Warmkammer-Druckgießen
Der Warmkammer-Druckguss ist ein Druckgussverfahren, das speziell für Metalle mit niedrigem Schmelzpunkt oder Nichteisenmetalle wie Zink, Magnesiumlegierungen usw. verwendet wird. Beim Warmkammer-Druckgussverfahren wird ein Teil der Druckgussmaschine beheizt, und das Gussmaterial wird in der Maschine vorgewärmt und dann durch Druck in die Form geleitet. Die Form wird dann schnell abgekühlt und erstarrt.
Der Vorteil des Warmkammer-Druckgusses besteht darin, dass er hochwertige und hochpräzise Teile mit hoher Produktivität herstellen kann. Da beim Warmkammerdruckguss eine vorgewärmte Metallflüssigkeit verwendet wird, können die Details der Form besser ausgefüllt werden, wodurch das Auftreten von Blasen und anderen Fehlern verringert wird.
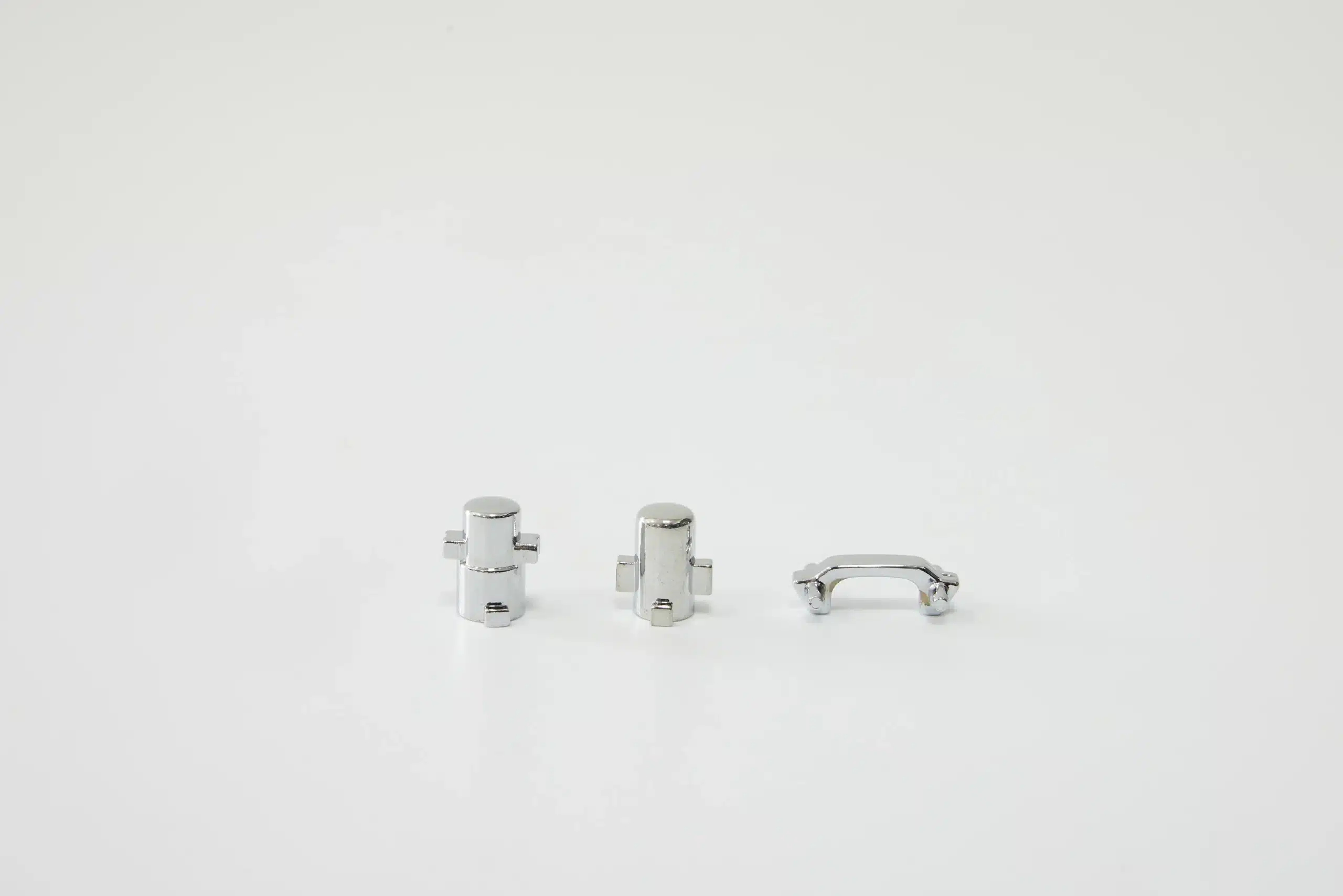
Was ist Warmkammer-Druckguss?
Der Warmkammerdruckguss ist ein weit verbreitetes Metallgussverfahren, das sich besonders für die Verarbeitung von Materialien mit niedrigem Schmelzpunkt wie Zink und Magnesium eignet. Der Warmkammerdruckguss ist ein Herstellungsverfahren, bei dem geschmolzenes Metall unter hohem Druck in eine Form gespritzt wird und dann schnell abkühlt und erstarrt, um präzise und komplexe Formen zu bilden. Bei dieser Technologie wird die besondere Konstruktion einer Warmkammer-Druckgießmaschine genutzt, die es ermöglicht, das Metall vor dem Einspritzen in die Form vorzuwärmen und eine präzise Füllung und Formgebung unter hohem Druck zu erreichen.
Verfahrensprinzip
Der Hauptbestandteil einer Warmkammer-Druckgießmaschine ist eine beheizte Druckgießkammer, die auch als "Warmkammer" bezeichnet wird. Diese Warmkammer wird auf der richtigen Temperatur gehalten, um das geschmolzene Metall aufzunehmen und zu halten. Wenn die Druckgießmaschine in Betrieb genommen wird, wird das geschmolzene Metall in die heiße Kammer eingespritzt und mit hohem Druck durch eine Düse oder ein Einspritzsystem in die Form gepresst. Die Form besteht in der Regel aus Stahl oder anderen hochtemperaturbeständigen Materialien und wird durch ein Kühlsystem schnell abgekühlt, um sicherzustellen, dass das Metall in der Form schnell erstarrt.
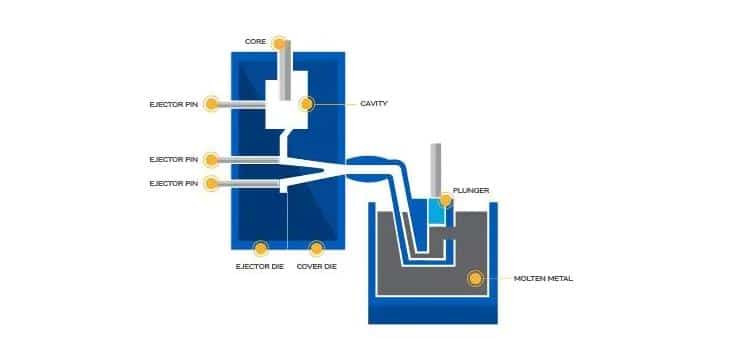
Kaltkammerdruckguss und Warmkammerdruckguss werden auf Materialien angewendet
Der Formkern besteht aus warmverformbarem Stahl wie SKD61, DAC, DH-31, 8407, 8418, H13, 3Cr2W8V, 4Cr5MoSiV, 1.2344, W302, etc.
Die meisten Formrahmen werden aus Stahlguss, Sphäroguss, Stahl mit mittlerem Kohlenstoffgehalt usw. hergestellt. Zum Beispiel QT550, QT600, S50C.
Das Warmkammer-Druckgussverfahren
Das Warmkammer-Druckgussverfahren ist ein komplexes und präzises Metallgussverfahren, bei dem geschmolzenes Metall in eine Form gespritzt wird, um präzise und komplexe Formen herzustellen. Durch ständige technologische Innovation und Verbesserung wird das Warmkammer-Druckgussverfahren weiterhin eine wichtige Rolle in der verarbeitenden Industrie spielen und die Entwicklung und den Fortschritt verwandter Branchen fördern. Im Folgenden wird das Warmkammer-Druckgussverfahren ausführlich vorgestellt:
- Vorbereiten der Form: Beim Warmkammer-Druckgussverfahren ist die Form von entscheidender Bedeutung. Die Formen werden aus hochtemperatur- und verschleißfesten Materialien wie Stahl, Kupfer oder Aluminiumlegierungen hergestellt. Konstruktion und Herstellung der Formen müssen bis auf den Mikrometer genau sein, um eine genaue Befüllung und Formgebung der Metallflüssigkeiten zu gewährleisten.
- (Besondere Erinnerung: Bei der Vorbereitung der Form müssen Sie sicherstellen, dass die Oberfläche der Form glatt ist und keine Mängel oder Risse aufweist. Außerdem müssen Sie prüfen, ob die Größe und Form der Form den Anforderungen des Produkts entspricht. Wenn es Probleme mit der Form gibt, muss sie repariert oder ersetzt werden. )
- Geschmolzenes Metall: Beim Warmkammer-Druckgussverfahren ist das flüssige Metall entscheidend. Das Metall wird über seinen Schmelzpunkt hinaus erhitzt, wodurch es schmelzflüssig wird. Dies kann mit Hilfe von Heizgeräten wie Induktionsspulen oder Widerstandsöfen erreicht werden. Während des Schmelzvorgangs müssen die Temperatur und die Zusammensetzung des Metalls konstant gehalten werden, um Qualitätsprobleme zu vermeiden.
- Einspritzen des Metalls: Wenn die Metallflüssigkeit fertig ist, wird sie durch die Düse oder das Einspritzsystem der Druckgussmaschine in die Form eingespritzt. Während des Einspritzvorgangs muss sichergestellt werden, dass die Metallflüssigkeit mit hohem Druck und hoher Geschwindigkeit in die Form eingespritzt wird, um eine genaue Füllung und Formung zu erreichen. Gleichzeitig müssen auch die Temperatur und die Fließgeschwindigkeit der Metallflüssigkeit kontrolliert werden, um Defekte oder Risse zu vermeiden.
- Abkühlung und Erstarrung: Wenn das flüssige Metall in die Form gespritzt wird, muss es abgekühlt und verfestigt werden. Dies geschieht durch Abkühlen der Form auf eine niedrigere Temperatur. Während des Abkühlungsprozesses müssen die Abkühlungsgeschwindigkeit und der Temperaturgradient kontrolliert werden, um thermische Spannungen oder Risse zu vermeiden. Gleichzeitig muss sichergestellt werden, dass das Metall vollständig erstarrt ist, um Defekte wie Schrumpfung oder Poren zu vermeiden.
- Entformung und Nachbearbeitung: Nachdem das Metall vollständig erstarrt ist, muss es entformt werden. Dazu wird die Form geöffnet und das Metallprodukt entnommen. Während des Entformungsvorgangs muss die Unversehrtheit der Metallprodukte sichergestellt und jegliche Beschädigung vermieden werden.
- Schließlich müssen die Metallerzeugnisse noch nachbearbeitet werden, z. B. durch Schleifen, Polieren, Lackieren usw. Diese Nachbearbeitungsschritte können die Qualität und das Aussehen Ihrer Metallprodukte weiter verbessern. Dies sind die Schritte für die Herstellung von Warmkammer-Druckgussprodukten der Mindwell Company.
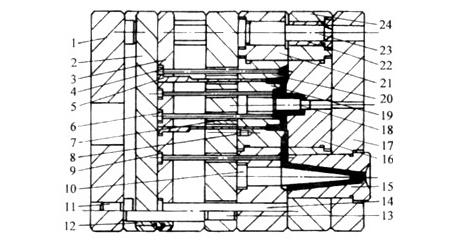
5 Vorteile des Warmkammer-Druckgusses
Warmkammerdruckguss ist ein Metallgussverfahren, das in verschiedenen Branchen weit verbreitet ist. Die Vorteile des Warmkammer-Druckgießens machen es zu einer der ersten Wahl in verschiedenen Branchen, insbesondere in den Bereichen Automobil, Elektronik, Luft- und Raumfahrt und anderen Bereichen. Im Zuge des technologischen Fortschritts und der Innovation wird das Warmkammer-Druckgussverfahren weiterhin eine wichtige Rolle spielen und die Entwicklung und den Fortschritt verwandter Branchen fördern. Zu seinen Vorteilen gehören die folgenden Aspekte:
- Hohe Produktionseffizienz: Beim Warmkammer-Druckguss wird das Stranggussverfahren angewandt, das eine effiziente Produktion ermöglicht. Beim Warmkammer-Druckgussverfahren wird geschmolzenes Metall durch eine Düse unter Druck in die Form gespritzt, wodurch die gewünschte Form entsteht, die dann schnell abkühlt und erstarrt. Da der gesamte Prozess eine kurze Zykluszeit hat und mehrere Gießvorgänge in kurzer Zeit abgeschlossen werden können, ist die Produktionseffizienz sehr hoch.
- Kosteneinsparungen: Das Warmkammer-Druckgussverfahren kann Rohstoffe und Energie einsparen, da für mehrere Gussteile nur ein Schmelzvorgang erforderlich ist, wodurch sich die Anzahl der Schmelz- und Gießvorgänge und damit die Kosten verringern. Außerdem kann das Warmkammer-Druckgussverfahren die Arbeitskosten durch die Automatisierung der Arbeitsabläufe senken.
Herstellung komplexer Teile: Mit dem Warmkammer-Druckgussverfahren können Teile mit komplexen Formen und Strukturen hergestellt werden, z. B. mit kleinen Löchern, Erhebungen und Vertiefungen. Dies macht das Warmkammer-Druckgussverfahren zu einem einzigartigen Vorteil bei der Herstellung bestimmter Präzisionsteile. - Optimiertes Design: Da mit dem Warmkammer-Druckgussverfahren komplexe Formen und Strukturen hergestellt werden können, können in der Entwurfsphase weitere Optimierungen vorgenommen werden, um die Leistung und die Qualität des Aussehens des Produkts zu verbessern.
- Umweltfreundlich und nachhaltig: Das Warmkammer-Druckgussverfahren kann die Erzeugung von Abfallstoffen reduzieren, da die Metallverwertungsrate hoch ist, was die Erzeugung von Schnitt-, Rest- und anderen Abfallstoffen reduziert. Darüber hinaus können im Warmkammer-Druckgussverfahren umweltfreundliche Energien und Materialien verwendet werden, wie z. B. die Nutzung erneuerbarer Energien und umweltfreundlicher Farben, wodurch die Auswirkungen auf die Umwelt verringert werden.
- Verbesserung der Produktqualität: Das Warmkammer-Druckgussverfahren kann das Auftreten von Gussfehlern wie Poren, Lunkern und anderen Problemen verringern. Da der gesamte Gießprozess in kurzer Zeit abgeschlossen werden kann, wird gleichzeitig die Verweildauer des Metalls bei hohen Temperaturen reduziert, wodurch die Möglichkeit der Oxidation und anderer chemischer Veränderungen verringert und die Qualität des Produkts verbessert wird.
Industrieanwendungen
Der Warmkammerdruckguss als effizientes Metallgussverfahren ist in vielen Branchen weit verbreitet. Von Automobilkomponenten bis hin zur Unterhaltungselektronik leistet der Warmkammerdruckguss einen wichtigen Beitrag zur Herstellung wichtiger Komponenten für diese Branchen.
- In der Automobilindustrie wird der Warmkammerdruckguss in großem Umfang zur Herstellung verschiedener Komponenten wie Motorteile, Fahrwerksteile, Bremssystemteile usw. verwendet.
- Auch im Bereich der Unterhaltungselektronik gibt es eine breite Palette von Anwendungen. So können beispielsweise Gehäuse, Tasten, Halterungen und andere Komponenten von Mobiltelefonen, Computern, Tablets und anderen Produkten im Warmkammer-Druckgussverfahren hergestellt werden.
- In der Luft- und Raumfahrt, zum Beispiel Teile von Flugzeugtriebwerken.
- Chirurgische Instrumente im Bereich der Medizintechnik.
- Baukonstruktionen im Bereich des Bauwesens, usw.
Diese Teile erfordern oft eine hohe Festigkeit, Korrosionsbeständigkeit und ein geringes Gewicht, und das Warmkammer-Druckgussverfahren erfüllt diese Anforderungen. Bei Mnwell werden die mit unseren Warmkammer-Druckgussmaschinen gegossenen Produkte in vielen Branchen eingesetzt. Dank seiner Vielseitigkeit kann das Verfahren an die Bedürfnisse verschiedener Branchen angepasst werden und leistet einen wichtigen Beitrag zur Herstellung wichtiger Komponenten.
Kaltkammer-Druckguss und Warmkammer-Druckguss
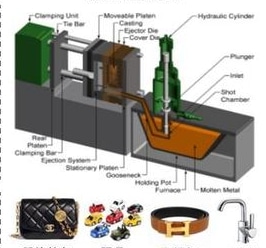
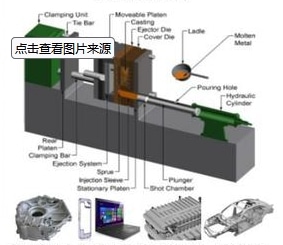
Kaltkammerdruckguss und Warmkammerdruckguss sind zwei verschiedene Druckgussverfahren, die sich in Bezug auf Anwendungsbereich, Materialauswahl, Produktionseffizienz und Umweltschutzanforderungen unterscheiden.
Wahl des Materials
Kaltkammerdruckguss eignet sich für Metalle mit hohem Schmelzpunkt, wie Kupfer, Aluminium, Zink usw. Aufgrund der höheren Schmelzpunkte dieser Metalle muss das Metall beim Kaltkammerdruckguss auf eine höhere Temperatur erhitzt werden, um es zu gießen. Folglich sind Kaltkammer-Druckgießanlagen in der Regel größer und benötigen mehr Energie zum Erhitzen. Das Warmkammer-Druckgussverfahren eignet sich für Metalle mit niedrigem Schmelzpunkt und Sondermetalle wie Magnesium und Titan. Diese Metalle haben einen niedrigen Schmelzpunkt, so dass sie ohne Heizvorrichtung gegossen werden können.
Umfang der Anwendung
Da beim Kaltkammerdruckguss die Metallflüssigkeit sorgfältiger verarbeitet wird, haben die gegossenen Teile im Allgemeinen eine höhere Festigkeit und Verschleißfestigkeit. Außerdem eignet sich der Kaltkammerdruckguss für die Herstellung großer oder komplexer Metallteile, da die Anlagen größeren Druck- und Temperaturschwankungen standhalten können.
Warmkammer-Druckgießanlagen sind relativ klein, und der Betrieb ist flexibler. Da die Metallflüssigkeit beim Warmkammerdruckguss eine höhere Temperatur hat, ist sie außerdem flüssiger und kann die Details der Form besser ausfüllen. Daher eignet sich das Warmkammer-Druckgussverfahren für die Herstellung von hochwertigen und hochpräzisen Teilen und für die Herstellung kleinerer und feiner Metallprodukte.
Anforderungen an die Umwelt
Was den Umweltschutz betrifft, so muss beim Kaltkammer-Druckguss die Anlage nicht beheizt werden, so dass der Energieverbrauch relativ gering, energiesparender und umweltfreundlicher ist. Beim Warmkammerdruckguss muss die Anlage vorgeheizt werden, und beim Produktionsprozess entstehen eine gewisse Menge an Abgasen und Rauch, so dass die Hersteller entsprechende Umweltschutzeinrichtungen einrichten müssen.
Zusammenfassend lässt sich sagen, dass das Kaltkammer- und das Warmkammer-Druckgussverfahren jeweils ihre Vorteile und ihren Anwendungsbereich haben. Bei der Wahl des am besten geeigneten Druckgussverfahrens müssen wir Faktoren wie Werkstoffe, Bauteilgröße, Produktionseffizienz und Produktionsumgebung berücksichtigen.
Kontaktieren Sie Mindwell, um kundenspezifische Warmkammer-Druckgussteile herzustellen
Was sind die Grenzen des Warmkammer-Druckgusses?
Zu den Einschränkungen des Warmkammer-Druckgusses gehören vor allem die folgenden Aspekte:
- Cost-effective only for high-volume production.
- High melting point metals cannot be used.
- High pressure range is required.
- Metals have low mobility, thus limiting product complexity.
- Heat treatment issues.
- Ejection marks and a small amount of burrs may remain on the mold separation line.
Which material is used in hot chamber die casting process?
In the hot chamber die-casting process, commonly used materials include non-ferrous metals and light metals such as aluminum alloy, zinc alloy, copper alloy, and magnesium alloy. These materials have the characteristics of low melting point, good fluidity, and easy processing, making them suitable for hot chamber die casting processes.
- Aluminum alloy has the advantages of low density, high specific strength, and good corrosion resistance, and is suitable for manufacturing lightweight and high-strength components;
- Zinc alloy has the characteristics of low melting point, good fluidity and easy processing, and is suitable for manufacturing small and thin-walled parts;
- Copper alloy has the advantages of good electrical conductivity, thermal conductivity, and corrosion resistance, and is suitable for manufacturing electrical components and wear-resistant parts.
During the hot chamber die-casting process, it is also necessary to select appropriate materials and alloy compositions based on the specific die-casting process and mold design requirements.
For parts requiring high strength and high toughness, materials such as aluminum alloy or zinc alloy can be selected; for parts requiring high electrical conductivity and high thermal conductivity, materials such as copper alloy can be selected.
At the same time, it is also necessary to select the appropriate alloy composition and melting process according to the mold design requirements to ensure the stability and reliability of the die casting. When selecting hot chamber die-casting materials, you need to consider the product’s usage requirements, processing performance, cost and other factors, as well as the specific die-casting process and mold design requirements, and select appropriate materials and alloy compositions.
Why is aluminum not good for hot chamber die casting?
The main reason why aluminum is not suitable for hot chamber die casting is its low melting point, only about 660°C, while the melting point of aluminum alloys is usually above 500°C. Due to its low melting point, aluminum needs to be heated to high temperatures to make it liquid, which is detrimental to the die-casting process.
Hot chamber die casting machines usually use metals such as zinc, tin, and lead as materials because these metals have relatively high melting points and can be die cast at lower temperatures. In addition, the hot chamber die casting process is usually used for die casting small castings, because large castings require higher pressure and longer cooling time, and the hot chamber die casting machine has limited pressure and cooling capabilities.
It should be noted that if aluminum or aluminum alloys are to be used for die casting, the cold chamber die casting process may be considered. Cold chamber die casting machines often use higher pressures and longer cooling times to produce high-quality aluminum parts.
Mindwell is a professional die cast manufacturer
Mindwell is a professional die-casting solution provider, providing hot chamber die casting and cold chamber die casting processes.
Mindwell has a professional technical team that provides customers with full-process services from product design, mold manufacturing to die casting production. At the same time, the company also pays attention to technological innovation and equipment maintenance to ensure that it provides customers with the highest quality products and services.


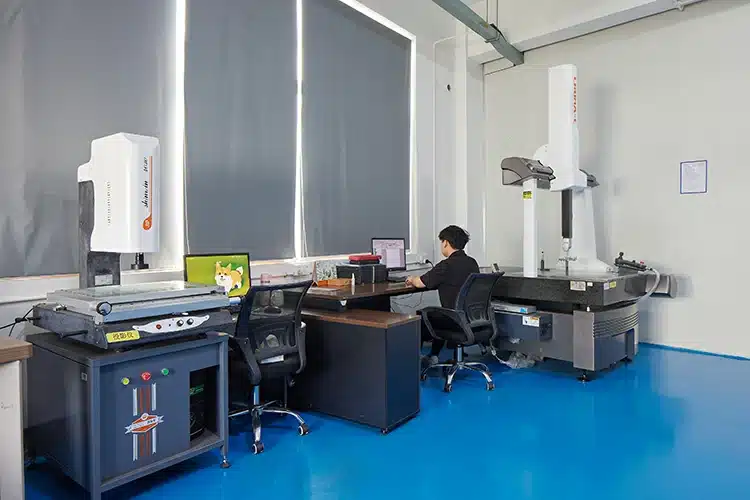