Die-casting is a star industry that is rising steadily with the development of automobile integration and industrial lightweighting. Die-casting products have the characteristics of lightweight material, strong wear resistance, high mechanical strength, good heat transfer and electrical conductivity, high temperature resistance, and beautiful appearance. , energy saving and high efficiency and many other advantages, it is increasingly widely used in all walks of life.
However, in the die-casting production and processing, the melting and heat preservation of the die-casting alloy, the preheating of the die-casting cavity, the spraying of paint, the operation of the die-casting machine, and the cleaning of die-casting parts will all produce smoke, harmful gases, oil droplets, oil stains, noise and Thermal radiation, etc., these pollutants not only cause great harm to the health of workers, but also cause pollution to the environment.
With the rapid development of the die-casting industry, relevant regulatory regulations and environmental policies are becoming more and more complete and strict. Environmental protection requires that the waste gas generated by die-casting must be collected and processed centrally, which can range from fines and rectification to shutdown and closure.
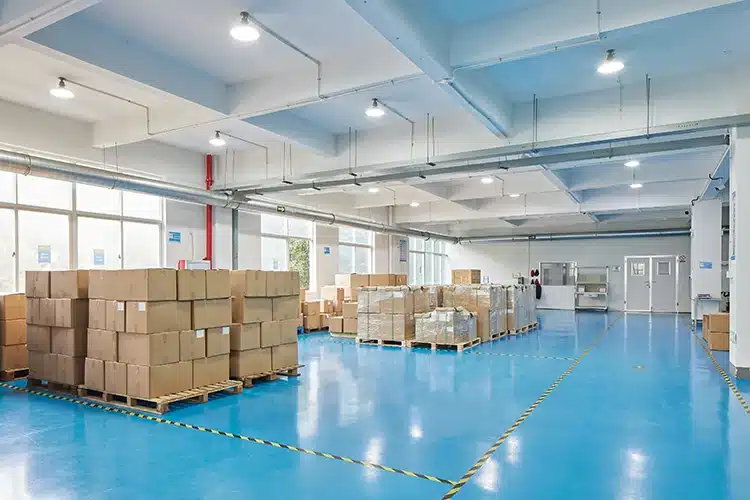
The main pollutants and environmental impacts in the die-casting workshop are:
- Pollutants and pollution sources: The main pollutants in the die-casting workshop and the workplace where they occur,
- The impact of pollutants on the environment and human body
The main pollutants in the die-casting workshop are discharged into the atmosphere, water and surrounding environment. Various types of waste are discharged directly to the outside without treatment. Some of them have exceeded national or local emission standards, which will cause environmental pollution and damage to the human body. Pollutants cause certain harm to the environment and human body.
Pollutant control and management methods
The management of various types of pollution in the die-casting workshop is a highly comprehensive technology. First of all, when planning a new workshop, try to use new materials, new processes, and new equipment that produce no or less pollutants. The second is to promote cleaner production in existing production workshops. The so-called cleaner production is a comprehensive approach that takes energy conservation, consumption reduction, and pollution reduction as its goals and uses management and technology as methods to control pollution throughout the entire process of industrial production and minimize the generation and emission of pollutants.
Use various effective measures to manage various pollutants, reduce pollutant emissions, and improve the working environment of the workshop.
Measures for air pollutants
- Change fuel melting furnaces and holding furnaces to gas furnaces or electric furnaces that cause less air pollution.
- Choose a flux that produces less harmful gases to reduce the generation of harmful gases during the smelting process.
- Smoke exhaust equipment should be used as much as possible in the melting equipment, slag cleaning area, and above the holding furnace. The shape of the smoke exhaust equipment should be determined according to different furnace structures and process operation requirements. Generally, the wind speed of the umbrella-shaped exhaust hood is about 1.5m.
- A fume filter is installed above the die-casting machine. Use the fume filter to inhale and filter the fumes generated during die-casting.
- Shot blasting, shot blasting, and grinding and polishing equipment should be equipped with dust removal equipment or exhaust equipment, and the spraying site should be equipped with oil mist separation equipment.
- For harmful gases such as sulfur dioxide, hydrogen chloride, and hydrogen fluoride, liquid spray equipment can be used to absorb it or activated carbon adsorption equipment can be used.
- Strengthen workshop ventilation measures. Workshop ventilation includes natural ventilation and mechanical ventilation. Natural ventilation uses wind pressure or hot air pressure for natural ventilation. This requires that the location and orientation of the workshop, the process placement in the workshop, the skylight planning and the distance between the workshops should all be conducive to natural ventilation. Mechanical ventilation is a ventilator installed on the roof or wall of the workshop to enhance ventilation in the workshop.
wastewater treatment
- Treatment of oily wastewater Typical treatment processes for single oily wastewater: Oily wastewater from die-casting workshops is often mixed with excessively sprayed release agent residues. Larger-scale product factories often choose to combine it with mechanical processing, painting, and domestic wastewater. Integrated processing, the processing technology is more complex.
- Treatment of wet dust removal wastewater Wet dust removal wastewater is treated in a sedimentation tank. Under the action of gravity, suspended particles with a density greater than that of the wastewater settle to the bottom of the pool, and particles with a density smaller than that of the wastewater float to the water surface to separate the solid particles from the water and reach treatment Purpose.
- Cooling water The primary characteristic of cooling water is thermal pollution and no other pollutants. It can generally be recycled after being cooled by a cooling tower.
Noise prevention
The noise in the die-casting workshop mainly comes from the working sound of mechanical equipment, the impact sound of castings and materials, the burning sound of the furnace, the current sound of induced current, the noise of hydraulic and pneumatic equipment, etc. Noise pollution is a kind of physical pollution. When the noise source stops outputting noise, the pollution disappears immediately, leaving no pollutants behind. However, if the noise in the workplace exceeds the permitted standard, it will also cause damage to people’s hearing and health. Noise prevention and control mainly involves controlling the source of sound, the transmission path of sound, and protecting the receivers.
- Reduce noise in process planning
① Use low-noise die-casting machines, trimming machines and other equipment, and adopt low-noise new processes and technologies.
② When transporting materials, try to reduce the impact of materials and reduce the material gap.
③When planning workshop processes, high-noise sections and low-noise sections should be placed separately.
④ Equipment with violent vibrations should not be placed on the steel structure platform.
- Sound insulation
① Offices, control rooms, studios, lounges, etc. that are located in high-noise areas should be sound-insulated. Use sound-insulating components for doors, windows, and walls to isolate the noise from the room and reduce the impact of noise on the interior. environmental impact.
② For some high-noise equipment, sound insulation covers and sound insulation barriers can be used to isolate the transmission of noise.
- Silencing: Installing a muffler on the compressed air discharge pipeline can effectively reduce air noise.
- Vibration reduction and vibration isolation Large equipment such as vibrating machines, etc., can be equipped with vibration isolation or vibration reduction equipment, such as springs, vibration damping cushions, etc.
- Personal protection: Personal protection is the most effective and economical method in many situations. A common method is to wear ear protectors.
Exhaust gas treatment
In order to ensure a good production environment in the workshop and the health of workers, as well as for the stable and long-term benefits of die-casting enterprises, the treatment of die-casting exhaust gas is imperative.
There are many traditional treatment methods for harmful components such as acidic gases HCl, H₂S, NOx, dust exhaust gas, formaldehyde, xylene, acetone, methyl ethyl ketone, acetic acid, and ethyl ester contained in die-casting waste gas. Common ones include activated carbon adsorption, Ion purification method, combustion method, UV photolysis purification method, etc.
Activated carbon adsorption method
The main principle of the activated carbon adsorption method is to use porous solid adsorbents (activated carbon, silica gel, molecular sieve, etc.) to treat organic waste gas. It is mainly used for the purification treatment of low-concentration organic waste gas with large air volume, low concentration (≤800mg/m³), no particulate matter, no sticky matter, and normal temperature.
- Advantages: high purification rate, wide application, simple operation.
- Disadvantages: The amount of consumables is large, and professional hazardous waste treatment is required after use, which is expensive.
Ion purification method
The ion purification method uses high-voltage discharge to separate oxygen ions and react with organic waste gas pollutants to achieve the purpose of purifying waste gas. Suitable for organic waste gases that are difficult to treat with other methods.
- Advantages: wide application range, high purification efficiency, small equipment footprint.
- Disadvantages: High-voltage discharge devices are prone to explosion in confined spaces with high concentrations of water, dust, and organic waste gas, posing safety hazards.
combustion method
The principle of the combustion method is to completely burn volatile organic compounds under high temperature and sufficient air conditions, and decompose them into CO₂ and H₂O. It is suitable for all types of organic waste gas and can be divided into direct combustion, thermal combustion and catalytic combustion.
- Advantages: higher purification rate.
- Disadvantages: extremely high cost, large floor space, continuous production, and easy generation of secondary pollution.
Intelligent Automation Solutions
The smart chip variable frequency drive realizes stepless adjustment of high-voltage output, saving about 70% of energy consumption under the same die-casting workshop conditions; the energy consumption of models below 2500 tons does not exceed 4.5KW/h, which is only equivalent to other similar products (15-23KW/ h) one-third.
- Three layers of purification, the smoke does not leak
Internationally advanced mist removal device and ion microparticle treatment method, 3 purification procedures, the treatment rate reaches 98%, and the particle size is as fine as 1um; after purification, PM2.5 in the workshop is <0.15mg/m³, which complies with indoor air standards and can be directly discharged without pressure.
- Intelligent monitoring and automatic cleaning
The temperature control and cleaning integrated screen control can realize networked collection of data such as temperature, voltage, current, etc., and the equipment status can be seen at a glance; intelligent operation can be set with one click according to actual working conditions, and automatic cleaning can be performed 24 hours a day, liberating manpower and improving efficiency.
- Two devices and one purification machine
The pollution source is collected close to the point and the anti-side leakage collection cover is used to bid farewell to the scattered and inefficient performance of traditional die-casting machines and melting furnaces that are divided into multiple sets of processors. One machine can easily cover a complete set; the processing efficiency is 25% higher than the traditional method, and the low emission value is only the traditional method. Way 10%.
The solid waste and air pollution produced by foundry enterprises in the production process are the most serious, and some small and medium-sized enterprises are relatively lacking in environmental awareness and strength. Foundry companies will continue to develop and will receive government support. However, as the government departments have become more and more stringent on environmental protection inspections in recent years, some relatively small and non-compliant enterprises are already facing bankruptcy, and some companies that can barely support are also required to be rectified by the Environmental Protection Bureau. Qualified manufacturers still attach great importance to environmental protection, and have invested a lot of money in this area to introduce or purchase very advanced environmental protection equipment and technology to cast steel castings, responding to the Environmental Protection Agency’s “green casting “The concept.