There are 9 advantages to using aluminum in high pressure die casting including high strength, corrosion resistance, thermal conductivity, lightweight, low noise, aesthetics, high compressive strength, good production technology and environmental sustainability. Aluminum alloy is light in weight, has clear shape, thin wall and deep cavity, making it suitable for manufacturing complex parts. The production process also guarantees high dimensional accuracy and surface roughness. Aluminum die-casting molds are easy to recycle, reducing resource waste and promoting environmental sustainability.
Advantages of Using Aluminum in High Pressure Die Casting
A common industrial technique is high pressure die casting, which involves injecting molten metal under high pressure into a mould cavity. This method is renowned for producing precise, intricate pieces with a high degree of surface quality. Although a variety of metals may be used in high pressure die casting, aluminium is a particularly well-liked option because of its many benefits.
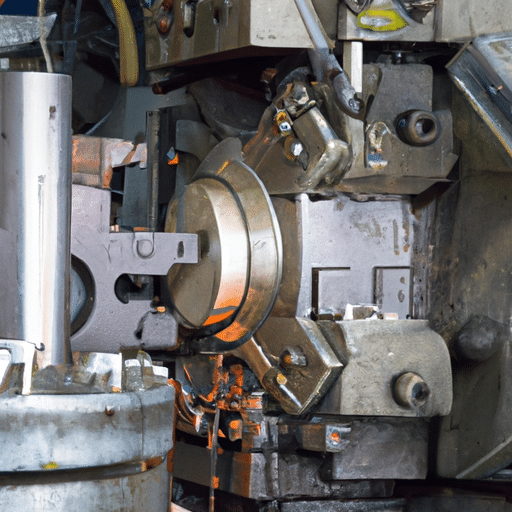
Lightweight and Strong
Aluminum’s strength and lightweight characteristics make it a valuable material for high pressure die casting. Due to its low density, aluminium weighs a lot less than other metals like steel or iron. This makes it perfect for uses where reducing weight is essential, including in the aerospace and automobile sectors. Aluminium provides exceptional strength and durability despite its lightweight nature, guaranteeing that the cast components can endure tough working environments.
Excellent Thermal Conductivity
Aluminium is a highly thermally conductive material that effectively transfers heat. This characteristic is very helpful in applications where heat dissipation is crucial, such heat exchangers or electrical equipment. Manufacturers are able to produce components with complex cooling channels that guarantee effective heat transmission and sustain ideal operating temperatures by using aluminium in high pressure die casting.
High Corrosion Resistance
Aluminum’s strong resistance to corrosion makes it a desirable material for high pressure die casting. On its surface, aluminium naturally produces an oxide layer that serves as a barrier to prevent corrosion. Because of this, aluminium components may be used in a variety of settings, such as ones that are damp, chemically charged, or very hot or cold. Aluminum’s ability to withstand corrosion may greatly increase the cast components’ lifetime and lower maintenance and replacement expenses.
Good Electrical Conductivity
Aluminum is also known for its good electrical conductivity, making it an ideal choice for applications that require efficient electrical performance. In high pressure die casting, aluminum can be used to create parts with intricate electrical pathways, ensuring reliable electrical connections. This makes aluminum a preferred material for components used in electrical systems, such as connectors, housings, and heat sinks.
Recyclability
Aluminum is highly recyclable, making it an environmentally friendly choice for high pressure die casting. The recycling process for aluminum requires significantly less energy compared to the production of primary aluminum. This not only helps reduce energy consumption but also minimizes the environmental impact of the manufacturing process. By using recycled aluminum in die casting, manufacturers can contribute to the sustainability goals and reduce the demand for virgin materials.
Cost-Effective
Another benefit that sets aluminium apart in high pressure die casting is its affordability. Because it is more readily available than other metals, aluminium is a more cheap metal. Its great recyclability also saves material prices, and its lightweight nature cuts transportation costs. Aluminum’s outstanding casting qualities—such as its low melting point and superior fluidity—also help to speed up production cycles, which saves manufacturers money.
In what situations is aluminium die casting acceptable to use?
The following situations are better suited for aluminium die casting:
- High criteria for corrosion resistance: Aluminium resists corrosion well, particularly in fresh water, the environment, and certain acidic media. Thus, aluminium die-casting can effectively increase the corrosion resistance and service life of components that must be exposed to the outside elements or come into contact with corrosive substances, such as windows and doors, construction tools, and decorating supplies.
- Needs for lightweight materials: Because aluminium is light and has a low density, die-casting aluminium is a great option in applications requiring weight reduction, including in the automotive, aerospace, and electronics industries. It can successfully lower the product’s total weight, enhance performance and fuel efficiency, and cut down on material waste.
- High needs for heat dissipation: Due to aluminum’s strong thermal conductivity, die-casting aluminium may substantially increase the heat dissipation performance of components that need it, including shell moulds and electronic connections. It may continue to provide superior electrical and shielding performance even in hot conditions.
- Mass manufacturing: Die-casting aluminium requires comparatively expensive production preparatory costs, but the die-casting equipment is very productive and appropriate for large-scale production. Therefore, the use of aluminium die casting may enhance production efficiency and product quality for items that need mass production and high dimensional precision and surface polish, such as automobile components and electronic device casings.
- complicated form requirements: Metal components with deep holes, thin walls, and complicated shapes may be produced with excellent surface polish and dimensional precision using aluminium die casting. Thus, aluminium die casting may satisfy the production needs for items that need complicated geometries, such engine blocks, petrol bottles, and hydraulic components.
- In conclusion, applications needing mass manufacturing, complicated geometries, high heat dissipation, corrosion resistance, and lightweight qualities are well suited for aluminium die-casting. It is extensively used in the automotive, aerospace, electronics, building, and military industries.
What are the characteristics of high-pressure aluminum die casting?
The following qualities of high pressure aluminium die casting are present:
- exceptional-pressure moulding: High-pressure moulding produces very thick castings with exceptional surface hardness and strength as aluminium liquid quickly fills the mould cavity.
- Rapid filling: The metal liquid may fill at a rate of 30 to 60 m/s and enters the mould cavity in the shape of a jet.
- Good surface quality: Castings often have a surface finish of Ra6.3 or even Ra1.6, which is a pretty high level of finish.
- may create thin-walled parts: Parts with a minimum wall thickness of up to 0.5mm may be produced by high-pressure aluminium die casting.
- Poor porosity: More gas is engaged within the product as a result of the molten metal filling quickly, which results in poor porosity.
- Not heat-treatable: Heat treatment might result in product flaws like bulges or fractures because the internal gas would expand.
- Minimal processing allowance: Too much processing will break down the thick layer on the surface, which will weaken the finished product.
- limited lifetime and high mould cost: The mould is under more pressure when it is moulded at high pressure, which causes a limited mould lifespan.
- Can cast deep holes: Better at casting deeper holes is high-pressure aluminium die casting.
- High dimensional precision: Castings have a high dimensional accuracy, often matching level 6–7 or even level 4.
- Good interchangeability: The castings have good interchangeability and are dimensionally stable.
What are the disadvantages of high pressure aluminum die casting?
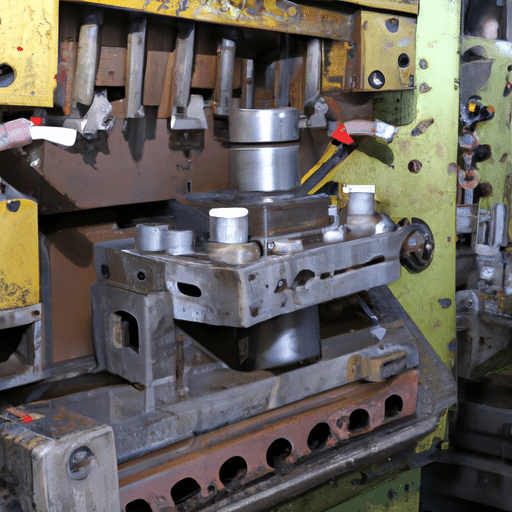
While high-pressure aluminium die casting offers several benefits, there are some drawbacks as well:
- Expensive: High-pressure aluminium die-casting necessitates high-pressure moulding, and the equipment needed is expensive.
- limited lifetime and high mould cost: The mould is under more pressure when it is moulded at high pressure, which causes a limited mould lifespan.
- High standards for raw and auxiliary materials: The raw and auxiliary materials used in aluminium die-casting must meet strict standards. To guarantee the quality of castings, premium aluminium ingots and supplementary materials are needed.
- Prolonged production cycle: The high-pressure aluminium die-casting process has a comparatively lengthy manufacturing cycle. Its lengthy production cycle necessitates the design, manufacture, testing, pouring, and other activities of the mould.
- Large castings cannot be produced with this method because high-pressure aluminium die casting requires the mould to be made at high pressure, which might result in very expensive mould maintenance and production costs.
- Porosity issue: More gas is incorporated into the product as a consequence of the molten metal filling quickly, which leads to low porosity.
- Not appropriate for producing castings with thinner walls: High-pressure aluminium die casting is not appropriate for producing castings with thinner walls because it is expensive to make and maintain moulds and might be challenging to guarantee casting quality.
The primary drawbacks of high-pressure aluminium die-casting are related to expenses, casting size, manufacturing cycle, and material quality. Comprehensive considerations based on real demands and circumstances are necessary when deciding whether to employ high-pressure aluminium die-casting.
Application of high pressure aluminum die casting

High-pressure aluminium die-casting is a popular die-casting technique that creates aluminium alloy components of a variety of forms by forcing molten aluminium into a casting mould at a high pressure. Numerous industries, including automotive, electronics, furniture, sports equipment, medical, construction, and aerospace, use high-pressure aluminium die-casting. The primary applications of high-pressure aluminium die-casting are as follows:
- Automobile manufacturing: Engine and chassis components, including cylinder heads, oil pans, gearbox boxes and so on, are often made using high-pressure aluminium die casting. Aluminium has a low density, which allows it to drastically lower the vehicle’s weight and increase fuel efficiency.
- Electronic product manufacturing: Housings, radiators, connections, and other components are made using high-pressure aluminium die-casting in this process. Because of its high thermal conductivity, aluminium can effectively dissipate heat from electrical goods.
- Furniture manufacturing: A variety of ornamental mouldings, doors, windows, and other components may be produced using high-pressure aluminium die-casting to enhance the overall durability and beauty of bespoke furniture.
- Medical device manufacturing: To satisfy the needs of lightweight, strong, and corrosion-resistant medical equipment, a variety of brackets, shells, and other components may be produced using high-pressure aluminium die-casting.
- Sports equipment manufacturing: A variety of lightweight, highly-strengthening items, including bicycle frames and skis, may be produced using high-pressure aluminium die-casting.
- Construction industry: A variety of ornamental materials, doors, windows, railings, and other elements that enhance the overall beauty and longevity of the structure may be produced using high-pressure aluminium die-casting.
- Aerospace manufacturing: To fulfil the lightweight, high strength, and corrosion resistance requirements of aircraft, high-pressure aluminium die-casting may be utilised to make a variety of structural elements, engine components, etc.
In conclusion, the advantages of using aluminum in high pressure die casting are numerous. Its lightweight and strong properties, combined with excellent thermal conductivity, corrosion resistance, and electrical conductivity, make it a versatile material for a wide range of applications. Additionally, its recyclability and cost-effectiveness further enhance its appeal. By leveraging these advantages, manufacturers can produce high-quality cast parts that meet the demands of modern industries.