Uncover the secrets of die-cast auto parts and how they improve vehicle performance. Discover the applications, benefits and technologies behind these precision-engineered components.
introduce
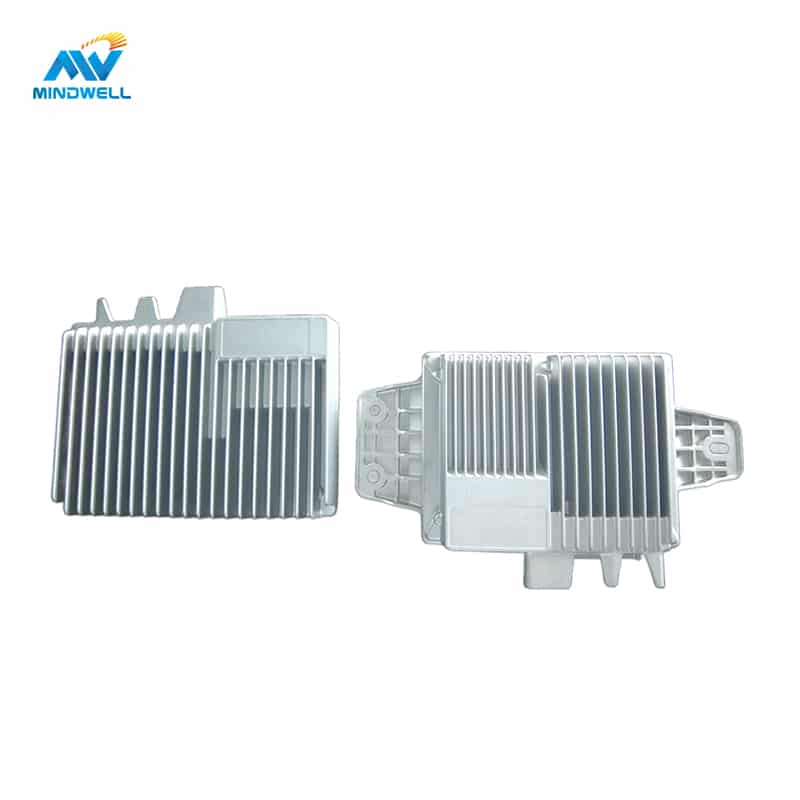
In the complex field of automotive manufacturing, die casting plays a vital role, especially in manufacturing high-performance automotive components. This guide takes an in-depth look at the world of die-cast automotive parts, revealing its applications, benefits, and technological innovations that are driving the automotive industry forward.
🔗 Enhance your automotive knowledge: Explore die casting applications
Understand die casting in automobile manufacturing
The evolution of die casting technology
Die-casting technology continues to develop and evolve over time to adapt to the needs and changes in the automotive manufacturing industry. Here’s how die-casting technology has evolved in automotive manufacturing:
- Initial stage: Early die-casting technology was mainly used to produce small, simple metal parts. Due to the small scale of the die-casting machine, the parts produced are also relatively small in size. Die-casting technology at this stage mainly focuses on improving production efficiency and reducing costs.
- Mature stage: With the development of the automobile industry, the demand for die-cast parts is gradually increasing. Die-casting machines are gradually becoming larger and more complex, capable of producing larger and more complex parts. At the same time, various aspects of die-casting technology have also been improved and optimized, such as mold design, material selection, production technology, etc.
- Innovation stage: In recent years, with the continuous advancement and innovation of science and technology, die-casting technology has also undergone many changes. For example, new die-casting materials such as aluminum, magnesium and other lightweight materials are widely used to improve the quality and performance of parts. At the same time, innovations in die-casting technology also include digital twin technology, 3D printing and other technologies, which can realize the manufacturing of complex-shaped parts and improve production efficiency and quality.
Die-casting technology has experienced multiple stages of development and evolution in automobile manufacturing. From traditional die-casting methods to modern innovative processes, die-casting technology is constantly improving to adapt to the needs and changes of the automotive manufacturing industry. In the future, with the continuous advancement and innovation of science and technology, die-casting technology will continue to develop and evolve, bringing more opportunities and challenges to the automobile manufacturing industry.
The Importance of Auto Parts Precision
In automotive parts manufacturing, precision is a crucial factor. For die-casting technology, precision directly affects the quality, performance and safety of parts. Here’s how precision plays a key role in die-cast automotive parts:
- Quality Assurance: Precision is a key factor in ensuring the quality of die-cast parts. During the die-casting process, the design and manufacturing accuracy of the mold, the control and filling of materials, the adjustment of pressure and temperature, etc. all need to be precisely controlled to ensure that the dimensional accuracy and surface quality of the final product meet the requirements. Only by reaching a certain level of accuracy can the reliability and service life of components be guaranteed.
- Performance improvements: Precision also directly affects the performance of die-cast parts. For example, high-precision die-cast parts can reduce friction and wear, improve transmission efficiency and service life. In addition, precision can also improve the strength, stiffness and fatigue resistance of components, thereby improving the overall performance of the vehicle.
- Safety guarantee: The precision of die-cast auto parts is also directly related to the safety of the vehicle. For example, high-precision braking system components can ensure the accuracy and timeliness of braking, and improve the braking performance and safety of vehicles. In addition, precision can also ensure the safe operation of other key components such as engines, gearboxes, etc., and avoid safety issues caused by component failures.
- Reduce costs: By improving the precision of die-cast parts, the difficulty and time of subsequent processing and trimming can be reduced, and production costs can be reduced. At the same time, high-precision parts can also reduce scrap and repair rates, thereby reducing overall operating costs.
- Realization of innovative designs: High-precision die-casting technology can support more complex and sophisticated automotive parts design. Designers can integrate more innovative ideas into product design to achieve more efficient, lightweight and high-performance automotive parts.
Precision plays a vital role in die-cast automotive parts. By improving the level of precision control of the die-casting process, the quality, performance and safety of parts can be ensured, production costs can be reduced, and the realization of innovative designs can be supported. Therefore, for die-casting technology, continuously improving precision is an important way to achieve the sustainable development of the automotive manufacturing industry.
Materials shaping the future: die-cast alloys
Die-cast alloys play a vital role in automotive manufacturing, as they directly impact the durability, strength and overall performance of automotive components. Here are some commonly used die casting alloys and their characteristics:
- Aluminum alloy: Aluminum alloy is one of the most commonly used alloys in die casting. It has the advantages of light weight, corrosion resistance, and good thermal conductivity. In automobile manufacturing, aluminum alloys are widely used to manufacture automobile parts, such as engine parts, braking system parts, etc. The strength and hardness of aluminum alloys are relatively low, but can be improved through heat treatment and the addition of alloying elements.
- Zinc Alloy: Zinc alloy is a relatively inexpensive die-cast alloy with good casting properties and corrosion resistance. In automobile manufacturing, zinc alloy is mainly used to make appearance parts and decorative parts, such as wheels, door trims, etc. Zinc alloys have relatively low strength and hardness, making them unsuitable for use in the manufacture of load-bearing components.
- Magnesium alloy: Magnesium alloy is a lightweight, high-strength die-cast alloy with good casting properties and corrosion resistance. In automobile manufacturing, magnesium alloys are widely used to manufacture load-bearing parts and appearance parts, such as hoods, doors, etc. Magnesium alloy has higher strength and hardness than aluminum alloy and zinc alloy, but the cost is also relatively high.
- Steel Alloy: Steel alloy is a die-cast alloy with high strength, high hardness and good corrosion resistance. In automobile manufacturing, steel alloys are mainly used to make load-bearing parts and safety parts, such as frames, airbags, etc. The cost of steel alloys is relatively low, but the casting performance is poor and the casting process needs to be strictly controlled.
When selecting a die-casting alloy, factors such as the use of the parts, performance requirements, and cost need to be considered. Different alloys have different advantages and disadvantages and need to be selected according to actual conditions. For example, for load-bearing parts that require high strength and corrosion resistance, you can choose magnesium alloys or steel alloys; for decorative parts that require good casting performance and beautiful appearance, you can choose zinc alloys or aluminum alloys.
In summary, die-cast alloys are an integral part of automobile manufacturing. Different alloys have different characteristics and application ranges, and they need to be selected according to actual conditions. With the continuous advancement and innovation of science and technology, future die-cast alloys will be more efficient, environmentally friendly and sustainable, bringing more opportunities and challenges to the automobile manufacturing industry.
Applications in the automotive industry
Engine components: providing power performance
Die-casting technology plays an important role in the manufacture of engine components and can increase the power and efficiency of internal combustion engines. The following are the applications of die casting in engine components:
- Cylinder Head: The cylinder head is an important part of the engine that encloses the cylinder and houses the piston. Die-casting technology can be used to manufacture cylinder heads. Through high-precision mold and material control, it can be ensured that the size and shape accuracy of the cylinder head meet the requirements. Die-cast cylinder heads are lightweight and high-strength to increase engine power and efficiency.
- Piston: The piston is one of the core components of the engine, and together with the cylinder, it forms the combustion chamber. Die-casting technology can be used to manufacture pistons, achieving lightweightness and miniaturization of the pistons through precise mold and material control. Die-cast pistons offer high strength, corrosion resistance and good thermal conductivity, which improves engine performance and reliability.
- Crankshaft: The crankshaft is a key component in the engine, used to transmit power and drive the piston movement. Die-casting technology can be used to manufacture crankshafts, achieving high strength, lightweight and corrosion resistance through high-precision mold and material control. Die-cast crankshafts increase engine power and efficiency and reduce fuel consumption.
- Camshaft: The camshaft is an important component in the engine and is used to control the opening and closing of the valves. Die-casting technology can be used to manufacture camshafts, achieving high precision and miniaturization through precise mold and material control. Die-cast camshafts offer high strength, corrosion resistance and good thermal conductivity, which improves engine performance and reliability.
- Flywheel: The flywheel is an important component in the engine and is used to store and release kinetic energy. Die-casting technology can be used to manufacture flywheels, achieving high strength, lightweight and corrosion resistance through precise mold and material control. Die-cast flywheels improve engine efficiency and fuel economy.
Transmission Housing: Seamless Power Transmission
Die casting plays an important role in the manufacture of gearbox housings. Through precision casting, high-quality, high-efficiency gearbox housings can be produced, helping to achieve seamless power transmission and optimizing the performance of automotive gearboxes.
First, die casting can produce gearbox housings with complex shapes and structures. Due to the good fluidity and filling ability of the molten metal during the die-casting process, thin-walled and complex structures can be manufactured, achieving lightweight and efficient production. This complex structure can improve the performance of the gearbox and increase transmission efficiency.
Secondly, the gearbox housing produced by die-casting has high precision and stable quality. Precision casting technology can ensure precise control of casting dimensions, thereby ensuring assembly accuracy and performance of the gearbox. In addition, the uniform filling and solidification of molten metal during the die-casting process can reduce defects such as stress concentration and shrinkage cavities, and improve the reliability and service life of the gearbox.
Finally, the die-cast gearbox housing enables customized production. Different car models and brands have different requirements for the performance and design of gearboxes, and die-casting technology can customize production according to different needs. This flexibility allows automakers to quickly adjust production plans based on market demand to meet the needs of different customers.
Chassis and Structural Components: Balancing Strength and Weight
Die casting plays an important role in the manufacture of chassis and structural components to achieve the perfect balance between strength and weight, which is crucial for vehicle safety and stability.
First, die casting can produce high-strength chassis and structural components. Due to the good fluidity and filling ability of the molten metal during the die-casting process, components with thin walls and complex structures can be manufactured, achieving lightweight and efficient production. At the same time, the uniform filling and solidification of molten metal during the die-casting process can reduce defects such as stress concentration and shrinkage cavities, and improve the strength and reliability of components. This high-strength chassis and structural component improves vehicle safety and stability.
Second, die casting can produce chassis and structural components with complex structures and precise dimensions. Precision casting technology can ensure precise control of casting dimensions, thereby ensuring assembly accuracy and performance of components. This precise size and structure reduces friction and vibration between components, improving vehicle stability and comfort.
In addition, die casting also has the capability of mass production. Due to the good fluidity and filling properties of the molten metal during the die-casting process, multiple parts can be manufactured and mass production can be achieved. This mass production capability can reduce production costs and improve production efficiency while meeting market demand for vehicle chassis and structural components.
Finally, die casting also enables customized production. Different vehicle models and brands have different requirements for the performance and design of chassis and structural components, and die-casting technology can customize production according to different needs. This flexibility allows automakers to quickly adjust production plans based on market demand to meet the needs of different customers.
3. Surface treatment technology
Die-casting surface treatment technology is critical to improving the aesthetics and corrosion resistance of automotive components. The following are several commonly used surface treatment technologies:
- Shot peening: Shot peening is a surface strengthening process that sprays projectiles onto the surface of the workpiece through high-speed airflow, causing plastic deformation on the surface of the workpiece, thereby improving the fatigue strength and corrosion resistance of the workpiece. Shot peening can be applied to die-cast automotive parts, such as cylinder heads, pistons, etc., to enhance their corrosion resistance and aesthetics.
- Powder spraying: Powder spraying is a commonly used surface coating process. The powder coating is evenly sprayed onto the surface of the workpiece through electrostatic spraying or fluidized bed spraying to form a dense coating. Powder coating can be applied to die-cast automotive parts, such as body panels, wheels, etc., to improve their corrosion resistance and aesthetics.
- Electroplating: Electroplating is a process that deposits metal onto the surface of a workpiece through the principle of electrolysis. It can form a layer of metal coating with special properties on the surface of the workpiece. Electroplating can be applied to die-cast automotive parts, such as bushings, gears, etc., to improve their corrosion resistance and wear resistance.
- Anodizing: Anodizing is a process that oxidizes the metal surface into an oxide film through the principle of electrolysis. It can form a dense oxide film on the metal surface to improve the corrosion resistance and aesthetics of the metal. Anodizing can be applied to die-cast automotive parts, such as aluminum alloy parts, to improve their corrosion resistance and aesthetics.
Die-casting surface treatment technology is critical to improving the aesthetics and corrosion resistance of automotive components. Different surface treatment technologies have different characteristics and application ranges, and need to be selected according to actual conditions. With the continuous advancement and innovation of science and technology, future surface treatment technology will be more efficient, environmentally friendly and sustainable, bringing more opportunities and challenges to the automobile manufacturing industry.

4. Frequently Asked Questions
What materials are commonly used for die-cast auto parts?
Aluminum, zinc and magnesium alloys are commonly used for die-cast automotive parts due to their lightweight nature and excellent mechanical properties.
How do die castings improve vehicle fuel efficiency?
The precision and lightweight properties of die-cast components help reduce vehicle weight and improve fuel efficiency by reducing energy consumption.
Are die-cast auto parts environmentally friendly?
Yes, die casting is an environmentally friendly process as it minimizes waste and the materials used are recyclable and consistent with sustainable manufacturing practices.
Can die castings be used for electric vehicle parts?
Of course, die casting is widely used in the manufacture of electric vehicle parts, contributing to their lightweight design and overall efficiency.
How do die castings ensure the safety of automobile structural parts?
The precision of the die-cast parts ensures that the structural components meet strict safety standards, providing durability and reliability in a variety of driving conditions.
What advancements are expected in die-casting technology for automotive applications?
Continuing advancements in die-casting technology include improved alloy formulations, increased automation, and increased efficiency in the production of complex parts.
Conclusion: Promoting the future of excellent automobiles
To sum up, die-cast automotive parts have become the backbone of modern automotive manufacturing, embodying precision, efficiency and innovation. As the automotive industry evolves, the role of die casting continues to drive excellence and shape the vehicles of the future.