The use of aluminum components in the automotive industry is very common, and aluminum parts offer several advantages. Firstly, the raw material is resistant to rust, has good heat dissipation properties, and reduces the overall vehicle weight. Aluminum alloy, known for its high plasticity during processing, can be used to create various complex and lightweight components. Lastly, aluminum alloy materials meet environmental certification standards.
As a material for vehicle bodies, aluminum is not inferior in strength to the three major components: the engine, transmission, and chassis. If a new car uses an aluminum alloy body, manufacturers not only emphasize its benefits in presentations but also showcase the bare aluminum body at car shows, dealerships, and malls. Consumers also pay significant attention to aluminum usage, and any reduction in aluminum components in a new car may lead to strong reactions from enthusiasts online. The question arises: How much stronger is aluminum compared to steel? Apart from being lightweight, what other unique advantages does aluminum have? Why do car manufacturers prefer aluminum?
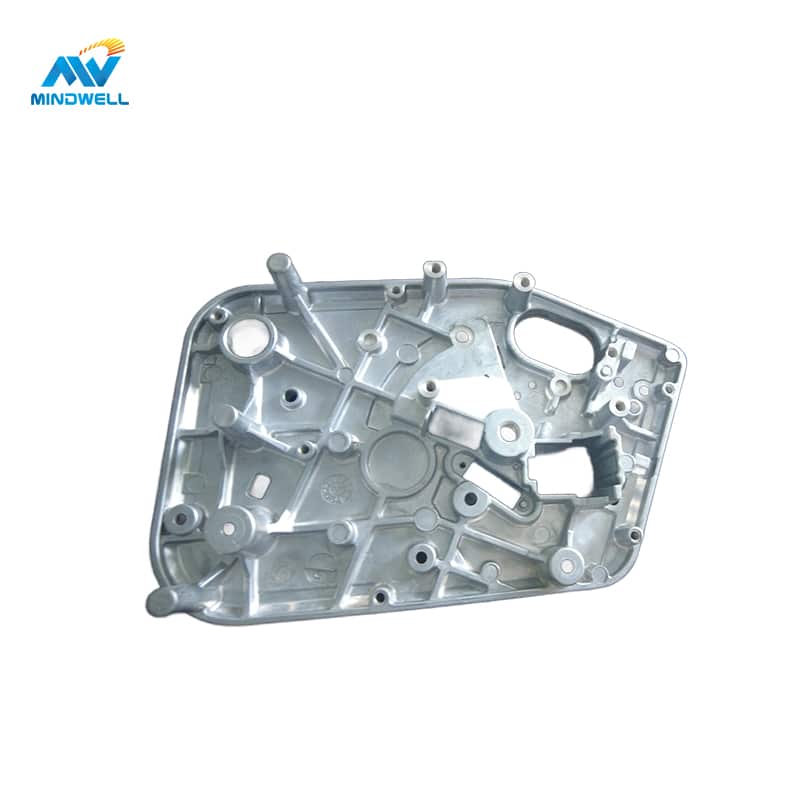
Lightweight
Compared to the steel used in budget cars, aluminum alloy’s most significant advantage is its lightweight nature. Steel has a density of 7.8g/cm³, whereas aluminum’s density is only 2.7g/cm³. This means that, for an equivalent volume, aluminum weighs only about one-third of steel, or even lighter than the well-known lightweight titanium alloy with a density of 4.5g/cm³.
Reducing the weight of vehicles with aluminum alloy materials brings numerous benefits. A lighter car has lower inertia, resulting in reduced resistance to changes in its state during acceleration, deceleration, or cornering, thereby improving response times. This lighter weight also significantly reduces fuel consumption. Research indicates that for every 100kg reduction in vehicle weight, fuel consumption can decrease by 0.3 to 0.6 liters per 100 kilometers. This reduction is crucial given the stringent fuel consumption and emission regulations in place.
In addition to the inertial benefits, using lighter aluminum alloy coverings can lower the vehicle’s center of gravity and optimize front-to-rear weight distribution. This optimization enhances the handling and driving experience by reducing body roll during cornering.
For electric vehicles, aluminum’s advantages become even more pronounced. With every 10% increase in weight, an electric vehicle’s energy consumption increases by 5.5%. The weight savings from using aluminum in the body can lead to more efficient energy use and extended range, making aluminum a preferred choice for high-end electric vehicles.
Suspension Components
Aluminum alloy shines in the walking parts of a vehicle, particularly in suspension components like control arms. The reduced weight of aluminum control arms means lower inertia, allowing for easier movement. This improved movement, especially over bumpy surfaces, enhances tire contact with the road, making the vehicle more controllable and improving ride comfort.
Enhanced Rigidity
Increasing a vehicle’s rigidity is typically achieved by adding more material. However, aluminum’s advantage becomes evident in this aspect. While aluminum requires 40% more volume than steel to achieve the same strength, its weight is only one-third of that of steel in the same volume. This allows aluminum-bodied vehicles to achieve superior rigidity by “recklessly” adding material, surpassing steel-bodied vehicles.
Energy Absorption
The flexibility and elasticity of aluminum alloy make it effective at absorbing energy, a quality observed in beverage cans made of aluminum. In collisions, aluminum can absorb twice as much energy as an equivalent weight of steel. This property is beneficial for enhancing crash safety by using aluminum in areas prone to deformation, reducing the impact transferred to the passenger compartment.
However, due to its softer nature, aluminum is not suitable for rigid areas like A and B pillars in a vehicle. Advanced steel manufacturing technologies, such as ultra-high-strength hot-formed steel with a strength of 1800 MPa, have emerged. These steels surpass aluminum in both strength and weight, providing a compelling alternative.
Corrosion Resistance
While galvanized steel is often used for corrosion resistance, aluminum alloy surpasses it in areas with harsh conditions. Aluminum naturally forms a dense aluminum oxide film on its surface, preventing further reactions with the environment. This corrosion resistance is particularly advantageous for regions where road salt or other corrosive agents are used.

в заключение
In summary, aluminum’s material characteristics, including its lightweight nature, enhanced rigidity, energy absorption capabilities, and corrosion resistance, make it a preferred choice for various automotive components. The focus on aluminum is driven by the automotive industry’s pursuit of lightweighting, improved fuel efficiency, and meeting stringent environmental standards. Despite the challenges in manufacturing and repair costs, the benefits of aluminum in modern vehicles outweigh these concerns, leading to its widespread use in the automotive industry.