Fundição injectada na indústria automóvel
A MNW fornece serviços personalizados de fabrico de peças automóveis para o desenvolvimento de produtos automóveis. Fornecemos vários processos de moldagem por injeção, CNC e fundição sob pressão em peças para automóveis. O modelo de produção a pedido da empresa satisfaz as necessidades individuais dos clientes.
- Equipamento de processamento avançado e equipamento de ensaio
- Fabricante experiente de peças para automóveis
- Engenharia 24/7, apoio pós-venda
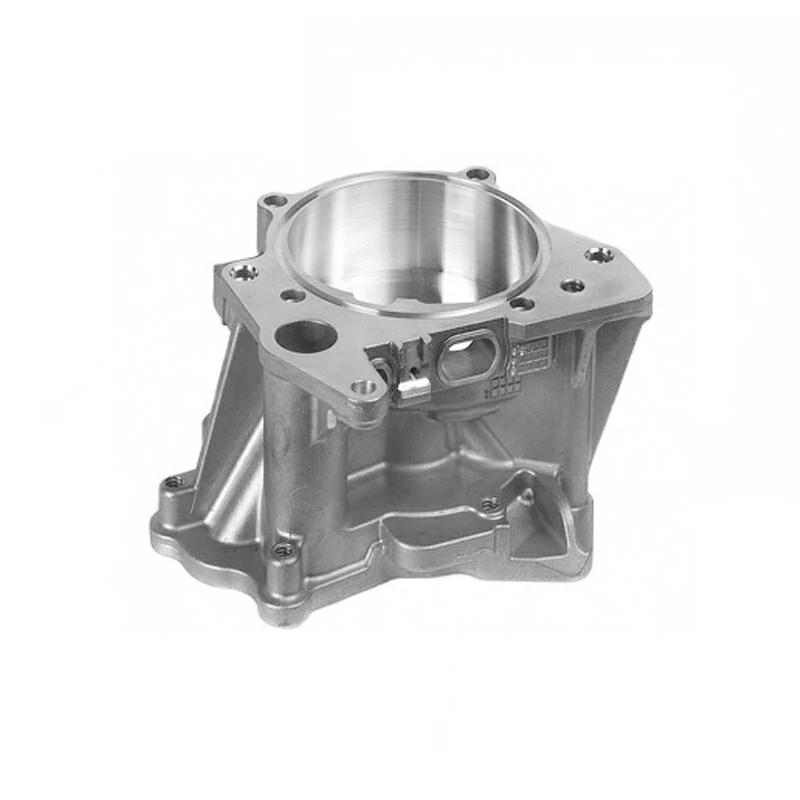
Produção a pedido
Capacidades de fabrico de automóveis
A equipa técnica da nossa empresa e o equipamento avançado de processamento e teste têm estado sempre na vanguarda da indústria. Na MINDWELL, temos uma vasta experiência no fabrico de peças para automóveis. Estamos familiarizados com o processo de desenvolvimento e a procura de produtos automóveis no mercado.
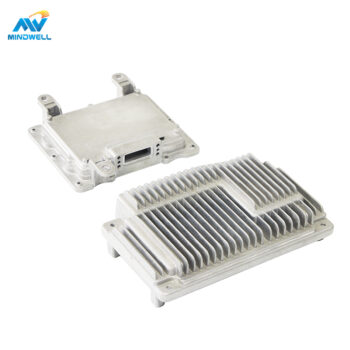
Fundição injectada
O nosso processo de fundição injectada de peças para automóveis é capaz de produzir peças para automóveis mais complexas e precisas com elevada precisão dimensional, elevado acabamento superficial e propriedades mecânicas. A fundição sob pressão de peças para automóveis é amplamente utilizada na indústria automóvel para fabricar blocos de motor, carburadores, caixas de transmissão, suportes e outros componentes críticos que exigem elevada resistência, durabilidade e desempenho.
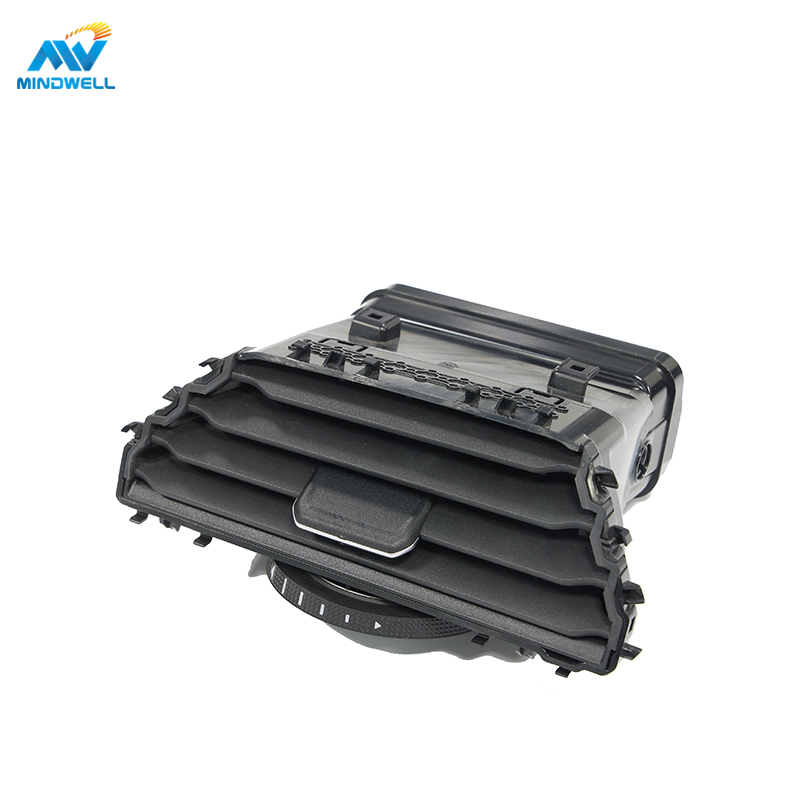
Moldagem por injeção
A moldagem por injeção para automóveis é amplamente utilizada na indústria automóvel devido à sua capacidade de produzir peças de alta qualidade com qualidade consistente e baixo desperdício. A nossa empresa fabrica peças para automóveis, tais como guarnições interiores e exteriores, caixas e outros componentes. Na MindWell, fornecemos aos nossos clientes a capacidade de produzir formas e desenhos complexos com elevada precisão e consistência.
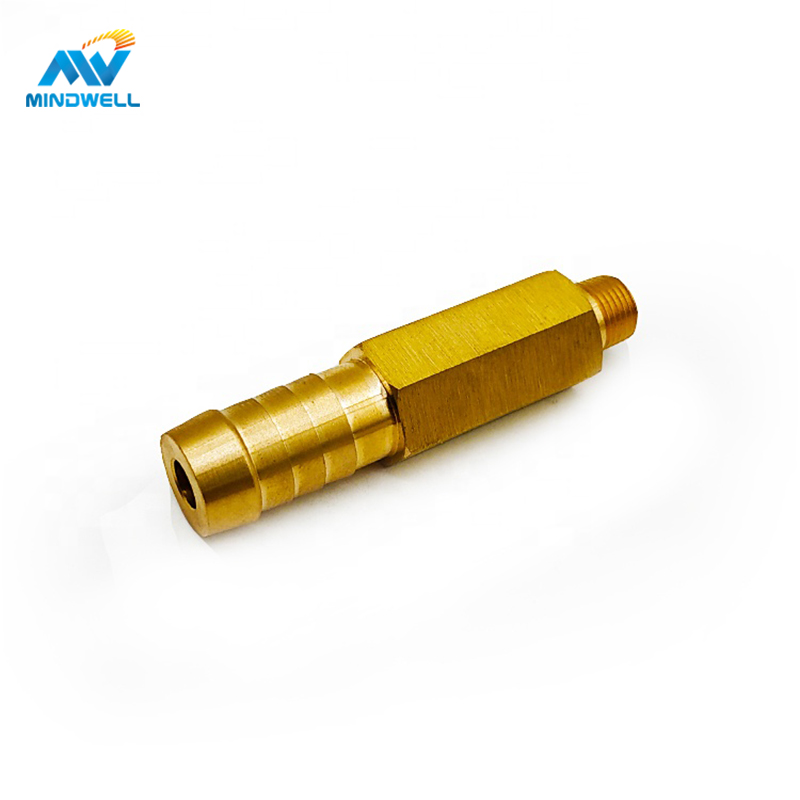
Maquinação CNC
O processamento CNC pode processar peças com alta precisão e alta eficiência, especialmente para formas complexas e peças difíceis, o processamento CNC pode atender a esses requisitos. A nossa empresa possui equipamento de processamento CNC de 4 eixos, que pode processar peças de alta precisão e alta eficiência. O processamento garante a qualidade e a precisão das peças. A maquinagem CNC também pode melhorar a eficiência da produção e reduzir os custos, pelo que é adoptada por cada vez mais fabricantes de automóveis.
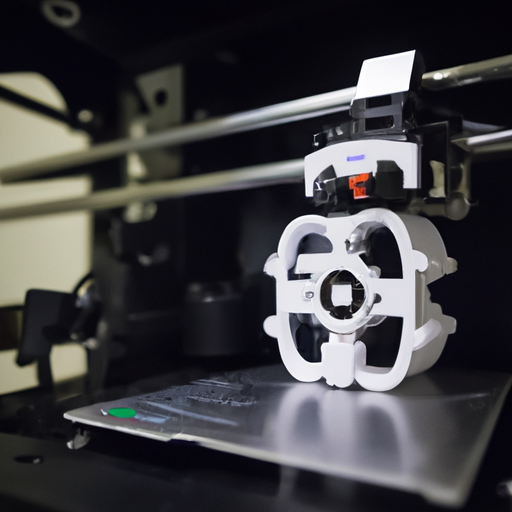
Impressão 3D
Quando os clientes de alguns produtos automóveis pretendem obter peças mais rapidamente, sugerimos-lhes que escolham a impressão 3D de peças automóveis, porque a tecnologia de impressão 3D pode produzir rapidamente peças automóveis de alta qualidade e precisas. Uma peça de automóvel pode ser produzida em poucas horas. Mas a impressão 3D impõe requisitos rigorosos quanto ao número e tipo de peças automóveis produzidas, e a resistência e durabilidade dos materiais também podem ser limitadas.
Fabricante de fundição de componentes para automóveis: Mindwell
Como Fabricante de fundição de componentes para automóveisA MNW fornece soluções personalizadas para peças de automóvel. A nossa empresa tem uma fábrica de fundição sob pressão, uma fábrica de moldagem por injeção, um centro de maquinação CNC e tecnologia de impressão 3D, que podem satisfazer as suas necessidades de fabrico.
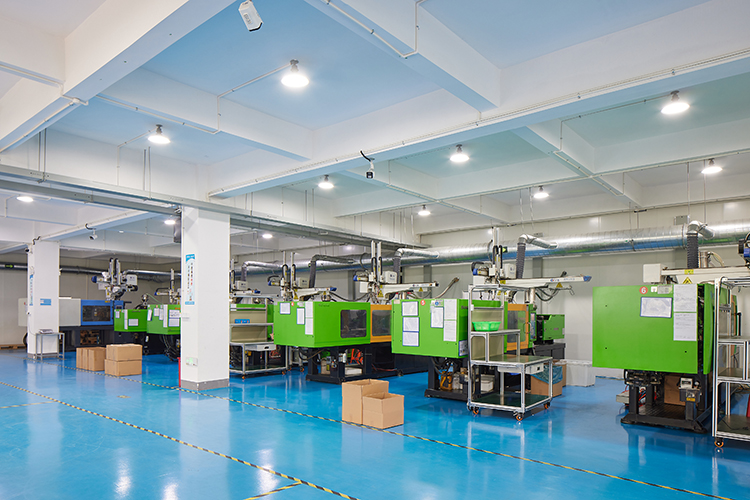
Moldagem por injeção para automóveis
Peças de moldagem por injeção para automóveis Os automóveis têm as caraterísticas de peso leve, moldagem complexa, resistência à corrosão e durabilidade. Proporcionamos aos clientes uma boa liberdade de design e eficiência de produção. Amplamente utilizado em peças interiores e exteriores de automóveis, como painéis de instrumentos, painéis de portas, faróis, luzes traseiras, bancos, volantes e peças sobressalentes.
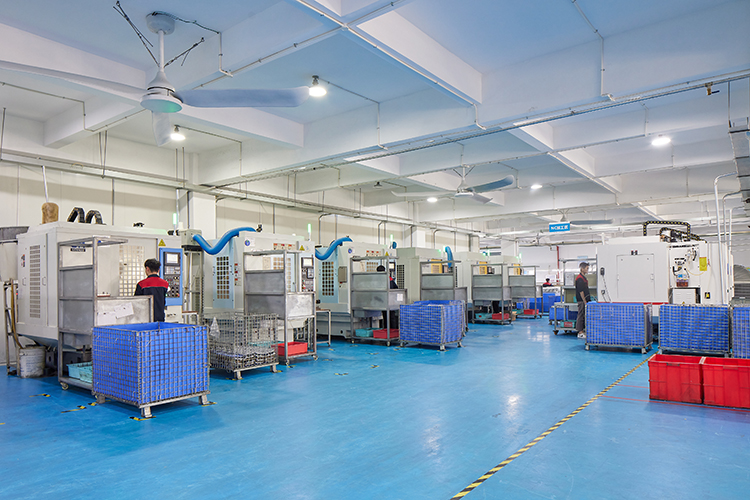
Fundição injectada para automóveis
A fundição injectada de peças automóveis refere-se a peças fundidas para peças automóveis produzidas pelo processo de fundição injectada. As peças fundidas sob pressão produzidas pelo processo de fundição sob pressão têm as caraterísticas de alta precisão, alta qualidade, alta resistência, alta resistência ao desgaste e alta densidade. São amplamente utilizadas em motores de automóveis, transmissões, sistemas de suspensão, sistemas de direção, sistemas de travagem e outros componentes


Comece agora com a fabricação automotiva personalizada de acordo com suas necessidades!
Materiais certos para o desenvolvimento de produtos automóveis
Os materiais de produção das peças para automóveis dividem-se em materiais metálicos, materiais não metálicos e materiais compósitos. Os tipos de carros para diferentes fins e os materiais para diferentes peças são diferentes. A nossa empresa pode personalizar todos os tipos de peças de automóvel que desejar.
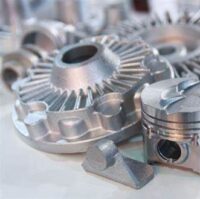
Alumínio
As peças fundidas sob pressão de alumínio têm uma excelente estabilidade dimensional e resistência à corrosão, o que as torna ideais para a indústria automóvel. Na indústria automóvel, as peças automóveis feitas de alumínio fundido sob pressão são mais eficientes em termos energéticos devido ao seu peso reduzido.
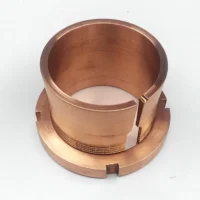
Cobre
Quer se trate de um veículo tradicional a combustível ou de um veículo movido a novas energias, a liga de cobre é a principal matéria-prima de base para os seus componentes importantes. Os materiais de liga de cobre de elevado desempenho são amplamente utilizados em sistemas de arrefecimento de automóveis, sistemas de energia eletrónica, sistemas de travagem e sistemas hidráulicos.
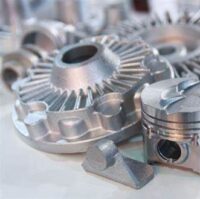
Magnésio
No fabrico de automóveis, as ligas de magnésio são utilizadas principalmente na carroçaria, no motor, no chassis e noutros componentes. Por exemplo, os materiais de liga de magnésio são utilizados na estrutura da carroçaria de alguns automóveis topo de gama, o que pode reduzir eficazmente o peso da carroçaria e melhorar o comportamento e a economia de combustível do veículo.
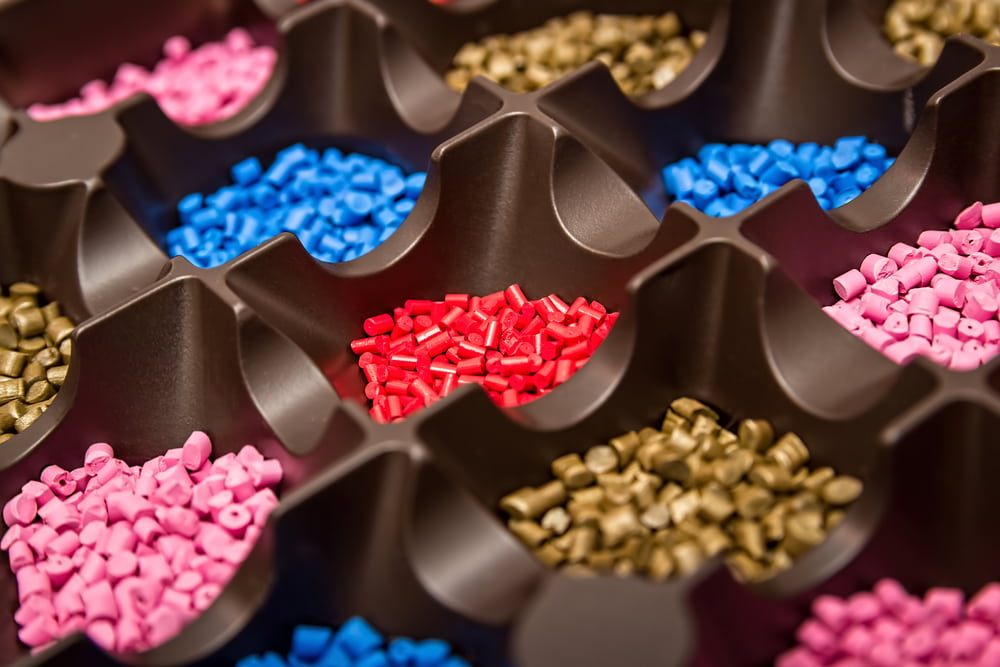
Termoplásticos
Os plásticos são utilizados em automóveis, tais como capôs, ventoinhas de arrefecimento, depósitos de água, grelhas de radiadores, etc. Os plásticos utilizados nos automóveis não só reduzem os custos de processamento, montagem e manutenção das peças, como também tornam o automóvel mais leve, económico em termos de energia e amigo do ambiente
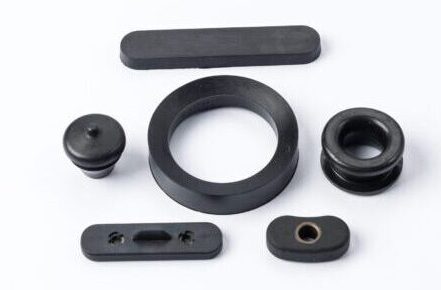
Borracha
As peças de borracha para automóveis estão todas instaladas em peças-chave, como o motor, a caixa de velocidades, o eixo e outras peças do automóvel, que têm de utilizar vedantes de óleo, mas o pequeno vedante de óleo de borracha é a chave para garantir o funcionamento normal destas peças e proteger a segurança e a durabilidade do automóvel

Acabamentos de superfície do fabrico de automóveis
O tratamento de superfície das peças automóveis pode melhorar a estética e a dureza da superfície das peças e evitar o desgaste e a corrosão das peças. Recomendamos a utilização de diferentes métodos de tratamento de superfície em diferentes peças e ambientes.
Por exemplo, recomendamos o uso de cromo / granalha para o console central do carro. explosão, os principais métodos de processamento estão listados abaixo:
- Revestimento
- Pulverização
- Tratamento térmico
- Polido
- Deposição
Produtos automóveis relacionados
A MindWell tem muitos anos de experiência no domínio do processamento de peças para automóveis. As peças automóveis que produzimos são amplamente utilizadas em várias marcas da indústria automóvel.
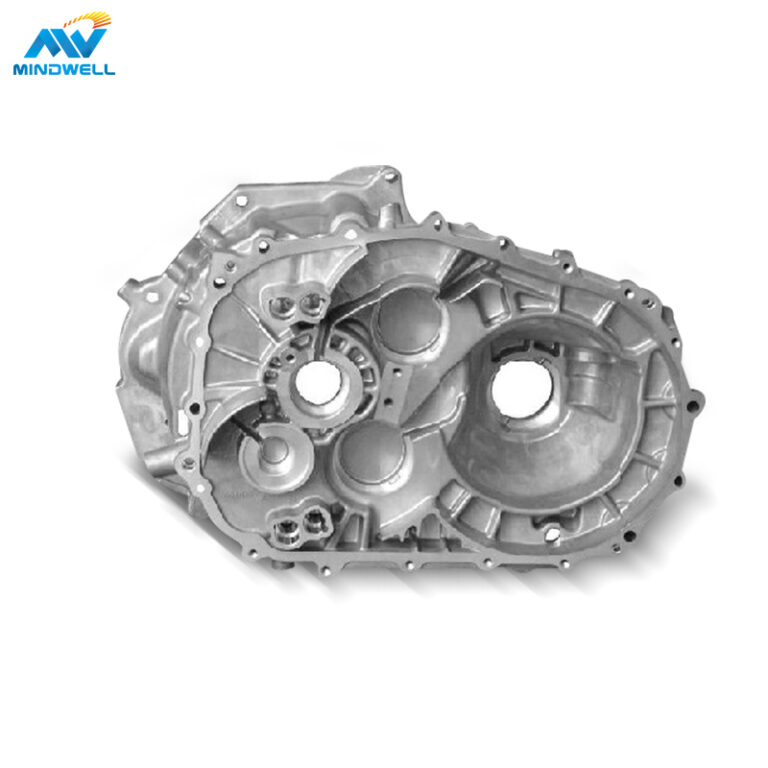
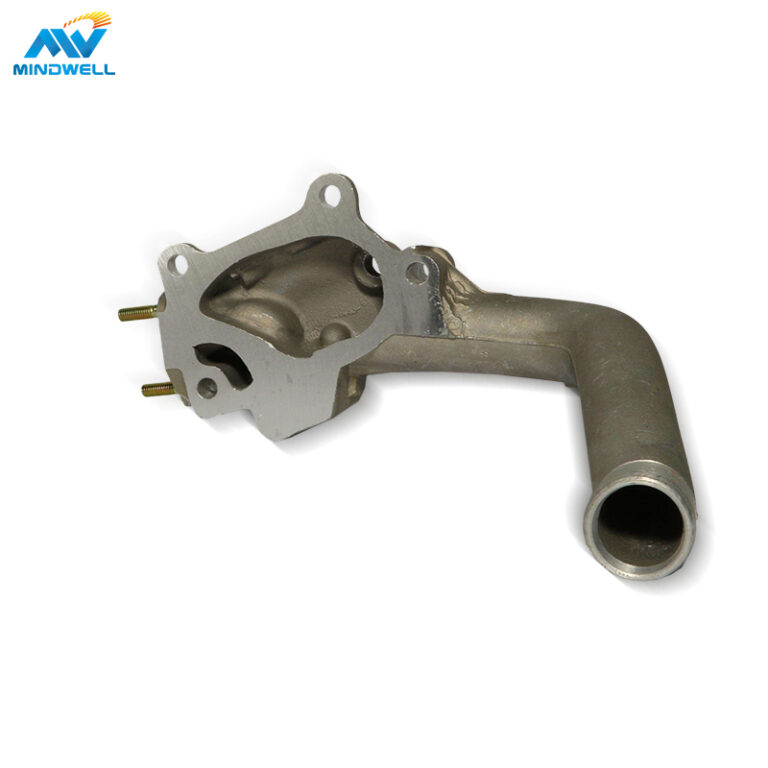
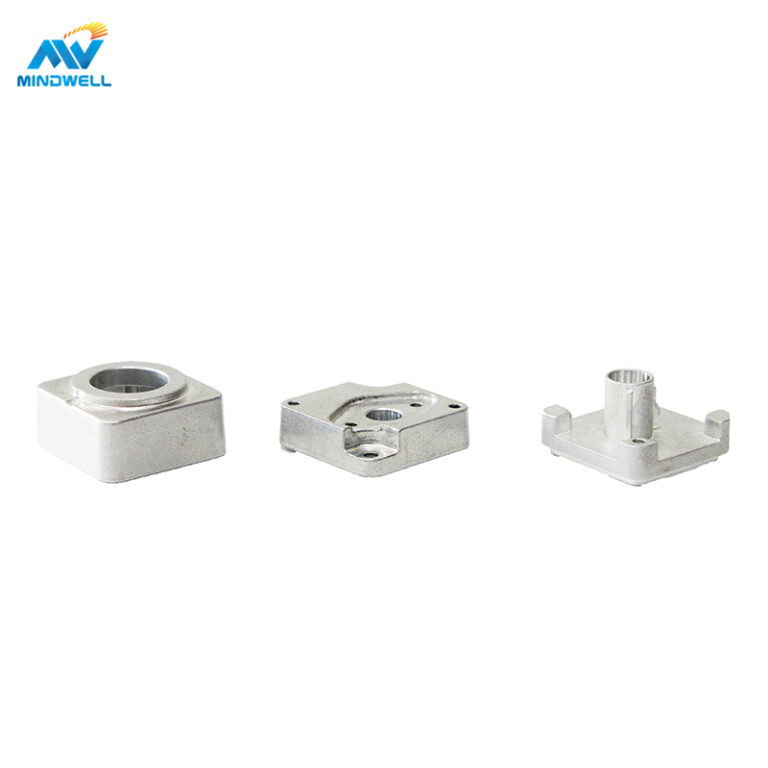

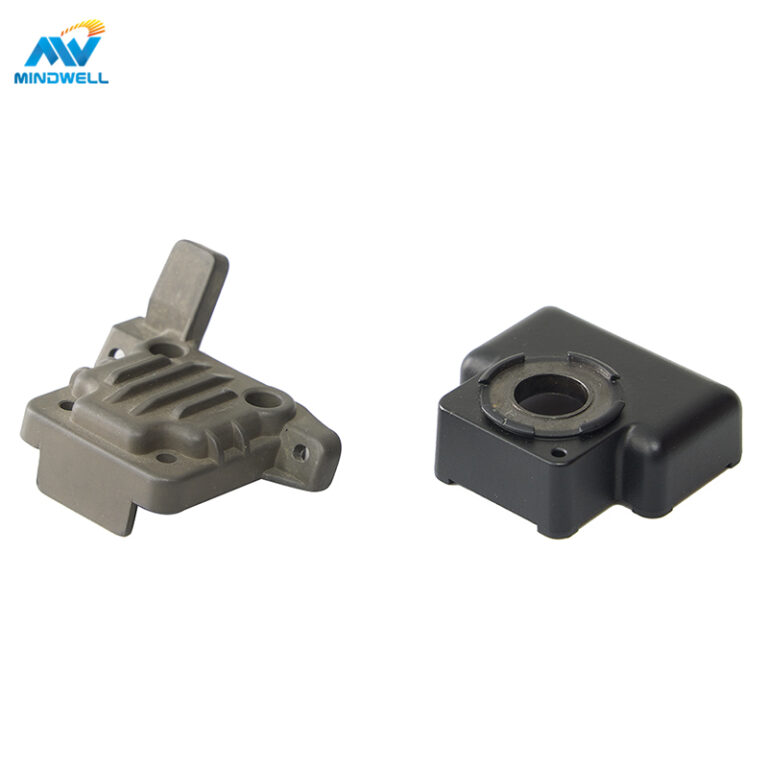
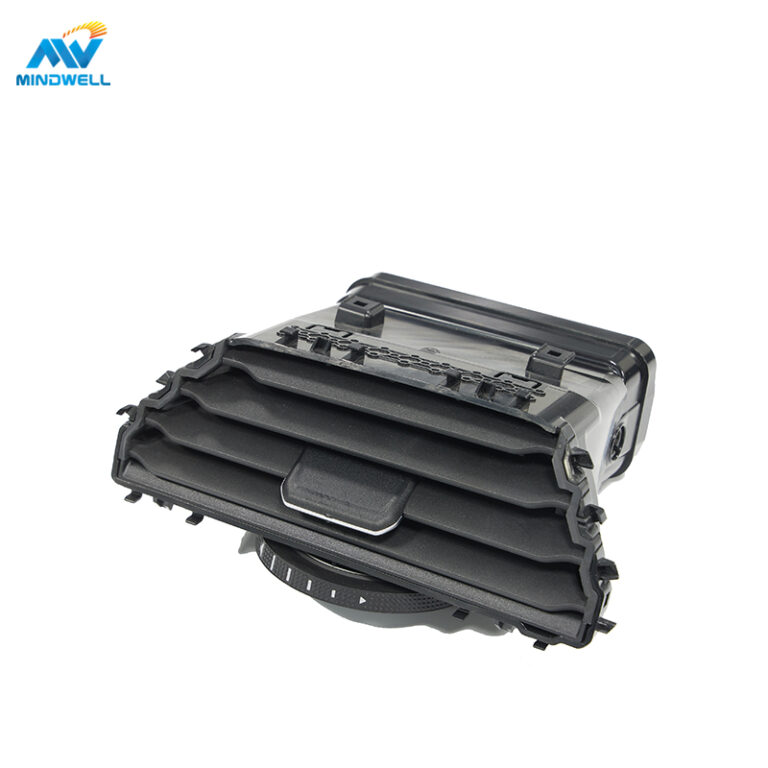
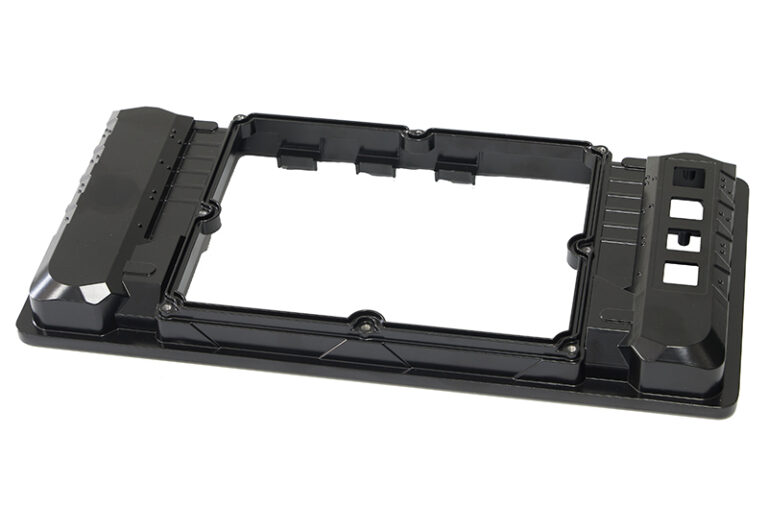
Fundição injectada Aplicação de peças para automóveis
Fornecemos processamento e fabrico de peças de moldagem por injeção para automóveis, peças de fundição sob pressão para automóveis e peças de maquinação CNC para automóveis. Na MindWell, temos experiência na produção de várias peças para automóveis. As aplicações automóveis comuns que realizamos são mostradas na figura

Produzir as peças de fundição sob pressão que os clientes desejam por fundição sob pressão. Os principais materiais são a liga de alumínio e a liga de zinco. Os principais métodos de tratamento de superfície são Cromagem / Pulverização / Jato de areia
- Assistência à retaguarda
- Chave do carro
- Consola central
- peças de motor
- Outros
As peças moldadas por injeção para automóveis têm funções estruturais importantes que podem aumentar a resistência da carroçaria, melhorar o desempenho do veículo e melhorar a experiência do utilizador. Ao mesmo tempo, devido às caraterísticas de elevada eficiência, baixo custo e elevada qualidade da tecnologia de moldagem por injeção, as peças moldadas por injeção para automóveis podem ser produzidas em massa e desempenhar um papel importante no fabrico de automóveis.
- Partes exteriores da carroçaria: tais como portas, espelhos retrovisores, capôs, para-choques, etc.
- Peças de decoração interior: tais como painéis de instrumentos, consolas centrais, bancos, etc.
- Partes funcionais: tais como lâmpadas, injectores de combustível, travões, saídas de ar condicionado

Índice
SOBRE NÓS
Fabricante de fundição de componentes para automóveis na China: Mindwell
Mindwell Company é uma empresa especializada na produção de liga de alumínio, moldes de liga de zinco e processamento de produtos de fundição sob pressão de zinco-alumínio. A empresa está localizada em Xiamen, Fujian, China. É uma das empresas líderes e de destaque que integra I&D, design, produção e operação. Uma empresa que integra a conceção e produção de moldes, fundição injectada, maquinação e peças personalizadas, com muitos anos de experiência profissional na produção de moldes de liga de alumínio e produtos de liga de alumínio, tornou-se um fabricante influente de fundição injectada de liga de alumínio na China.
A Mindwell possui fortes capacidades de conceção e produção. Produz principalmente peças de fundição sob pressão de precisão em liga de alumínio e liga de zinco para automóveis, lâmpadas LED, electrodomésticos, motociclos, ferramentas eléctricas, motores, acessórios electrónicos, etc. A empresa passou a versão ISO9001: 2015 do sistema de qualidade. Certificação, estabelecendo um sistema de gestão rigoroso e completo, a empresa implementa o propósito de "continuar melhorando e operando com integridade", se esforça para inovar e superar continuamente na base existente, e acredita firmemente que: os requisitos do cliente são nossa busca.
Equipamento atualmente detido:
- --30 conjuntos de máquinas de fundição injetada 200T-1600T.
- --2 máquinas de fundição injectada de liga de zinco a quente de 200T.
- --3 centros de maquinagem CNC, 3 máquinas de gravação; 2 máquinas de faísca,
- Máquinas de perfuração CNC: 4 unidades, máquinas de perfuração radial: 8 tornos CNC.
- --5 prensas hidráulicas.
- --20 máquinas automáticas de furar e roscar
- --Um espetrómetro de leitura direta de espetro total
- --10 máquinas de gravação a laser
A empresa está totalmente equipada para fornecer aos clientes serviços integrados, tais como conceção e produção de moldes, fundição injectada de precisão, maquinagem CNC e tratamento de superfícies, e fornecer produtos de alta qualidade.
Obter um orçamento imediato
Solicite hoje mesmo o seu orçamento gratuito de moldagem por injeção e entraremos em contacto consigo para estabelecer comunicação.
Fundição Automóvel: Um guia de perguntas frequentes
A fundição injectada de alumínio é um tipo de peça de fundição injectada produzida por uma máquina de fundição injectada mecânica. Ao deitar alumínio líquido aquecido ou liga de alumínio na porta de alimentação da máquina de fundição injetada, a máquina de fundição injetada realiza a fundição injetada. A forma e o tamanho do produto são limitados pelo molde de fundição. As peças em alumínio ou em liga de alumínio são frequentemente designadas por peças fundidas em alumínio.
Na Mindwell, utilizamos materiais de alumínio de alta qualidade e tecnologia avançada de fundição injectada. As peças de fundição automóvel que produzimos incluem: acessórios de motor automóvel em alumínio fundido sob pressão, blocos de motor em alumínio fundido sob pressão, cabeças de cilindro de motor a gasolina em alumínio fundido sob pressão, balancins de válvula em alumínio fundido sob pressão e válvulas em alumínio fundido sob pressão. Suportes, peças de alimentação em alumínio fundido, tampas de extremidade de motor em alumínio fundido, invólucros em alumínio fundido, invólucros de bomba em alumínio fundido, peças de construção em alumínio fundido, peças decorativas em alumínio fundido, peças de guarda-corpos em alumínio fundido, rodas em alumínio fundido.
O que são a fundição e a fundição sob pressão no processo de fabrico de peças para automóveis?
No processo de fabrico de peças para automóveis, a fundição e a fundição injetada são um dos métodos de processamento de peças para automóveis, especificamente no domínio do processamento de metais.
- Fundição: A fundição é um método que consiste em verter metal ou liga fundida num molde preparado, arrefecer e solidificar para obter peças com a forma pretendida. Durante o processo de fundição, a trajetória do movimento e os parâmetros do equipamento de fundição podem ser controlados utilizando tecnologia de software programada para obter operações de fundição precisas. Por exemplo, as peças fundidas de grandes dimensões, como blocos de motor, cárteres, caixas de transmissão, etc., são normalmente produzidas utilizando processos de fundição.
- Fundição injectada: A fundição sob pressão é um método que consiste em injetar metal ou liga fundida num molde sob alta pressão, arrefecendo e solidificando rapidamente para obter peças com a forma pretendida. A fundição sob pressão é normalmente adequada para a produção de peças com formas complexas e requisitos de elevada precisão. Durante o processo de fundição sob pressão, a tecnologia de software programado pode ser utilizada para controlar parâmetros como a trajetória do movimento, a velocidade de injeção e a pressão da máquina de fundição sob pressão para garantir a qualidade e a precisão das peças. Por exemplo, as cabeças dos cilindros dos motores dos automóveis, as caixas de transmissão, as pinças de travão e outras peças são normalmente produzidas através de processos de fundição injetada.
A aplicação de tecnologia de processamento avançada no processo de fundição e injeção pode melhorar a precisão, a qualidade e a eficiência da produção de peças. Ao utilizar o sistema de controlo CNC, os operadores podem escrever programas para controlar com precisão vários parâmetros durante o processo de fundição ou injeção, realizar a produção automatizada e reduzir o impacto dos factores humanos na qualidade das peças. Ao mesmo tempo, a maquinagem CNC também pode proporcionar mais flexibilidade e ajustabilidade para satisfazer as necessidades de peças de automóveis de diferentes modelos e especificações.

Guia de utilização de peças de fundição injectada para veículos de energia nova
As peças fundidas sob pressão para veículos movidos a novas energias são uma direção importante para o desenvolvimento futuro da indústria automóvel. Com a melhoria contínua da consciência ambiental, a procura do mercado de veículos de energia nova continua a aumentar. As peças fundidas sob pressão, como parte importante dos novos veículos de energia, desempenharão um papel importante no desenvolvimento futuro.
A tecnologia de fundição injetada é um método de fabrico de peças de alta eficiência e qualidade, sendo amplamente utilizada em automóveis, aviação, maquinaria e outros domínios. O fabrico de peças fundidas sob pressão para veículos de energia nova tem de ter as caraterísticas de alta precisão, alta resistência e alta densidade para cumprir os requisitos dos veículos de energia nova em termos de eficiência energética, desempenho de segurança e distância de condução.
A vantagem das peças fundidas sob pressão para veículos movidos a novas energias é o facto de poderem melhorar o desempenho global do veículo, como a redução do peso do veículo, a melhoria da estabilidade e da segurança do veículo. Além disso, as peças fundidas sob pressão para veículos de energia nova também podem reduzir o consumo de combustível e as emissões do veículo, cumprindo assim melhor os requisitos de proteção ambiental.
Atualmente, o desenvolvimento e a aplicação da tecnologia de fundição injectada tem feito grandes progressos, e a aplicação de peças de fundição injectada para veículos de energia nova tem-se tornado cada vez mais generalizada. Por exemplo, as caixas das baterias de lítio, as caixas dos motores, as engrenagens de direção, as peças do chassis, etc., são todas peças fundidas sob pressão comuns nos novos veículos de energia.
Na concorrência do mercado de veículos de energia nova, a qualidade e o nível técnico das peças de fundição injectada tornar-se-ão a chave da concorrência empresarial. Por conseguinte, as empresas têm de se concentrar e melhorar a tecnologia de fundição injectada e melhorar a qualidade e o desempenho das peças fundidas sob pressão para satisfazer a procura do mercado.
Em suma, as peças fundidas sob pressão para veículos de energia nova são uma direção importante para o desenvolvimento futuro da indústria automóvel. As empresas precisam de se concentrar e melhorar a tecnologia e melhorar continuamente a qualidade e o desempenho das peças fundidas sob pressão para satisfazer a procura do mercado e contribuir para o desenvolvimento da indústria automóvel das novas energias.

O que é a tecnologia de fundição injectada de uma só peça para automóveis?
Em julho de 2019, a Tesla emitiu uma nova patente, nomeadamente uma máquina de fundição multidirecional integrada na carroçaria e métodos de fundição relacionados para estruturas de automóveis, propondo uma tecnologia de fundição integrada na estrutura e concepções de máquinas de fundição relacionadas.
O processo tradicional de fabrico de automóveis inclui principalmente quatro processos principais: estampagem, soldadura, pintura e montagem final. A tecnologia de fundição injectada integrada utiliza uma máquina de fundição injectada de grandes dimensões para moldar centenas de peças que têm de ser montadas de uma só vez. As peças completas podem ser obtidas diretamente. Requer menos 79 peças do que anteriormente e pode reduzir os custos de fabrico em 40%.
Vantagens da tecnologia de fundição injectada integrada para automóveis
- Poupar o processo: Mais de 70 peças e peças de soldadura que precisam de ser estampadas podem ser omitidas diretamente. Através da tecnologia de fundição injectada integrada, o corpo pode ser diretamente fundido.
- Poupança de tempo: redução do tempo de fabrico de mais de uma hora para menos de 3 minutos.
Poupança de máquinas: Inicialmente, eram necessários 300 robots no processo de fabrico, mas agora só é necessária uma máquina de fundição injetada de grandes dimensões. - Poupança de mão de obra: Os 300 trabalhadores inicialmente necessários na oficina de soldadura podem ser reduzidos a apenas cerca de 30 trabalhadores integrados na manutenção da máquina de fundição injetada.
- Poupança de espaço: o espaço de chão da oficina de soldadura pode ser muito reduzido, poupando cerca de 30% do espaço de chão do que o projeto anterior.
- Redução do peso: Em termos de todo o veículo, o conjunto do piso traseiro adopta o modo integrado de fundição sob pressão, o que reduz o peso em cerca de 30%, aumentando assim a autonomia de cruzeiro em 14% e poupando nas contas de eletricidade.
- Poupança de custos: Em comparação com o original, os custos de fabrico foram reduzidos em cerca de 40%, o que melhorou consideravelmente o ModeI Y em termos de resistência do produto e de desempenho em termos de custos.
Os obstáculos técnicos ao futuro da fundição injectada integrada
- Em termos de materiais, baseia-se principalmente em materiais de liga de alumínio tratados termicamente.
- Em termos de equipamento, existem requisitos elevados para a força de aperto das máquinas de fundição injectada. As máquinas de fundição injectada têm barreiras técnicas à conceção e desenvolvimento personalizados, bem como despesas de capital relativamente elevadas.
- Em termos de moldes, as peças integradas de fundição injectada têm estruturas complexas e elevados custos de fabrico, bem como longos ciclos de preparação, o que coloca requisitos mais elevados na produção de moldes de fundição injectada.
- Em termos de tecnologia, uma vez que a atual tecnologia de fundição injetada integrada ainda está a dar os primeiros passos, os fundidores precisam de ter uma vasta experiência e acumulação de tecnologia no processo de produção para garantir a taxa de rendimento da produção em massa.
Questões a que é necessário prestar atenção na fundição injectada integrada
Pay attention to the cooperative relationship between automobile companies and third-party die-casting companies. If the cooperation changes or becomes unstable, it will have a great impact.
Since the parts are all die-cast into one, the repair cost will be very high in the event of a collision.
Die-casting process and surface treatment technology of auto parts
The die-casting process of automobile parts is a process of organic combination and comprehensive application of three elements: die-casting machine, die-casting mold, and alloy. The process of filling the cavity with metal during die casting is a process that unifies process factors such as pressure, speed, temperature and time. The process programming is based on the drawing requirements of the shell parts, fully considering the existing conditions, and utilizing the existing conditions as much as possible. Having the equipment to eliminate weak links in production, striving to improve product quality, and shortening the process preparation (manufacturing) cycle are issues that must be considered when planning the die-casting process for automotive parts.
Automotive die casting process flow:
- Plan review,
- Prepare materials,
- processing,
- Mold base processing,
- mold core processing,
- electrode processing,
- Mold parts processing,
- inspection,
- assembly,
- flying models,
- Mold testing
- production.
Aluminum casting process flow:
Furnace charge preparation: batching, feeding, melting, slag removal, transfer introduction, refining, introduction into holding furnace.
Die-casting of automotive parts: four steps: mold opening, die casting, post-processing, inspection/mold opening.
That is the design and manufacturing of molds. This needs to be considered based on product specifications and sizes, materials, usage environment and mold materials.
The whole process of die casting
Die casting is a process in which molten metal is injected into a mold through a die-casting machine, cooled, and then pushed out with a push rod. There are many relevant factors in this step, such as mold temperature, pouring temperature, raw material quality, injection speed, cooling speed, etc. Post-processing consists of multiple processing procedures aimed at improving corrosion resistance, wear resistance and texture of metal die castings through various treatments. Full inspection is where quality inspectors inspect the quality of die-casting parts, including appearance, size, performance, etc.
Advantages and applications of die-casting technology for automotive parts
Auto parts die-casting technology has advantages that other die-casting parts cannot match, such as appearance, light weight, corrosion resistance, etc., and is deeply loved by users. Especially since automobiles are lightweight, die-casting parts have been improved in the automotive electronics industry. One that is generally available. The engine block is the heart of the vehicle. The key issue in the quality of automotive service is whether the engine can work safely and with high quality, and one of the main components of the engine is the cylinder block.
Cylinder blocks are generally made of high-pressure casting or sand casting, but judging from the current mainstream models of automobile engines and automobile manufacturers, aluminum alloy die-cast cylinders are used. Although the manufacturing cost of aluminum alloy die-cast cylinders is higher than the previous two, with the demand for engine oil and lightweight vehicles, the rise of aluminum alloy die-cast cylinders is increasingly adopted by automobile manufacturers.
Because aluminum alloys have better thermal conductivity than cast iron, aluminum cylinder heads and blocks can improve the appearance of the engine. The casting process of the cylinder block is very complicated. The composition and strength of aluminum alloy auto parts die-casting parts have an important impact on the quality of the die-casting parts. By adjusting relevant components, the tensile strength and fluidity of die castings can be improved.
When choosing a processing method for CNC machining of automotive parts, factors such as material, shape, size, etc. must be considered.
During the Maquinação CNC process of auto parts, it is usually necessary to choose a suitable CNC machining method to meet production needs. When selecting a processing method, factors such as the material, shape, and size of the parts need to be considered. For auto parts processing, both five-axis and four-axis machining have their advantages and limitations. Let’s analyze the issue of choosing between five-axis machining and four-axis machining.
First of all, four-axis processing refers to adding a rotation axis to the three-axis, which can realize processing at any angle in the plane, and is suitable for processing a large number of similar or simple parts. Five-axis machining adds an inclined axis to the four-axis to enable more complex parts processing, such as curved surface processing and special-shaped parts processing.
Secondly, five-axis machining has higher accuracy and better surface quality, and can achieve more stringent processing requirements. Four-axis machining can only process in a plane and cannot meet the high-precision requirements of five-axis machining.
However, the equipment cost of five-axis machining is relatively high, maintenance is difficult, and it requires higher technical level and experience. The equipment cost of four-axis machining is relatively low, maintenance is relatively simple, and the operation difficulty is low.
To sum up, the choice between five-axis machining and four-axis machining needs to be determined based on the specific situation. If the shape of the auto parts is complex and requires high precision and high surface quality, then five-axis machining should be chosen; if the shape of the auto parts is relatively simple and the requirements are not too high, then four-axis machining can meet the needs. Of course, for some special parts processing tasks, other processing methods may need to be used, and the choice needs to be based on the actual situation.