One manufacturing method that stands out for being both flexible and effective is high-pressure die casting (HPDC), which has revolutionised the creation of complex and superior metal components. This article delves into the intricacies of high-pressure die casting, examining its fundamentals, uses, and technical developments that have made it a mainstay in the metalworking industry.
An Introduction to High-Pressure Die Casting
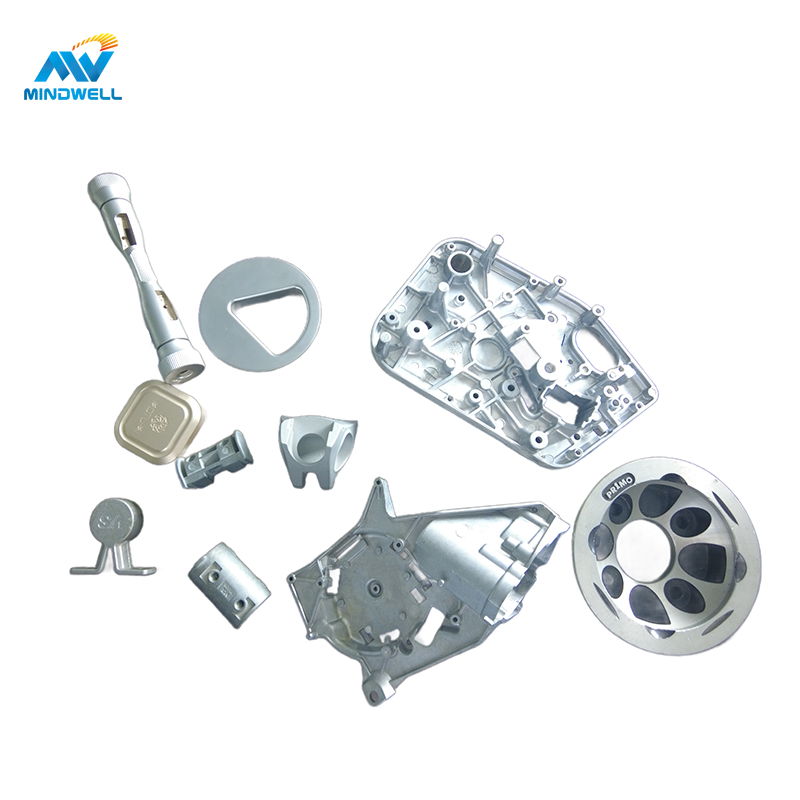
High pressure die casting is a precision casting method, also known as die casting. The basic idea behind it is to cool the molten metal after it has been hydraulically forced into a steel mould under intense pressure. This casting technique works well for casting metal components made of aluminium, zinc, copper, and other alloys with intricate structures, thin walls, high accuracy requirements, and melting temperatures lower than those of steel. The company’s products are extensively utilised in a variety of sectors, including industrial, household appliances, autos, and aircraft, due to their numerous benefits, including accuracy, low weight, and beauty.
Process of High-Pressure Die Casting:
Fundamentally, high-pressure die casting is a metal casting technique that involves injecting molten metal into a precisely crafted mould, or die, under high pressure. This method is very useful for producing complicated and detailed items with outstanding dimensional precision. High-integrity castings are produced as a consequence of the pressure, which usually ranges from 10,000 to 30,000 psi. This guarantees that the mould is filled quickly and completely.
High-Pressure Die Casting Machine:
The high-pressure die casting machine, a sturdy apparatus built to resist the pressures required in the injection of molten metal, is essential to the process. These devices are essential to reaching the high production levels connected with HPDC.
How high pressure die casting works?
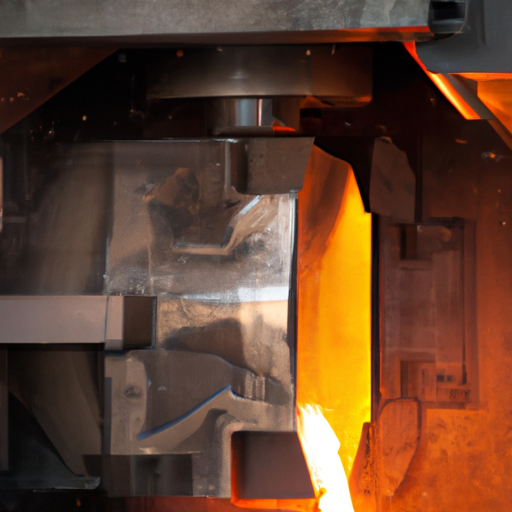
Die-casting, or high-pressure die-casting, is a precision casting technique. The basic idea behind it is to rapidly and intensely pressurise liquid or semi-liquid metal into the die-casting mould cavity, then solidify the metal under pressure to create a casting. In particular, the die-casting machine’s furnace heats and melts liquid or semi-liquid metal. The metal is hydraulically driven into the mould cavity via the die-casting machine’s pressure chamber once it reaches the casting temperature. High pressure causes the molten metal to fill the mould cavity fast, forcing air and impurities upward to be released from the mould. To enable the molten metal to solidify under pressure once it has filled the mould cavity, the mould is kept under high pressure for a while. At last, the casting is evacuated and taken from the mould once the mould is opened.
Die-casting has a great production efficiency since the molten metal is typically under pressure of 20–200 MPa, the inner gate speed during mould filling may reach 15–70 m/s, and the mould filling time is just 0.01-0.2 s. The high-pressure die-casting technique produces high-density and mechanically strong castings that can be produced quickly because of the high-speed filling and high-pressure solidification of liquid metal. This casting technique works well for casting metal components made of aluminium, zinc, copper, and other alloys with intricate structures, thin walls, high accuracy requirements, and melting temperatures lower than those of steel. The company’s products are extensively utilised in a variety of sectors, including industrial, household appliances, autos, and aircraft, due to their numerous benefits, including accuracy, low weight, and beauty.
The Benefits of High Pressure Die Casting
Accuracy in Dimensions and Precision:
Outstanding dimensional precision is a result of the high pressures used in HPDC, which minimises the need for extra machining.
intricate geometries:
HPDC is well known for its capacity to create complicated, detailed pieces with thin walls that satisfy the requirements of contemporary design.
Quick Rates of Production:
Because of its efficiency, HPDC can produce a lot of components in a short amount of time, which makes it perfect for high-volume manufacturing.
Superior Material Integrity:
Castings with enhanced mechanical qualities, reduced porosity, and increased material integrity are the outcome of carefully filling the mould under high pressure.
Systems with hot and cold chambers
High-pressure die casting includes hot chamber and cold chamber systems.
The hot chamber system is mainly used to process low-temperature non-ferrous alloys. Its distinctive feature is the gooseneck, which sends the molten metal straight into the mould chamber. The metal in a hot chamber die casting unit is supplied straight into the mould cavity via the gooseneck since the unit has an integrated furnace for melting the metal. The highest temperature at which hot chamber equipment can safely die-cast alloys, such as zinc, magnesium, lead, and other alloys, is around 450°C. Furthermore, low-melting-point alloys used in hot chamber casting have less of an effect on the mould, extending its lifespan.
Cold chamber systems are mainly used to process high-temperature non-ferrous alloys. They are distinguished by having an exterior melting furnace and requiring the use of manually or mechanically controlled ladles to move the molten metal to the machine. A common processing temperature of 600°C or above is used to process various metal alloys, such as brass, copper, and aluminium. Because the molten metal must be handled by hand throughout the casting process, cold chamber casting requires a longer cycle time. In cold chamber machines, the mould deteriorates more quickly because of the molten metal’s greater temperature.
In conclusion, there are important distinctions between cold chamber and hot chamber systems with regard to alloy type, processing temperature, mould life, etc.
Suitable for materials that need high pressure die casting
Cast iron: It is one of the commonly used die-casting mold materials, with good machining performance and casting performance, and low cost. Nevertheless, cast iron is readily distorted by high temperatures, has low wear resistance and hardness, and is prone to brittle fracture.
Alloy steel: It is one of the high-end materials for die-casting molds. In particular, it possesses high strength, high hardness, and high heat resistance. It also has outstanding hot processing and anti-wear qualities. As a result, alloy steel can create intricate and sizable die-casting moulds, albeit at a comparatively expensive cost.
High-speed steel and carbide: Despite being more expensive, these materials provide superior thermal stability and wear resistance, making them ideal for producing intricate die-casting moulds subjected to high pressure and temperature.
Aluminum/magnesium/zinc/copper and other alloy materials: These are the base materials used in the high-pressure casting industry, among which high-pressure aluminum die-casting is the most widely used.
High-Pressure Die Casting Applications
Automobile Sector:
In the automobile industry, HPDC is commonly used to produce parts including engine blocks, gearbox housings, and structural elements. The process’s capacity to produce strong, lightweight components fits in well with the automobile sector’s quest of performance and fuel economy.
Electronics for consumers:
HPDC is used in the consumer electronics industry to create small, complex parts like laptop parts and casings for smartphones. These components are guaranteed to fulfil the exacting criteria of contemporary electronic gadgets by the accuracy of the procedure.
High-Pressure Die Casting’s Future
Technological Progress:
High-pressure die casting is constantly evolving due to developments in die casting technology, such as the creation of sophisticated materials and improved machine capabilities. Efficiency gains, component quality improvements, and application range expansions are driven by these advancements.
Mindwell Manufacturer of Customized High Pressure Die Casting Services
Mindwell is able to provide services for high pressure die casting.
- Technology and equipment: Mindwell has cutting-edge melting furnaces, die-casting machines, moulds, and other high-pressure die-casting apparatus. These devices use the most recent technological advancements and production techniques to guarantee the creation of castings of the highest calibre. The business also has a skilled technical staff that can provide complete technological solutions and assistance.
- Material Handling: Mindwell is skilled in working with a wide range of materials, including ferrous metals like steel and non-ferrous metals like aluminium, zinc, and magnesium. Based on the requirements of the client and the properties of the material, the firm may recommend an appropriate die-casting procedure and material choice.
- Mould design: Mindwell has a qualified mould design staff that can create precise and effective mould designs in accordance with client specifications and product specifications. For mould design and manufacture, the firm employs CAD/CAM software, which guarantees mould accuracy and production efficiency.
- Quality control: Mindwell has put in place a stringent quality control system to guarantee the dependability and quality of castings. Every step in the supply chain, from the acquisition of raw materials to the delivery of completed goods, is subject to stringent quality inspection and supervision. Additionally, the business has successfully completed the ISO 9001 quality management system certification process to provide clients more trustworthy quality guarantee.
- Service and support: Mindwell offers a comprehensive variety of services and support, such as technical assistance, after-sale service, and guidance on the die-casting process. The business guarantees seamless production and high-quality client products by keeping regular lines of communication open and quickly resolving issues that arise throughout the manufacturing process.
Mindwell has all the necessary tools, technology, material handling, mould design, quality control, and service and support systems to provide high-pressure die-casting services. Due to these qualities, the business has gained the respect and goodwill of its clients.
In summary
High-pressure die casting, which provides unmatched accuracy, efficiency, and diversity, has firmly established itself as a mainstay in the metalworking industry. The high-pressure die casting method continues to influence sectors and spur innovation in anything from consumer electronics to automobile components. The capabilities of HPDC are expected to grow as technology develops, creating new avenues for the production of complex and superior metal components.