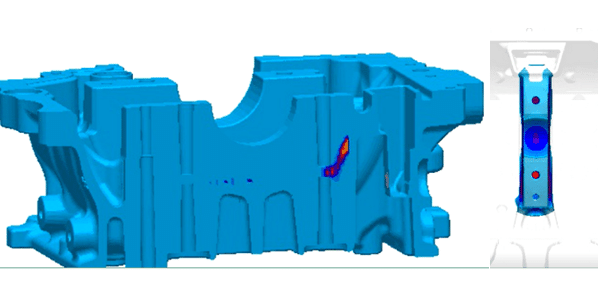
Проведено исследование усадочных полостей в алюминиевых отливках под давлением и стратегии снижения уровня брака с 5% до 0,2%. Усадочные полости, распространенные внутренние дефекты в литых под давлением деталях из алюминиевых сплавов, часто возникают в местах с большой толщиной стенок или в горячих точках. Хотя в целом они допустимы, если не влияют на характеристики изделия, некоторые критически важные детали, такие как каналы подачи охлаждающей воды или смазочного масла в блоках цилиндров автомобильных двигателей, должны быть свободны от усадочных отверстий.
Усадочные полости - распространенные внутренние дефекты в деталях, отлитых под давлением из алюминиевого сплава. Они часто появляются в местах, где толщина стенок изделия относительно велика или где есть вероятность образования горячих точек. В целом, если усадочные полости не влияют на эксплуатационные характеристики изделия, оно будет считаться квалифицированным. Однако для некоторых важных деталей, таких как отверстия для прохода охлаждающей воды или смазочного масла в блоке цилиндров автомобильного двигателя, появление усадочных отверстий не допускается.
Картер двигателя из алюминиевого сплава определенной компании отлит на машине для литья под давлением с холодной камерой Bühler 28 000 кН и изготовлен из сплава ADC12. Масса литой заготовки составляет 6,3 кг. Во время рентгеновского контроля в ходе постпроцесса было обнаружено, что в масляном канале второго отверстия подшипника коленчатого вала появились усадочные отверстия, которые находились на расстоянии около 8 мм от масляного канала, и существовал большой риск утечки масла. Согласно статистике, показатель брака усадочных полостей в этом месте в 2017 году составил 5%. После ряда исследований уровень брака был успешно снижен до 0,2%.
Механизм и морфология усадочных полостей в отливках из алюминиевых сплавов под давлением
Механизм образования усадочной полости
Существует множество причин, по которым усадочные полости в отливках из алюминиевых сплавов. Если проследить ее происхождение, то в основном она вызывается недостаточной подачей алюминиевой жидкости при переходе из жидкой фазы в твердую фазу алюминиевого сплава. К распространенным причинам усадки относятся:
- Градиент температуры в пресс-форме неоправдан, что приводит к непостоянной локальной усадке алюминиевой жидкости.
- Количество заливаемой алюминиевой жидкости слишком мало, что приводит к образованию тонкой лепешки материала и недостаточной компенсации давления на этапе форсирования.
- На пресс-форме есть горячие узлы или острые участки.
- Внутренний затвор формы недостаточно широк и имеет небольшую площадь, что приводит к преждевременному застыванию отливки, препятствует передаче давления на этапе прессования и не позволяет подавать алюминиевую жидкость.
- Если давление литья установлено слишком низко, эффект подачи будет плохим.
Морфология литейной усадочной полости
Усадочные полости являются распространенным внутренним дефектом деталей из алюминиевых сплавов, полученных литьем под давлением, и даже отливок. Они часто появляются в местах с большой толщиной стенок, острыми углами формы и большим перепадом температур в форме. На рис. 2 показана форма усадочного отверстия в картере определенного двигателя. Усадочное отверстие имеет овальную форму, расположено примерно в 10 мм от отверстия для прохода масла в подшипник, а его внутренняя стенка шероховатая и тусклая. Сайт толщина стенки отливки в усадочной полости относительно велика, около 22 мм; на переднем конце штифта отверстия для прохода масла нет охлаждающей воды, и температура пресс-формы относительно высока. Две основные шейки коленчатого вала автомобильного двигателя (коренная шейка и шейка шатуна) испытывают большую рабочую нагрузку и сильно изнашиваются, поэтому во время работы необходимо осуществлять смазку под давлением. В этом случае, если рядом с отверстием для прохода масла в шейке имеются усадочные отверстия, это серьезно повлияет на эффект смазки.
Меры, связанные с усадочными полостями
Причины дефекты литья в алюминиевом сплаве дефекты литья под давлением включают структурные особенности самого изделия, необоснованную конструкцию формы, необоснованную конструкцию литниковой системы и системы охлаждения, а также необоснованную конструкцию технологических параметров. Основываясь на общих причинах дефектов литья и процедурах обработки дефектов литья алюминиевых сплавов, мы исследуем соответствующие контрмеры для устранения усадочных полостей в толстых и крупных деталях литья алюминиевых сплавов под давлением.
Ранний анализ и контрмеры
Предварительный анализ усадочных полостей в отливках начинается с простых в обработке параметров процесса. По результатам измерений и наблюдений на месте, измеренная толщина внутреннего затвора формы составляет 4 мм, расчетная скорость внутреннего затвора - 40 м/с, а толщина стенки самой тонкой части изделия - 4,6 мм; толщина коржа материала - 25 мм; давление литья - 60 МПа. Из опыта известно, что если конструкция формы соответствует структурным характеристикам изделия, то литниковая система формы не должна иметь проблем с недостаточной подачей материала на этапе прессования. Однако подача алюминиевой жидкости на стадии прессования напрямую зависит от толщины коржа материала и давления прессования. Только подходящие толщина лепешки материала и давление литья могут сформировать отливки с плотной внутренней структурой. Поэтому можно предположить, что усадочные полости вызваны отклонением давления литья. Причиной является низкое и тонкое тесто.
Существует две стратегии устранения усадочных полостей в отливках:
- Давление литья было увеличено с прежних 65 МПа до 90 МПа.
- Толщина жмыха регулируется с первоначальных 25 мм до 30 мм. После принятия вышеуказанных мер, коэффициент усадки был снижен с 5% до 4,8% после проверки специального потока в малых партиях. Эффект не был очевидным, что говорит о том, что технологические параметры не являются основной причиной усадки отливок.
Промежуточный анализ и меры противодействия
Поскольку основной причиной возникновения усадочных полостей в отливках является недостаточное питание во время затвердевания расплавленного алюминия, неравномерное распределение температуры в форме может легко привести к неразумной последовательности затвердевания расплавленного алюминия, что приведет к недостаточному питанию. Поэтому среднесрочный анализ контрмер в основном сосредоточен на обеспечении разумной формы. Начните с температуры. Из 3D-модели изделия видно, что толщина стенок усадочной полости отливки составляет 22,6 мм. Большая толщина стенок может легко привести к повышению температуры формы. Когда алюминиевая жидкость застывает, алюминиевая жидкость внутри отливки с большой толщиной стенки все еще находится в жидкой фазе или в фазе смешения твердой и жидкой фаз из-за высокой температуры, и в это время питающий канал внутреннего затвора может затвердеть. Таким образом, на этапе прессования в отливку не может подаваться расплавленный алюминий, что может привести к образованию усадочных полостей. Для обеспечения надлежащей температуры формы использовался тепловизор, с помощью которого максимальная температура формы после распыления разделительного агента составила 272°C, что выше, чем обычная температура формы после распыления. Температура пресс-формы и распределение в других областях в целом нормальные. Поэтому необходимо снизить температуру формы в усадочной полости. Кроме того, измеряется, что расстояние между дном отверстия для охлаждающей воды и поверхностью полости пресс-формы составляет 20 мм. Поскольку большее расстояние теплопередачи снижает охлаждающий эффект пресс-формы, необходимо изменить отверстие для охлаждающей воды.
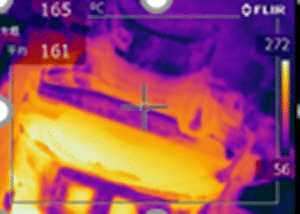
Для снижения температуры формы в усадочной полости используются три основных метода:
- Улучшить систему охлаждения пресс-формы. Углубите глубину отверстия для охлаждающей воды в усадочной полости крепления с 20 мм до 12 мм от поверхности пресс-формы, чтобы быстро отводить тепло от близлежащей пресс-формы и снизить температуру пресс-формы; пронумеруйте все водопроводные трубы охлаждения пресс-формы и водопроводные трубы в едином порядке, соответствующие одна к одной, чтобы предотвратить ошибку в сохранении пресс-формы, которая влияет на эффект охлаждения.
- Понизьте температуру заливки с 675 °C до 645 °C.
- Увеличить время распыления формы в усадочной полости с 2 с до 3 с. После реализации вышеуказанных мер по исправлению ситуации температура формы в области усадочной полости значительно снизилась после распыления, примерно до 200°C, что находится в пределах нормы. Скорость усадки снизилась с 4,8% до 4%, что указывает на то, что такие меры оказывают определенное влияние на усадку, но не могут полностью решить проблему усадки в этой области.
Поздний анализ и контрмеры
Благодаря двум предыдущим усовершенствованиям можно гарантировать, что литейная форма находится в теоретически обоснованном состоянии, то есть система заливки спроектирована разумно, система охлаждения организована правильно, а параметры процесса оптимальны. Однако скорость усадки отливок по-прежнему составляет 4%. Толщина стенок усадочной полости отливки составляет 22,6 мм, что значительно больше толщины стенок других деталей. Большая толщина стенки может стать причиной недостаточного питания при затвердевании в центре отливки. После завершения прессования эта область еще не полностью затвердела и продолжает сжиматься, образуя усадочные полости. Поэтому решение проблемы недостаточного питания в усадочных полостях отливок может стать ключом к решению проблемы. Вообще говоря, подача отливок осуществляется по пути кек → литник → слиток → отливка. Поскольку толстый часть литья затвердевает на внутреннем затворе, канал подачи на более поздней стадии прессования перекрывается, поэтому подача невозможна.
В отличие от традиционной стадии прессования, инжекционный пуансон оказывает давление литья через кек материала для достижения эффекта подачи. Принятая мера заключается в добавлении структуры, напоминающей шлаковый мешок, рядом с усадочным отверстием литье, которое используется в качестве материала пирог и использовать пару механизмов вытягивания стержня масляного цилиндра для работы в качестве пуансона Во-первых, на поздней стадии затвердевания отливки вторичное давление и подача осуществляются на участки, подверженные усадочным полостям, для достижения цели устранения усадочных полостей. В общем случае такой механизм вторичного прижатия называется экструзионным штифтом. Принцип его работы заключается в том, чтобы приложить соответствующее давление после заливки расплавленного металла или сплава и до его полного застывания, чтобы усилить эффект застывания и подачи отливки и улучшить качество отливки. Плотность: уменьшение или устранение усадочных полостей. Затвердевание под давлением может изменить физические параметры и процесс кристаллизации металлов и их сплавов, изменить распределение и размер свободных пустот, повысить плотность отливок, улучшить прочность на разрыв, твердость и другие свойства отливок.
В соответствии с законом подачи и давления литья, сигнал действия экструзионного штифта принимает сигнал давления процесса литья и задерживается в качестве сигнала запуска на этой основе. Таким образом, экструзионный штифт в основном управляет двумя параметрами: глубиной экструзии и временем задержки экструзии. . Глубина экструзии зависит от структуры отливки и распределения и размера усадочных отверстий, обычно 10~20 мм; задержка экструзии в основном относится к настройке времени экструзии, обычно 2~5 с. В реальной технике определение параметров экструзии основано на эмпирических значениях и затем оптимизируется в зависимости от ситуации с отливкой. Для того чтобы легко регулировать параметры экструзии, обычно используется отдельный масляный цилиндр для управления действием экструзионного штифта.
Для отливок картера впоследствии были приняты следующие меры: расположение двух экструзионных штифтов симметрично вблизи отверстий для подшипников формы и оптимизация вторичного давления на экструзионные штифты путем регулировки двух основных параметров: глубины экструзии и задержки экструзии. В результате снижается усадочная пористость отливок. На основе вышеупомянутых мер, после того как в форму были добавлены два дополнительных экструзионных штифта, скорость усадки значительно снизилась, а количество дефектов уменьшилось с 4% до 0,2%. В то же время среди дефектных изделий с усадочными полостями 0,2% размер усадочных полостей значительно уменьшился. Таким образом, решение с использованием экструзионного штифта играет лучшую роль в контроле скорости усадки отливок с увеличенной толщиной стенки. Однако в процессе совершенствования отливок также наблюдались колебания уровня дефектности усадочных полостей. Оптимизация параметров экструзии - глубина экструзии 15 мм, время задержки экструзии 2,5 с, заданный срок службы экструзионного штифта (раз/8000 форм) и другие соответствующие характеристики - позволили стабилизировать коэффициент дефектности отливок на уровне около 0,2%.
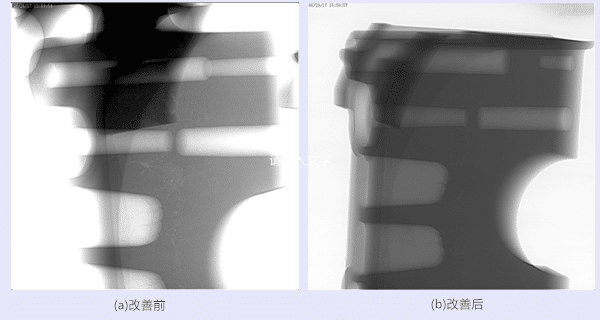
Рентгеновская дефектоскопия
Сравнительные фотографии рентгеновской дефектоскопии до и после улучшения области усадочных полостей отливки Видно, что усадочные отверстия в отливках появляются вблизи отверстий под подшипники, широко распространены и разбросаны, а структура относительно рыхлая. Поскольку отверстия под подшипники в блоке цилиндров должны заполняться смазочным маслом под давлением, существует риск утечки масла в отливках во время эксплуатации. После усовершенствования свободное распределение усадочных полостей больше не видно на снимках рентгеновского контроля, а внутренняя структура отливки выглядит более плотной.
в заключение
- Усадочные полости являются распространенным внутренним дефектом отливок и, как правило, появляются в областях с большей толщиной стенок и более высокой температурой формы. Обычно это связано с несколькими аспектами, такими как конструкция формы (система заливки, система охлаждения), настройка параметров процесса и гарантия условий литья Для отливок с большой толщиной стенок традиционные меры по улучшению могут только облегчить проблему, но не могут решить ее полностью.
- Два экструзионных штифта предназначены для имитации эффекта подачи пуансона на этапе прессования, что оказывает вторичное прессование и затягивание на область усадочных отверстий, и эффект очевиден.