Custom Die Casting Services
MINDWELL adopts advanced die-casting machines, including FANUC, Yizumi, Zhengao, etc.
Focus on the production of aluminum alloy and zinc alloy die-casting parts.
- Workpiece precision machining
- Capacity: 50 to 500 tons
- Manual and automated production
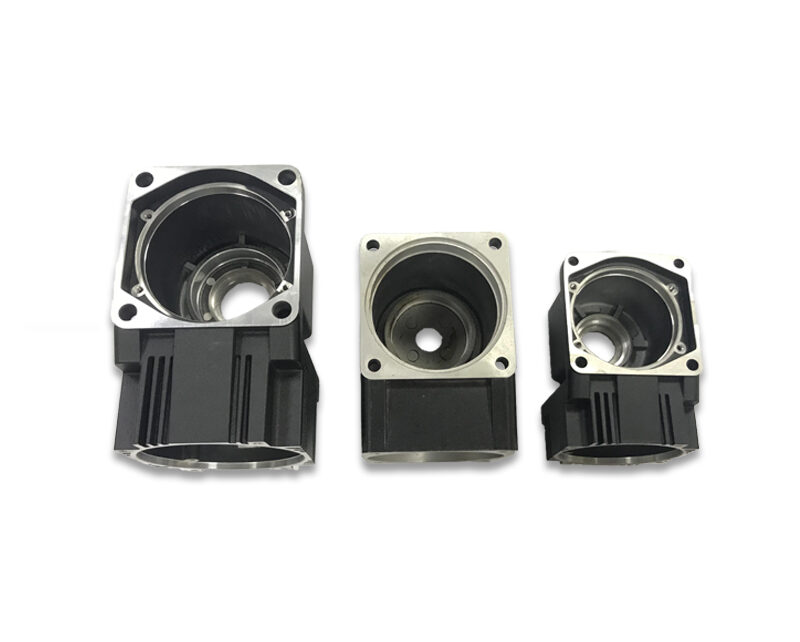
Precision Machining Services
Our Types Of Die Casting Process
MNW is a professional die-casting service manufacturer. We have been serving the European market since 2008. We have been producing die-casting parts according to European standards. If you consider customizing metal parts, MNW will be your best choice. We use Advanced die-casting equipment, and proficiency in the following three die-casting process capabilities.

Hot chamber die casting
Hot chamber die casting is a high-pressure casting technique, also known as hot chamber injection casting. It involves heating metal material to a certain temperature, injecting it into the mold of a die casting tool in molten form, and then forming the desired shape under high pressure. This technique is suitable for producing large and complex parts, such as engine housings for automobiles and computer casings. Compared to other casting techniques, hot chamber die casting provides higher production efficiency and higher product accuracy.
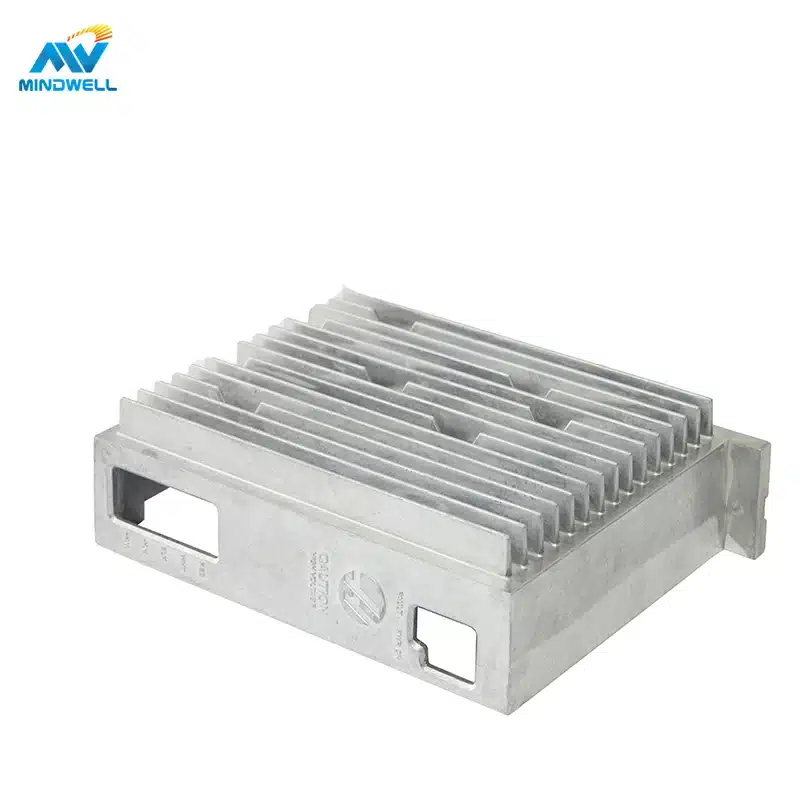
Cold chamber die casting
Cold chamber die-casting is the process of high-pressure injection during which the metal is kept in a molten state by a cooling system. This technology is suitable for producing high-strength and high-quality castings, especially for manufacturing engineering components and large-scale structural components. Cold chamber die-casting has the advantages of high production efficiency, high product accuracy, and low production cost, and is therefore widely used in fields such as automotive, aerospace, military, electronics, and communications.

Vacuum die casting
Vacuum casting is a casting technique that involves pressure casting in a vacuum environment to produce high-quality castings. In a vacuum, oxygen and other gases in the casting are extracted, which can eliminate gas pores, reduce gas suspension, gas entrapment, and other defects, improving the density and strength of the casting and achieving better surface quality. Vacuum casting is commonly used to manufacture high-performance alloy castings, such as aerospace engine components, automotive engine components, and medical equipment.
Custom Die Casting Materials
According to the manufacturing requirements of metal die-casting parts, different materials are selected for die-casting. The characteristics of each material are different, so different materials can be selected according to the industry used and the use scene of the parts.
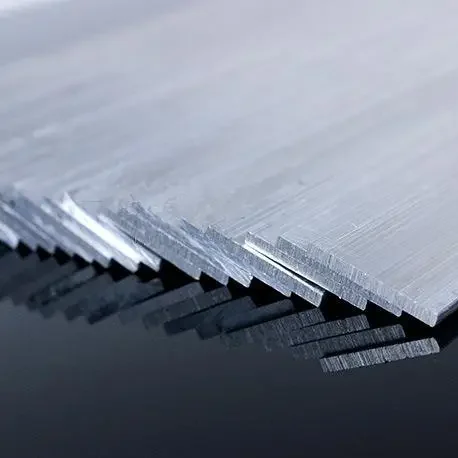
Aluminum Alloy Die Casting
We can also do pure aluminum die-casting, more die-casting will use aluminum alloy materials,Aluminum alloy is a material composed of aluminum and other alloying elements. Aluminum alloys are characterized by low density, high strength, good corrosion resistance, and good electrical conductivity. Aluminum alloy also has good plasticity and weldability, and is easy to process and assemble.
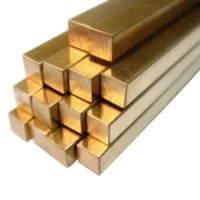
Pirinç Basınçlı Döküm
Brass is a yellow metal with good electrical conductivity, thermal conductivity and plasticity, so it is widely used in electric power, construction, communication, automobile, machinery manufacturing and other fields. Brass has good corrosion resistance and reliable strength, and can be made into various forms such as pipes, wires, and alloys. Commonly used Brass materials are copper, brass, bronze, copper-titanium alloy, etc.
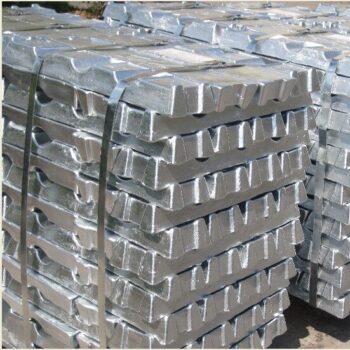
Çinko Alaşımlı Basınçlı Döküm
Zinc alloy is a material composed of zinc and other elements. It usually has excellent physical and chemical properties, such as high strength, toughness, corrosion resistance and easy casting. Zinc alloys are commonly used in the manufacture of automotive parts, aerospace components, electronic equipment, locks, zippers and other mechanical parts. Commonly used zinc alloys include Zamak, Zinkam, Zplex, and ZAc, etc.,

Magnesium Alloys
Magnesium alloy die casting is a manufacturing process in which magnesium alloy is melted and injected into a die-casting mold,Due to the lightweight, high strength and good corrosion resistance of magnesium alloys, magnesium alloy die casting has the advantages of high productivity, low cost, high quality and repeatability compared to other manufacturing methods.It is widely used in automotive, electronics, aerospace and other fields.
Why Choose MINDWELL for Die Casting Parts
MindWell Die Casting Factory can provide a variety of different production methods and solutions according to the needs and requirements of customers. We have rich experience and advanced die-casting equipment in die-casting process. We have a complete quality management system, implement ISO 9001 international standards, and provide customers with the most suitable solutions and products.
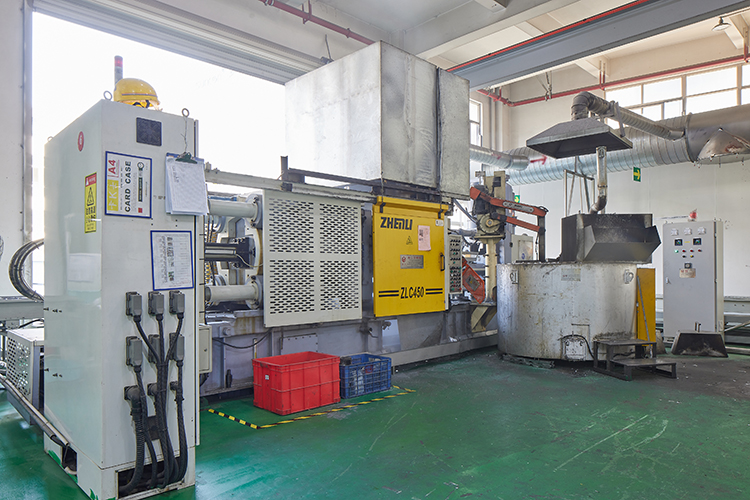
Advanced technology
MindWell die-casting factory has the most advanced die-casting equipment and technology to meet various needs of customers.

Die Casting Workshop
MindWell die casting factory has more than 15 years of experience, which can provide professional service and high-quality products..
Get Started Now with Custom Die Casting Services According to Your Needs!
Custom Die Casting Solutions
Our company offers custom die-casting services, where customers can request a quote based on their specific needs, and we will quickly confirm and reply. As a professional die-casting supplier, we always provide on-demand services and can customize any shape, size, or material according to your requirements.
1. Drawing inquiry
According to the requirements and needs of customers, understand the shape, size, material and other requirements of parts, and propose suggestions and solutions.
2. Design and production
According to the data provided by the customer, conduct quotation and feasibility analysis, and make samples through 3D printing technology, CNC or die-casting technology.
3. Sample confirmation
send the sample to the customer for confirmation, if improvement is needed, you can continue to improve the design.
4. Mass production
After sample confirmation, enter the mass production stage, and produce according to customer order requirements.
5. Quality inspection
Carry out quality inspection for the produced die castings to ensure compliance with customer requirements and standards.
6. Packaging and delivery
After the quality inspection is completed, the product is packaged and sent to the customer.
Die Casting Surface Finishes
In the production of die-casting parts, in order to improve the surface quality and function of the parts, we usually carry out surface treatment. The surface treatment of MNW’s metal parts is done by outside cooperation within 3 kilometers, which can be carried out quickly and at low cost.
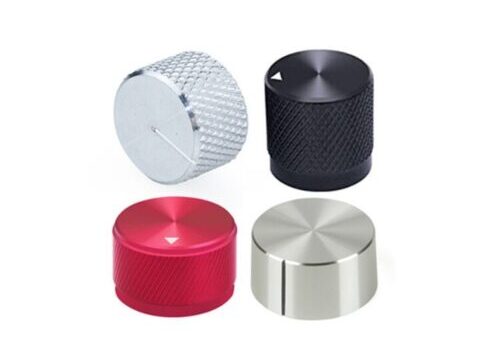
The surface treatment of die castings includes the following:
- Parlatma
- Püskürtme
- Kaplama
- Oxidation treatment
- Kumlama
- Spray phosphating
- Paint
environmental impact of die casting:
MNW avoids the impact of the die-casting process on the environment, and starts with the selection of environmentally friendly materials, improvement of the production process, and waste treatment to achieve long-term protection of the environment.
- Use environmentally friendly materials
- Fully adopt closed production process
- Reasonable selection of process
- Enhance waste utilization and treatment
- Introduce advanced control technology
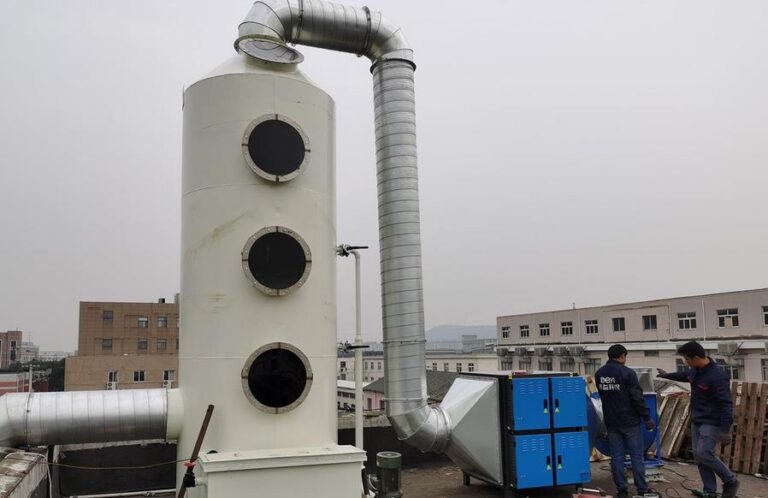
Casting Products Examples
For 15 years, MNW has dedicated itself to delivering top-notch die-cast parts to clients in Europe and the United States. Our factory has rigorously adhered to technical standards, ensuring the provision of only premium custom die-casting services to our customers. Should you require custom die-casting parts, we invite you to peruse our collection of produced die-castings.
Die Casting Applications
Die casting is an efficient and precise processing technology. Due to its high efficiency, precision and high quality, the die casting process is mainly suitable for the production of large quantities of metal parts, such as automobile and motorcycle parts, used in electronic equipment, construction and manufacturing Metal products, as well as household appliances and so on.
Otomotiv Endüstrisi
Die casting has the characteristics of high strength, light weight, wear resistance, good sealing, etc., and can also ensure precision and surface finish. Therefore, it is widely used in auto parts, involving many aspects such as engine, transmission system, suspension system and braking system.
Furniture
The use of die castings in furniture manufacturing can achieve the purpose of strengthening product structure, improving product quality and aesthetics. Such as sofas, beds and chairs, applied to frame structures, high-quality connectors, handles and handles, etc.
Electronic
Many parts in electronic equipment can be manufactured using die castings, some of the applications include: electronic housings that protect the circuits and electronic components inside electronic equipment, heat sinks, electrical connectors, computer heat sinks, electronic switches, buttons, LEDs Electronic inserts for lamps, etc.
Medical
Die-casting technology is widely used in medical equipment. Many medical equipment need to use die-casting parts, such as aluminum alloy castings for X-ray machines, and casings for cardiac pacemakers. Die-casting technology can improve product quality, reduce production costs, and shorten production cycles
Advantages Of Pressure Die Casting
The die casting process can produce castings with high density and uniform structure, so it is more suitable for the manufacture of parts with higher quality requirements than other casting methods.
MNW has accumulated rich manufacturing experience in the die-casting process, and compared with other processes, it has summarized the following advantages:
- High product precision
- Stable process
- High efficiency
- Strong plasticity
- Saving raw materials
Custom Die Casting Related Blogs
MINDWELL has a professional technical team. Our professional technical personnel have rich experience in fine control of product design, manufacturing process, process flow, etc., and will share these experiences with you.
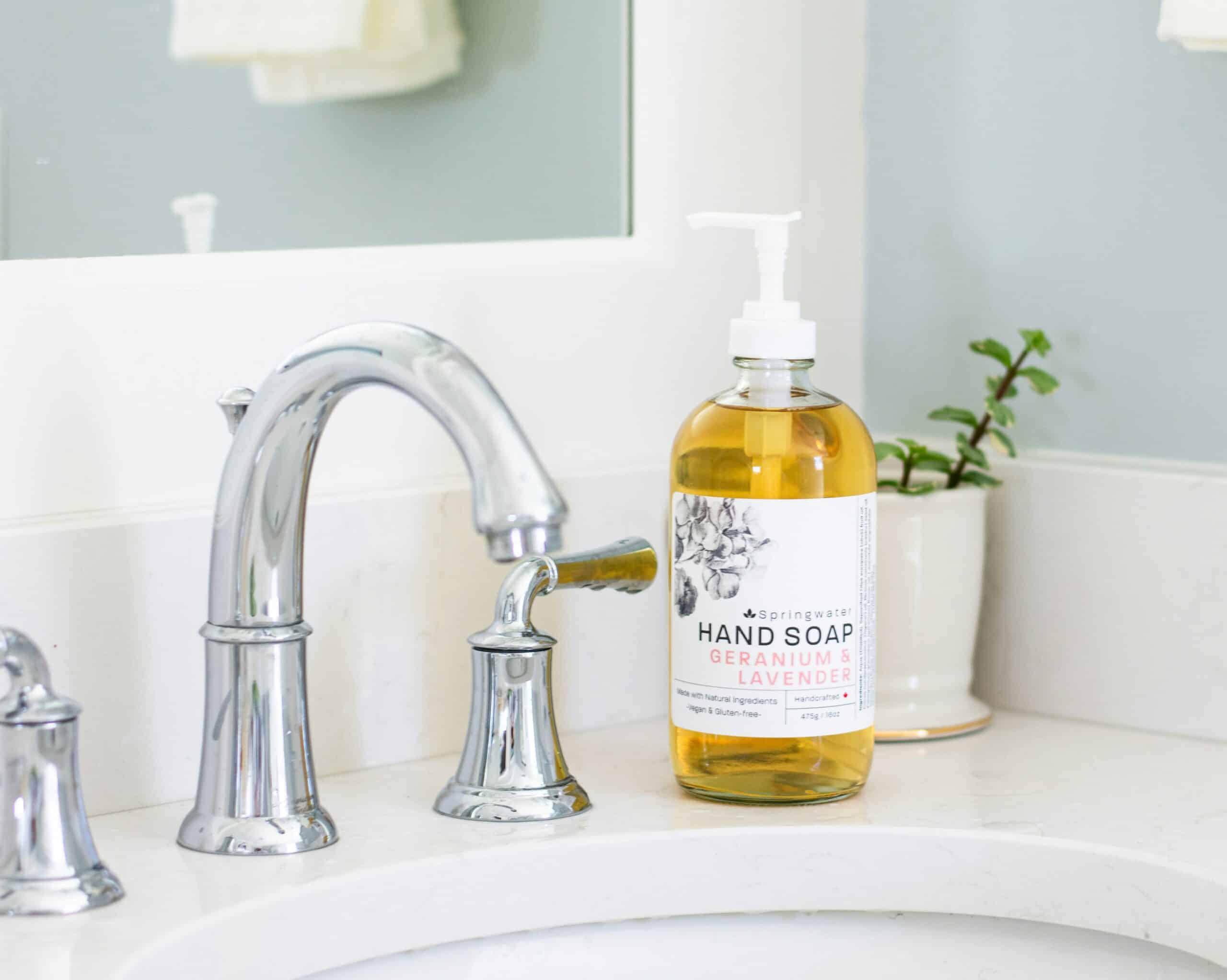
Elektronik Bileşenler için Isı Yönetiminde Alüminyum Isı Emici Muhafazanın Önemi
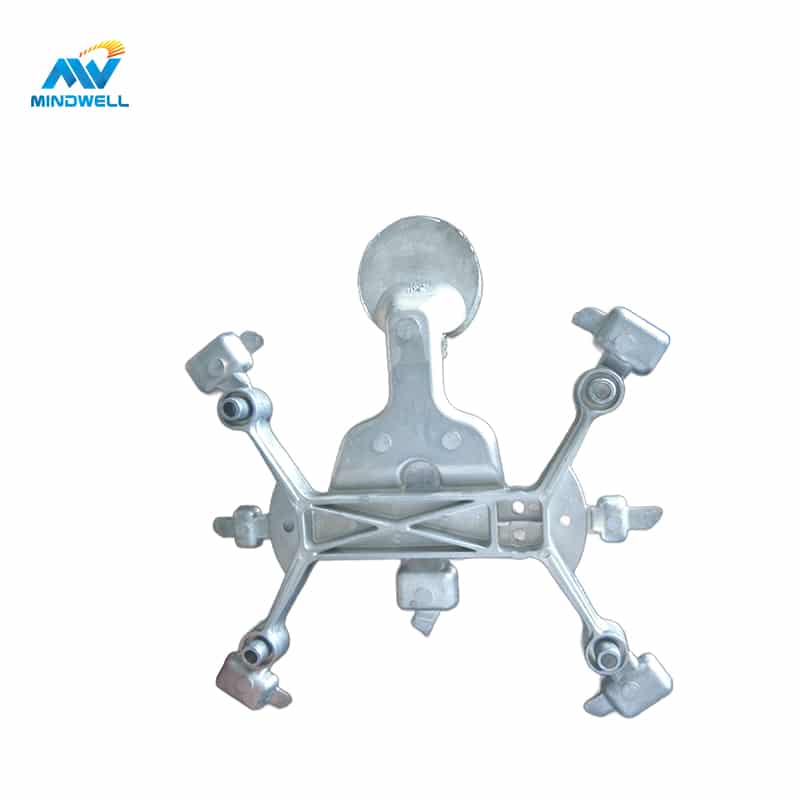
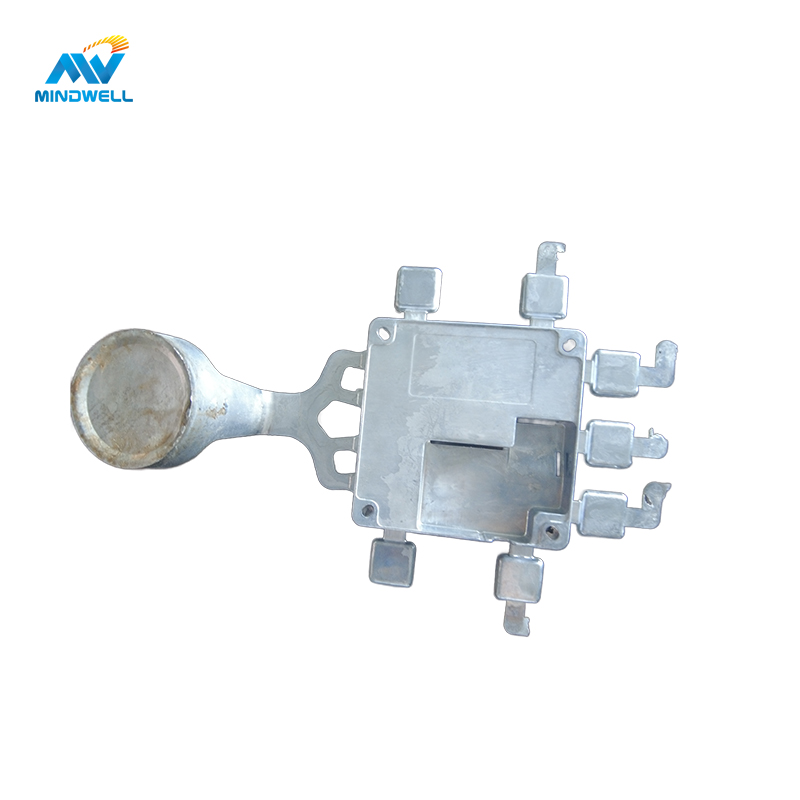
Yüksek Basınçlı Alüminyum Basınçlı Dökümde Ürünlerin Estetiğini Hangi Adımlar Geliştirebilir?
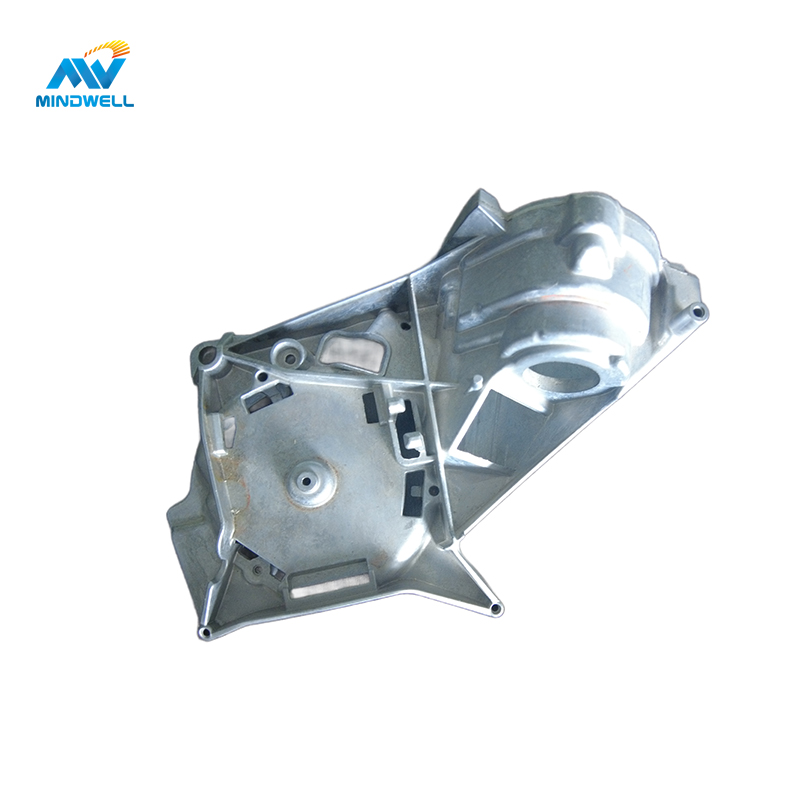
Dayanıklılık Üretmek: Yüksek Basınçlı Alüminyum Basınçlı Dökümün Rolü

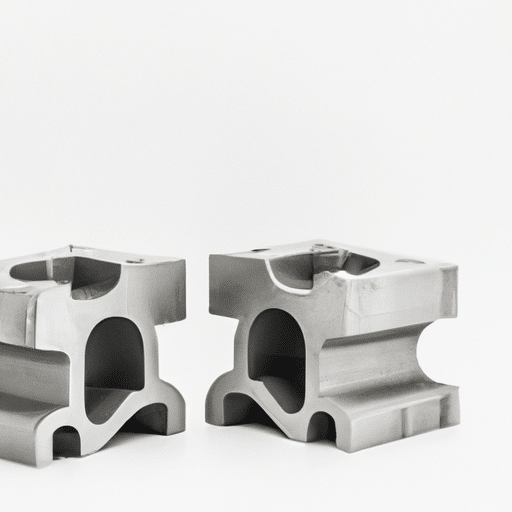

Yüksek Basınçlı Dökümde Alüminyum Kullanmanın Avantajları Nelerdir?

Yüksek Basınçlı Alüminyum Basınçlı Dökümden Ne Tür Ürünler Faydalanabilir?
Sıkça Sorulan Sorular
Die casting is a process in which aluminum, zinc, copper, magnesium, and other alloy melts are injected into a die casting machine’s mold under pressure, and then cooled and solidified to form a product. Die casting parts typically have a high degree of precision and surface quality and can be processed and treated as needed.
Common die casting materials include aluminum alloy, zinc alloy, magnesium alloy, copper alloy, and plastic. Aluminum alloy is one of the most commonly used materials and is widely used due to its high strength, corrosion resistance, and plasticity.
The die casting manufacturing process involves several critical steps, such as mold design, heat treatment, die casting, coating, and surface treatment. Mold design is crucial and must be accurately tailored to the product’s shape, size, and specifications, taking into account material flow and cooling. dapibus leo.
Die castings have several key advantages, including low manufacturing cost, high machining precision, excellent surface quality, and stable dimensions. Die castings are also well-suited for mass production, allowing for the production of complex shapes with exceptional accuracy.
MNW is a professional custom die casting service manufacturer with extensive experience and cutting-edge die casting technology. Our advanced die-casting equipment has the capacity to meet various customization needs, ranging from 50-500 tons, catering to different customer requirements.
Anında Teklif Alın
Ücretsiz enjeksiyon kalıplama teklifinizi bugün talep edin ve iletişim kurmak için size geri dönelim.