Surface treatment
Surface treatment is a method used to improve the state of a part’s surface and its mechanical, physical or chemical properties. Generally, products manufactured by casting, injection molding and other mechanical processing methods, so most of them need to be further cleaned, hardened, ground, polished, painted or electroplated on all or part of the surface to improve various characteristics of the surface. Smoothness and aesthetics.
- Customize different surface treatment methods according to characteristics
- Extend the service life of parts
- Restoring calculation accuracy of part surface dimensions

Customizable
4 types of surface treatment process
Surface treatment is a process of artificially forming a surface layer on the surface of a base material with mechanical, physical and chemical properties different from the base, in order to meet the corrosion resistance, wear resistance, decoration or other special functional requirements of the product

Electrochemical surface treatment
Electrochemical surface treatment: anodizing, electrochemical polishing, electroplating
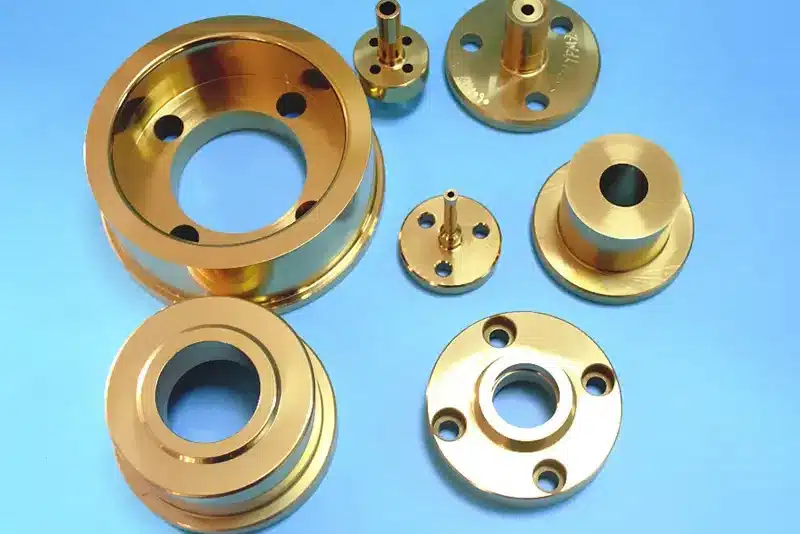
Modern surface treatment
Modern surface treatment: chemical vapor deposition CVD, physical vapor deposition PVD, ion implantation, ion plating, laser surface treatment, etc.

Mechanical surface treatment
Mechanical surface treatment includes sandblasting, shot blasting, polishing, rolling, polishing, brushing, spraying, painting, oiling, etc.

Chemical surface treatment
Chemical surface treatment: blue and black, phosphating, pickling, chemical plating of various metals and alloys, TD treatment, QPQ treatment, chemical oxidation, etc.
Surface Finish Specification
Our surface treatment specifications are differentiated for metal casting parts and plastic injection molding parts, and surface treatment methods can be selected according to different characteristics of different materials.
Metal surface finishing specifications

Anodizing
Mainly the anodic oxidation of aluminum is to use electrochemical principles to form a layer of Al2O3 (aluminum oxide) film on the surface of aluminum and aluminum alloy. This oxide film has special properties such as protection, decoration, insulation, and wear resistance.

ED-Electrophoresis deposition
Used in stainless steel, aluminum alloy, etc., can make the product present various colors, and maintain the metallic luster, while enhancing the surface properties, with good anti-corrosion performance.
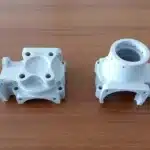
Micro Arc Oxidation (MAO)
The process of applying a high voltage in an electrolyte solution (usually a weakly alkaline solution) to form a ceramic surface film layer is the result of the synergistic effect of physical discharge and electrochemical oxidation.

Physical vapor deposition(PVD)
It is an industrial manufacturing process, which mainly uses physical processes to deposit thin films.
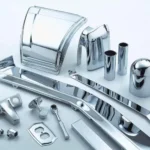
Electroplating
It is a technology that uses electrolysis to attach a layer of metal film to the surface of the metal to prevent corrosion, improve wear resistance, conductivity, reflectivity and enhance the appearance.
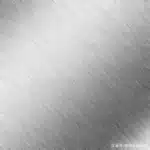
Metal wire drawing
It is a surface treatment method that forms lines on the surface of the workpiece by grinding products to achieve a decorative effect. According to the different textures after wire drawing, it can be divided into: straight wire drawing, chaotic wire drawing, corrugated, and swirling.
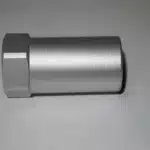
Sand blasting
It uses compressed air as the power to form a high-speed jet beam to spray the spray material onto the surface of the workpiece to be treated at high speed, so that the appearance or shape of the outer surface of the workpiece surface changes, and a certain degree of cleanliness and different roughness are obtained. a craft.

Polishing
The finishing process of the surface of the workpiece by using flexible polishing tools and abrasive particles or other polishing media.

Etching
Usually refers to etching, also known as photochemical etching, which refers to removing the protective film of the area to be etched after exposure to plate making and development, and contacting chemical solutions during etching to achieve the effect of dissolution and corrosion, forming concave-convex or hollow-out molding.
Plastic part surface finish specification
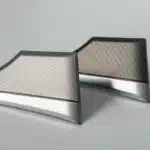
In-Mold Decoration-IMD
Put the patterned diaphragm into the metal mold, inject the resin for molding into the metal mold and join the diaphragm, so that the printed patterned diaphragm and the resin are integrated and solidified into a mold. A method of forming a finished product.
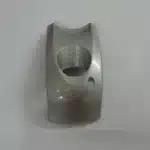
Painting
A coating method in which the paint is atomized with a spray tool such as a spray gun and sprayed on the workpiece to be coated.
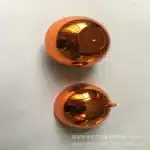
NCVM
Also known as discontinuous coating technology or non-conductive electroplating technology, it uses thin films such as metal and insulating compounds, and uses the discontinuous characteristics to obtain a final appearance that has a metallic texture and does not affect wireless communication transmission. .
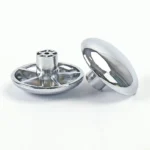
Plastic electroplating
Make plastics obtain metal effect surface with high yield and low cost. Similar to PVD, PVD is a physical principle, and electroplating is electroless plating, which is mainly divided into vacuum electroplating and water electroplating.
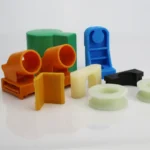
Plastic parts printing
It is a process of printing the required pattern on the surface of plastic parts by means of pad printing, screen printing, transfer printing, etc.

Laser engraving
also called laser engraving or laser marking, is a surface treatment process using optical principles, similar to screen printing and pad printing, through which laser engraving can be used to type or pattern on the surface of the product.

Bite pattern
It is a process method in which chemicals such as concentrated sulfuric acid are used to corrode the inside of the plastic molding mold to form lines in the form of snake lines, etch lines, plowing lines, etc. After the plastic is formed through the mold, the surface has corresponding lines.
MINDWELL's Surface Processing Capabilities
Mindwell is a hardware processing company, we have the ability of die-casting production workshop as well as injection molding production workshop and CNC machining. In many cases, the parts we manufacture need additional surface treatment according to the environment and characteristics of use, so our company also has the ability of surface treatment to bring customers a better experience.
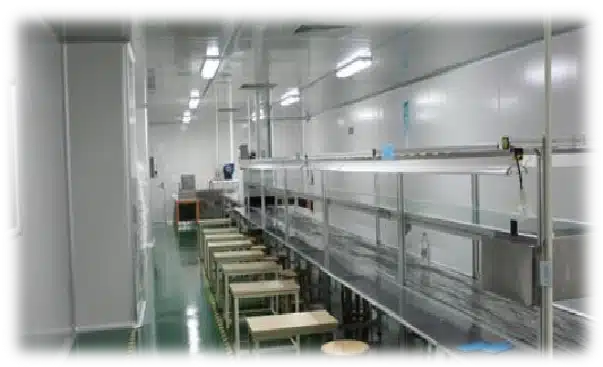


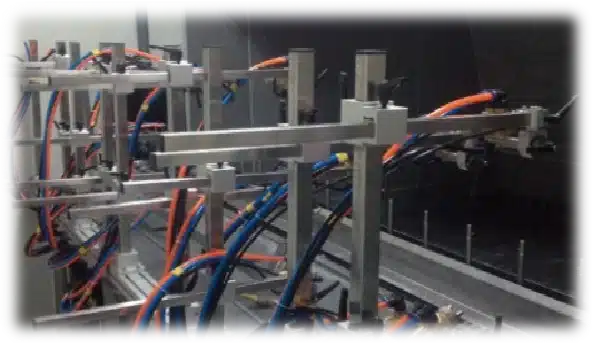

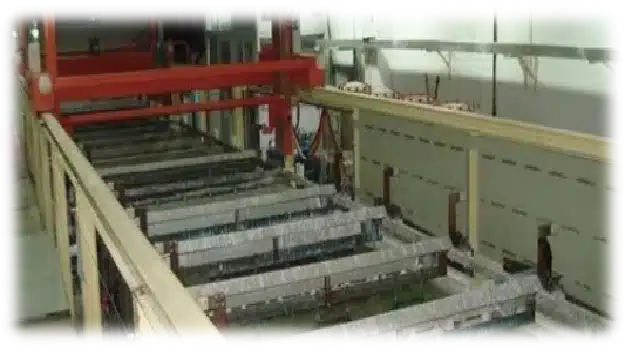
Get Started Now with Custom Surface treatment Services According to Your Needs!
Surface treatment examples
Products manufactured by casting and other mechanical processing methods, so most of them need to be further cleaned, hardened, ground, polished, painted or electroplated on all or part of the surface to improve the various characteristics, smoothness and electroplating of the surface. Beautiful etc.
Application and purpose of surface treatment:
- Increase surface hardness, wear resistance, fatigue resistance and other mechanical properties, and are used in molds, pistons, cylinders, machine tools, slide rails, shafts, gears, etc.
- Increase the resistance of the surface to corrosion and corrosion, and it is used in chemical machinery, veterinary appliances, and automobile sheet metal.
- Increase the heat resistance, heat conduction, heat reflection and other characteristics of the surface, and it is applied to heat sinks, aerospace engine parts, etc.
- Improve surface roughness and friction, and apply to the sliding surface of mechanical components, shafts and bearings, knives, tools, etc.
- Change the conductivity and resistance properties of the surface, and it is applied to electronic parts, memory, semiconductor components, etc.
- Change the reflection of light on the surface, selective absorption, weather resistance and other characteristics, and are used in reflectors, automobile and motorcycle parts, etc.
- Improve the cleanliness, luster, color, and beauty of the surface, and it is applied to various types of household products, sports equipment, and decorations.
Frequently Asked Questions
Surface treatment is the physical, chemical, or mechanical modification of a material’s surface in order to improve its performance, appearance, and durability.
Surface treatment can increase the material’s corrosion resistance, wear resistance, appearance, electrical conductivity, and other qualities, making it appropriate for a variety of applications and situations.
Surface treatment may improve the qualities of almost any material, including metals, polymers, glass, ceramics, and others.
Surface treatments can impact material strength depending on the manner of treatment and the kind of material. Some heat treatments can improve the material’s strength, while some coatings can influence the material’s hardness.
Yes, several surface treatment procedures, including as painting, spraying, and polishing, may modify the look of the material to produce various ornamental effects.
Painting, electroplating, heat treatment, sandblasting, polishing, nitriding, coating, etching, and other surface treatment processes are available.
Yes, surface treatment, particularly sophisticated treatment technologies, may raise the production cost of the material. They do, however, generally provide greater performance and look.
Material type, application demands, climatic conditions, budget, and design criteria must all be considered when choosing a surface finish. The best strategy may entail a trade-off between these variables.
specific surface preparation procedures, particularly for specific coatings and coatings, may have an effect on the recyclability of materials. Choosing environmentally friendly disposal options can help you lessen your environmental impact.
Some surface treatments, particularly coatings and paints, need ongoing upkeep. Maintenance ensures that materials continue to function and appear as intended.
Get Instant Quote
Request your free injection molding quote today and we will get back to you to establish communication.