Basınçlı döküm otomobil parçalarının sırlarını ve araç performansını nasıl artırdıklarını ortaya çıkarın. Bu hassas mühendislik ürünü bileşenlerin arkasındaki uygulamaları, faydaları ve teknolojileri keşfedin.
tanıtmak
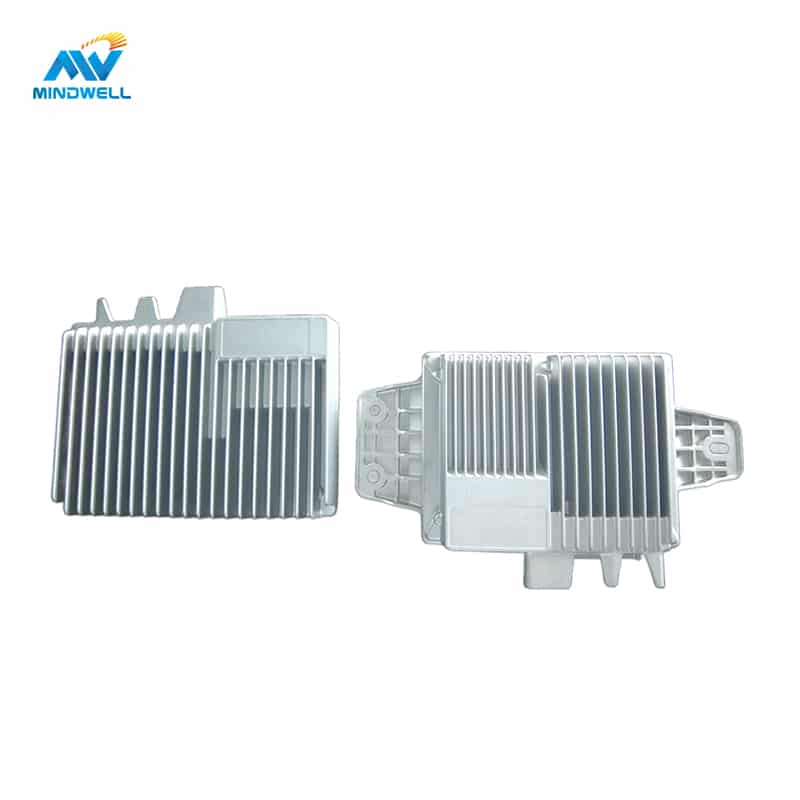
Karmaşık bir alan olan otomotiv üretiminde basınçlı döküm, özellikle yüksek performanslı otomotiv bileşenlerinin üretiminde hayati bir rol oynamaktadır. Bu kılavuz, otomotiv endüstrisini ileriye götüren uygulamaları, faydaları ve teknolojik yenilikleri ortaya koyarak basınçlı döküm otomotiv parçaları dünyasına derinlemesine bir bakış atmaktadır.
🔗 Otomotiv bilginizi geliştirin: Basınçlı döküm uygulamalarını keşfedin
Otomobil üretiminde basınçlı dökümün anlaşılması
Basınçlı döküm teknolojisinin evrimi
Basınçlı döküm teknolojisi, otomotiv imalat endüstrisindeki ihtiyaçlara ve değişikliklere uyum sağlamak için zaman içinde gelişmeye ve evrimleşmeye devam ediyor. İşte kalıp döküm teknolojisinin otomotiv üretiminde nasıl geliştiği:
- İlk aşama: İlk kalıp döküm teknolojisi çoğunlukla küçük, basit metal parçalar üretmek için kullanılıyordu. Basınçlı döküm makinesinin küçük ölçekli olması nedeniyle, üretilen parçaların boyutları da nispeten küçüktür. Bu aşamadaki basınçlı döküm teknolojisi esas olarak üretim verimliliğini artırmaya ve maliyetleri düşürmeye odaklanmaktadır.
- Olgunluk aşaması: Otomobil endüstrisinin gelişmesiyle birlikte basınçlı döküm parçalara olan talep giderek artmaktadır. Basınçlı döküm makineleri giderek daha büyük ve daha karmaşık hale gelmekte, daha büyük ve daha karmaşık parçalar üretebilmektedir. Aynı zamanda, kalıp tasarımı, malzeme seçimi, üretim teknolojisi vb. gibi kalıp döküm teknolojisinin çeşitli yönleri de geliştirilmiş ve optimize edilmiştir.
- İnovasyon aşaması: Son yıllarda, bilim ve teknolojinin sürekli ilerlemesi ve yenilikçiliği ile birlikte, kalıp döküm teknolojisi de birçok değişikliğe uğramıştır. Örneğin, alüminyum, magnezyum ve diğer hafif malzemeler gibi yeni kalıp döküm malzemeleri, parçaların kalitesini ve performansını artırmak için yaygın olarak kullanılmaktadır. Aynı zamanda, kalıp döküm teknolojisindeki yenilikler, karmaşık şekilli parçaların üretimini gerçekleştirebilen ve üretim verimliliğini ve kalitesini artırabilen dijital ikiz teknolojisi, 3D baskı ve diğer teknolojileri de içerir.
Basınçlı döküm teknolojisi, otomobil üretiminde birçok gelişim ve evrim aşamasından geçmiştir. Geleneksel kalıp döküm yöntemlerinden modern yenilikçi süreçlere kadar, kalıp döküm teknolojisi otomotiv üretim endüstrisinin ihtiyaçlarına ve değişikliklerine uyum sağlamak için sürekli olarak gelişmektedir. Gelecekte, bilim ve teknolojinin sürekli ilerlemesi ve yenilikçiliğiyle, kalıp döküm teknolojisi gelişmeye ve evrimleşmeye devam edecek ve otomobil üretim endüstrisine daha fazla fırsat ve zorluk getirecektir.
Otomobil Parçaları Hassasiyetinin Önemi
Otomotiv parçaları üretiminde hassasiyet çok önemli bir faktördür. Basınçlı döküm teknolojisi için hassasiyet, parçaların kalitesini, performansını ve güvenliğini doğrudan etkiler. İşte hassasiyetin aşağıdakilerde nasıl kilit bir rol oynadığı döküm otomoti̇v parçalari:
- Kalite Güvencesi: Hassasiyet, basınçlı döküm parçaların kalitesinin sağlanmasında kilit bir faktördür. Basınçlı döküm işlemi sırasında, kalıbın tasarım ve üretim doğruluğu, malzemelerin kontrolü ve doldurulması, basınç ve sıcaklığın ayarlanması, vb. nihai ürünün boyutsal doğruluğunun ve yüzey kalitesinin gereksinimleri karşılamasını sağlamak için hassas bir şekilde kontrol edilmesi gerekir. Bileşenlerin güvenilirliği ve hizmet ömrü ancak belirli bir doğruluk seviyesine ulaşılarak garanti edilebilir.
- Performans iyileştirmeleri: Hassasiyet, basınçlı döküm parçaların performansını da doğrudan etkiler. Örneğin, yüksek hassasiyetli basınçlı döküm parçalar sürtünmeyi ve aşınmayı azaltabilir, şanzıman verimliliğini ve hizmet ömrünü artırabilir. Buna ek olarak, hassasiyet bileşenlerin mukavemetini, sertliğini ve yorulma direncini de artırarak aracın genel performansını iyileştirebilir.
- Güvenlik garantisi: Döküm otomobil parçalarının hassasiyeti de doğrudan aracın güvenliği ile ilgilidir. Örneğin, yüksek hassasiyetli fren sistemi bileşenleri frenlemenin doğruluğunu ve zamanında yapılmasını sağlayabilir ve araçların frenleme performansını ve güvenliğini artırabilir. Buna ek olarak, hassasiyet motorlar, şanzımanlar vb. gibi diğer önemli bileşenlerin de güvenli çalışmasını sağlayabilir ve bileşen arızalarından kaynaklanan güvenlik sorunlarını önleyebilir.
- Maliyetleri azaltın: Basınçlı döküm parçaların hassasiyetini artırarak, sonraki işleme ve düzeltme işlemlerinin zorluğu ve süresi azaltılabilir ve üretim maliyetleri düşürülebilir. Aynı zamanda, yüksek hassasiyetli parçalar hurda ve onarım oranlarını da azaltarak genel işletme maliyetlerini düşürebilir.
- Yenilikçi tasarımların gerçekleştirilmesi: Yüksek hassasiyetli kalıp döküm teknolojisi daha karmaşık ve sofistike otomotiv parçaları tasarımını destekleyebilir. Tasarımcılar daha verimli, hafif ve yüksek performanslı otomotiv parçaları elde etmek için ürün tasarımına daha yenilikçi fikirler entegre edebilir.
Hassasiyet, basınçlı döküm otomotiv parçalarında hayati bir rol oynar. Basınçlı döküm işleminin hassasiyet kontrol seviyesinin iyileştirilmesiyle parçaların kalitesi, performansı ve güvenliği sağlanabilir, üretim maliyetleri azaltılabilir ve yenilikçi tasarımların gerçekleştirilmesi desteklenebilir. Bu nedenle, basınçlı döküm teknolojisi için hassasiyetin sürekli olarak iyileştirilmesi, otomotiv imalat endüstrisinin sürdürülebilir gelişimini sağlamanın önemli bir yoludur.
Geleceği şekillendiren malzemeler: döküm alaşımları
Basınçlı döküm alaşımları, otomotiv bileşenlerinin dayanıklılığını, gücünü ve genel performansını doğrudan etkiledikleri için otomotiv üretiminde hayati bir rol oynamaktadır. İşte yaygın olarak kullanılan bazı basınçlı döküm alaşımları ve özellikleri:
- Alüminyum alaşım: Alüminyum alaşımı, basınçlı dökümde en yaygın kullanılan alaşımlardan biridir. Hafiflik, korozyon direnci ve iyi termal iletkenlik avantajlarına sahiptir. Otomobil üretiminde, alüminyum alaşımları motor parçaları, fren sistemi parçaları vb. gibi otomobil parçalarını üretmek için yaygın olarak kullanılmaktadır. Alüminyum alaşımlarının mukavemeti ve sertliği nispeten düşüktür, ancak ısıl işlem ve alaşım elementlerinin eklenmesiyle geliştirilebilir.
- Çinko Alaşım: Çinko alaşımı, iyi döküm özellikleri ve korozyon direncine sahip nispeten ucuz bir döküm alaşımıdır. Otomobil üretiminde, çinko alaşımı esas olarak jantlar, kapı kaplamaları vb. gibi görünüm parçaları ve dekoratif parçalar yapmak için kullanılır. Çinko alaşımları nispeten düşük mukavemet ve sertliğe sahiptir, bu da onları yük taşıyan bileşenlerin üretiminde kullanım için uygun hale getirmez.
- Magnezyum alaşımı: Magnezyum alaşımı, iyi döküm özelliklerine ve korozyon direncine sahip hafif, yüksek mukavemetli bir döküm alaşımıdır. Otomobil üretiminde, magnezyum alaşımları yük taşıyan parçaların ve kaput, kapı gibi görünüm parçalarının üretiminde yaygın olarak kullanılır. Magnezyum alaşımı, alüminyum alaşımı ve çinko alaşımından daha yüksek mukavemet ve sertliğe sahiptir, ancak maliyeti de nispeten yüksektir.
- Çelik Alaşım: Çelik alaşımı, yüksek mukavemet, yüksek sertlik ve iyi korozyon direncine sahip bir döküm alaşımıdır. Otomobil üretiminde, çelik alaşımlar esas olarak yük taşıyan parçalar ve çerçeveler, hava yastıkları vb. gibi güvenlik parçaları yapmak için kullanılır. Çelik alaşımların maliyeti nispeten düşüktür, ancak döküm performansı zayıftır ve döküm sürecinin sıkı bir şekilde kontrol edilmesi gerekir.
Bir basınçlı döküm alaşımı seçerken, parçaların kullanımı, performans gereksinimleri ve maliyet gibi faktörlerin göz önünde bulundurulması gerekir. Farklı alaşımların farklı avantaj ve dezavantajları vardır ve gerçek koşullara göre seçilmeleri gerekir. Örneğin, yüksek mukavemet ve korozyon direnci gerektiren yük taşıyıcı parçalar için magnezyum alaşımlarını veya çelik alaşımlarını seçebilirsiniz; iyi döküm performansı ve güzel görünüm gerektiren dekoratif parçalar için çinko alaşımlarını veya alüminyum alaşımlarını seçebilirsiniz.
Özetle, döküm alaşımları otomobil üretiminin ayrılmaz bir parçasıdır. Farklı alaşımların farklı özellikleri ve uygulama aralıkları vardır ve gerçek koşullara göre seçilmeleri gerekir. Bilim ve teknolojinin sürekli ilerlemesi ve yenilikçiliği ile gelecekteki basınçlı döküm alaşımları daha verimli, çevre dostu ve sürdürülebilir olacak ve otomobil üretim endüstrisine daha fazla fırsat ve zorluk getirecektir.
Otomotiv endüstrisindeki uygulamalar
Motor bileşenleri: güç performansı sağlama
Basınçlı döküm teknolojisi, motor bileşenlerinin üretiminde önemli bir rol oynar ve içten yanmalı motorların gücünü ve verimliliğini artırabilir. Aşağıda motor bileşenlerinde basınçlı döküm uygulamaları yer almaktadır:
- Silindir Kapağı: Silindir kapağı, silindiri çevreleyen ve pistonu barındıran motorun önemli bir parçasıdır. Silindir kapaklarını üretmek için kalıp döküm teknolojisi kullanılabilir. Yüksek hassasiyetli kalıp ve malzeme kontrolü sayesinde silindir kapağının boyut ve şekil doğruluğunun gereksinimleri karşılaması sağlanabilir. Döküm silindir kapakları, motor gücünü ve verimliliğini artırmak için hafif ve yüksek mukavemetlidir.
- Piston: Piston, motorun temel bileşenlerinden biridir ve silindirle birlikte yanma odasını oluşturur. Kalıp döküm teknolojisi piston üretiminde kullanılabilir, hassas kalıp ve malzeme kontrolü sayesinde pistonların hafifliği ve minyatürleştirilmesi sağlanabilir. Basınçlı döküm pistonlar yüksek mukavemet, korozyon direnci ve iyi termal iletkenlik sunar, bu da motor performansını ve güvenilirliğini artırır.
- Krank mili: Krank mili, motorda gücü iletmek ve piston hareketini sağlamak için kullanılan önemli bir bileşendir. Kalıp döküm teknolojisi, yüksek hassasiyetli kalıp ve malzeme kontrolü sayesinde yüksek mukavemet, hafiflik ve korozyon direnci elde ederek krank milleri üretmek için kullanılabilir. Döküm krank milleri motor gücünü ve verimliliğini artırır ve yakıt tüketimini azaltır.
- Eksantrik Mili: Eksantrik mili motorda önemli bir bileşendir ve valflerin açılıp kapanmasını kontrol etmek için kullanılır. Döküm teknolojisi, hassas kalıp ve malzeme kontrolü sayesinde yüksek hassasiyet ve minyatürleştirme elde ederek eksantrik milleri üretmek için kullanılabilir. Döküm eksantrik milleri yüksek mukavemet, korozyon direnci ve iyi termal iletkenlik sunar, bu da motor performansını ve güvenilirliğini artırır.
- Volan: Volan, motorda önemli bir bileşendir ve kinetik enerjiyi depolamak ve serbest bırakmak için kullanılır. Hassas kalıp ve malzeme kontrolü sayesinde yüksek mukavemet, hafiflik ve korozyon direnci elde ederek volan üretmek için kalıp döküm teknolojisi kullanılabilir. Döküm volanlar motor verimliliğini ve yakıt tasarrufunu artırır.
Şanzıman Muhafazası: Dikişsiz Güç Aktarımı
Basınçlı döküm, şanzıman gövdelerinin üretiminde önemli bir rol oynar. Hassas döküm sayesinde yüksek kaliteli, yüksek verimli şanzıman gövdeleri üretilebilir, bu da kesintisiz güç aktarımına yardımcı olur ve otomotiv şanzımanlarının performansını optimize eder.
İlk olarak, basınçlı döküm karmaşık şekil ve yapılara sahip dişli kutusu gövdeleri üretebilir. Basınçlı döküm işlemi sırasında erimiş metalin iyi akışkanlığı ve doldurma kabiliyeti nedeniyle, ince duvarlı ve karmaşık yapılar üretilebilir, hafif ve verimli üretim elde edilebilir. Bu karmaşık yapı, dişli kutusunun performansını iyileştirebilir ve aktarım verimliliğini artırabilir.
İkinci olarak, basınçlı dökümle üretilen dişli kutusu muhafazası yüksek hassasiyete ve istikrarlı kaliteye sahiptir. Hassas döküm teknolojisi, döküm boyutlarının hassas kontrolünü sağlayabilir, böylece dişli kutusunun montaj doğruluğunu ve performansını garanti eder. Buna ek olarak, kalıp döküm işlemi sırasında erimiş metalin düzgün bir şekilde doldurulması ve katılaşması, gerilim yoğunlaşması ve büzülme boşlukları gibi kusurları azaltabilir ve dişli kutusunun güvenilirliğini ve hizmet ömrünü artırabilir.
Son olarak, kalıp döküm şanzıman muhafazası özelleştirilmiş üretime olanak tanır. Farklı otomobil modellerinin ve markalarının dişli kutularının performansı ve tasarımı için farklı gereksinimleri vardır ve kalıp döküm teknolojisi üretimi farklı ihtiyaçlara göre özelleştirebilir. Bu esneklik, otomobil üreticilerinin farklı müşterilerin ihtiyaçlarını karşılamak için pazar talebine göre üretim planlarını hızla ayarlamasına olanak tanır.
Şasi ve Yapısal Bileşenler: Güç ve Ağırlığın Dengelenmesi
Basınçlı döküm, araç güvenliği ve dengesi için çok önemli olan güç ve ağırlık arasındaki mükemmel dengeyi sağlamak için şasi ve yapısal bileşenlerin üretiminde önemli bir rol oynar.
İlk olarak, basınçlı döküm yüksek mukavemetli şasi ve yapısal bileşenler üretebilir. Basınçlı döküm işlemi sırasında erimiş metalin iyi akışkanlığı ve doldurma kabiliyeti nedeniyle, ince duvarlı ve karmaşık yapılara sahip bileşenler üretilebilir, hafif ve verimli üretim elde edilebilir. Aynı zamanda, kalıp döküm işlemi sırasında erimiş metalin düzgün bir şekilde doldurulması ve katılaştırılması, gerilim yoğunlaşması ve büzülme boşlukları gibi kusurları azaltabilir ve bileşenlerin gücünü ve güvenilirliğini artırabilir. Bu yüksek mukavemetli şasi ve yapısal bileşen, araç güvenliğini ve dengesini artırır.
İkinci olarak, basınçlı döküm karmaşık yapılara ve hassas boyutlara sahip şasi ve yapısal bileşenler üretebilir. Hassas döküm teknolojisi, döküm boyutlarının hassas kontrolünü sağlayabilir, böylece bileşenlerin montaj doğruluğunu ve performansını garanti eder. Bu hassas boyut ve yapı, bileşenler arasındaki sürtünmeyi ve titreşimi azaltarak aracın dengesini ve konforunu artırır.
Ayrıca basınçlı döküm seri üretim kabiliyetine de sahiptir. Basınçlı döküm işlemi sırasında erimiş metalin iyi akışkanlığı ve doldurma özellikleri nedeniyle, birden fazla parça üretilebilir ve seri üretim sağlanabilir. Bu seri üretim kabiliyeti, araç şasisi ve yapısal bileşenlere yönelik pazar talebini karşılarken üretim maliyetlerini düşürebilir ve üretim verimliliğini artırabilir.
Son olarak, basınçlı döküm ayrıca özelleştirilmiş üretime de olanak tanır. Farklı araç modelleri ve markaları, şasi ve yapısal bileşenlerin performansı ve tasarımı için farklı gereksinimlere sahiptir ve basınçlı döküm teknolojisi, üretimi farklı ihtiyaçlara göre özelleştirebilir. Bu esneklik, otomobil üreticilerinin farklı müşterilerin ihtiyaçlarını karşılamak için pazar talebine göre üretim planlarını hızlı bir şekilde ayarlamasına olanak tanır.
3. Yüzey işleme teknolojisi
Basınçlı döküm yüzey işleme teknolojisi, otomotiv bileşenlerinin estetiğini ve korozyon direncini iyileştirmek için kritik öneme sahiptir. Aşağıda yaygın olarak kullanılan birkaç yüzey işleme teknolojisi yer almaktadır:
- Shot peening: Shot peening, yüksek hızlı hava akışı yoluyla iş parçasının yüzeyine mermiler püskürten, iş parçasının yüzeyinde plastik deformasyona neden olan ve böylece iş parçasının yorulma mukavemetini ve korozyon direncini artıran bir yüzey güçlendirme işlemidir. Shot peening, korozyon direncini ve estetiğini artırmak için silindir kapakları, pistonlar vb. gibi döküm otomotiv parçalarına uygulanabilir.
- Toz püskürtme: Toz püskürtme yaygın olarak kullanılan bir yüzey kaplama işlemidir. Toz kaplama, yoğun bir kaplama oluşturmak için elektrostatik püskürtme veya akışkan yataklı püskürtme yoluyla iş parçasının yüzeyine eşit olarak püskürtülür. Toz kaplama, korozyon direncini ve estetiğini iyileştirmek için gövde panelleri, jantlar vb. gibi döküm otomotiv parçalarına uygulanabilir.
- Elektrokaplama: Elektrokaplama, elektroliz prensibiyle bir iş parçasının yüzeyine metal biriktiren bir işlemdir. İş parçasının yüzeyinde özel özelliklere sahip bir metal kaplama tabakası oluşturabilir. Elektrokaplama, korozyon direncini ve aşınma direncini artırmak için burçlar, dişliler vb. gibi döküm otomotiv parçalarına uygulanabilir.
- Eloksal: Eloksal, elektroliz prensibiyle metal yüzeyini oksitleyerek bir oksit filmi haline getiren bir işlemdir. Metalin korozyon direncini ve estetiğini iyileştirmek için metal yüzeyinde yoğun bir oksit filmi oluşturabilir. Eloksal, korozyon direncini ve estetiğini iyileştirmek için alüminyum alaşımlı parçalar gibi döküm otomotiv parçalarına uygulanabilir.
Basınçlı döküm yüzey işleme teknolojisi, otomotiv bileşenlerinin estetiğini ve korozyon direncini iyileştirmek için kritik öneme sahiptir. Farklı yüzey işleme teknolojileri farklı özelliklere ve uygulama aralıklarına sahiptir ve gerçek koşullara göre seçilmeleri gerekir. Bilim ve teknolojinin sürekli ilerlemesi ve yenilikçiliğiyle, gelecekteki yüzey işleme teknolojisi daha verimli, çevre dostu ve sürdürülebilir olacak ve otomobil üretim endüstrisine daha fazla fırsat ve zorluk getirecektir.

4. Sıkça Sorulan Sorular
Döküm otomobil parçaları için yaygın olarak hangi malzemeler kullanılır?
Alüminyum, çinko ve magnezyum alaşımları, hafif yapıları ve mükemmel mekanik özellikleri nedeniyle kalıp döküm otomotiv parçaları için yaygın olarak kullanılmaktadır.
Basınçlı dökümler araç yakıt verimliliğini nasıl artırır?
Basınçlı döküm bileşenlerin hassas ve hafif özellikleri, araç ağırlığını azaltmaya ve enerji tüketimini azaltarak yakıt verimliliğini artırmaya yardımcı olur.
Döküm otomobil parçaları çevre dostu mu?
Evet, basınçlı döküm, atıkları en aza indirdiği ve kullanılan malzemeler geri dönüştürülebilir ve sürdürülebilir üretim uygulamalarıyla tutarlı olduğu için çevre dostu bir süreçtir.
Basınçlı dökümler elektrikli araç parçaları için kullanılabilir mi?
Elbette basınçlı döküm, elektrikli araç parçalarının üretiminde yaygın olarak kullanılmakta, hafif tasarımlarına ve genel verimliliklerine katkıda bulunmaktadır.
Basınçlı dökümler otomobil yapısal parçalarının güvenliğini nasıl sağlar?
Basınçlı döküm parçaların hassasiyeti, yapısal bileşenlerin katı güvenlik standartlarını karşılamasını sağlayarak çeşitli sürüş koşullarında dayanıklılık ve güvenilirlik sağlar.
Otomotiv uygulamaları için basınçlı döküm teknolojisinde ne gibi gelişmeler bekleniyor?
Basınçlı döküm teknolojisinde devam eden gelişmeler arasında gelişmiş alaşım formülasyonları, artan otomasyon ve karmaşık parçaların üretiminde artan verimlilik yer almaktadır.
Sonuç: Mükemmel otomobillerin geleceğini desteklemek
Özetle, basınçlı döküm otomotiv parçaları modern otomotiv üretiminin bel kemiği haline gelmiş olup, hassasiyet, verimlilik ve yenilikçiliği bünyesinde barındırmaktadır. Otomotiv endüstrisi geliştikçe, basınçlı dökümün rolü mükemmelliği teşvik etmeye ve geleceğin araçlarını şekillendirmeye devam ediyor.