Aluminum alloy die-casting is a common process in which aluminum alloy is melted and injected into a mold, and then solidified under high pressure. Some main process parameters are involved in the die-casting process, such parameters determine the quality of product molding, such as “injection force”, “specific pressure”, “injection speed”, “mold temperature”, “filling time”, “holding time”, etc. .
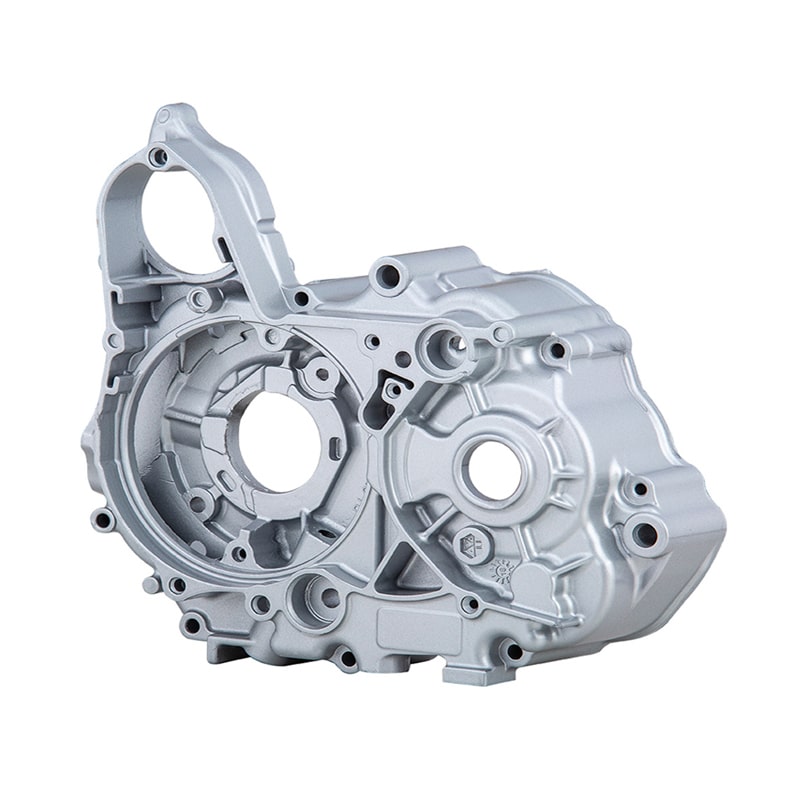
Die casting temperature
Aluminum alloy die-casting temperature is generally between 640°C and 700°C, too high or too low will affect the quality of aluminum parts.
Die casting pressure
Aluminum alloy die castings need to apply a certain pressure, usually between 80-200MPa, high or low pressure will affect the density and shape of aluminum parts.
Die casting pressure is one of the main parameters in the die casting process. The pressure in the die casting process is generated by a pressure pump. The pressure pump delivers the aluminum alloy solution through the accumulator to the injection piston, which is then applied to the metal in the pressure chamber through the injection punch. The pressure acting on the molten metal is the main factor in obtaining a structurally dense, well-defined casting. Therefore, it is necessary to understand and master the pressure changes acting on the liquid metal during the die-casting process, so that the pressure can be used correctly and the pressure value can be reasonably selected at each stage of the die-casting process.
Die casting speed
Aluminum alloy die casting speed is generally between 6-12m/s, too fast or too slow will affect the surface quality and structural performance of aluminum parts. In the die-casting process, speed control is very critical, it directly affects the quality of the product and production efficiency. This article will introduce in detail several key speed parameters in the aluminum alloy die casting process, including ejection speed, exhaust speed, gate speed, punch speed and injection speed.
Ejection speed
The ejection speed refers to the speed at which the cooled casting is pushed out of the mold by the ejector rod during the die-casting process. The control of the ejection speed directly affects the surface quality and dimensional accuracy of the casting. If the ejection speed is too fast, it will cause defects such as scratches or dents in the casting; if the ejection speed is too slow, it will cause the casting to stick to the mold or cause the mold to break. Therefore, in actual production, it is necessary to determine the appropriate ejection speed according to the specific situation.
exhaust velocity
Exhaust speed refers to the speed at which the gas in the mold is exhausted during the die-casting process. Aluminum alloys are prone to bubbles at high temperatures. If they are not removed in time, defects such as pores and bubbles will exist inside the casting. Therefore, controlling the proper exhaust velocity is very important to ensure the quality of castings. Excessive exhaust velocity may cause splashing of liquid metal, while excessively slow exhaust velocity may result in incomplete removal of air bubbles. Therefore, it is very important to adjust the exhaust velocity reasonably according to the shape and size of the specific casting and the characteristics of the aluminum alloy.
Gate speed
The gate speed refers to the speed at which the molten aluminum alloy is injected into the mold during the die-casting process. The control of the gate speed directly affects the filling condition and solidification process of the casting. If the gate speed is too fast, it will cause defects such as inclusions and pinholes inside the casting; if the gate speed is too slow, it will cause uneven filling or cold shut. Therefore, in actual production, it is necessary to determine the appropriate gate speed according to the fluidity and solidification characteristics of the aluminum alloy to ensure the quality and dimensional accuracy of the casting.
Punch speed
The punch speed refers to the speed at which the injection piston of the die casting machine advances during the die casting process. The speed of the punch will directly affect the filling and compaction of the aluminum alloy in the mold. If the punch speed is too fast, it may cause defects such as flash and slag inclusions on the surface of the casting; if the punch speed is too slow, it may cause incomplete solidification of the aluminum alloy, affecting the strength and surface quality of the casting. Therefore, in actual production, it is necessary to determine the appropriate punch speed according to the specific situation.
Injection speed
The injection speed refers to the speed at which the die-casting machine injects the molten aluminum alloy into the mold. The control of injection speed directly affects the filling condition and solidification process of aluminum alloy. If the injection speed is too fast, it will cause air bubbles and metal splashes in the aluminum alloy during the filling process, which will affect the quality and surface condition of the casting; if the injection speed is too slow, the aluminum alloy will not be able to fill the mold cavity or produce cold shut. Therefore, in actual production, it is necessary to determine the appropriate injection speed according to the specific shape and size of the casting and the fluidity of the aluminum alloy.
These speed parameters play a vital role in the aluminum alloy die casting process, and are of great significance to ensure the quality and production efficiency of castings. Therefore, in actual production, it is necessary to reasonably adjust these speed parameters according to the shape and size of the specific casting and the characteristics of the aluminum alloy to achieve the best die-casting effect.
Die casting time
Aluminum alloy die-casting time is generally between 1-2min, too short or too long will affect the density and structural properties of aluminum parts.
The filling time is the time required for the aluminum alloy metal liquid to start filling the cavity, which is called the filling time. Aluminum alloy die casting filling time: 0.01S~0.1S. The principle of choosing the filling time is: (1) the alloy pouring temperature is high, the filling time should be longer; (2) the mold temperature is high, the filling time is longer; (3) if the thick wall part is far away from the inner door, the filling time should be longer (4) For alloys with high melting heat, the filling time should be longer; (5) When the exhaust effect is poor, the filling time should be longer.
The holding time is also called the holding time, which is the time required for the metal liquid to solidify under the action of the specific pressure after the metal liquid fills the cavity. The function of holding pressure is to make the solidified metal crystallize under pressure, so as to obtain a casting with a dense internal structure. When the wall thickness of the casting is less than 1.2MM, the holding time of die-casting aluminum is 2 to 5 seconds, and when the wall thickness of the casting is 3 to 8MM, the holding time is 2.5 to 6 seconds. The selection principles are: (1) The crystallization temperature range of the die-casting alloy is higher, and the holding time is longer; (2) The wall thickness of the casting is large, and the holding time can be longer; the longer, the thicker the holding time of the gate, and the longer it should be.
Chill time, which is the residence time of the casting in the mold. That is, the time required from the start of packing to the ejection of the casting from the mold. Sufficient residence time ensures that the casting is completely solidified in the mold, cools and has a certain strength. Usually it is advisable to keep the casting from deforming and cracking in the shortest time. The residence time of die-cast aluminum alloy castings is 5S~30S, which is directly related to the wall thickness of the castings. The thicker the wall thickness of the casting, the longer the dwell time.
Die casting mold temperature
The temperature of aluminum alloy die-casting molds is generally between 150°C and 200°C. Too high or too low will affect the surface quality and structural properties of aluminum parts. The mold temperature is the temperature of the mold during the production process. The temperature of the aluminum alloy die-casting mold during the normal production process is: 200°C to 280°C. Generally, the thinner the casting, the more complex the structure, and the higher the requirement for the mold temperature.
Temperature Control System
In the aluminum alloy die casting process, a temperature control system is required to control the temperature. Control parameters such as mold temperature and die-casting temperature to ensure the quality of aluminum parts.
The above are some basic contents of die-casting aluminum technical parameters, for the production of aluminum alloy die-casting parts
Reasonable control of these parameters during processing can effectively improve the quality and production efficiency of aluminum parts.