Short description: aluminum die casting for die casting site, automation, intelligent equipment has been applied in the production, but how to make these equipment long-term stable production, the main work is “stability”, find out the fluctuation factors of each link, with feasible and reliable way to restore it to a stable state, “first seek stability, and then seek improvement”, this work is week after week, there is no once and for all, there is no shortcut to go. First seek stability, and then seek to improve”, this work is week after week, there is no once and for all, there is no shortcut to go. Die casting product quality problems encountered at the scene may not be caused by a factor, in solving the problem need to be integrated with a number of factors to deal with, so that the product can be efficient, high-quality stable production. Text use management six factors (5M1E) to find out on the die casting process site may be destabilizing factors, and these factors to control and improve, put forward the die casting process stabilization strategy.
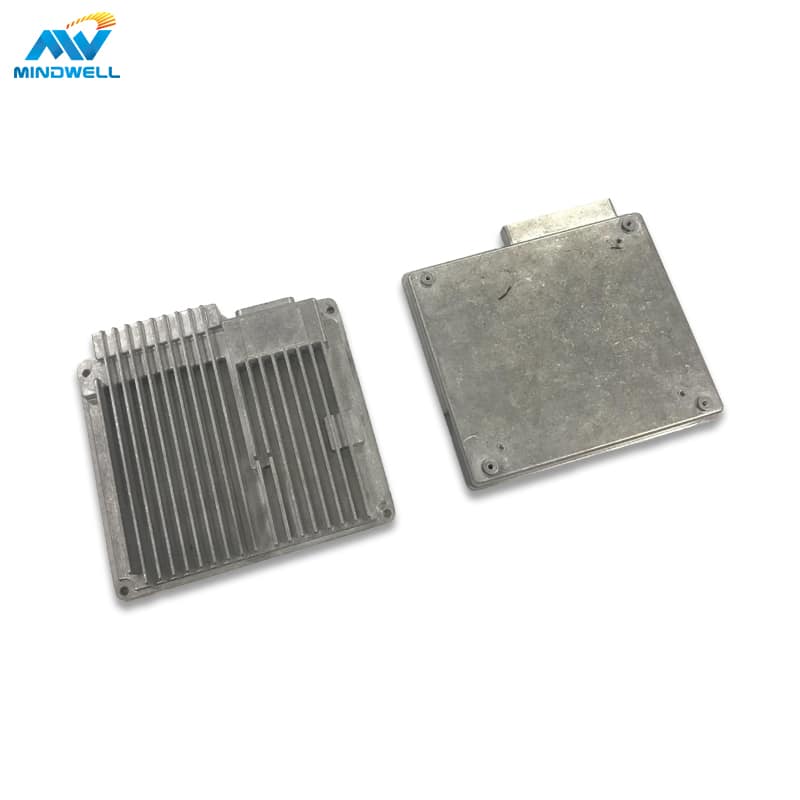
What is Aluminum die casting?
Aluminum die casting is a highly automated, high-efficiency production of complex shaped parts technology. This technology produces aluminum die casting parts with good densification, high precision, less machining allowance, excellent mechanical properties and other advantages, in the automobile, mechanical equipment and other fields have been widely used.
High-pressure aluminum casting industry, die casting of porosity, shrinkage, internal cold segregation problem has been plagued by die-casting people. Although the requirements for the porosity shrinkage holes have a prescribed scale, but often due to a variety of uncertain fluctuating factors in the production process and make the quality of die casting repeated, sometimes good and sometimes bad, which leads to the quality of die casting is not stable.
Due to the rapid filling forming, aluminum die casting parts will be due to a variety of factors inside the residual amount of gas. With the emergence of vacuum die casting, oxygenated die casting, local extrusion and other advanced technology, from a certain degree to improve the internal quality of aluminum die casting parts, but the existence of pores, shrinkage holes, cold segregation still can not be avoided. Even so, it can be done to control the porosity, shrinkage, cold segregation and other problems within a certain range.
Die casting in fact refers to the die casting machine, die casting alloy and die casting mold three elements of the collective name, die casting process is the integration of these three elements applied to the production. Hoda Dini et al. studied the die casting pressure on the deformation of die casting AZ91D alloy casting and the effect of residual stresses, the results of the study show that the die casting pressure on the deformation of the casting and the residual stresses of the casting of the impact of the larger; increase the pressure of the die casting, casting of deformation will be reduced, but surface residual stresses. However, the residual stress on the surface will increase. Many scholars on the mold and die casting in the process of die casting temperature field distribution and temperature gradient and other issues have been studied. p. Sharifi et al. through experiments to study the process parameters in the process of die casting casting influence. The results show that among many process parameters the size of the punch speed has the greatest effect on the porosity of the castings, but there are some special alloys where the effect of slow ejection speed is again greater.
Now more and more companies are using the Internet big data on the die casting process real-time monitoring and adjustment of die casting parameters. The development of die casting process program is a very important part, the rationality of the process directly affects the quality of the castings and subsequent processing and production links. The quality of die casting is often good or bad and many factors, reasonable and effective control of the quality of die casting need to comprehensively consider many factors, the long-term stability of the quality of die casting for the enterprise’s cost, profit and so on is very important, but the complexity of the die casting site makes the control and management of the quality of die casting increased difficulty. Based on this, put forward based on the site management six factors (5M1E) die casting process stabilization strategy, systematic solution to die casting site to die casting quality management problems.
Die casting site problems and measures
When the die casting quality fluctuation, the field technicians often first choose to adjust the process parameters rather than from the root to find the cause. For example:
- When there is internal bad, change the high speed switching point, increase the fast pressure injection speed, increase the booster opening;
- When there is mold pulling, increase the amount of mold release agent spray or extend the spray time;
- When there is a jamming punch, increase the amount of lubricant;
- When the temperature of the aluminum liquid in the heat preservation furnace is not enough to use a flame gun to bake on the liquid surface of the pouring mouth.
Each of the above inappropriate adjustments may bring 3% of the defective rate, there are more than three inappropriate adjustment action may bring more than 10% of the defective rate. So we should not think too much about the problem, but for each problem from the details to find the cause, with the appropriate method to solve the problem from the root and maintain. This is the firm belief that we field technicians need to have.
Die casting site stability factors
When the equipment and mold and process technology conditions have to meet the quality requirements of the die casting, die casting site is the most critical for the stability of the comprehensive factors to implement control. Such as: equipment and mold comprehensive condition, compressed air quality and air pressure fluctuation range, alloy liquid heat preservation effect and temperature fluctuation range, mold temperature and environmental temperature. Comprehensive factors are stable, the quality of die casting can be relatively stable.
Site management six factors
Site management of six factors refers to Man, machine, material, Method, Measurement, Environments, referred to as 5M1E.
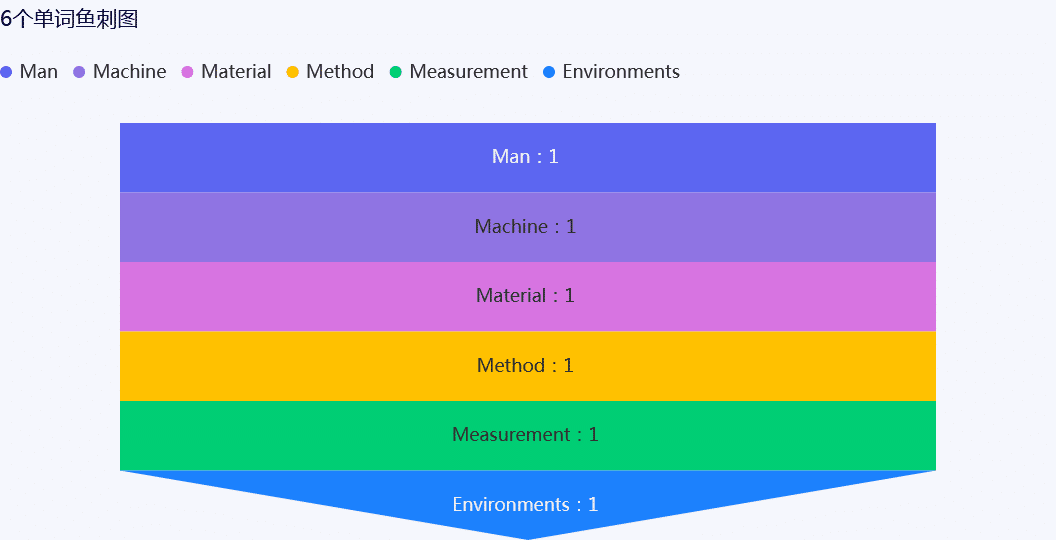
man factor
People dominate the die casting site and are the first of all factors. Including production safety, all the work around the production activities are decided by people. Product quality will always fluctuate, the use of management tools to analyze and solve the problem, the fluctuation value of each link to control the minimum range, reduce the rate of defective products, which all still rely on people.
Machine factor
Machine refers to the work of the mother machine, molds and auxiliary equipment with its matching device. Because of the importance of the mold in the die casting process, will be analyzed separately as a factor below. The ability of the machine equipment is the determining factor of the manufacturing capacity, so the more high-end equipment for the maintenance requirements are also higher.
In the production arrangement process, for different products, choose the machine and equipment suitable for it. Do a good job of daily inspection, so that there are problems can be found in a timely manner, timely repair. Do regular maintenance or choose the machine maintenance, to ensure that the equipment is intact and stable performance. Strictly forbidden to dismantle the east to patch up the west, keep the equipment intact. Die casting production site is easy to ignore the problem points:
- The impact of poor coordination of the connecting part of the ejection rod on the quality of die castings;
- feeding machine feeder is not stable on the quality of die casting.
Spray machine spray volume and atomization effect is not stable can also have an impact on the quality of die casting. Large fluctuations in compressed air pressure, normal air pressure should be controlled at 5.5 ~ 6.5 kg / c ㎡, which is very important; large fluctuations in air pressure caused by the mold release agent pressure delivery pressure also fluctuated greatly. Air pressure and water pressure fluctuations caused by the release agent spray volume and atomization effect with the change of air pressure changes, mold temperature and mold lubrication effect also followed the changes in the quality of the product also fluctuated. So the bottom of the storage tank and the lowest point of the main pipe should be installed with automatic drain valve, regular automatic drainage, minimize the moisture in the compressed air.
Mold factor
In the equipment has to meet the premise of the site conditions, die casting mold condition on the quality of die casting parts of the impact of the main factors. Die casting production process, the site personnel with time and energy on the mold is often the most, so the daily maintenance of the mold is very important, mainly need to pay attention to the following points.
- ensure that the parting surface intact. The parting surface is not good with easy to appear gas edge or flying material, flying material will cause the cavity loss of pressure and no material to make up shrinkage, so that the die casting inside the larger air holes and large areas of loose. In order to quality and safety must be strictly controlled.
- the inner sprue size and shape maintenance. Die casting production site, the inner sprue thickness, width and the extension of the inner sprue control is very important. Production process with the inner sprue is constantly erosion, the inner sprue width, thickness is increasing, the inner sprue extension is getting shorter and shorter, die casting internal defective rate will be higher and higher.
The above phenomenon is called sprue erosion, is die casting production process will inevitably occur phenomenon. Sprue channel erosion brought about by the adverse consequences is common, but also is often ignored. Because of the erosion increased the width and thickness of the inner sprue size so that the inner sprue cross-sectional area increased, caused by the process parameters of the consequences of change as follows:
- The filling resistance is reduced, the flow rate of the inner sprue is changed, and the filling time is also changed;
- shorten the filling time, increase the pressure of gas in the cavity, increase the exhaust resistance;
- Exhaust speed changes, some of the gas can not be discharged in time to remain inside the die casting;
- too late to discharge the gas residue in the die casting inside the formation of pores, and the distribution of the situation from the regular gradually evolved into irregular, continue to erode down the casting inside the cold segregation also gradually appeared.
Therefore, the inner sprue width, thickness and inner sprue extension size change control in a reasonable range is necessary to do the work. According to the empirical data, the extension of the inner sprue should be 1 to 2 times the size of the inner sprue thickness. Its main role is: in the high-speed filling will be slow filling process in the sandwiched channel in the liquid aluminum gas rubbing broken, to avoid the formation of large air holes in the casting, for the reduction of cold separation also has some help.
(3) Cooling water circuit to keep clean and smooth and stable water pressure. Mold temperature control is an effective means to stabilize the quality of die casting. In the absence of mold temperature machine with the case, the mold cooling system is complete and effective die casting production process is necessary to control a link.
The cooling effect is not good, the mold temperature is high (more than 250 ℃), will be due to the steam rebound caused by the mold release agent is difficult to effectively attached, so that the die casting internal shrinkage holes, the surface of the local adhesion of aluminum, etc., but also affect the production efficiency. Excessive cooling will make the mold temperature is low (below 180 ℃), will cause the mold release agent can not be effectively attached, affecting the effect of mold release, water can not be normal evaporation, will cause the die casting internal porosity, cold segregation, local cold material accumulation and other undesirable phenomena.
Die casting production site is easy to ignore a few problem points?
- The gate set and the melting cup with poor quality of die casting.
- exhaust block exhaust slot blockage on the quality of die casting. Production site, especially the old mold will often appear in this situation: the parting of the surface of many places can be exhaust, but only the exhaust slot and exhaust block is blocked, can not be normal exhaust. This phenomenon is often ignored, but in fact it changes the exhaust sequence. Filling order and exhaust order should be opposite to each other, not relative to each other. This is also mistaken for mold exhaust effect is very good, but die casting hole rate is always higher one of the factors.
- cooling water leakage on the quality of die casting. Cooling water leakage is a common problem in die casting site, see is small, in fact, but hides big hidden danger: ① leakage to cavity and melt cup in the water is not only cause local temperature drop problem, when the water meets the aluminum liquid will quickly gasification produce a large amount of hydrogen, and is absorbed by the aluminum liquid after filling into the cavity, this is also one of the factors of the high rate of die casting hole; ② from the point of cold holes, centralized distributor and so on place leakage of water to the mold frame is also Not to be underestimated, the leakage of a larger amount of water it will pull down the temperature of the mold frame so that the temperature of the core is difficult to maintain, but also from the gap into the cavity, which is also one of the factors of die casting hole rate is high.
- oil cylinder oil leakage on the quality of die casting. Cylinder oil leakage will not only produce and water leakage and the same porosity problem, will also cause a larger oil consumption, directly increase production costs, will also leave safety, environmental protection and other hidden dangers.
Material Factors
Raw materials affect the quality of die casting (mainly refers to the porosity) are mainly the following factors.
- the internal density of the aluminum ingot, according to experience to determine the aluminum ingot fracture neat, section crystals fine and uniform can be judged as a good material, while the fracture surface crystals coarse is easy to cause the die casting of the internal air holes, as shown in the figure. The left side of the aluminum ingot section crystals coarse, the right side of the part section crystals fine and uniform.
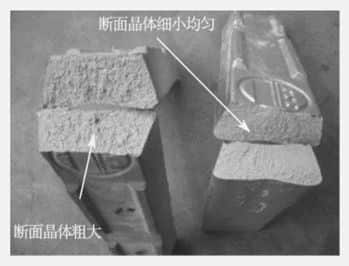
- melting temperature: central melting furnace insulation chamber of aluminum liquid temperature should be controlled at 720 ~ 740 ℃, the temperature is too high easy to cause the material crystals coarse, so that the die casting internal porosity, the temperature is too low is difficult to maintain the turnover process in the various aspects of the cumulative temperature drop.
- heat preservation temperature: heat preservation temperature in the heat preservation furnace should be maintained at 650 ~ 680 ℃, for small die casting when the material temperature is lower than 650 ℃ (especially lower than 640 ℃), die casting is easy to produce internal porosity and cold segregation.Die casting production site is easy to ignore the problem points: melting furnace insulation pool temperature whether to reach 720 ℃ or more; Transfer process whether to cause too much heat loss; Insulation furnace whether there is enough heat preservation and warming capacity.Whether the holding furnace has enough heat preservation and warming capacity, we should pay attention to the following points: whether the seal is intact between the furnace body and the furnace cover; whether the charging trough is sealed with a cover plate; whether the seal is intact between the charging trough and the furnace body.Negligence in each of the above links will cause heat loss, resulting in low temperature of liquid aluminum pouring.
- auxiliary materials: auxiliary materials including refining agent, slagging agent, mold releasing agent, punching oil (particles), etc., the quality of these auxiliary materials, or whether the use of timely and effective will also have a direct impact on the quality of die casting.
Methods Factors
Methods, technology which is one of the management tools throughout the entire process of production activities, each of the above four factors out of the problem can be analyzed by this tool, find out the reasons and develop improvement programs and implementation measures, and then follow up on the effect of the summary, and so on and so forth, but need to pay attention to the following points.
- safe production, equipment management and maintenance work, the daily inspection process and the production process to meet the identified problems in the response rate and countermeasures to ensure that the operating conditions of the equipment to meet the needs of the production technology and process, which is an unshakeable premise.
- (before and after production and production process for the use of mold, maintenance and maintenance work, the potential failure mode analysis (FMEA), the development of wearing parts stocking plan, according to the amount of procurement to formulate a spare mold plan and implementation.
- die-casting process development and implementation and review, daily inspection to ensure the seriousness of the process card.
- aluminum liquid temperature control, this is a problem can not be avoided, the lower limit of 650 ℃ this red line can not be broken.
Most of the production site technicians only focus on the fast pressure injection and pressurization part of the data, in fact, slow pressure injection speed set improperly on the casting quality impact is very big. Die casting production site is easy to ignore the problem: slow injection speed on the quality of die casting; slow filling state theory and the actual difference.
Slow pressure injection is fast pressure injection of the former section, the theory of slow pressure injection is the role of the liquid aluminum full of runners and pushed to the inner sprue near,in fact, when the front peak of the liquid aluminum there are a small amount of has crossed the inner sprue, and sprue and can not be completely full, and also mixed with gas, this phenomenon of the slow speed of slow pressure injection the faster the more serious. Therefore, it is important to choose the appropriate slow compression injection speed.
Blowing is an effective way to remove moisture residue, but the spray machine blowing too many times, blowing too long is not good, over-reliance on blowing not only loss of mold temperature, but also a waste of resources. The lower the mold temperature, the more moisture residue, the more you have to rely on the blowing solution, and so on and so forth. Therefore, the concentration of the release agent should be as high as possible, in order to enhance the lubrication of the mold at the same time to reduce the amount of water sprayed.
Environmental factors
Environmental factors can have an impact on all of the above, mainly in terms of safety, which is also a factor that can not be ignored. Changes in ambient temperature will affect the mood of the personnel, there are security risks, but also affect the accuracy and performance of the equipment, equipment failure rate is always higher in the summer. For precision cutting process and testing process, the ambient temperature for the dimensional accuracy of the impact is great, some small details are often not concerned.
Die casting production site is easy to ignore the problem: for no mold temperature machine with the production site, must be based on the ambient temperature changes in summer and winter, instantly adjust the concentration of the release agent and spray time and cooling water flow, so that the mold temperature is maintained in the appropriate relatively stable temperature range. For example, if the ambient temperature is high in summer, the mold release agent can be used with lower concentration and longer spraying time. In winter, the ambient temperature is low and the mold release agent can be used with higher concentration and shorter spraying time. According to the ambient temperature change in summer and winter, increase the cooling water flow in summer and reduce the cooling water flow in winter. Clean the cooling waterway regularly to maintain the cooling effect.
For the area of high relative humidity of air, when the relative humidity of air reaches 90% or higher, in addition to the die casting is easy to blacken and moldy, the gas produced by the air compressor will also contain a large amount of emulsified water, so that the die casting produces stomata and so on.
High humidity season is easy to cause electrical failure, for the suspension of production equipment should be kept regularly energized, especially weak control system energized can let it rely on self-heating to keep dry.
Measurement Factors
Measurement is quality inspection, which mainly refers to measuring tools, measuring methods, and trained and authorized measuring people. Measurement is an important factor in the modern production process, and it is difficult to guarantee product quality without inspection control. In the measurement control need to pay attention to:
- Whether the responsible person is appointed;
- Whether the prescribed measuring tools are used;
- Whether in the specified measurement point;
- Whether the correct measurement method is applied;
- Whether the measurements are carried out according to a certain frequency;
- Whether records are kept. Improving the ease of operation of measuring instruments and ensuring the accuracy of measurement is helpful for product quality control.
Die casting process stabilization strategy application examples
Mold release agent stabilization
Individually proportioned mold release agent application example shown in the figure below the valve body, due to individual holes in the mold starting slope is very small, so can only use 5027 mold release agent, and the proportion of the concentration of high (1:160 ~ 180), so the product quality is better, can achieve the stability of the site production.
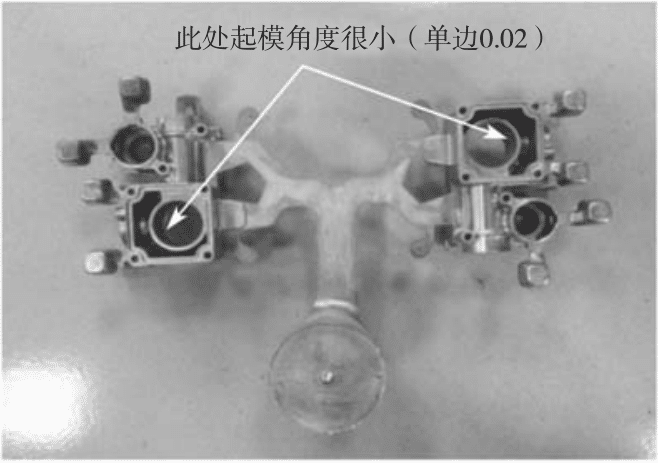
Inner sprue dimensions stabilized
Flame splitter has a diameter of 140 mm and a height of 28 mm, which requires a large surface area with mirror finish without any air holes, micro-spots, flow marks, color difference, etc. Inner sprue size: two points in the middle 18mm × 1.2mm (limit 1.4mm), two points on both sides 16mm × 1.1mm (limit 1.3mm), punch diameter 55 mm, inner sprue size ejection head area ratio of 1:30.3, fast ejection speed set at 2.3m / s (real speed 1.9 ~ 2m / s). By adopting such inner sprue size, the product has better quality and achieves production stability.
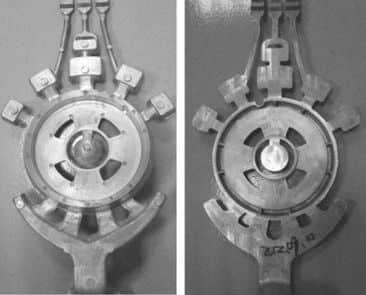
Under the premise of the setting conditions remain unchanged, when the actual speed of fast pressure injection reaches 2m/s or more, the machined surface will appear porosity and micro-spot.
Mold parting surface stabilization
Aluminum die casting splitter as shown in the figure below, this piece has 7 extracted cores die casting, the requirements of the surface of a large area after mirror processing is not allowed to have air holes, micro-spots, flow marks, color difference, etc., this piece in the die casting production process, if the parting surface phi seams, die casting machining surface will appear air holes, and has been verified many times. Therefore, keep the parting surface intact, die casting without phi seams, keep the inner casting channel size in the established range, is this set of mold maintenance work focus.

Wnioski
In the six elements, the results of the analysis of the last five elements, the factors affecting production are wide-ranging, diverse, changing, and precautionary.
But when the bad factors appear, whether the problem can be found in time or get attention, and whether it can be dealt with in time, how to deal with, by whom to deal with, how to deal with the results and so on this is the key. Here all the spearheads are pointing to people, so the talent is the six elements in the most core elements.
For die-casting site, the main work is “stability”, find out the fluctuation factors of each link, with feasible and reliable way to restore it to a stable state, “first seek stability, and then seek to improve”, this work is week after week, there is no once-and-for-all, there is no Shortcut can go.
In the die-casting site a product problem may be caused by several elements of the six elements of the joint role in solving the problem is not only solve one of the elements can solve the product problem, but the six elements, comprehensive solution. Therefore, according to the die-casting process “stability” strategy can be efficient, high-quality solution to product problems. Mindwell is China producent odlewów aluminiowych, we have many years of experience accumulation, in aluminum die casting technology update welcome to communicate with you.