Precision aluminum die-casting is a process technology for manufacturing aluminum products. It uses a mold to pour high-temperature molten aluminum alloy liquid into a die-casting machine, and forms a metal product under pressure. Precision aluminum die castings have the characteristics of high precision, smooth surface, complex structure, energy saving and environmental protection, and a wide range of uses. They are widely used in automobiles, electronics, aviation, aerospace, military and other fields.
The main advantages of precision aluminum die-casting include high complexity and precision. Improving the precision of aluminum die-casting parts requires a comprehensive consideration of multiple factors such as materials, design, process control, and quality management. Through continuous improvement of these aspects, highly precise and consistent aluminum die cast parts can be produced.
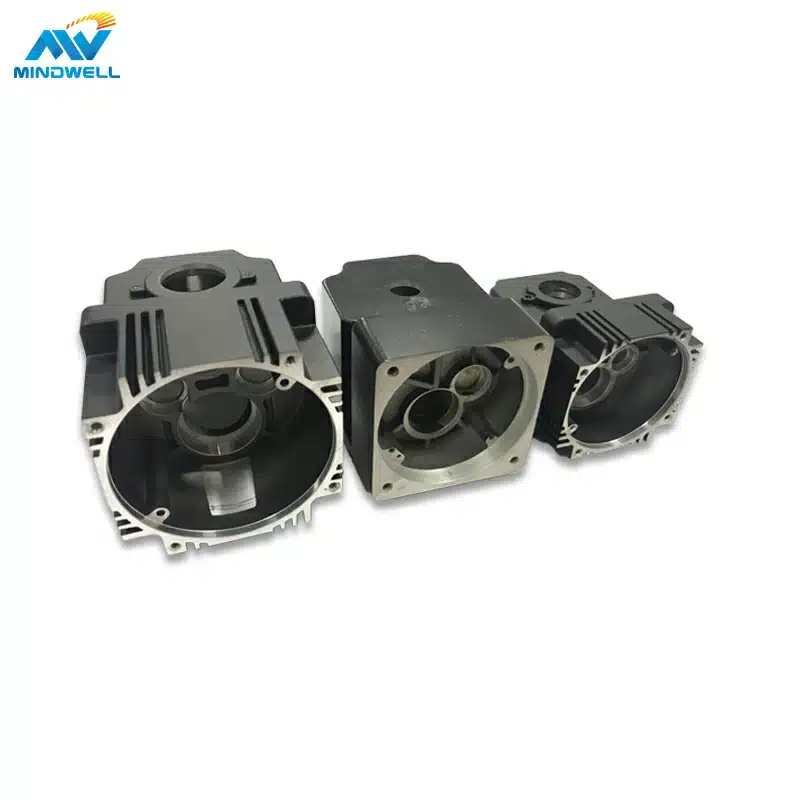
Mold Design and Manufacturing
Mold design and manufacturing play a vital role in improving the precision of aluminum die-casting parts. The higher the precision of the mold, the higher the precision of the produced aluminum die-casting parts. The following points can improve the precision of mold design and manufacturing.
- The use of CAD/CAM software: High-precision CAD/CAM software is a key tool for designing and manufacturing precision molds. These software allow engineers to create complex mold geometries and ensure their accuracy. Additionally, CAD/CAM software can also be used to simulate the injection and solidification process of the mold to help predict potential problems and make improvements.
- Selection of Mold Material: It is crucial to choose the appropriate mold material. Tool steel or cemented carbide are usually used to make molds because of their high hardness and wear resistance, which are very important for long-term use. The choice of mold material should also consider the working temperature and mold life.
- Temperature control system: The temperature control system of the mold is very important, because it will affect the fluidity and solidification speed of aluminum alloy. Uniform temperature distribution helps reduce internal stress and shrinkage cavities, and increases part precision. High-quality temperature control systems can be achieved with cooling channels and heating elements.
- Mold manufacturing process: Manufacturing high-quality molds requires high-precision craftsmanship. This includes the use of CNC machine tools, electrical discharge cutting, wire cutting and other processes to ensure the precision and surface quality of the mold.
- Mold Maintenance: Regular maintenance and care of molds is key to ensuring their performance and longevity. This includes cleaning, lubricating, checking for damaged parts and repairing or replacing them promptly.
- Mold trial and adjustment: It is very important to conduct mold trial and adjustment before formal production. This can help identify and resolve potential issues and ensure parts meet precision and quality requirements.
- Training of mold technicians: Our company’s mold operation and maintenance personnel have received appropriate training and have many years of experience in mold design and assembly, so they can operate and maintain molds correctly.
The precision and consistency of aluminum die-casting parts can be improved by carefully designing and manufacturing molds to ensure precise geometry and dimensions of the parts and reduce variability in manufacturing.
Diseño de productos
Good design minimizes defects during pressure, filling and cooling, improving the dimensional accuracy and surface finish of the part. The design should take into account the part’s structure, wall thickness, holes and protrusions and other characteristics.

Material Selection
Choosing the right aluminum material is critical to the precision and performance of piezas de fundición de aluminio. How do we choose raw materials in the production of precision aluminum die casting, mainly as follows:
- Performance requirements: According to the application of different aluminum die casting parts, the performance requirements of the parts need to be clearly defined. In aluminum die casting, the strength, hardness, corrosion resistance, thermal conductivity, and electrical conductivity of the material need to be considered the most. Different aluminum alloy materials have different performance characteristics, so the selected material should be optimized according to specific requirements.
- Quality Control: In order to ensure the consistency of the material, stringent quality control measures are required. This includes purchasing qualified raw materials from reliable suppliers, performing compositional analysis to ensure alloy compositions meet requirements, and monitoring the mechanical properties of the material. Our company has many years of experience in aluminum die-casting, and quality control has always been one of the procedures that our company attaches great importance to.
- Design Flexibility: Depending on the application, minor adjustments to the specific alloy composition may be required to meet performance requirements. This can be achieved by addition of specific alloying elements or heat treatment.
- Corrosion resistance: If the part will be used in a corrosive environment, an aluminum alloy with good corrosion resistance needs to be selected. This may require the aluminum alloy to be subjected to surface treatments such as anodizing or plating to improve its corrosion resistance.
- Thermal and electrical conductivity: If a part needs to have good thermal or electrical conductivity, it is necessary to select an aluminum alloy suitable for these properties. Aluminum alloys generally have good thermal conductivity, but the specific alloy and treatment may affect these properties.
process control
Optimization of the melting and casting process:
- Temperature Control: To ensure that the melting point of the alloy and the pouring temperature are precisely controlled. Use advanced melting equipment, such as induction heating furnaces, to ensure temperature consistency and stability.
- Pressure Control: Appropriate pressure is applied to force the molten cast alloy to fill the mold. Make sure the pressure is neither too high nor too low to avoid deformation or defects.
- Flow control: Ensure that the flow of the molten cast alloy in the mold is uniform by designing the appropriate gate and gating system. Simulation and computational fluid dynamics to optimize flow paths.
- Pouring Speed Control: Control the pouring speed of molten cast alloys to avoid air pockets, hot cracks and surface defects.
High performance injection equipment and automation control system:
High-performance injection machine: To produce precision aluminum die-casting parts, it is necessary to be equipped with advanced die-casting machine, which can provide precise pressure and flow control to ensure that the alloy is filled in the mold and reaches the desired shape.
Automated Control System: Use a PLC (programmable logic controller) or similar control system to monitor and adjust key parameters such as temperature, pressure and pouring speed. This helps to maintain consistent process conditions and reduce human error.
Data Monitoring & Analysis:
Integrated data monitoring system, capable of real-time monitoring of process parameters, including temperature, pressure and flow. This helps to detect anomalies in a timely manner and take corrective actions.
Use data analysis tools, such as statistical process control (SPC), to analyze historical data and identify potential trends and issues. This facilitates process improvements and preventative measures.
By implementing these methods of process control, greater precision and consistency can be achieved in the aluminum die casting process, ensuring that the parts produced are of high quality standards. Continuous monitoring, analysis, and improvement will help maximize production efficiency and reduce variability in manufacturing.

Cooling and solidification:
- The control of the cooling rate is a key factor to ensure the precision of the part. Excessive or uneven cooling may result in stress concentrations and deformation.
- The design and placement of cooling channels can be optimized for specific part geometries to ensure even cooling.
- Coolant selection and maintenance are very important in maintaining proper process temperatures.
Post-processing procedure:
- Machining, grinding, and polishing require the use of high-precision equipment to ensure the surface finish and dimensional accuracy of the parts.
- Surface treatment processes, such as painting, anodizing, and plating, can improve the corrosion resistance and decorative properties of parts.
- Use high-precision measurement tools, such as 3D scanning and optical measurement, to detect and correct the precision and surface quality of the parts.
Quality Control and Testing:
- Quality control is the most important in precision die casting, implementing strict quality control procedures covering every manufacturing stage from raw materials to final products can ensure that aluminum die casting parts meet precision usage specifications.
- Quality inspection includes checking the size of the part, surface quality, internal defects, etc. Advanced non-destructive testing technologies such as X-ray testing, CT scanning and ultrasonic testing can be used to check internal defects of parts, correct molds in time, and adjust directions in time.
- The QC department will formulate a suitable inspection plan according to the progress of production, including sampling inspection and comprehensive inspection, so as to meet the quality requirements.
Training and Experience:
Die casting technicians are key to ensuring the process is executed correctly. Operators and technicians need to understand the operation and maintenance of equipment and have extensive experience in die casting, so as to be able to ensure that there will be no problems during operation.
Ongoing training helps workers keep up with the latest technology and best practices, improving their skill level and ensuring process stability and consistency.
crafts improvement:
Ongoing process improvement can be achieved by collecting and analyzing production data on a regular basis. This helps to identify potential issues and take corrective action to improve part precision.
Use quality tools and methodologies, such as Six Sigma and SPC (Statistical Process Control), to improve process stability and controllability.
Mold maintenance:
Regular maintenance and maintenance of molds can prolong their service life and ensure the stability of their performance.
Damage or wear of mold parts should be repaired or replaced in time to avoid affecting the precision and quality of the parts.
Taking these elements together and integrating them into the aluminum die casting manufacturing process will help improve the precision and consistency of your parts, ensuring that your product meets specifications and quality requirements.
To improve the accuracy of aluminum die casting parts, multiple factors such as materials, design, process control and quality management need to be considered. Only by continually improving these aspects can highly precise and consistent aluminum die cast parts be produced.