La fundición a presión de aluminio es un proceso en el que la aleación de aluminio se calienta hasta alcanzar un estado líquido y se inyecta en un molde de fundición a presión para su enfriamiento y conformación. Este proceso ofrece ventajas como la reducción de costes, la precisión, la eficiencia y la fabricación a gran escala. Su tasa de utilización de material es alta, y la tasa de utilización de piezas en bruto llega hasta 90%, lo que reduce los costes. Las aplicaciones incluyen industria del automóvil, electrónica, electrodomésticos, construcción y decoración, aeroespacial, militar y maquinaria en general. Las piezas moldeadas a presión de aluminio tienen una excelente compatibilidad, buena rugosidad superficial y gran precisión dimensional.
Introducción
La fundición a presión de aluminio es un proceso en el que la aleación de aluminio se calienta hasta un estado líquido y luego se inyecta en un molde de fundición a presión para enfriarla y darle forma. La fundición a presión de aluminio ofrece muchas ventajas, como la reducción de costes, la precisión, la eficiencia y la fabricación a gran escala. Su tasa de utilización de material es alta, y la tasa de utilización de piezas en bruto llega hasta 90%, lo que reduce los costes.
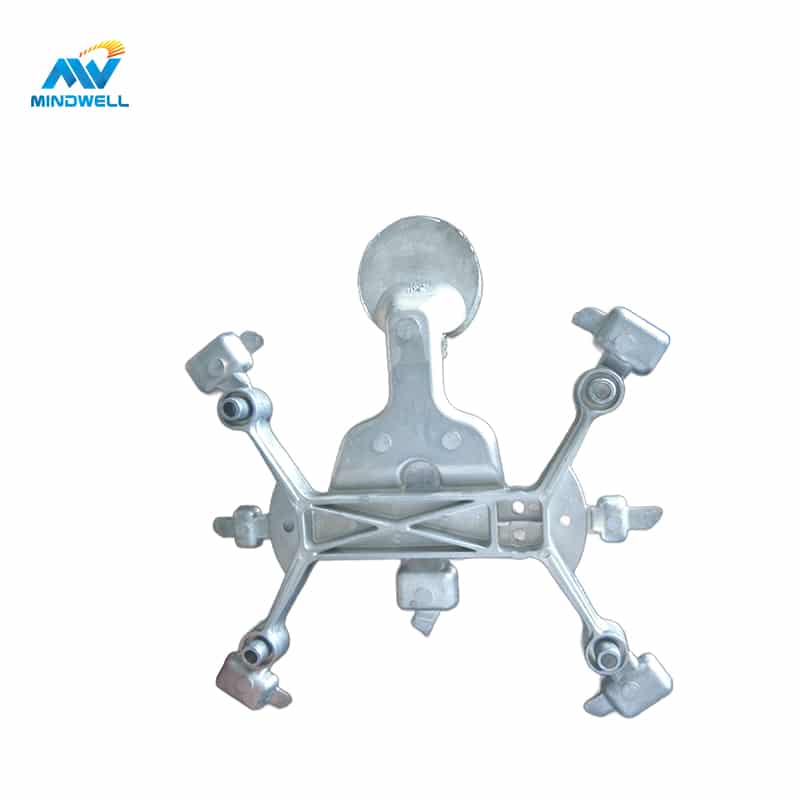
Definición e importancia de la fundición de aluminio a presión
El método de fundición de aluminio a presión consiste en calentar una aleación de aluminio hasta convertirla en líquido e inyectarla en un molde de fundición a presión, donde se enfría y solidifica. Las ventajas de la fundición de aluminio a presión sobre otras técnicas de producción son el alto aprovechamiento del material, la alta productividad y la gran precisión del producto. La fundición a presión de aluminio es otro nombre que reciben los artículos de aluminio fundido a presión. La fundición a presión de aluminio tiene varios usos, como la producción de equipos, componentes electrónicos y de automoción. Los componentes de aluminio fundido a presión son ligeros, fuertes y resistentes a la corrosión, todo lo cual puede aumentar significativamente el rendimiento y la eficiencia de combustible de un automóvil. Los componentes de aluminio fundido a presión ofrecen fuertes propiedades mecánicas y una alta conductividad térmica, lo que ayuda a prolongar la vida útil y la estabilidad del producto. Las piezas de fundición a presión de aluminio son componentes fiables y de alta calidad utilizados en la fabricación de maquinaria que pueden prolongar la vida útil y el rendimiento de los equipos. Como resultado, la fundición de aluminio a presión se ha desarrollado y empleado ampliamente en una gran variedad de industrias. A medida que se creen nuevos materiales y la tecnología de fabricación contemporánea siga ganando popularidad, las posibilidades de aplicación de la fundición de aluminio a presión se ampliarán.
Campos de aplicación de la fundición a presión de aluminio
El proceso de fundición a presión de aluminio se utiliza en muchos campos. Estos son algunos de los principales ámbitos:
- Industria del automóvil: Piezas de motor, frenos, engranajes de dirección y otros componentes son algunos de los muchos productos de la industria del automóvil que emplean la tecnología de fundición a presión de aluminio. La resistencia, ligereza y conductividad térmica de la aleación de aluminio le permiten satisfacer los requisitos de eficiencia energética y ligereza de los vehículos.
- Equipos electrónicos y de comunicación: Los componentes de equipos electrónicos y de comunicación, como carcasas, radiadores, conexiones y tomas de corriente, etc., se fabrican mediante el método de fundición a presión de aluminio. Gracias a su fuerte apantallamiento electromagnético y su conductividad térmica, la aleación de aluminio puede mejorar la estabilidad y el rendimiento de los equipos.
- Electrodomésticos: El campo de los electrodomésticos y equipos eléctricos, como carcasas de aire acondicionado, tambores de lavadoras, componentes de frigoríficos y soportes de televisores, es otro ámbito en el que se utiliza mucho la técnica de fundición a presión de aluminio. Los productos fabricados con aleaciones de aluminio pueden mejorar su textura y estética gracias a la calidad y apariencia de su superficie.
- Sector de la construcción y la decoración: En este sector se fabrican marcos de ventanas, accesorios para puertas y ventanas, elementos de decoración interior y otros artículos mediante el método de fundición a presión de aluminio. En los ámbitos de la construcción y la decoración, la aleación de aluminio puede satisfacer criterios de solidez del material, resistencia a la corrosión y atractivo, ya que es ligera, resistente a la intemperie y maleable.
- Otros ámbitos: Los sectores aeroespacial, militar, de maquinaria general y otros también hacen un amplio uso de la tecnología de fundición de aluminio a presión. Por ejemplo, la fundición a presión de aluminio puede utilizarse para fabricar hélices, piezas de motores, carcasas de aviones y otros componentes. Además, con la técnica de fundición a presión de aluminio se pueden fabricar diversos componentes para equipos mecánicos en general, como piezas de máquinas herramienta, cuerpos de bombas, válvulas, recipientes a presión, etc.
Ventajas y limitaciones de la fundición de aluminio a presión
La fundición inyectada de aluminio tiene la ventaja de ser barata, muy precisa, eficaz y capaz de producir formas complicadas. Pero también tiene algunas restricciones que, según la aplicación, deben tenerse muy en cuenta.
Ventajas de la fundición de aluminio a presión:
- El metal fundido conserva una gran fluidez a alta presión y velocidad, lo que permite fabricar objetos metálicos huecos y profundos con geometrías complicadas, contornos nítidos y paredes finas.
- Las piezas moldeadas a presión de aluminio presentan una excelente compatibilidad, buena rugosidad superficial y gran precisión dimensional.
- Los costes pueden reducirse gracias a la elevada tasa de utilización del material y de la pieza en bruto 90%.
- Excelente productividad y adecuada para la fabricación a gran escala.
- Las incrustaciones pueden utilizarse para satisfacer necesidades de rendimiento específicas y son fáciles de emplear.
- económico. La fundición a presión de aluminio puede reducir los costes de producción y ofrece un proceso de fabricación más sencillo que las técnicas de fabricación convencionales.
- Es capaz de producir grandes volúmenes de piezas de metal fundido y es extremadamente repetible.
- Gracias a su gran resistencia, el material es capaz de tolerar tensiones en situaciones con cargas elevadas y altas temperaturas.
- La superficie es fácil de trabajar y pintar, y el revestimiento puede mejorar su atractivo, resistencia a la corrosión y durabilidad.
Sin embargo, la fundición a presión de aluminio presenta varios inconvenientes.
- Las piezas moldeadas a presión no son adecuadas para la fabricación de lotes pequeños porque suelen tener agujeros e impurezas oxidadas.
- Tanto los tipos de aleaciones de fundición a presión como los tamaños de los artículos de fundición a presión están restringidos.
- Los moldes y el equipamiento son costosos y requieren una inversión importante.
- Durante el proceso de fabricación se producen residuos y gases de escape que deben tratarse para proteger el medio ambiente.
- La mayoría de los componentes de aluminio fundido a presión son finos y frágiles.
- La fundición a presión de aluminio puede no ser la opción ideal para aplicaciones que requieren un alto nivel de resistencia y rigidez.
Preparación de la materia prima

Selección y control de calidad de los lingotes de aluminio
Garantizar la calidad de los productos de fundición a presión de aluminio requiere una serie de pasos previos, como la selección de lingotes de alta calidad que cumplan las especificaciones y un riguroso control de calidad. Para garantizar la calidad y funcionalidad del producto acabado, también es vital prestar atención a otros elementos del proceso de fundición a presión de aluminio, como el diseño del molde, la configuración de los parámetros de fundición a presión, los procedimientos de postprocesado, etc.
A la hora de seleccionar los lingotes de aluminio, deben tenerse en cuenta los siguientes elementos:
- Contenido de aluminio: Para garantizar la calidad y pureza de las materias primas, los lingotes de aluminio deben tener un contenido mínimo de aluminio de 99,5%.
- Contenido de impurezas: El contenido de impurezas de los lingotes de aluminio debe cumplir todas las normativas nacionales aplicables. Para evitar efectos negativos en el rendimiento de la fundición a presión, el contenido de impurezas, como hierro, silicio, cobre, etc., debe mantenerse dentro de ciertos límites.
- El lingote de aluminio debe tener forma de paralelepípedo rectangular regular y carecer de defectos visibles de distorsión o deformación. No debe presentar defectos como poros, fisuras o inclusiones de escoria; la superficie debe ser lisa y nivelada.
- Especificaciones dimensionales: La longitud, la anchura y la altura de los lingotes de aluminio deben cumplir las especificaciones del contrato o las normas nacionales aplicables. La precisión dimensional de los lingotes también debe cumplir los criterios para garantizar la estabilidad y la precisión dimensional de las piezas moldeadas a presión.
- Certificado de calidad de la materia prima: Para garantizar la calidad, trazabilidad y fiabilidad de las materias primas, deben utilizarse lingotes de aluminio con este certificado.
Para el control de calidad de los lingotes de aluminio deben realizarse las siguientes tareas:
- Inspección del material entrante: Verificar que los lingotes de aluminio que entran en la planta cumplen todos los criterios mediante una inspección de calidad que abarca aspectos como la calidad del aspecto, las normas dimensionales, la composición química, etc.
- Inspección del proceso: Para asegurarse de que las piezas de fundición a presión se ajustan a las especificaciones, se examinan al azar o a fondo durante el proceso de fundición a presión para verificar la calidad del aspecto de las piezas, la corrección dimensional, la composición química, etc.
- Gestión de productos no cualificados: Rastrear y gestionar las piezas de fundición a presión o los lingotes de aluminio no cualificados, identificar las causas y tomar las medidas adecuadas para evitar que se repita el problema.
- Mantener registros de calidad: A efectos de análisis de calidad y trazabilidad, lleve un registro de los detalles de fabricación y del estado general de calidad de las piezas moldeadas a presión y los lingotes de aluminio.
- Mejora continua: Optimizamos continuamente el proceso de fabricación y la calidad de las materias primas, mejoramos la calidad y estabilidad de nuestros productos e identificamos cualquier problema y oportunidad de mejora mediante el estudio de los datos del proceso de producción y la calidad.
Fundición y transformación de aleaciones de aluminio
- Preparación de las materias primas: Combinar las materias primas de la aleación de aluminio, como lingotes de aluminio, virutas, chatarra de aluminio, etc., en una proporción determinada.
Calentamiento y fusión: Para fundir las materias primas, hay que colocarlas en el horno y calentarlas a alta temperatura. Los hornos de resistencia eléctricos o de gas son los más comunes.
Control de la temperatura de fusión: La temperatura del horno se regula, normalmente entre 700 y 900 grados centígrados, en función de las distintas fórmulas y especificaciones de las aleaciones de aluminio. - Ajuste de la composición: Para cumplir los criterios de rendimiento necesarios, añada los componentes adecuados a la aleación de aluminio y realice las modificaciones necesarias en su composición en función de las especificaciones del producto.
- Tratamiento de las escorias: Durante el proceso de fundición se formarán algunas impurezas y óxidos que harán necesario el tratamiento de las escorias. Normalmente, se utiliza como agente escorificante un producto químico capaz de absorber y purificar las impurezas de la masa fundida.
- Tratamiento de desgasificación: Para mejorar la calidad de la aleación de aluminio y eliminar los gases durante el proceso de fundición, hay que realizar rápidamente un tratamiento de desgasificación. A menudo se utilizan varias técnicas de desgasificación, como los procedimientos de pulverización y aspirado.
- Control del tiempo de fusión: La calidad de una aleación de aluminio depende en gran medida del tiempo de fusión. La aleación de aluminio se mezclará de forma desigual si el tiempo de fusión es demasiado corto, y se oxidará rápidamente si el tiempo de fusión es demasiado largo. Por ello, es necesario controlar el tiempo de fusión.
Ajuste de la composición y control de calidad del aluminio líquido
El rendimiento y la calidad del producto acabado dependen en gran medida de la modificación de la composición y el control de calidad del líquido de aluminio, que son pasos cruciales en el proceso de fundición a presión de aluminio.
Una etapa esencial en el control de calidad del líquido de aluminio es la modificación de la composición. Para alcanzar los criterios de rendimiento del producto, hay que controlar la composición química del líquido de aluminio. En el ajuste de la composición del líquido de aluminio intervienen principalmente los siguientes factores:
- Elemento de aluminio: Con un porcentaje típico de más de 85%, el aluminio es el principal constituyente de la aleación de aluminio fundido a presión. Los elementos de aluminio influyen significativamente en la fluidez, la contracción, la propensión al agrietamiento en caliente y las características mecánicas de las aleaciones de aluminio. En función de la aplicación prevista y de las normas de rendimiento del producto, hay que determinar la composición y el tipo del elemento de aluminio.
- Elementos de aleación: Además de los elementos de aluminio, deben añadirse proporciones adecuadas de elementos de aleación, como magnesio, zinc, cobre, etc. Estos elementos de aleación pueden mejorar las características mecánicas, la resistencia a la corrosión y la estabilidad térmica de las aleaciones de aluminio. Elija el tipo de elemento de aleación y el contenido adecuados en función de las necesidades de la aplicación y el rendimiento del producto.
- Impurezas: El hierro, el silicio y otras impurezas pueden mezclarse con la aleación de aluminio a medida que se funde. Estos componentes de impureza repercutirán en la calidad y el rendimiento de la aleación de aluminio. Por consiguiente, para eliminar o reducir la cantidad de componentes de impureza, debe modificarse la composición.
Se pueden utilizar técnicas de análisis químico para detectar rutinariamente el líquido de aluminio durante el proceso de ajuste de la composición con el fin de determinar su composición química y la concentración de impurezas. La composición del líquido de aluminio se modifica de acuerdo con los resultados de las pruebas para satisfacer las especificaciones de rendimiento del producto.
Un componente crucial para cambiar la composición del líquido de aluminio es el control de calidad. Para garantizar la calidad y pureza de las materias primas, hay que regularlas estrictamente empezando por las materias primas. Al mismo tiempo, variables como la temperatura de fundición, la duración y el porcentaje de carga deben gestionarse a lo largo de toda la operación para evitar que disminuya la calidad del aluminio fundido. Para asegurarse de que el rendimiento y la calidad del aluminio líquido cumplen las especificaciones, también debe someterse a pruebas y evaluaciones rutinarias.
Diseño y fabricación de moldes

Principios básicos del diseño de moldes
- Funcionalidad: El molde debe ser capaz de cumplir la función de moldeo prevista y garantizar que el tamaño, la forma y la precisión del producto satisfacen las especificaciones.
Estructura racional: La estructura del molde debe ser sencilla y fácil de entender, fácil de fabricar y montar, y cómoda de sustituir y mantener durante su uso. - Estabilidad: Para garantizar una calidad constante del producto durante un periodo de tiempo prolongado, el molde debe tener una excelente estabilidad y durabilidad con un uso repetido.
- Seguridad: Para evitar contratiempos como desprendimientos, grietas, etc. durante el uso del molde, la seguridad de funcionamiento debe tenerse en cuenta durante el diseño.
- Economía: Los costes de fabricación y utilización del molde deben reducirse al mínimo sin dejar de cumplir las normas funcionales y de calidad.
Selección y procesamiento de materiales para moldes
- Selección de materiales: Elija materiales con la resistencia, dureza, resistencia al desgaste, resistencia a la corrosión y estabilidad térmica adecuadas en función de las exigencias del producto y las circunstancias de funcionamiento del molde (temperatura, presión, fricción, etc.).
- Tratamiento térmico: Para mejorar las cualidades mecánicas y prolongar la vida útil del material del molde, aplique el tratamiento térmico adecuado, como temple, revenido, carburación, etc.
- Tratamiento de la superficie: Para aumentar la resistencia del molde a la corrosión y la calidad de su superficie, ésta se pule, se rectifica, se recubre y se somete a tratamientos adicionales.
Flujo del proceso de fabricación de moldes
- Diseño de moldes: Crear planos y diseñar la estructura del molde basándose en las especificaciones del producto y el entorno operativo.
- Preparación del material: Conseguir o producir los materiales del molde, y llevar a cabo el preprocesamiento y la inspección necesarios.
- Procesamiento y fabricación: Las piezas de molde se fabrican mediante corte por hilo, electroerosión, procesamiento mecánico y otras técnicas, de acuerdo con las especificaciones especificadas en los planos.
- Montaje y depuración: Ensamble los componentes del molde procesado, solucione problemas y pruebe el molde para asegurarse de que funciona como debe.
- examen y aceptación: Antes de liberar el molde para su uso, realice un examen exhaustivo para asegurarse de que satisface todos los criterios de diseño y del producto.
Mantenimiento y cuidado del moho
- Inspecciones frecuentes: Realice inspecciones minuciosas de los moldes con frecuencia para identificar y solucionar a tiempo cualquier problema, como desgaste, corrosión, grietas, etc.
- Limpieza y mantenimiento: Para evitar daños en la superficie del molde y el deterioro de la calidad del producto, mantenga el molde limpio y elimine rutinariamente el aceite y otros contaminantes de su superficie.
- Lubricación y mantenimiento: Para minimizar el desgaste y alargar la vida útil del molde, lubrique regularmente los componentes móviles del molde.
- Reparación y sustitución: Para garantizar el funcionamiento regular del molde y la calidad del producto final, repare o sustituya rápidamente los componentes del molde que estén muy desgastados o dañados.
- Gestión de registros: Lleva un registro del uso, las reparaciones y el mantenimiento del molde para poder gestionarlo y mantenerlo en el futuro.
Proceso de fundición a presión de aluminio
La fundición a presión de aluminio es un proceso en el que se inyecta aluminio líquido en un molde a alta presión y se enfría para obtener productos de aluminio de la forma y el tamaño deseados.
- Fabricación de aluminio líquido: Para fabricar aluminio líquido, primero hay que fundir los lingotes de aluminio de mayor calidad hasta que estén fundidos y, a continuación, añadir los componentes de aleación necesarios. Para garantizar su pureza durante todo este proceso, el aluminio líquido debe pasar por procedimientos de purificación que incluyen la desgasificación y la eliminación de escorias.
- Elija una máquina de fundición a presión: Elija una máquina de fundición a presión que cumpla las especificaciones de los productos de fundición a presión en cuanto a tamaño, forma y precisión. Los dos tipos de máquinas de fundición a presión son las de cámara caliente y las de cámara fría. Los objetos pequeños y de paredes finas pueden fabricarse con la primera, mientras que los grandes y de paredes gruesas pueden fabricarse con la segunda.
- Instalación y ajuste de los moldes de fundición a presión: Establecer el molde previsto en los moldes móviles y permanentes de la máquina. A continuación, realice los ajustes necesarios en la ubicación del molde y la carrera de apertura/cierre para garantizar un ajuste seguro y preciso.
- Vertido y llenado: El aluminio fundido entra en la cavidad del molde a través del bebedero durante el proceso de fundición a presión. El efecto de llenado del aluminio líquido y la calidad del producto final dependen en gran medida de la temperatura y la velocidad del vertido. El llenado es el proceso por el que el aluminio líquido llena rápidamente y a alta presión la cavidad del molde; la fundición a presión se realiza tras un breve periodo de solidificación.
- Desmoldeo y enfriamiento: Una vez finalizado el llenado de líquido de aluminio, el molde se enfría para endurecer la pieza fundida a presión. El tamaño y la complejidad del producto determinan el tiempo que tarda en enfriarse. La fundición a presión se extrae del molde abriéndolo cuando alcanza una cierta dureza.
- Control e inspección de calidad: Los componentes de fundición a presión deben someterse a pruebas de calidad, incluidas las dimensiones, el peso y el aspecto, una vez desmoldeados. Es necesario filtrar y manipular los artículos no cualificados para asegurarse de que la calidad del producto acabado satisface las especificaciones.
Proceso de tratamiento posterior
Recorte y retirada de bebederos
Los bebederos y rebosaderos son elementos importantes en el proceso de fundición a presión que dirigen el aluminio fundido a la cavidad del molde. Una vez realizada la fundición a presión, estas estructuras ya no son necesarias. Por ello, el corte y la eliminación de los bebederos son procedimientos cruciales del proceso de fundición a presión.
- Recorte: Para asegurarse de que la pieza moldeada cumple las especificaciones de diseño, recorte el material sobrante alrededor del borde con una recortadora de bordes o un punzón. El recorte limpia la pieza fundida al eliminar el metal sobrante.
- Retirar el bebedero: se trata del canal que conecta la cavidad del molde con la compuerta. Estas secciones de conexión deben extraerse después de la fundición a presión. Para esta operación se pueden utilizar técnicas manuales, mecánicas o de corte por láser.
Tecnología de tratamiento de superficies
Las piezas moldeadas a presión pueden presentar imperfecciones superficiales como rebabas, poros y protuberancias. El tratamiento de la superficie suele ser necesario para mejorar su aspecto y funcionalidad.
- Pulido: Para eliminar los defectos de la superficie y alisar el fundición a presión superficie, utilice una pulidora o un pulido manual. Además, el pulido puede mejorar el aspecto y la textura del metal.
- Recubrimiento por pulverización: Las piezas moldeadas a presión pueden tener un revestimiento protector aplicado a su superficie mediante la tecnología de revestimiento por pulverización para aumentar la resistencia al desgaste y a la corrosión, entre otras propiedades. A menudo se pulverizan pintura, plástico y otros materiales.
- La técnica de aplicar materiales metálicos o no metálicos a las superficies de las piezas moldeadas a presión se denomina galvanoplastia. La galvanoplastia es una técnica que puede utilizarse para generar una capa de revestimiento con cualidades específicas en la superficie de la pieza moldeada a presión, como el niquelado o el cromado.
Tratamiento térmico y proceso de refuerzo
Los métodos de tratamiento térmico y refuerzo son esenciales para mejorar aún más el rendimiento de la fundición a presión.
- Tratamiento térmico: La estructura metalográfica interior de la pieza moldeada a presión se modifica para mejorar sus características mecánicas y su estabilidad calentándola y enfriándola. A menudo se utilizan el recocido, el temple y otros procedimientos de tratamiento térmico.
- Proceso de refuerzo: Mediante determinadas técnicas, las piezas de fundición a presión se hacen más duras y resistentes al desgaste a través del proceso de refuerzo. Las piezas de fundición a presión con tratamiento de endurecimiento superficial, por ejemplo, tienen una superficie más dura y mejor resistencia al desgaste.
Inspección de calidad y envasado de productos acabados
Para asegurarse de que los componentes fundidos a presión cumplen las especificaciones, es necesario realizar una inspección de calidad tras una serie de procedimientos de postprocesado.
- Inspección de calidad: utilice pruebas de rendimiento, mediciones dimensionales, exámenes visuales y otros métodos para evaluar a fondo la calidad de las piezas fundidas a presión. Las piezas de fundición a presión que se consideren no cualificadas deben repararse o desecharse.
- Embalaje del producto final: Para preservar su integridad durante el almacenamiento y el tránsito, los componentes de fundición a presión cualificados deben embalarse adecuadamente. Los materiales y técnicas de embalaje adecuados, como cajas de madera, cartones, bolsas de plástico, etc., pueden elegirse en función de las especificaciones y características de los componentes de fundición a presión.
Gestión y optimización de la producción
creación y ejecución de programas de producción
Un paso crucial en el proceso de fundición a presión de aluminio es la creación de la planificación de la producción. Para ello hay que tener muy en cuenta factores como la disponibilidad de materias primas, la capacidad de fabricación y la demanda del mercado. Los principales procedimientos para crear y llevar a cabo planes de producción son los siguientes:
- Investigación y análisis de mercado: Conozca el panorama competitivo, las tendencias de desarrollo de productos y la demanda del mercado a través de estudios de mercado, que también sirven de base para el diseño del plan de producción.
- Crear planes de producción: A partir de la información obtenida en el estudio de mercado, los objetivos estratégicos de la empresa y los recursos disponibles, elabore planes de producción exhaustivos a corto y largo plazo.
- Programación y asignación de recursos: Para garantizar que el proceso de fabricación avanza sin problemas, distribuye de forma lógica recursos como mano de obra, maquinaria, materias primas, etc. de acuerdo con el plan de producción.
- Programación y ejecución de la producción: Trabajar con el plan de producción para programar los distintos eslabones de la producción, asegurarse de que se sigue el plan y resolver con prontitud los problemas que surjan a lo largo del proceso de producción.
- Los datos de fabricación pueden seguirse en tiempo real, lo que permite identificar y resolver rápidamente los problemas del proceso de fabricación. Los planes de producción también pueden modificarse para garantizar la entrega a tiempo.
Controlar y ajustar la producción
El seguimiento en tiempo real y los ajustes del proceso de fabricación son necesarios para garantizar la estabilidad y la calidad de la fundición a presión de aluminio. A continuación se indican algunos pasos esenciales de seguimiento y corrección:
- Supervisión del estado de los equipos: Asegúrese de que las máquinas de fundición a presión, los moldes y otros equipos funcionan correctamente vigilando su estado operativo en tiempo real mediante sensores e instrumentos de los equipos.
- Control de los parámetros del proceso: A lo largo del proceso de fundición a presión, los parámetros críticos del proceso, como la temperatura, la presión y el tiempo, se controlan y gestionan en tiempo real para garantizar la estabilidad y precisión de los parámetros.
- Inspección de calidad: Para asegurarse de que la calidad del producto satisface los requisitos, se examinan al azar o a fondo los componentes de fundición a presión para buscar problemas de tamaño, rendimiento, aspecto y otras indicaciones.
- Tratamiento de los productos no cualificados: Para evitar que se repita el problema, examine las razones de los componentes de fundición a presión no cualificados y modifique rápidamente el proceso de fabricación.
- Registro y análisis: Para analizar y mejorar el proceso de producción, registre diversos datos a lo largo de todo el proceso, incluidos los parámetros del proceso, los parámetros de funcionamiento de los equipos, los resultados de las inspecciones de calidad, etc.
Gestión y optimización de los costes de producción
La gestión de costes es esencial en el proceso de fabricación de la fundición de aluminio a presión. He aquí algunas formas de ahorrar costes:
- Optimice los parámetros del proceso: De este modo, puede reducir el consumo de energía y el desperdicio de materias primas.
- Aumente la eficiencia de la producción: Al mejorar el mantenimiento y la utilización de los equipos, se aumenta la eficiencia de la producción y se reducen los gastos de fabricación por unidad de producción.
- Reducir la tasa de residuos: Reduzca la tasa de residuos mejorando el control de calidad, optimizando los procedimientos de fabricación y tomando otras medidas que reduzcan los residuos.
- Gestión de inventarios y compras razonables: Para evitar despilfarros y retrasos en el inventario, compre correctamente las materias primas en función de la demanda real de producción. Una gestión eficaz del inventario también reduce los gastos asociados a las existencias.
- Gestión de los recursos humanos: Asignar los recursos con sensatez, aumentar la productividad de los trabajadores y reducir los gastos laborales.
Tendencias de desarrollo e innovación en el proceso de fundición a presión de aluminio
El método de fundición de aluminio a presión evoluciona constantemente debido al progreso de la tecnología y a las cambiantes necesidades del mercado. A continuación se indican algunos posibles avances y tendencias de desarrollo:
- Utilización de materiales novedosos: Crear nuevos materiales de aleación de aluminio para mejorar las características mecánicas y la resistencia a la corrosión de las piezas fundidas a presión. Investigar los posibles usos de otros metales en la industria de la fundición a presión.
- Producción inteligente: Para lograr la automatización, informatización e inteligencia del proceso de producción y mejorar la eficiencia productiva y la calidad de los productos, introducir tecnologías inteligentes como robots industriales, Internet de las Cosas, análisis de big data, etc.
- Fomento de una fabricación respetuosa con el medio ambiente: A medida que aumenta la conciencia medioambiental, se impulsa el crecimiento ecológico de la industria de fundición a presión de aluminio para reducir el derroche de recursos y la contaminación del medio ambiente durante la producción. Por ejemplo, se toman medidas como reciclar la basura y utilizar agentes desmoldeantes ecológicos.
- Conseguir flexibilidad en la personalización y la fabricación de lotes pequeños exige desarrollar herramientas y procedimientos que permitan cambiar rápidamente los moldes, adaptarse a los cambios en la demanda del mercado y realizar la personalización y la producción de lotes pequeños.
- Ampliar los campos de aplicación: Investigar los posibles usos de la tecnología de fundición de aluminio a presión en los ámbitos aeroespacial, de aligeramiento de automóviles, de nuevas energías y otros, y ampliar la gama de aplicaciones de los componentes de fundición de aluminio a presión. Para obtener información más precisa y exhaustiva sobre las tendencias de innovación y desarrollo, consulte la bibliografía o los especialistas pertinentes.
Seguridad y medio ambiente
Riesgos para la seguridad y precauciones que deben tomarse al fundir aluminio a presión:
El proceso de fundición de aluminio a presión puede incluir varios riesgos para la seguridad. Para garantizar la seguridad de la producción, deben realizarse las acciones preventivas correspondientes. A continuación se indican algunos riesgos y medidas de seguridad típicos:
- Quemaduras por altas temperaturas: Las quemaduras por el líquido metálico a alta temperatura utilizado en la fundición a presión del aluminio son bastante frecuentes. Llevar el equipo de protección adecuado, como guantes y calzado, y evitar el contacto directo con líquidos metálicos calientes son ejemplos de precauciones.
- Lesiones mecánicas: Los pellizcos, cortes y otras formas de daños mecánicos pueden producirse mientras una máquina de fundición a presión está en funcionamiento. El cumplimiento estricto de los protocolos de funcionamiento, el uso de guantes y equipos de protección adecuados, y asegurarse de que los equipos cuentan con protecciones de seguridad son ejemplos de medidas preventivas.
- Gases y polvo: Durante la fundición a presión del aluminio pueden generarse gases y polvos peligrosos que ponen en peligro la salud de los trabajadores. La mejora de la ventilación, el uso de equipos de protección individual adecuados y la limpieza y el control rutinarios del entorno son ejemplos de medidas preventivas.
- Ruido y vibraciones: La máquina de fundición a presión producirá ruidos y vibraciones durante su funcionamiento, que pueden ser perjudiciales para la comodidad y la audición de los trabajadores. Controlar las fuentes de ruido, utilizar silenciadores, realizar exámenes auditivos periódicos y ofrecer a los empleados un espacio de trabajo agradable son ejemplos de métodos preventivos.
- Otros riesgos para la seguridad son los relacionados con la seguridad eléctrica, el trabajo en altura, etc. Es necesario tomar las precauciones adecuadas, como inspeccionar rutinariamente los equipos eléctricos y garantizar la seguridad de la plataforma de trabajo.
Leyes y normas medioambientales para la eliminación de residuos:
Para garantizar que el proceso de fabricación cumple las normas medioambientales, la industria de fundición de aluminio a presión debe respetar las normas medioambientales pertinentes y los criterios de eliminación de residuos. A continuación se indican algunas leyes típicas relativas al medio ambiente y la eliminación de residuos:
- Control de emisiones contaminantes: Para garantizar que las emisiones contaminantes cumplen los criterios, las empresas de fundición a presión de aluminio están obligadas por las normas nacionales y municipales de protección del medio ambiente a regular la emisión de gases residuales, aguas residuales y residuos sólidos.
- Categorización y tratamiento de los residuos: Dependiendo del tipo y la naturaleza de los residuos, se utilizan muchas técnicas de tratamiento. Es necesario clasificar la basura reciclable en distintas categorías y entregarla a organizaciones de reciclaje certificadas para su tratamiento. Los residuos peligrosos deben enviarse a instalaciones de eliminación certificadas, y los residuos generales también deben tratarse correctamente de acuerdo con la legislación vigente.
- Instalaciones y equipos de protección del medio ambiente: Para garantizar un tratamiento adecuado de los contaminantes durante el proceso de producción, las empresas de fundición de aluminio a presión deben estar dotadas de instalaciones y equipos de protección medioambiental adecuados, como instalaciones de tratamiento de aguas residuales y dispositivos de tratamiento de gases de escape.
- Evaluación del impacto ambiental y aceptación Antes de ser utilizados, los proyectos de fundición a presión de aluminio de nueva construcción, remodelados y ampliados deben someterse a una evaluación de impacto ambiental y ser aprobados por la agencia de protección del medio ambiente.
- Mejora de la concienciación y la formación de los empleados: Para garantizar la correcta aplicación de la normativa de protección medioambiental en todo el proceso de producción, las empresas de fundición de aluminio a presión deben proporcionar a su personal formación en materia de protección medioambiental para aumentar su nivel de concienciación y perfeccionar sus habilidades operativas.
Técnicas ecológicas de fabricación, reducción de la contaminación y ahorro de energía:
El sector de la fundición de aluminio a presión puede reducir el consumo de energía, disminuir las emisiones y aumentar la eficiencia en la utilización de los recursos utilizando una serie de técnicas ecológicas de fabricación y ahorro de energía. He aquí algunas posibles medidas:
- Optimice los parámetros del proceso: Elegir cuidadosamente los parámetros del proceso de fundición a presión permite reducir el consumo de energía y el desperdicio de materias primas. Por ejemplo, maximizando el diseño del molde, gestionando variables del proceso como la presión y la temperatura, aumentando los índices de certificación de la fundición a presión y reduciendo los índices de rechazo.
- Reciclaje de energía: Para reducir el despilfarro de energía, se recupera y reutiliza el calor residual del proceso de fundición a presión de aluminio utilizando tecnología de recuperación del calor residual. Por ejemplo, los moldes de fundición a presión se calientan o precalientan utilizando el calor residual del horno de fundición.
- Emplear energías limpias: Para reducir la dependencia de los combustibles fósiles, dé prioridad al uso de energías limpias en el proceso de fabricación, como la solar, la eólica y otras formas de energía.
- Aumentar la eficiencia de los equipos: Gracias a los avances tecnológicos y a las actualizaciones de los equipos, las máquinas de fundición a presión y otros equipos de fabricación pueden funcionar de forma más eficiente y consumir menos energía y recursos. Ponga como ejemplo los dispositivos de ahorro energético, como la iluminación de bajo consumo y los motores de alta eficiencia.
- Impulse la gestión de la producción: Preparando con sensatez los calendarios de producción, racionalizando los procedimientos de producción y adoptando otras medidas, podrá reducir la cantidad de energía y recursos utilizados durante la producción. Al mismo tiempo, reforzaremos la supervisión y la gestión medioambientales a lo largo de todo el proceso de fabricación para garantizar que los contaminantes se gestionan eficazmente y que las emisiones cumplen la normativa.
- Fomentar la creación de una cadena de suministro ecológica: Las empresas de fundición a presión de aluminio pueden trabajar con los proveedores para fomentar los materiales ecológicos y las técnicas de fabricación ecológicas, así como para alcanzar en colaboración objetivos de desarrollo sostenible.
- Innovación y mejora continua: Buscar siempre nuevos métodos y herramientas, mejorar y optimizar el proceso de fabricación, aumentar la eficacia en el uso de los recursos y consumir menos energía. También se insta a los empleados a participar en proyectos creativos, técnicas de ahorro energético y estrategias de reducción de emisiones para apoyar colectivamente el crecimiento sostenible de la empresa.
en conclusión
La fundición de aluminio a presión es un proceso crítico que implica la selección de lingotes de alta calidad que cumplan las especificaciones y se sometan a un estricto control de calidad. La fundición y el procesamiento de las aleaciones de aluminio incluyen la preparación de la materia prima, el calentamiento y la fusión, el ajuste de la temperatura de fusión, el ajuste de la composición, el tratamiento de la escoria, el tratamiento de desgasificación, el control del tiempo de fusión, etc. El aluminio es un material clave en la producción de una gran variedad de productos, incluidos los moldes. El proceso de diseño de moldes implica seleccionar y procesar los materiales, garantizar que cumplen las especificaciones requeridas y que reciben el tratamiento térmico y de superficie adecuados. Las piezas fundidas a presión de aluminio se someten a diversas técnicas de tratamiento superficial para mejorar su aspecto y funcionalidad. La fundición de aluminio a presión es un proceso en rápida evolución que sigue evolucionando debido a los avances tecnológicos y a la demanda del mercado. La industria está explorando nuevos materiales para mejorar las propiedades mecánicas y la resistencia a la corrosión de las piezas de fundición a presión. La tecnología de producción inteligente se introduce continuamente para mejorar la eficiencia y la calidad del producto. La industria de la fundición de aluminio a presión también está promoviendo la fabricación ecológica con el objetivo de reducir el desperdicio de recursos y la contaminación medioambiental. La industria también está explorando la aplicación de la tecnología de fundición a presión de aluminio en los campos aeroespacial, de aligeramiento de automóviles y de nuevas energías.