High pressure aluminum die casting is an essential process for producing strong, long-lasting components. The remarkable strength and accuracy of this method enable the fabrication of complicated and intricate designs. We’ll look at the uses and advantages of high pressure aluminum die casting in this blog article, along with the main elements that make it durable.
Что такое литье алюминия под высоким давлением?
A high-pressure injection of molten aluminum alloy into a steel mold is the process of high pressure aluminum die casting. The intended component is formed when the molten metal fills the mold cavity. The mold is opened and the completed component is ejected after the metal has solidified.
This casting technique is renowned for producing parts with outstanding surface polish and dimensional precision. It is extensively used in many different sectors, including as telecommunications, electronics, automotive, and aerospace.
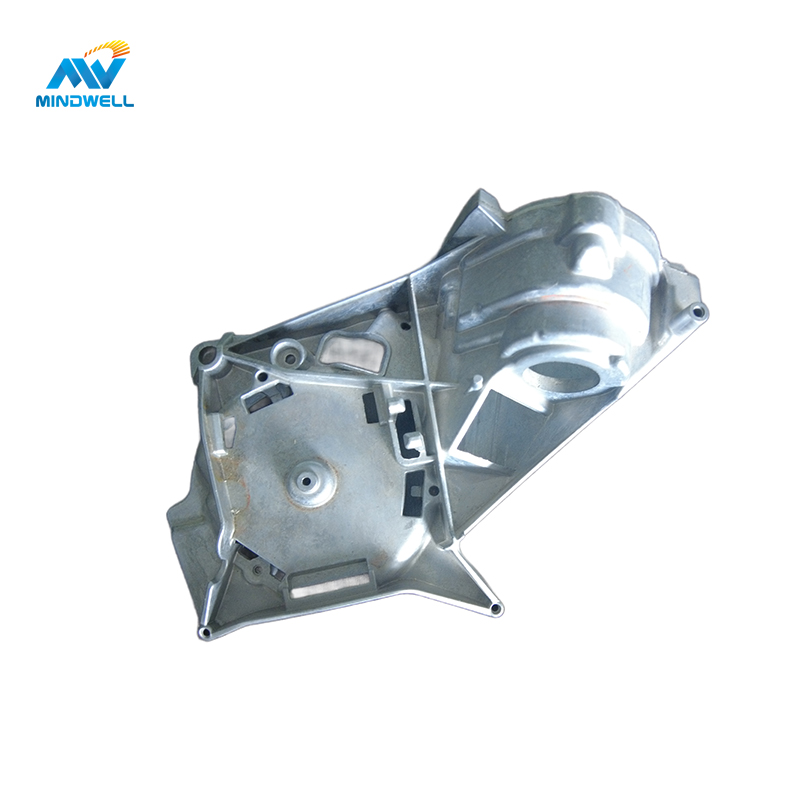
High Pressure Aluminum Die Casting’s Advantages
- Strength and Durability: Aluminum die castings have a remarkable strength-to-weight ratio, which makes them perfect for applications requiring components that are both lightweight and robust. Parts with exceptional strength and structural integrity are produced as a consequence of the high pressure used during the casting process, which guarantees that the material fills the mold entirely.
- Complex Geometry: With high pressure aluminum die casting, it is feasible to produce fine details and complex forms that would be hard or impossible to do with conventional manufacturing techniques. This adaptability makes it possible to create components with exact requirements and offers up a broad variety of design options.
- Cost-Effectiveness: High pressure aluminum die casting is quite affordable when compared to other production techniques. It is an affordable option for large-scale manufacturing because to its short production cycle and high output rates. Aluminum die castings’ long-term endurance also lowers maintenance and replacement expenses.
Elements That Affect Durability
High pressure aluminum die castings’ durability is influenced by a number of factors:
- Material Selection: The durability of the castings is greatly influenced by the aluminum alloy that is used. The mechanical characteristics, resistance to corrosion, and thermal conductivity of different alloys differ. Manufacturers may guarantee that the castings fulfill the necessary performance criteria by using the right alloy.
- Design Optimization: To achieve the highest level of durability, proper design optimization is necessary. This covers elements including draft angles, fillet radii, rib design, and wall thickness. Well-designed parts uniformly distribute stress, lowering the chance of failure and extending the part’s lifetime.
- Heat Treatment: The mechanical qualities of aluminum die castings may be greatly improved by heat treatment procedures such solution heat treatment and aging. Increased durability is the outcome of these operations, which also enhance the material’s strength, hardness, and dimensional stability.
- Quality Control: To guarantee the longevity of high pressure aluminum die castings, strict quality control procedures are necessary. Throughout the production process, this entails routine testing and inspections to find any flaws or irregularities that might jeopardize the integrity of the finished product.
Utilization of Aluminum Die Casting at High Pressure
High pressure aluminum die castings are appropriate for a variety of applications due to their durability and adaptability, which include:
- automobile sector: Engine parts, transmission housings, and structural pieces are often made using aluminum die castings in the automobile sector. Aluminum’s lightweight composition increases fuel economy without sacrificing strength or durability.
- Aerospace Industry: Essential parts for aircraft engines, landing gear systems, and structural elements are made from high pressure aluminum die castings. Aluminum has a high strength-to-weight ratio, which makes it a great material for aircraft.
- Electronics Industry: Heat sinks, enclosures, and connections are among the many applications for aluminum die castings in the electronics sector. Aluminum’s superior thermal conductivity contributes to efficient heat dissipation, guaranteeing the lifetime and best possible performance of electrical equipment.
- Telecommunications Sector: Base stations, satellite components, and antenna housings are all made using high pressure aluminum die castings. Aluminum is a great material for outdoor applications exposed to extreme climatic conditions due to its durability and corrosion resistance.

To sum up, high pressure aluminum die casting is an essential manufacturing technique that makes it possible to produce components that are both high-quality and long-lasting. Its many advantages—such as strength, adaptability, and affordability—make it a top option across a range of sectors. Manufacturers can guarantee the lifetime and durability of aluminum die castings by taking into account variables including material selection, design optimization, heat treatment, and quality control.