture of aluminum products and enhance their aesthetics.
In short, surface treatment is required after precision machining of CNC aluminum products to improve their surface quality and corrosion resistance. Common surface treatment methods include anodization, electrophoretic coating, sand blasting, polishing, etc.
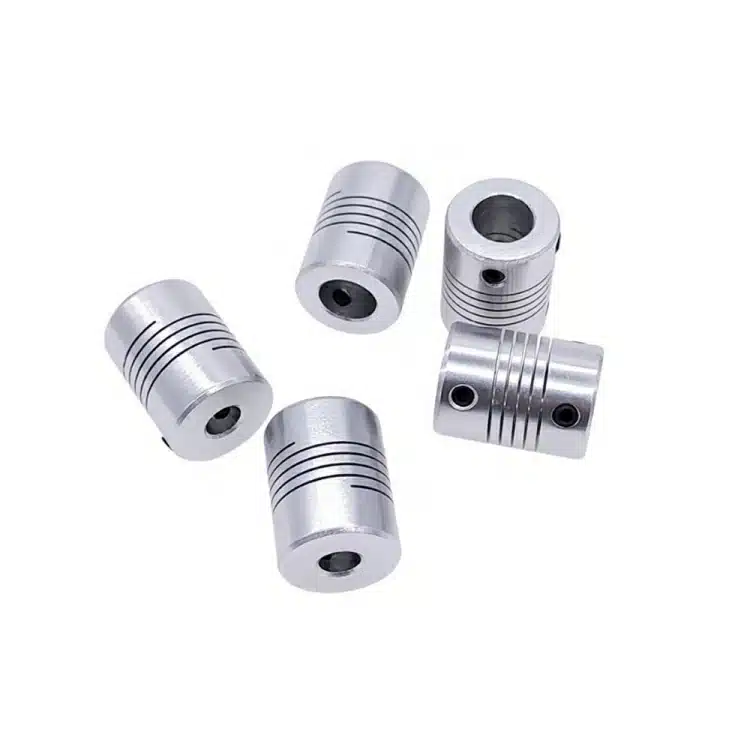
The advantages and disadvantages of CNC aluminum parts processing
CNC machining is a method in which machine tools are controlled by a computer program for processing. It has many advantages and some disadvantages. Here’s a detailed explanation of the pros and cons of CNC machining:
Advantages:
The advantages of CNC aluminum parts mainly lie in high precision, high efficiency, flexibility, reduced labor intensity, stable product quality and customizable services, making CNC processing technology have broad application prospects in the field of aluminum parts manufacturing.
- High precision: CNC machining can achieve very high machining accuracy, usually within a few microns. This makes CNC machining very suitable for industries that require high-precision parts, such as aerospace, medical equipment, etc.
- High Repeatability: Since CNC machining is controlled by a computer program, it ensures that every part is the same size and shape. This is very important for mass production, increasing production efficiency and reducing human errors.
- Versatility: CNC machine tools can perform a variety of different types of machining operations, such as milling, turning, drilling, cutting, etc. This makes CNC machining extremely flexible to meet the needs of different industries and applications.
- High degree of automation: During the CNC machining process, the operator only needs to write programs and monitor the operation of the machine tool without directly participating in the machining process. This reduces labor costs and enables continuous processing without human intervention.
- High machining efficiency: CNC machine tools can process at higher speeds and feed rates, thereby improving production efficiency. In addition, due to the high degree of automation, human errors and downtime can be reduced, further increasing processing efficiency.
shortcoming:
- High Cost: CNC machine tools are costly to purchase and maintain. Additionally, operators need to be trained to write programs and operate machine tools, which also increases training costs.
- High requirements for operators: CNC machining requires operators to have certain programming and machine tool operating skills. For operators without relevant experience, learning and mastering these skills may take some time and effort.
- Requires professional maintenance: CNC machine tools require regular maintenance and upkeep to ensure their normal operation and accuracy. This requires professional technicians to maintain, increasing maintenance costs and workload.
To sum up, CNC processing has the advantages of high precision, high repeatability, versatility, high degree of automation and high processing efficiency. However, it also suffers from the disadvantages of high cost, high operator requirements and size, and the need for professional maintenance. In practical applications, the suitability of CNC machining needs to be evaluated according to specific needs and conditions.
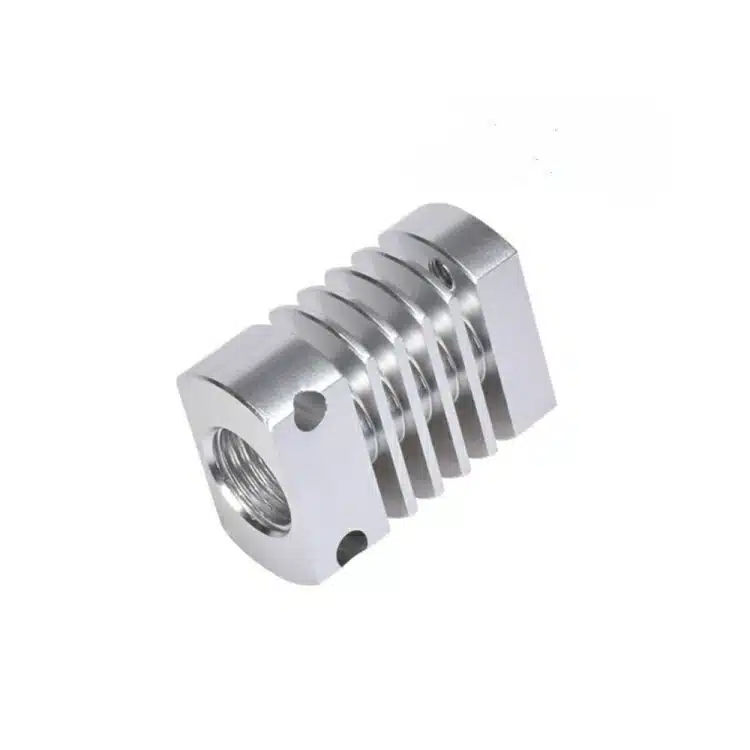
Application fields of aluminum CNC processing
- Automobile manufacturing industry: Aluminum CNC processing technology has been widely used in the automobile manufacturing industry.
For example, the processing of parts such as automobile bodies and engines requires high-precision and high-quality processing, and aluminum CNC processing technology can meet these needs.
- Aerospace industry: CNC processing technology for aluminum materials also has important applications in the aerospace industry.
The aerospace industry has very high requirements for precision and quality of parts, and aluminum CNC processing technology can achieve high-precision, high-quality processing, so it is widely used in aerospace manufacturing.
- Electronic product manufacturing industry: The electronic product manufacturing industry has high requirements for the accuracy and size of parts, and aluminum CNC processing technology can meet these requirements.
For example, the casing components of electronic products such as mobile phones and tablet computers usually require high-precision processing, and aluminum CNC processing technology can achieve this requirement. The application fields of CNC aluminum parts are very wide, mainly depending on the accuracy and quality requirements of the parts. With the continuous development of science and technology, the accuracy and efficiency of CNC processing technology will be further improved, and the application fields of CNC aluminum parts will be more extensive in the future.
FAQs about CNC aluminum parts
What aluminum is used for CNC?
CNC machining is a traditional manufacturing process that uses drills and turning tools to create parts by removing material from solid blocks of material. This process is fast, highly repeatable, and ideal for creating parts with tight tolerances. CNC machining can be done with any sufficiently rigid material—from plastic to metal to fiberglass—with aluminum being a popular choice for product teams.
Broadly speaking, aluminum is a strong, non-magnetic, cost-effective material that is highly resistant to corrosion. Here’s everything engineers and designers should know about the most common aluminum types used for CNC machining, and how to choose the type that’s best for their next project.
1.Aluminum 6061-T6
6061-T6 is one of the most popular aluminum alloys on the market and is used by most manufacturing companies as a standard grade for CNC machining. It is versatile and easy to process, and 6061 can even be heat treated differently.
6061-T6 is an excellent general-purpose material suitable for a variety of use cases. Although this material has a good strength-to-weight ratio, it is not suitable for high-stress applications. Common applications include automotive parts such as chassis, bicycle frames, valves, computer parts, and more.
Mechanical specifications:
Ultimate tensile strength: 310 MPa
Elongation at break: 17%
Modulus of elasticity: 68.9 GPa
Hardness: 60 HRB
2.Aluminum 7075-T6
For high stress or high performance applications, engineers should consider 7075-T6. This grade of aluminum is known for its excellent strength-to-weight ratio and its hardness can rival even some softer steels.
It is widely used in high stress applications in the aerospace and military industries. Common applications include aircraft parts, missile parts and fuse parts. Some performance bicycle and sporting goods products also include parts made from aluminum 7075-T6.
Although 7075-T6 has high strength and excellent mechanical properties, it also has its disadvantages. This material is less ductile and less corrosion-resistant than other grades. What’s more, aluminum 7075-T6 may be too expensive for some product teams.
Mechanical specifications:
Ultimate tensile strength: 434 – 580 MPa
Elongation at break: 10-15%
Modulus of elasticity: 69 – 76 GPa
Hardness: 79-86 HRB
Maximum operating temperature: 100°C
Aluminum 2024-T4
Aluminum 2024-T4 is a medium to high strength alloy with good fatigue resistance and fracture toughness. Aluminum 2024-T4 is not as strong as 7075-T6 but is still suitable for aerospace applications.
Common applications for aluminum 2024-T4 include aircraft fuselages, transport vehicle components and wing tension members. However, product teams should be aware that this grade of aluminum has poor corrosion resistance and is highly sensitive to thermal shock.
Mechanical specifications:
Ultimate tensile strength: 200 – 540 MPa
Elongation at break: 14 – 20%
Modulus of elasticity: 71 – 73.1 GPa
Hardness: 70 – 120 HB
Maximum operating temperature: 200 °C
4.Aluminum MIC 6
Aluminum MIC 6 is unique because its specific combination of alloy and casting method was developed to produce stable, high-tolerance plates. MIC 6 offers impressive stress relief performance, outstanding precision and high machinability. Aluminum MIC 6 is also stain-free and non-porous. This sleek, lightweight option can be found in machined parts, electronics, and even laser technology.
One drawback is that MIC 6 threads are not as strong as threads made from 6061, and particularly thin threads can cause early thread failure. Product designers should keep this limitation in mind during the material selection phase.
Mechanical specifications:
Ultimate tensile strength: 166 MPa
Elongation at break: 3%
Modulus of elasticity: 71 GPa
Hardness: 65 HB
Maximum operating temperature: 427°C
5.Aluminum 6082
Aluminum 6082 has similar properties to Aluminum 6061; however, 6082 has slightly higher tensile strength. Additionally, this type of aluminum has the highest strength of all 6000 series alloys and is very resistant to corrosion. The 6082 is a good choice for engineers who want more strength than the 6061 offers but don’t want to invest in the 7000 series.
Aluminum 6082 is ideal for general-purpose applications where increased strength and toughness are required. This material is popular in the construction industry and can be found in many bridges, towers and trusses. However, product designers should keep in mind that thin walls are difficult to produce with aluminum 6082.
Mechanical specifications:
Ultimate tensile strength: 140 – 340 MPa
Elongation at break: 6.3 – 18%
Modulus of elasticity: 69 – 71 GPa
Hardness: 35-56 HRB
Maximum operating temperature: 130 – 150 °C
Choose the right material for the job
If product teams choose to machine parts from aluminum, they can be confident that they are choosing a material that is strong, conductive, and resistant to corrosion. Aluminum alloys 2024-T4, 7075-T6 and 6082 are best suited for high performance applications, while 6061 and MIC 6 can be used in most situations where general purpose aluminum is sufficient.
Because CNC machining is so versatile, it can be difficult for engineers to narrow down the list of materials that are suitable for a specific project. With decades of technical experience, MINDWELL’s team of expert designers and engineers can help make material selection easier for every product team. We are committed to helping every customer innovate and achieve their desired results throughout the manufacturing process – and through our expert consultancy services, teams can be assured that their material selection will meet all key requirements.
Can you CNC 6061 aluminum?
With the continuous development of automobiles, aerospace, electronics and other fields, the requirements for aluminum plates used in CNC processing are also getting higher and higher. As a common aluminum alloy material, 6061 aluminum plate has the characteristics of good processing performance, corrosion resistance, high toughness, and no deformation after processing, so it has been widely used in the field of CNC machining. In the future, with the continuous development of various industries, the demand for 6061 aluminum plates for CNC processing will continue to increase, and at the same time, the requirements for its performance and quality will continue to increase.
When performing CNC machining, you need to understand the product specifications of 6061 aluminum plate. Typically, the specifications of 6061 aluminum plates can range from 0.1mm to 350mm, and the specific specifications can be customized according to actual needs. In addition, it is also necessary to understand the thickness, length, width and other parameters of the aluminum plate in order to better perform CNC processing.
6061 aluminum plate has good processing properties and can be processed in various shapes and sizes. At the same time, it also has good corrosion resistance and high toughness, allowing it to maintain stable performance in various environments. In addition, the 6061 aluminum plate also has good characteristics of not deforming after processing, which can ensure the accuracy of processing precision. When carrying out CNC processing, using 6061 aluminum plates can greatly improve production efficiency and product quality.
6061 aluminum plate for CNC machining has the characteristics of good processing performance, corrosion resistance, high toughness and no deformation after processing, and can meet the needs of different fields. In the future, with the continuous development of various industries, the demand for 6061 aluminum plates for CNC processing will continue to increase, and at the same time, the requirements for its performance and quality will continue to increase. Therefore, it is necessary to continuously strengthen technological research and development and product upgrades to meet the market demand for high-quality aluminum alloy materials.
Why do we usually not choose CNC precision machining method for processing mobile phone casings?
The reasons why CNC precision processing is not usually chosen for processing mobile phone casings are as follows:
High cost: CNC precision machining equipment and technology are relatively complex and require high investment costs. For the mass production of mobile phone casings, the use of CNC precision machining methods may lead to excessive costs and uncompetitiveness.
Low processing efficiency: CNC precision processing is usually a point-by-point or line-by-line processing method. For large-area mobile phone casings, the processing efficiency is relatively low. Mobile phone casings usually need to be mass-produced in a short time, so higher processing efficiency is required.
Material waste: CNC precision machining usually requires the entire workpiece to be fixed on a fixture before processing, and then processed point by point or line by line through the tool. For large-area workpieces such as mobile phone casings, using CNC precision machining methods may lead to a lot of material waste.
Surface treatment limitations: CNC precision machining usually cannot meet the special requirements of the surface of the mobile phone casing, such as smoothness, texture, anti-fingerprint coating, etc. Traditional injection molding, die-casting and other processing methods can better meet these requirements.
Complexity limitations: CNC precision machining has better processing results for parts with complex shapes and structures. However, for workpieces with large areas and many curves such as mobile phone casings, there may be processing difficulties and limitations.
In summary, although CNC precision machining has advantages in some areas, in terms of mobile phone casing processing, it is usually not the first choice due to factors such as high cost, low processing efficiency, material waste, surface treatment limitations, and complexity limitations. Way. In contrast, traditional processing methods such as injection molding and die-casting are more suitable for the mass production of mobile phone casings.
Why should we choose the appropriate cutting fluid when CNC precision machining aluminum alloy?
When precision CNC machining of aluminum alloys, it is very important to select the appropriate cutting fluid. Here are several commonly used cutting fluid types:
Water-soluble cutting fluid: Water-soluble cutting fluid is a common type of cutting fluid that is made of water mixed with additives. It has good cooling and lubrication properties, which can effectively reduce the processing temperature, extend tool life, and improve surface quality. For precision CNC machining of aluminum alloys, it is better to choose a water-soluble cutting fluid that contains anti-corrosion and antioxidants.
High-Performance Cutting Fluids: High-performance cutting fluids are typically synthetic liquids that provide excellent cooling, lubrication, and rust-preventive properties. They are able to provide higher cutting speeds and longer tool life while maintaining lower processing temperatures. For high-speed, high-precision precision CNC machining of aluminum alloys, using high-performance cutting fluid can achieve better processing results.
Dry machining: Dry machining means that no cutting fluid is used during the machining process, but cooling and lubrication are carried out by air or other means. Dry machining can reduce the use and disposal costs of cutting fluid while avoiding the impact of cutting fluid on the environment. However, dry machining may cause problems such as excessive processing temperatures and accelerated tool wear for precision CNC machining of aluminum alloys, so evaluation and selection need to be made based on the specific situation.
When choosing a cutting fluid, in addition to considering its performance characteristics, you should also pay attention to factors such as compatibility with aluminum alloys, environmental friendliness, and operating safety. The best cutting fluid selection should be evaluated based on comprehensive factors such as specific machining requirements, equipment conditions, and material properties, and should follow relevant safe operating procedures and regulations.
The difference between CNC professional processing and precision mechanical parts processing
CNC professional machining and precision mechanical parts processing are two different concepts, and there are some differences in scope, requirements and technology. The following are the differences between CNC professional processing and precision machinery parts processing:
range:
CNC professional machining usually refers to the use of computer numerical control (CNC) technology for the processing of various materials, including metal, plastic, wood, etc. It can range from simple parts to complex structures.
Precision mechanical parts processing focuses more on the processing of high-precision and high-demand mechanical parts, which are usually used in precision instruments, aerospace, medical equipment and other fields.
Processing requirement:
CNC professional processing focuses on production efficiency and cost control, and pursues higher processing speed and lower cost. Although a certain degree of accuracy is also required, compared to precision mechanical parts processing, the requirements for surface quality and dimensional tolerances may be looser.
The processing of precision mechanical parts has higher requirements on dimensional accuracy, surface quality, shape complexity, etc. High accuracy and tolerance requirements are often required to meet specific functional and assembly requirements.
techinque level:
The technical threshold for professional CNC processing is relatively low. Operators mainly need to master basic skills such as CNC programming, machine tool operation and tool selection.
The processing of precision mechanical parts requires a higher technical level and experience, and operators need to have more in-depth knowledge and skills in machining, including precision measurement, process optimization and processing parameter adjustment.
Equipment required:
CNC professional processing is usually performed using CNC machine tools, which can adapt to the processing needs of different materials and shapes.
Precision mechanical parts processing may require more specialized equipment and tools, such as high-precision CNC milling machines, grinders, wire cutting machines, etc., to meet higher processing requirements.
To sum up, there are some differences in scope, requirements and technology between CNC professional machining and precision mechanical parts machining. CNC professional processing pays more attention to production efficiency and cost control, while precision mechanical parts processing pays more attention to high-precision and high-demand processing, which requires a higher technical level and professional equipment. Choosing the right machining method depends on specific machining needs, materials and requirements
What is the CNC cutting speed of aluminium?
CNC cutting speed of aluminum The speed can be determined based on the following points
1.The total length of the outer diameter of the workpiece
2.Smooth and clean required
3.Processing technology
4.Machine turning performance
The speed and knife need to be matched well
Fine car can cost 100-200
Rough turning can cost 200-600