Введение
Литье алюминия под высоким давлением подходит для производства крупногабаритных, высокоточных, высокоплотных алюминиевых отливок, таких как автомобильные капоты, алюминиевые рамы и т.д. Благодаря таким преимуществам, как высокая эффективность, высокая точность и хорошая обработка поверхности, литье алюминия под высоким давлением также подходит для производства электрических приборов, радиосвязи, телевизоров, компьютеров, сельскохозяйственной техники, медицинского оборудования, стиральных машин, холодильников, часов, камер, архитектурного декора и компонентов для различных изделий, таких как повседневная фурнитура.
Литье алюминия под высоким давлением - это гибкий и эффективный метод производства, обладающий рядом преимуществ для различных товаров. В этом процессе расплавленный алюминий впрыскивается под высоким давлением в стальную форму, в результате чего получаются замысловатые, детализированные изделия, отличающиеся удивительной точностью и качеством. В этом посте мы рассмотрим множество категорий продукции, которые могут получить огромную выгоду от литья алюминия под высоким давлением.
Что такое литье алюминия под высоким давлением?
Технология литья алюминия под высоким давлением подразумевает впрыскивание расплавленного алюминия под высоким давлением в стальную форму или литейную форму с помощью оборудования для литья под давлением для получения готовой алюминиевой отливки. Литье под давлением и литье под высоким давлением - вот некоторые названия этой техники.
Технология литья алюминия под высоким давлением предполагает быстрое заполнение полости литейной формы жидким алюминием, жидким металлом или сплавом, содержащим упрочняющие фазы, под высоким давлением. Затем жидкость застывает под давлением, образуя отливку. Скорость заливки металла составляет от 0,5 до 120 м/с, а обычно используемый диапазон давлений - 4~500 МПа. Двумя основными отличиями и существенными характеристиками процесса литья под давлением являются высокое давление и высокая скорость, так как расплавленный металл заполняет полость формы в среднем за 0,01-0,2 секунды.
Этот метод литья подходит для производства крупногабаритных алюминиевых отливок, таких как автомобильные капоты и алюминиевые рамы, и может обеспечить высокую плотность и высокую точность алюминиевых отливок. Кроме того, поскольку алюминиевые отливки могут быть сформированы в различные более сложные формы, они также могут быть созданы с большей гладкостью и точностью, что уменьшает количество металлических припусков и механической обработки, необходимых для литья, и экономит деньги на рабочую силу, металлические материалы и электроэнергию.
Однако литье алюминия под высоким давлением имеет ряд недостатков, среди которых дорогостоящее оборудование, невозможность изготовления крупных деталей и непригодность для производства тонкостенных компонентов. Напротив, литье алюминия под низким давлением имеет такие преимущества, как простота эксплуатации и управления, менее дорогое оборудование и возможность производства деталей с тонкими стенками. Однако его стоимость выше, он не может создавать огромные детали, а эффективность производства относительно низкая.
На каких типах продуктов он может применяться?
Автомобильные запчасти
Литье алюминия под высоким давлением является одним из основных компонентов, используемых в автомобильной промышленности для производства различных деталей и компонентов. Для автомобильной промышленности эта технология производства обеспечивает прочность, долговечность и точность размеров, необходимые для всех деталей - от блоков и головок цилиндров до корпусов коробок передач и деталей подвески. Легкие свойства алюминия также повышают общую производительность и топливную экономичность автомобиля.

Электроника
В электронной промышленности литье алюминия под высоким давлением широко используется для производства корпусов, радиаторов и других компонентов. Алюминий - отличный материал для рассеивания тепла и обеспечения нормальной работы электронного оборудования благодаря своей исключительной теплопроводности и электрическим характеристикам. Свобода дизайна электрических устройств еще больше увеличивается благодаря возможности создавать тонкие барьеры и сложные формы.
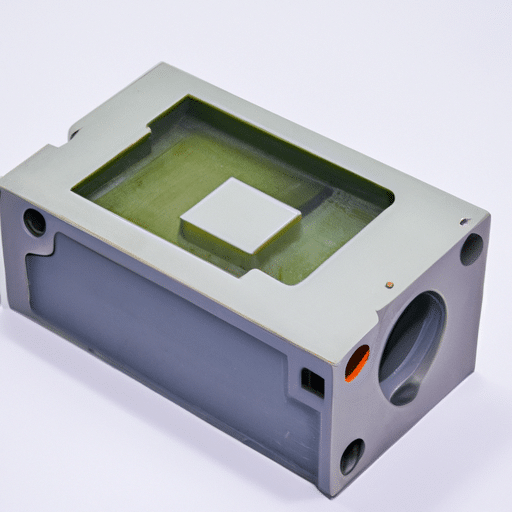
Промышленное оборудование
Литье алюминия под высоким давлением - распространенный метод, используемый производителями промышленного оборудования для создания прочных и надежных компонентов. Алюминиевые компоненты обеспечивают исключительную коррозионную стойкость, высокое соотношение прочности и веса, а также стабильность размеров для всего - от насосов и клапанов до компрессоров и турбин. Эти характеристики делают их идеальными для сложных промышленных применений, где важны долговечность и производительность.
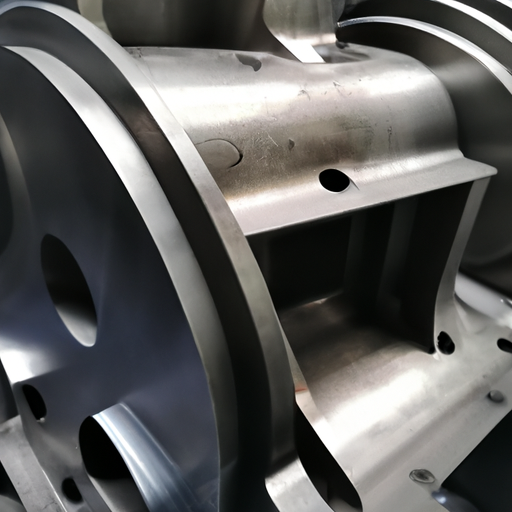
Аэрокосмическая промышленность
Прочные и легкие компоненты необходимы авиационной промышленности, и литье алюминия под высоким давлением удовлетворяет эту потребность. Эта процедура используется авиастроителями для изготовления деталей, включая структурные элементы, кронштейны и корпуса двигателей. Благодаря малому весу, высокой прочности и жесткости алюминий является идеальным материалом для аэрокосмической промышленности, где снижение веса необходимо для повышения производительности и экономии топлива.
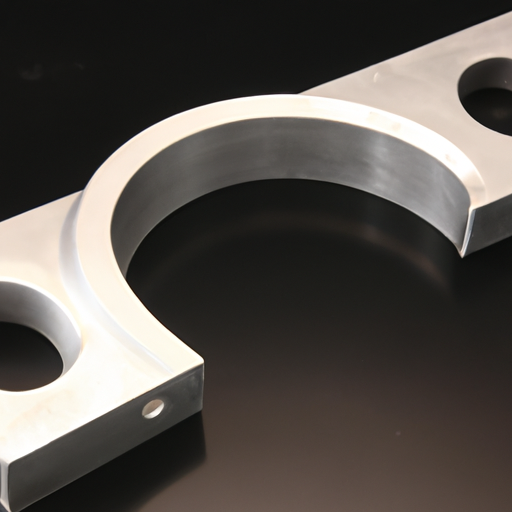
Спорт и отдых
Спорт и досуг - еще одна отрасль, в которой широко используется литье алюминия под высоким давлением. Алюминий является распространенным материалом для компонентов рыболовных катушек, туристического снаряжения, велосипедных рам и головок клюшек для гольфа благодаря своим легким и прочным качествам. Производители могут оптимизировать производительность и функциональность при сохранении соответствующих весовых и прочностных характеристик благодаря возможности разработки сложных конструкций и сложных форм.
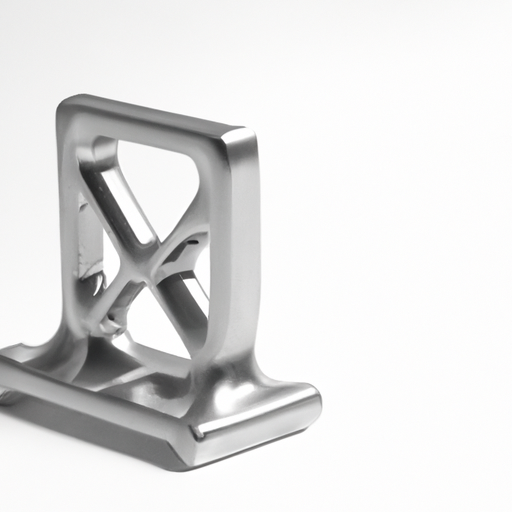
Преимущества и недостатки литья алюминия под высоким давлением
Литье алюминия под высоким давлением имеет следующие преимущества:
- высокая точность и плотность: Впрыск под высоким давлением может гарантировать высокую точность и плотность алюминиевых отливок, что приводит к производству высококачественных алюминиевых отливок.
- Подходит для производства больших алюминиевых отливок: Литье алюминия под высоким давлением подходит для производства крупных алюминиевых отливок, включая автомобильные капоты и алюминиевые рамы, так как оно может производить большее давление.
- Высокая эффективность производства: Благодаря постоянному производству большого количества изделий литье алюминия под высоким давлением может снизить производственные затраты и повысить эффективность производства.
- Простота и легкость в управлении: Литье алюминия под высоким давлением - сравнительно простой в эксплуатации процесс, что может снизить эксплуатационные трудности и повысить стабильность производства.
Тем не менее, у литья алюминия под высоким давлением есть и ряд недостатков.
- Непомерные расходы на оборудование Затраты на оборудование значительны для литья алюминия под высоким давлением, поскольку для него требуются машины для литья под высоким давлением и соответствующие пресс-формы.
- Не подходит для производства тонкостенных деталей: при литье алюминия под высоким давлением создается большее давление, что может привести к разрушению или деформации тонкостенных деталей. По этой причине оно не подходит для производства тонкостенных деталей. порция.
- Невозможность изготовления огромных деталей: Хотя крупные алюминиевые отливки можно изготавливать с помощью литья алюминия под высоким давлением, производство очень крупных деталей может быть ограничено формами и оборудованием.

Разница между литьем под высоким давлением и литьем под низким давлением
Различия между литьем под высоким и низким давлением заключаются в изменении давления и скорости заполнения. Как литье под низким давлением, так и литье под высоким давлением имеют свои преимущества и недостатки, поэтому выбор оптимального метода для конкретного применения зависит от требований и назначения конечного продукта.
Давление при литье под высоким давлением сравнительно велико: обычно оно составляет от сотен до тысяч кПа, а иногда достигает десятков тысяч кПа. Одновременно с этим скорость заливки столь же высока, часто составляет от 10 до 50 м/с, а иногда превышает 100 м/с. Два основных преимущества литья под высоким давлением - возможность получения отливок с точными размерами и гладкой поверхностью: высокое давление и высокая скорость заполнения литейных форм. Кроме того, прочность и твердость отливок выше - как правило, на 25-30% выше, чем при литье в песчаные формы. Кроме того, литейная форма, используемая при литье под высоким давлением, долговечна, позволяет получать сложные и тонкостенные отливки, обладает высокой производительностью, проста в автоматизации и механизации.
Литье под низким давлением, с другой стороны, обычно работает при давлении от 0,01 до 0,05 МПа. В целом, темп заливки похож на гравитационную заливку и является несколько вялым. Литье под низким давлением имеет плохую полировку поверхности и низкую эффективность производства из-за низкого давления и вялых характеристик заливки. Как правило, оно не подходит для изделий с тонкими стенками.
Заключение
несколько преимуществ литье алюминия под высоким давлением для широкого спектра изделий в нескольких отраслях. Благодаря превосходному качеству, точности и адаптируемости, это излюбленная технология производства электроники, предметов для спорта и отдыха, промышленного оборудования, автомобильных деталей и аэрокосмических компонентов. Используя преимущества литья алюминия под высоким давлением, производители могут выпускать надежные и креативные товары, отвечающие требованиям современного рынка.