Blog
MindWell communicates with you on the technical details and experience in the design and manufacture of customized die-casting parts and injection molding parts, and we look forward to your attention.
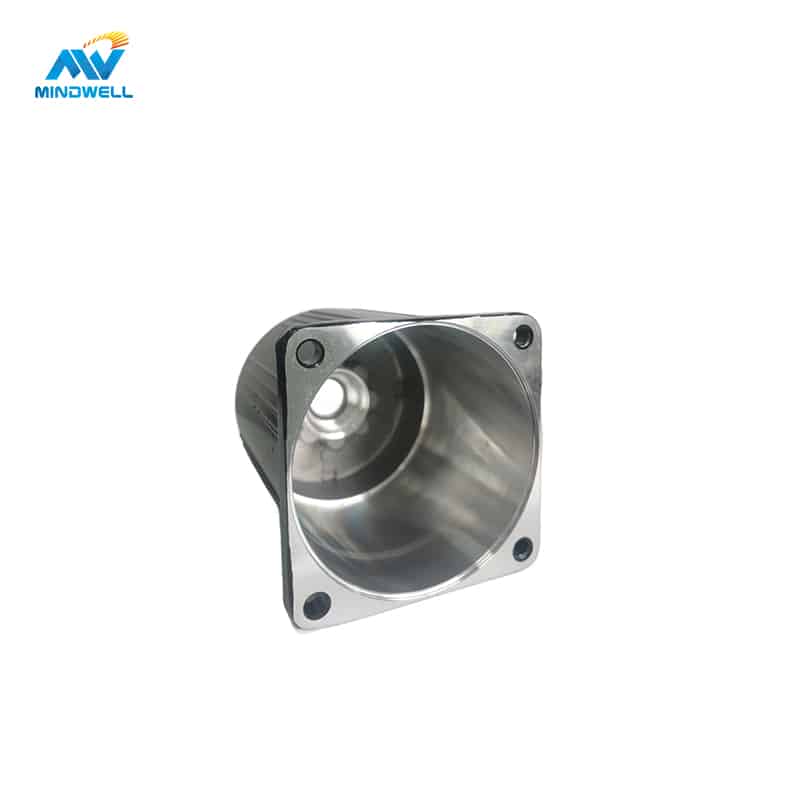
What are the types of aluminum alloys?
Is aluminum alloy? Yes, is the straightforward response. Rarely is pure aluminium, a lightweight and resistant-to-corrosion metal, used in industrial settings. Rather, it is mixed

High-Pressure Aluminum Die Casting: The Complete Guide
In the field of metal manufacturing, constant innovation is shaping the landscape of precision and efficiency. High-pressure aluminum die-casting stands out as a key technology

What Types of Products Can Benefit from High Pressure Aluminum Die Casting?
High-pressure aluminium die casting is a versatile production technique used in various sectors, including automotive, consumer electronics, lighting fixtures, industrial equipment, medical equipment, aerospace, and household appliances. This technique allows for the production of intricate, high-precision components with exceptional dimensional accuracy and material integrity. It is particularly beneficial for automotive components, such as cylinder heads, engine blocks, and gearbox cases, as well as for consumer electronics like laptops, tablets, and smartphones. Die-cast aluminium die casting also ensures heat dissipation and electromagnetic shielding, making it ideal for creating durable and lightweight enclosures for electronic devices. It also meets the demands of the aerospace sector, providing lightweight, high-performance materials for aircraft parts. The versatility of aluminium die casting continues to find new applications in various sectors.

What is high pressure die casting?
High pressure die casting is a precision casting method that involves injecting molten metal into a precisely crafted mould under high pressure. This technique is ideal for casting metal components made of alloys like aluminium, zinc, copper, and other alloys with intricate structures, thin walls, high accuracy requirements, and melting temperatures lower than steel. High-pressure die casting produces high-density and mechanically strong castings, ensuring the mould is filled quickly and completely. The process is facilitated by a high-pressure die casting machine, which is essential for reaching high production levels. Benefits of high-pressure die casting include accuracy in dimensions and precision, intricate geometries, quick rates of production, and superior material integrity.

What is high pressure aluminum die casting?
A very effective and adaptable production technique, high-pressure aluminum die casting is used to precisely create complex and detailed aluminum components. Because it can produce
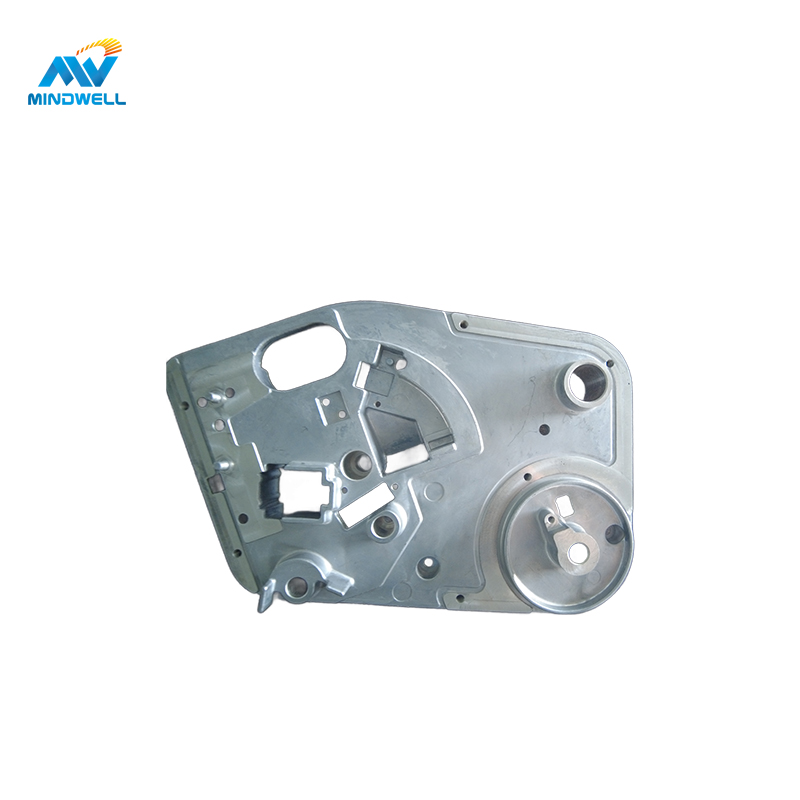
Customized High Pressure Aluminum Die Casting
High pressure aluminum die casting is a versatile manufacturing process that allows for the production of complex and intricately designed aluminum parts. This article will

Custom die-cast Aluminum Enclosures
Introductio Die casting is a popular manufacturing process used to create high-quality metal enclosures for various applications. One of the most commonly used materials for
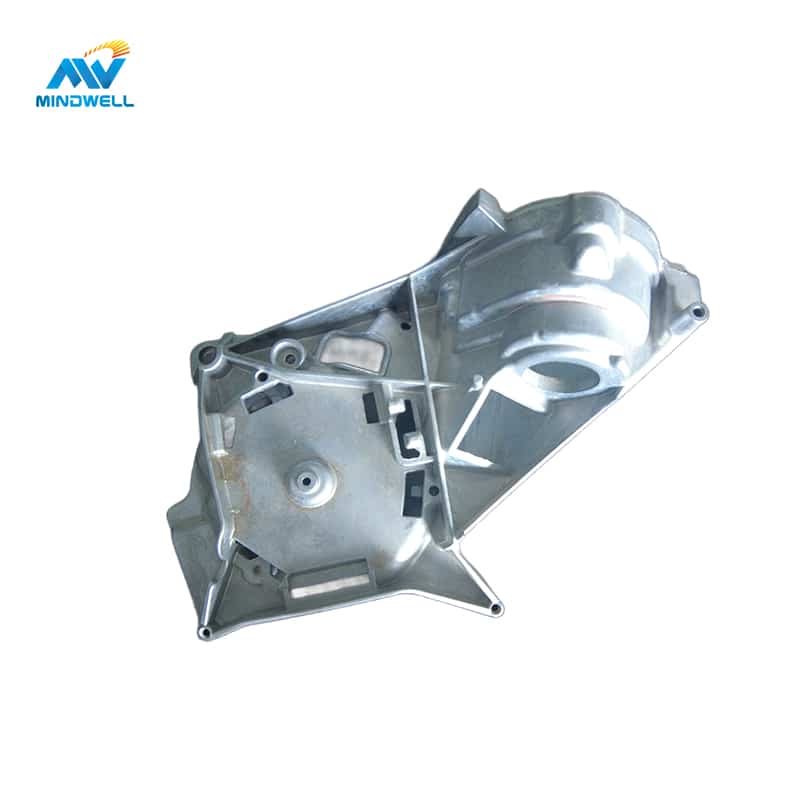
Aluminum Pressure Die Cast Motor Body: Engineering Excellence Unveiled
Explore the intricacies of manufacturing aluminum die-cast motor bodies. This comprehensive guide reveals the engineering excellence behind the process, its applications and the exceptional performance it brings to motors.
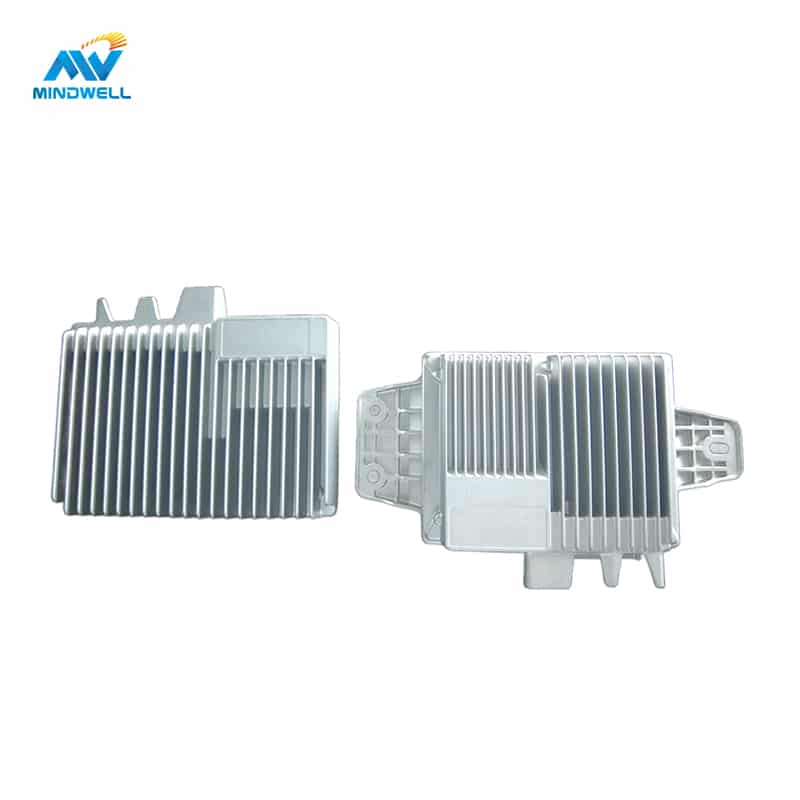
What Are High-Pressure Aluminum Die Casting Parts?
Unlock the secrets of high-pressure aluminum die casting in this comprehensive guide. Explore their applications, benefits, and innovative processes that define this precision manufacturing technology.