Alu Die Casting
In the world of manufacturing, aluminum die castings play an important role as the cornerstone of precision and durability. This comprehensive guide delves into the intricacies of aluminum die casting, detailing its applications, benefits, and transformative role in different industries.
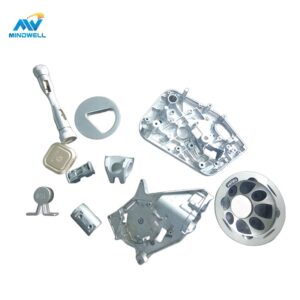
I. The Essence of Alu Die Casting
1.1 Understanding the Die Casting Process
Alu die casting is an advanced manufacturing technology that involves injecting molten aluminum into precision-crafted molds to create complex and dimensionally precise parts. This process requires highly specialized skills and advanced equipment to ensure the quality and precision of the final product.
The process of aluminum die casting includes the following steps:
- Mold Preparation: First, a precision mold needs to be designed and manufactured. This mold is usually made of high-hardness steel and can withstand high temperatures and pressures. The design of the mold needs to consider the shape, size and accuracy requirements of the product.
- Preparation of molten aluminum: Pure aluminum or aluminum alloy is heated to the melting point so that it becomes liquid. This process requires strict temperature control to ensure aluminum quality.
- Injection: Molten aluminum is injected into the mold at high pressure. This step requires precise control of the injection speed and pressure to ensure that the aluminum completely fills the mold and avoids bubbles or other defects.
- Cooling and Solidification: Once the aluminum is injected into the mold, the mold is quickly cooled, allowing the aluminum to solidify quickly. This step is crucial to ensure the strength and hardness of the product.
- Demolding and post-processing: When the aluminum is completely cured, the mold is opened and the product is removed. The product may then require some post-processing steps, such as deburring, polishing or heat treatment, to achieve final precision and surface quality.
The advantage of alu die-casting is its ability to produce parts with complex shapes and precise dimensions, and its production efficiency is high. In addition, due to aluminum’s light weight, electrical conductivity, and corrosion resistance, aluminum die castings find widespread use in multiple industries, such as automotive, aerospace, electronics, and lighting.
1.2 The Role of Aluminum in Die Casting
Die-cast aluminum was chosen for its superior properties, including high thermal conductivity, light weight, and versatility for complex designs. These properties make die-cast aluminum widely used in industries such as automotive, aerospace, electronics and lighting. These performance features are detailed below.
High thermal conductivity
The high thermal conductivity of die-cast aluminum is one of its important advantages. Aluminum is a good thermal conductive material with a high thermal conductivity. During the die-casting process, molten aluminum fills the mold and, after cooling and solidifying, forms a component with good thermal conductivity. This high thermal conductivity makes die-cast aluminum a significant advantage in scenarios where efficient heat dissipation is required. For example, in LED lamps, since the heat generated by the LED chip needs to be dissipated quickly to maintain stable performance and extend service life, the high thermal conductivity of die-cast aluminum has become an ideal choice for LED lamp manufacturing.
Lightness
The lightweight nature of die-cast aluminum is another important advantage. Aluminum is a relatively light metallic material with low density. During the die-casting process, aluminum fills the mold and solidifies, resulting in a part that has less weight. This lightweight nature makes die-cast aluminum a significant advantage in applications where weight reduction is required. For example, in automobile manufacturing, in order to improve fuel economy and reduce emissions, the overall weight of the vehicle needs to be reduced. The lightweight nature of die-cast aluminum allows it to be used to manufacture automotive parts, such as engine blocks, cylinder heads, etc., to reduce the overall weight of the vehicle.
Versatility in complex designs
The versatility of die-cast aluminum’s complex designs is its third important advantage. Through precise mold design and manufacturing processes, metal parts with complex shapes, clear outlines, thin walls and deep cavities can be manufactured. This sophisticated design capability allows die-cast aluminum to be highly flexible in the manufacturing process and can meet a variety of complex design needs. For example, in the aerospace field, parts with complex shapes and structures need to be manufactured, such as aircraft engine parts, spacecraft structural parts, etc. Die-cast aluminum’s sophisticated design capabilities allow it to meet these demands and produce high-quality, high-performance parts.
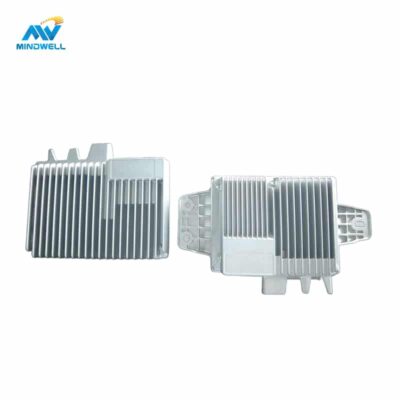
Inhaltsübersicht
II. Advantages Unveiled
2.1 Thermal Efficiency for Enhanced Performance
Aluminum has excellent heat dissipation capabilities, allowing it to quickly conduct heat away from the mold during the die casting process. This ability to dissipate heat is important to ensure that the die-cast part remains at an optimal temperature, as this reduces temperature differences within the product and avoids any potential problems due to overheating.
In many applications, especially those involving high-power electronic equipment or applications that require long-term operation, such as automotive engines, LED lighting fixtures, etc., the temperature control and heat dissipation capabilities within the product are critical to ensure optimal performance and reliability of the product. . If a component overheats, it can cause performance degradation, accelerated aging, or even failure.
However, by using alu die-casting technology, it is possible to create parts with efficient heat dissipation capabilities. This is because aluminum has a high thermal conductivity and is able to conduct heat quickly. During the die-casting process, molten aluminum fills the mold and rapidly cools and solidifies, forming parts with good thermal conductivity. This efficient heat dissipation helps extend the life of the product and improves its reliability and performance.
2.2 Lightweight Construction for Versatility
Aluminum’s lightweight nature not only makes it easy to work with, but also provides a variety of functional benefits, including energy efficiency, material savings, optimized design and environmentally friendly options. These advantages make aluminum an ideal material choice in a variety of applications, whether it is in the automotive, aerospace, electronics or lighting industries, where aluminum die castings are widely used to meet various needs. Here are some details on the versatility of aluminum lightweight construction:
- Energy efficiency: Aluminum’s lightweight nature means less energy is used during transportation. Whether transported by land or air, the lightweight nature of aluminum products can reduce transportation costs and thus reduce environmental impact.
- Material Savings: Due to the low density of aluminum, material can be saved during the manufacturing process. This not only reduces production costs, but also reduces resource waste and is in line with the principle of sustainable development.
- Optimized design: The lightweight properties of aluminum allow designers to design products more flexibly. They can focus more on product functionality and performance without worrying about excessive weight. This flexibility allows aluminum products to excel in a variety of applications.
Environmentally - Friendly Choice: Aluminum is a recyclable material, so it can be recycled and reused after use, reducing the impact on the environment. This recyclability makes aluminum an environmentally friendly choice that meets sustainability requirements.
2.3 Precision Engineering for Complex Designs
Die-casting technology can produce metal parts with complex shapes, clear outlines, thin walls and deep cavities, which are difficult to achieve by other manufacturing methods. The precision engineering capabilities of this complex design give die cast aluminum a significant advantage in meeting the changing needs of a variety of industries.
In certain industries, such as aerospace, automotive manufacturing, and electronic equipment manufacturing, the precision and complexity of components is critical. These industries need to manufacture parts with high precision, strength and complex shapes to meet specific performance requirements and safety standards.
Die-casting technology can achieve high-precision parts manufacturing through precise mold design and manufacturing processes. During the die-casting process, molten aluminum is poured into a mold and, after cooling and solidifying, forms parts of the desired shape and size. This precision manufacturing capability allows die-cast aluminum to meet the precision and complexity requirements of these industries.
In addition, die casting technology can also produce parts with thin walls and deep cavities that are difficult to achieve with other manufacturing methods. This thin-walled and deep-cavity design can provide better strength and stiffness while reducing the amount of material used, further reducing cost and resource consumption.
To sum up, die-casting technology can create complex and precise designs that meet the ever-changing needs of an industry that demands precision in every part. The precision engineering capabilities of this complex design have led to the widespread use of die-cast aluminum in aerospace, automotive manufacturing, electronic equipment manufacturing and other industries.
Customized alu die castings, Mindwell is your trusted choice
III. Applications Across Industries
3.1 Automotive Sector
Alu die castings are widely used in the automotive industry, covering many key areas such as engine systems, suspension systems and chassis, body structures, and electrical systems. They provide lightweight, high-strength and corrosion-resistant parts for vehicles, improving their fuel economy, performance and reliability. The following is the detailed application range of aluminum die castings in the automotive industry:
- Engine System: Alu die castings play an important role in engine systems. They can be used to make critical components such as engine blocks, cylinder heads and crankcases. These components need to withstand high temperatures, pressures and high-speed movements, and therefore require high strength and corrosion resistance. Aluminum die castings are ideal for manufacturing these parts due to their excellent mechanical properties and corrosion resistance.
- Suspension system and chassis: Aluminum die castings are also widely used in suspension systems and chassis. They can be used to manufacture various components in suspension systems, such as suspension arms, control arms and steering knuckles. These components are required to withstand complex forces and movements and therefore require high strength and stiffness. Aluminum die castings are ideal for manufacturing these parts due to their lightweight nature and excellent mechanical properties.
- Body structure: Alu die castings are also used to manufacture various components in the body structure, such as doors, hoods, body frames, etc. These components need to be lightweight, strong and corrosion-resistant to provide better fuel economy and safety. Aluminum die castings are ideal for manufacturing these parts due to their lightweight nature and excellent mechanical properties.
- Electrical system: Alu die castings are also used to manufacture various components in electrical systems, such as battery boxes, motor housings, etc. These components need to be lightweight, high-strength and corrosion-resistant to provide better electrical performance and reliability. Alu die castings are ideal for manufacturing these parts due to their lightweight nature and excellent mechanical properties.
3.2 Electronics and Technology
Alu die castings are also widely used in electronic equipment, mainly involving casing and chassis manufacturing, radiator manufacturing, and antenna manufacturing. They provide lightweight, high-strength and corrosion-resistant parts for electronic equipment, improving the performance and reliability of the equipment, mainly involving the following aspects:
- Housing and chassis manufacturing: Aluminum die castings are often used to manufacture housings and chassis for electronic equipment. These components need to be lightweight, high-strength and corrosion-resistant to provide better protection and stability. Aluminum die castings are ideal for manufacturing these parts due to their excellent mechanical properties and corrosion resistance.
- Radiator manufacturing: Electronic equipment generates a lot of heat when working, so heat dissipation is an important issue. Aluminum die castings have excellent thermal conductivity and can quickly conduct and dissipate heat, helping to keep the temperature of the equipment within a safe range. Therefore, aluminum die castings are also often used to manufacture heat sinks for electronic equipment.
- Antenna manufacturing: Antennas in electronic devices also need to be lightweight, high-strength and corrosion-resistant. Aluminum die castings are ideal for manufacturing these parts due to their excellent mechanical properties and corrosion resistance.
3.3 Consumer Goods
Aluminum die castings are widely used in consumer products, from kitchen appliances to handheld devices, and their versatility ensures seamless integration of components in a variety of consumer products. Here are some applications of aluminum die castings in consumer products:
- Kitchen utensils: Aluminum die castings are widely used in kitchen utensils, such as pressure cookers, steamers, ovens, etc. These appliances need to withstand high temperatures and pressures, so they need to have high strength and corrosion resistance. Aluminum die castings are ideal for manufacturing these appliances due to their excellent mechanical properties and corrosion resistance. In addition, aluminum die castings are also used to manufacture components such as kitchen faucets and water pipes, which need to have good corrosion resistance and environmental protection.
- Handheld devices: Aluminum die castings are also widely used in handheld devices, such as mobile phones, tablets, digital cameras, etc. These devices require lightweight, high strength and corrosion resistance to provide a better operating experience and reliability. Aluminum die castings are ideal for manufacturing the housings of these devices due to their light weight and excellent mechanical properties. At the same time, aluminum die castings are also used to manufacture internal mechanical components, such as camera brackets, buttons, etc.
- Personal care products: Aluminum die castings are also widely used in personal care products, such as electric toothbrushes, razors, etc. These products require lightweight, high strength and corrosion resistance to provide a better user experience and reliability. Aluminum die castings are ideal for manufacturing the housings of these products due to their light weight and excellent mechanical properties.
- Sports equipment: Aluminum die castings are also widely used in sports equipment, such as bicycles, scooters, etc. These equipment require lightweight, high strength and corrosion resistance to provide better performance and user experience. Aluminum die castings are ideal for manufacturing frames and components for these equipment due to their light weight and excellent mechanical properties.
IV. The Production Journey
4.1 Mold Creation and Injection
The die-casting process begins with the creation of a mold, followed by a precise injection of molten aluminum to form components with unmatched precision. Here is a detailed introduction to mold creation and injection:
Tool creation
- Design stage: First, based on product requirements and design requirements, the designer will create a 3D model. This model will determine the product’s shape, size and all details.
- Mold manufacturing: Next, high-quality mold steel materials are used to manufacture the mold based on the 3D model. Molds usually consist of two main parts: upper mold and lower mold. The upper mold is used to form the external shape of the product, while the lower mold is used to form the internal shape of the product.
- Mold trial stage: Before formal production, a trial mold is usually conducted. At this stage, the mold is checked for accuracy, flowability, and other key parameters. If any problems are discovered, the mold can be adjusted and repaired in time.
injection stage
- Molten Aluminum Preparation: Put the aluminum block into the smelting furnace and heat it to the melting point, then convert it into molten aluminum. This process requires precise control of temperature and time to ensure the quality of the molten aluminum.
- Injection process: When the molten aluminum is ready, it is injected into the mold through the pipe. During this process, the injection speed, pressure and temperature need to be precisely controlled to ensure that the aluminum liquid can evenly fill all parts of the mold.
- Cooling and demolding: After the molten aluminum has cooled and solidified in the mold, the demolding operation can be performed. This process is required to ensure product integrity and avoid any possible damage.
- Post-processing: After demoulding, the product may need some post-processing, such as grinding, polishing, etc., to obtain the desired appearance.
Throughout the process, precision and quality control are crucial. Through precise mold design and manufacturing, along with precise injection processes, die castings can be manufactured with unparalleled precision. These parts often offer high strength, corrosion resistance and good thermal conductivity, making them ideal for a variety of applications.
4.2 Precision Machining and Finishing
Die-cast components often require further processing to ensure they meet precise specifications and to enhance their durability and aesthetics. The following is a detailed introduction to precision machining and finishing:
Feinmechanische Bearbeitung
Rough machining: After the die casting is complete, the part may need to be rough machined. This basically involves removing excess material to achieve the desired shape and size. Rough machining can include operations such as cutting, drilling, milling, etc.
Finishing: Compared to roughing, finishing is more detail-oriented and precise. This may include operations such as grinding, polishing, fine milling, etc., to further refine the surface of the part and ensure that its shape and size exactly match the design requirements.
The significance of finishing
Finishing not only increases the accuracy of the part, but also enhances its aesthetics and durability. For example, by polishing or grinding, defects on the surface of a part can be removed, making its surface smoother, thus improving its wear and corrosion resistance. At the same time, finishing can also improve the appearance quality of the parts, making them more beautiful.
Finishing techniques
In order to achieve precision machining, advanced processing equipment and processes are required. For example, CNC machine tools, grinding machines, polishing machines, etc. are all commonly used finishing equipment. In addition, in order to ensure machining accuracy, high-precision tools and fixtures are also required.
Schlussfolgerung
Precision machining and finishing are important steps after die casting to ensure the accuracy, aesthetics and durability of the part. Through the use of advanced equipment and processes, high-precision parts manufacturing can be achieved to meet the needs of various applications.
V. Quality Assurance Measures
5.1 Non-Destructive Testing
Non-Destructive Testing (NDT for short) is a method that uses sound, light, magnetism, electricity and other characteristics to detect whether there are defects or unevenness in the object without damaging the performance of the object. , a general term for all technical means that provide information on the size, location, nature and quantity of defects, and then determine the technical status of the inspected object (such as qualified or not, remaining life, etc.).
At Mindwell Company, we use non-destructive testing for every die-cast component. The following is a detailed introduction to non-destructive testing:
Purpose of non-destructive testing: The main purpose of non-destructive testing is to detect internal and surface defects in die-cast components without damaging or changing them. These defects may be cracks, pores, inclusions, etc., which can affect the performance and service life of the component.
Commonly used non-destructive testing methods: In the die-casting industry, common non-destructive testing methods include ultrasonic testing (UT), radiographic testing (RT), magnetic particle testing (MT) and penetrant testing (PT). Each method has its specific application scope and advantages and disadvantages.
Ultrasonic testing (UT): Utilizes the propagation characteristics of ultrasonic waves in materials to detect defects. This method can detect defects such as cracks and pores inside die-cast parts.
Radiographic Inspection (RT): Uses X-rays or gamma rays to penetrate die-cast parts and identify defects by detecting transmitted or scattered rays. This method is suitable for detecting defects such as inclusions and shrinkage cavities inside castings.
Magnetic Particle Inspection (MT): This is done by applying a magnetic field to the surface of a die-cast part and using magnetic particles to reveal defects. This method is suitable for detecting surface or near-surface defects such as cracks.
Penetrant Testing (PT): Using a penetrant to penetrate into defects on the surface of the die-cast part, and then using a developer to draw the penetrant out and reveal the defects. This method is suitable for detecting defects with surface openings.
Advantages of non-destructive testing: Non-destructive testing methods offer the following advantages:
Non-destructive: Testing can be carried out without damaging or changing die-cast parts, avoiding the waste and cost of traditional destructive testing.
High Accuracy: Modern non-destructive testing technology has extremely high accuracy and resolution and can accurately identify minute defects.
Comprehensiveness: Die-cast parts can be fully inspected, including internal and external defects, to ensure the overall quality of the product.
Applications of non-destructive testing: At Mindwell we mainly use it in the following aspects:
- Quality Control: During the production process, die-cast parts are inspected non-destructively to ensure they meet quality standards.
- Product Acceptance: Before product delivery, die-cast parts are subjected to final non-destructive testing to confirm that they meet customer needs and specifications.
- Failure analysis: When a die-cast part fails, non-destructive testing technology can be used to analyze the cause and nature of the failure.
In short, non-destructive testing is one of the important means to ensure the quality of die-cast components. By employing appropriate non-destructive testing methods and techniques, our company can accurately detect defects in die-cast parts, ensuring that each component meets the highest quality standards.
5.2 Dimensional Inspections
Mindwell’s dimensional inspection of die castings is a very important quality control step. Dimensional inspection can verify whether the die casting meets the design requirements and ensure its dimensional accuracy and consistency.
When performing dimensional inspection, measuring tools such as calipers, micrometers, measuring instruments, etc. are usually used to accurately measure various dimensions of die castings. These measurements are compared to the values specified on the design drawing to determine if the die cast meets specifications.
The purpose of dimensional inspection is to ensure the dimensional consistency and accuracy of die castings. If there are dimensional deviations in a die cast part, it can cause assembly issues, performance issues, or quality issues. Therefore, these problems can be discovered and corrected in time through dimensional inspection, ensuring reliable and consistent quality of die castings.
In order to improve the accuracy and efficiency of dimensional inspection, Mindwell may use advanced measuring equipment and measurement technology. These equipment and technologies can provide high-precision measurement results, reduce human errors, and improve detection efficiency.
In short, Mindwell’s dimensional inspection of die castings is one of the important means to ensure product quality. Through strict dimensional inspection, you can ensure that die castings meet design requirements, improve product reliability and consistency, and thus meet customer needs and specifications.
VI. Customization in Alu Die Casting
6.1 Tailoring Solutions for Varied Industries
Mindwell’s ability to tailor solutions for various industries is one of its core competencies. Through an in-depth understanding of industry needs, custom design, manufacturing capabilities and continuous optimization, Mindwell is able to provide customers with high-quality, high-performance custom die-cast parts that meet the specific needs of specific industries. . The ability to customize die-cast parts allows manufacturers to meet the specific needs of specific industries, ensuring a tailor-made solution.
The following is a detailed introduction to Mindwell’s customized solutions for various industries:
- Deep understanding of industry needs: Mindwell works closely with various industries to gain a deep understanding of their needs and challenges. This includes knowledge of industry standards, regulatory requirements, performance requirements and more. By working closely with customers, Mindwell is able to accurately grasp industry needs and trends.
- Customized design: Based on an in-depth understanding of industry needs, Mindwell is able to provide customers with customized design solutions. This includes customization of die-cast parts in terms of shape, size, material selection, surface treatment, and more. By working with the client’s design team, Mindwell is able to ensure that the design meets the client’s specific needs.
- Manufacturing capabilities: Mindwell has advanced die-casting equipment and manufacturing technology to ensure the manufacturing of high-quality custom die-cast parts. During the manufacturing process, Mindwell strictly controls every aspect, including mold design, raw material selection, smelting, die-casting, post-processing, etc., to ensure high precision and high quality of parts.
- Continuous optimization: During the customization process, Mindwell maintains close communication with customers and provides timely feedback and adjustments to the design plan. Through continuous optimization, Mindwell is able to ensure that customized die-cast parts meet customer expectations and requirements, and to continuously improve product performance and reliability.
- Providing a full range of services: In addition to customizing die-cast parts, Mindwell also provides customers with a full range of services, including product testing, quality assurance, technical support, etc. These services ensure customers receive optimal performance, reliability and reduced operating costs when using custom die-cast parts.
6.2 Impact on Design and Functionality
Customization has a positive impact on the design and functionality of die-cast products. It not only meets specific functional requirements, but also improves design aesthetics and personalized touch, bringing higher added value and market competitiveness to die-cast products.
- Meet functional requirements: The primary purpose of customization is to meet specific functional requirements. Different industries and application scenarios have different functional requirements for die castings. Through customization, you can ensure that die castings fully meet specific functional requirements in terms of shape, size, strength, wear resistance, etc. This precise matching ensures that the die cast parts will perform optimally in the actual application.
- Improvement of design aesthetics: Customization not only focuses on functional requirements, but also on design aesthetics. The look and feel of die-cast products is an important part of the user experience. Through customization, designers can get creative with shapes, lines, finishes, and more to create a unique and attractive look. This not only improves the visual beauty of the product, but also increases user recognition and satisfaction.
- Personalized touch: Customization provides a personalized touch to die-cast products. Through different surface treatment processes, such as polishing, sandblasting, electroplating, etc., die castings can be given different textures and touches. This personalized touch not only adds to the uniqueness of the product, but also enhances the user experience.
- Space for innovation: Customization provides designers with greater space for innovation. On the basis of meeting functional requirements, designers can try new design elements and creative concepts to create unique die-cast products. This kind of innovation can not only meet the diverse needs of the market, but also help enhance brand image and product competitiveness.
- Flexible adjustment and optimization: During the customization process, designers can flexibly adjust and optimize based on customer feedback and market demand. This flexibility ensures that the product can closely match actual usage scenarios and user needs, improving product practicality and satisfaction.
VII. Sustainability Initiatives
7.1 Material Efficiency and Waste Reduction
Alu die-casting is a manufacturing process whose sustainability is primarily in terms of material efficiency and waste reduction. Here is a detailed introduction to these two aspects:
Material efficiency:
Optimized design: Through accurate design and engineering analysis, materials can be maximized and waste reduced. For example, optimizing the design of die-casting parts to make them more in line with the characteristics of the die-casting process, thereby reducing material use and energy consumption during the production process.
Recycling and reuse: For die castings that have been used, the consumption of new materials can be reduced through recycling and reuse. For example, scrap aluminum die castings are recycled and reused to produce new die castings after processing.
Use high-strength materials: Using high-strength, lightweight materials can reduce the amount of material used in the manufacturing process while improving the strength and durability of your product.
Waste reduction:
Reduce scrap rate: By optimizing the production process and using advanced mold technology, the scrap rate generated during the production process can be reduced. This not only reduces waste but also reduces production costs.
Environmentally friendly manufacturing processes: The impact on the environment can be reduced by adopting environmentally friendly manufacturing processes, such as using environmentally friendly coatings and additives, and using energy-efficient equipment.
Properly arrange the production plan: By properly arranging the production plan, overproduction and inventory backlog can be avoided, thus reducing waste and storage costs.
Waste recycling: Waste generated during the production process can be processed through recycling. For example, scrap aluminum die castings are recycled, processed and reused to produce new die castings.
Through the above measures, the aluminum die-casting process can reduce the impact on the environment while improving manufacturing efficiency. This sustainable manufacturing process helps drive the development of green manufacturing and a circular economy.
7.2 Recycling Possibilities
The recyclability of aluminum die-casting is an important part of its sustainability and is in line with sustainability goals. Here’s a closer look at the recycling possibilities for aluminum die casting:
Recyclability of Aluminum:
Aluminum is a very recyclable material. It has the characteristics of corrosion resistance, easy processing and wide application, so it is widely used in many fields, including construction, automobile, electronics, etc. Recycling of aluminum can reduce reliance on natural resources, lower production costs, and reduce environmental impact.
Recyclability of die-casting parts:
- Recycling of waste die-casting parts: Wasted aluminum die-casting parts can be disposed of through recycling and reuse. The recycling process involves steps such as crushing, screening, and smelting die castings, which are then reused to make new die castings. Not only does this reduce the need for raw materials, it also reduces production costs.
- Recycling of die-casting molds: In the die-casting process, the mold is an important consumable. Used molds can also be recycled and reused. The recycled molds are repaired and reprocessed and can be reused to produce new die-cast parts.
Opportunities to practice environmentally friendly practices:
- Promote the circular economy: Through the recycling and reuse of aluminum die-casting, we can promote the development of the circular economy. Circular economy emphasizes the effective use of resources and the reduction and recycling of waste. The recycling and reuse of aluminum die-casting is in line with this concept.
- Reduce carbon emissions: The recycling and reuse of aluminum die castings can reduce the need for raw materials, thus reducing carbon emissions during the production process. This has important implications for combating climate change and achieving the Sustainable Development Goals.
- Improve resource efficiency: Through the recycling and reuse of aluminum die-casting, the efficiency of resource utilization can be improved and the consumption of natural resources can be reduced. This plays a positive role in protecting the environment and promoting sustainable development.
In conclusion, the recyclability of alu die-casting provides opportunities for its sustainability. Recycling and reusing used die-casting parts and molds can reduce the need for raw materials, reduce production costs, and reduce environmental impact. This is in line with sustainable development goals and provides opportunities for environmentally friendly practices in the die casting sector.
In conclusion
In conclusion, this guide sheds light on the multifaceted world of aluminum die casting. From precision engineering to multifunctional applications and sustainability initiatives, aluminum die casting continues to shape the industry and pave the way for a future of innovation and efficiency. Mindwell has also been committed to promoting the development of industrial manufacturing along the way. We have more than ten years of experience in the aluminum die-casting industry, and we hope to continue to contribute to the aluminum die-casting industry.
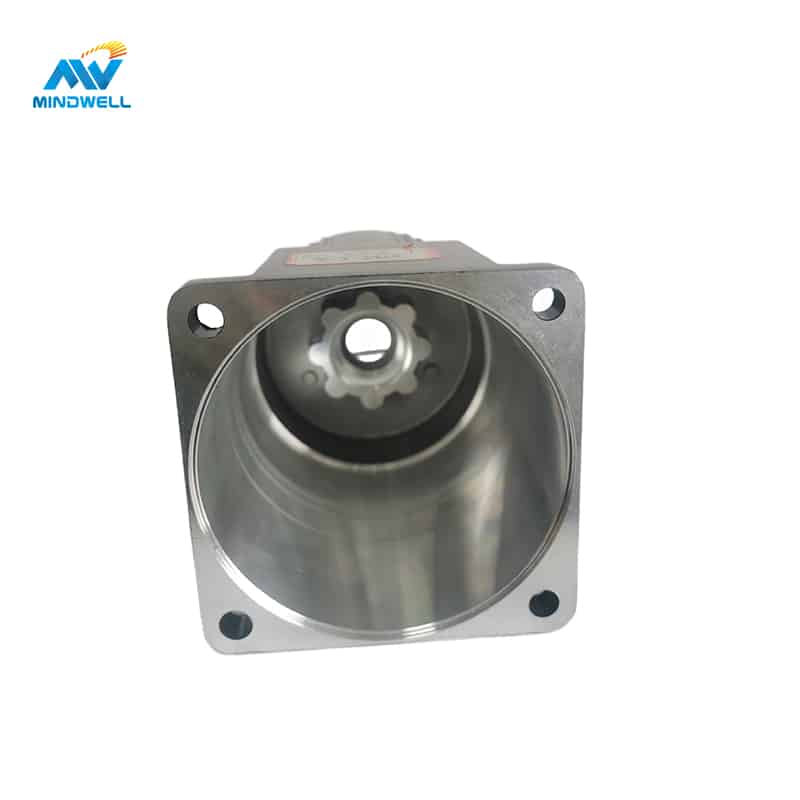
Are alu die castings suitable for all industries?
Aluminum alloy die castings are widely used in many industries due to their lightweight, high strength, corrosion resistance and other properties. For example:
- Automotive industry: Aluminum alloy die castings are used to manufacture automobile engines, chassis, bodies and other components. They have the advantages of lightweight, improved fuel economy, and reduced emissions.
- Electronics industry: Aluminum alloy die castings are used to manufacture housings, radiators, connectors, etc. for electronic equipment and have excellent electrical conductivity and heat dissipation properties.
- Consumer goods industry: Aluminum alloy die-casting parts are used to manufacture shells and structural parts of consumer goods such as household appliances, toys, and fitness equipment. They are beautiful, durable, and environmentally friendly.
Therefore, it can be said that aluminum alloy die castings are suitable for all industries that require lightweight, high strength, corrosion resistance and other properties.
How does aluminum contribute to the sustainability of die casting?
As a recyclable material, aluminum has the following advantages in the die-casting process, helping to achieve sustainable manufacturing:
- Recyclability: Aluminum is a recyclable material that can be used over and over again, reducing the need for raw materials. By recycling and reusing scrap aluminum die castings, production costs can be reduced and the impact on the environment can be reduced.
- Energy saving and emission reduction: Aluminum has a low density and requires relatively little energy during the die-casting process. In addition, aluminum has good thermal conductivity, which helps to quickly cool molds and parts, shorten production cycles, and reduce energy consumption.
- Environmental protection: Waste gas, waste water, waste residue and other waste generated during the aluminum die-casting process can be recycled and reused through effective treatment measures to reduce the impact on the environment.
Aluminum therefore has significant advantages in promoting the sustainability of die casting.
Can die cast parts be customized for specific applications?
Yes, die cast parts can be customized for specific applications. By changing the design and manufacturing process of the mold, die castings of different shapes, sizes and properties can be produced. In addition, the strength, hardness, corrosion resistance and other properties of die castings can be improved by changing the material composition and adding alloy elements to meet the requirements of specific applications.
What measures are taken to ensure the quality of die castings?
In order to ensure the quality of die castings, the following measures can be taken:
- Strict quality control: Establish a complete quality control system to strictly monitor and test all aspects of the die-casting process to ensure that product quality meets standards.
- Non-destructive testing: Use non-destructive testing technology to conduct comprehensive testing of die-casting parts, including appearance, size, internal structure, etc., to ensure that the product is free of defects and defects.
- Mold design and manufacturing: The design and manufacturing quality of the mold directly affect the quality of die castings. Therefore, it is necessary to adopt advanced mold design and manufacturing technology to ensure the accuracy and stability of the mold.
- Raw material control: Strictly control the quality and composition of raw materials to ensure that they meet standard requirements.
- Production process control: Optimize production process parameters to ensure that parameters such as temperature, pressure, and time during the production process meet standard requirements.
- Employee training: Strengthen employees’ quality awareness and skills training, and improve employees’ understanding of product quality and operating skills.
Through the comprehensive application of the above measures, the quality of die castings can be effectively guaranteed.