Una técnica de producción muy eficaz y adaptable, fundición de aluminio a alta presión se utiliza para crear con precisión componentes de aluminio complejos y detallados. Gracias a su capacidad para producir formas intrincadas, tolerancias precisas y productos finales de alta calidad, esta tecnología se ha popularizado en diversos sectores. En este artículo se tratan los principios, las ventajas y los usos de la fundición de aluminio a alta presión.
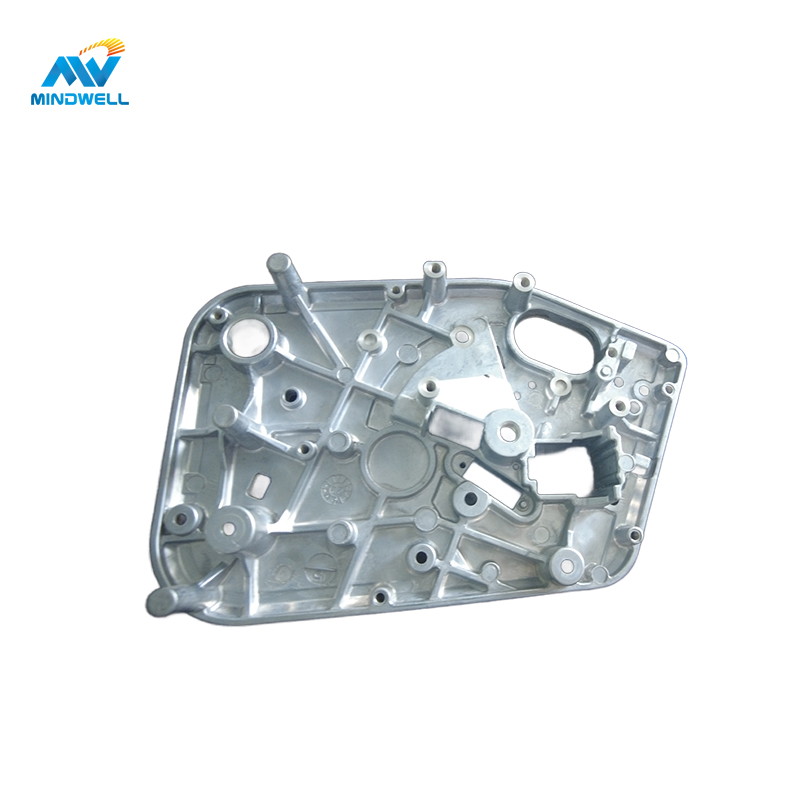
qué es el proceso de fundición de aluminio a alta presión?
Para crear con precisión componentes metálicos complejos y detallados se utiliza una sofisticada técnica de fabricación denominada fundición de aluminio a alta presión. Para crear formas intrincadas y tolerancias precisas, se inyecta aluminio fundido a alta presión en la cavidad de un molde. Preparar el molde, inyectar el aluminio fundido, enfriar y solidificar, y expulsar la pieza fundida son los pasos esenciales del proceso de fundición de aluminio a alta presión.
La principal característica de la fundición a presión de aluminio de alta presión es su alta presión y velocidad de inyección, que permiten que el metal llene rápidamente las esquinas del molde y produzca piezas con un alto grado de precisión y densidad. La mayoría de las piezas fundidas a alta presión no necesitan ser desbarbadas, taladradas o roscadas una vez producidas.
Además, como el aluminio es muy resistente y ligero, las piezas moldeadas a presión de aluminio pueden sustituir al acero en un producto, reduciendo su peso total sin sacrificar su resistencia.
Proceso de fundición de aluminio a alta presión:
Preparación del moho:
El primer paso del procedimiento consiste en crear un molde metálico con la forma del componente requerido. Este molde suele ser de acero o hierro. Se pretende que el molde tolere la alta presión y temperatura que conlleva el proceso de fundición.
Se inyecta aluminio fundido.
El aluminio se funde en un horno y luego se vierte en el molde a una presión muy alta, a menudo entre 1500 y 25.000 psi (libras por pulgada cuadrada). El aluminio también puede reciclarse. Esta alta presión garantiza que el metal se funda completamente en las cavidades del molde.
El proceso de enfriamiento y solidificación.
El aluminio fundido se deja enfriar y solidificar después de llenar el molde, adoptando la forma del molde durante este proceso. Para garantizar las cualidades correctas del material y evitar fallos, el proceso de enfriamiento se regula meticulosamente.
Retirada del molde:
El componente de aluminio recién formado se libera del molde una vez solidificado. Después, el molde puede volver a utilizarse para más piezas fundidas.
¿Cómo funciona el proceso de fundición a alta presión?
- Tras calentarse hasta su punto de fusión, el metal fundido se convierte en líquido.
- En todo el proceso de fundición a presión se utiliza alta presión para forzar rápidamente el metal líquido en la cavidad precisa del molde metálico.
- El metal fundido se enfría y se solidifica bajo presión para crear la pieza de fundición deseada.
- Abra el molde de fundición a presión, extraiga la pieza fundida y termine el proceso de fundición a presión una vez que el metal líquido haya fraguado por completo.
Las dos técnicas fundamentales para producir fundición inyectada de aluminio a alta presión son la fundición inyectada en cámara fría y la fundición inyectada en cámara caliente. El metal fundido se vierte en la cámara de presión de una máquina de fundición a presión de cámara fría mediante un sistema de vertido manual o automatizado. A continuación, el punzón de inyección fuerza hidráulicamente el metal en la cavidad del molde a medida que avanza. En el método de fundición a presión de cámara caliente, la cámara de presión se coloca perpendicular al crisol. El metal fundido entra automáticamente en la cámara de presión a través del orificio de alimentación, y el punzón de inyección desciende para forzar el metal fundido en la cavidad del molde.
Ventajas de la fundición de aluminio a alta presión:
- Alta precisión y densidad: La inyección a alta presión puede garantizar una alta precisión y densidad en las piezas fundidas de aluminio, lo que se traduce en productos de mayor calidad.
- Ideal para grandes piezas de fundición de aluminio: las grandes piezas de fundición de aluminio pueden producirse mediante la técnica de fundición de aluminio a presión, lo que la hace perfecta para su uso en grandes aplicaciones industriales.
- Alta eficiencia de producción: La fundición a presión de aluminio puede fabricar constantemente grandes cantidades de artículos y aumentar la eficiencia de la producción porque puede solidificarse rápidamente a alta presión para formar el producto requerido.
- Costes de producción mínimos: El método de fundición a presión de aluminio consiste en inyectar metal fundido en un molde, que se solidifica rápidamente a alta presión para crear el resultado deseado. El coste de producción es bajo porque esta tecnología permite crear un gran número de componentes de tamaño pequeño y mediano ahorrando mucha energía y recursos.
- Alta precisión de fabricación: La precisión de los productos fabricados puede aproximarse a niveles milimétricos, ya que la fundición de aluminio a alta presión se produce de forma totalmente automatizada.
- Calidad estable del producto: La tecnología para procesar el aluminio fundido a presión puede eliminar el trabajo manual y evitar problemas con la calidad del producto provocados por factores humanos. Al mismo tiempo, cada paso del proceso de fabricación, incluida la elección de las materias primas, garantiza que los productos sean del más alto calibre.
- La fundición a presión de aluminio tiene un tiempo de ciclo rápido y una gran eficacia de producción en comparación con otros métodos de fabricación. En la mayoría de los casos, todo el proceso, desde el diseño del producto hasta su fabricación, dura sólo unas semanas. La eficiencia de producción de la empresa puede aumentar considerablemente gracias a este rápido ciclo de fabricación.
- Alta plasticidad: Mediante el proceso de fundición a presión del aluminio pueden fabricarse productos de formas muy variadas. Además, la fundición a presión de aluminio de precisión puede satisfacer las demandas de diversas industrias en cuanto a formas de productos debido a la alta plasticidad del aluminio.
- Protección del medio ambiente y ahorro de energía: El método de fabricación de la fundición a presión de aluminio utiliza aleación de aluminio fundido en lugar de disolventes peligrosos, adhesivos u otros productos químicos, lo que satisface tanto las normas medioambientales como las de conservación de energía. Con el fin de lograr el reciclaje de recursos y reducir los costes de fabricación, los residuos de aluminio también pueden reciclarse mientras se fabrica el producto.
Fundición inyectada de aluminio de alta presión frente a baja presión
El aluminio y otros metales se funden mediante dos procesos diferentes: fundición a alta presión (HPDC) y fundición a baja presión (LPDC). La presión utilizada durante el proceso de fundición es el aspecto en el que más difieren estas técnicas.
Fundición a alta presión (HPDC):
Proceso:
- En el HPDC, el metal fundido se inyecta a gran velocidad y presión en una cavidad de molde metálica.
- La alta presión se mantiene durante todo el proceso de solidificación para garantizar la formación de piezas fundidas detalladas y precisas.
Presión:
Normalmente, la fundición a presión de alta presión implica presiones que oscilan entre 10.000 y 30.000 psi (70 y 200 MPa).
Ventajas:
- Altos índices de producción: HPDC es conocido por su capacidad para producir rápidamente grandes cantidades de piezas complejas de alta integridad.
- Excelente precisión dimensional y acabado superficial.
- Adecuado para paredes finas y diseños intrincados.
Desventajas:
- Los costes de equipamiento pueden ser relativamente elevados.
- Tooling costs are significant.
- Limited to smaller casting sizes compared to low-pressure processes.
Die Casting at Low Pressure (LPDC):
Method:
Melted metal is poured into the mold using a regulated low-pressure mechanism in LPDC.
Usually, throughout the casting process, the pressure is kept at a lower level.
Apply pressure:
Generally speaking, LPDC operates at lower pressures, between a few hundred and several thousand psi (about 0.07 and 3 MPa).
Benefits
- less expensive tools and equipment than high-pressure procedures.
- Ideal for bigger, more substantial castings.
- Reduced turbulence in the molten metal may lead to a decrease in the number of gas porosities.
Drawbacks:
- lower output rates in contrast to die casting at high pressure.
- may not be able to achieve elements that are really complex and elaborate.
A number of variables, including the part’s size and complexity, production volume, financial concerns, and necessary material qualities, must be taken into account when deciding between high-pressure and low-pressure die casting. Low-pressure die casting could be more appropriate for bigger, simpler parts with lower production quantities, whereas high-pressure die casting is often used for high-volume manufacturing of smaller, intricate components. The choice of procedure is contingent upon the particular demands of the casting project, since each method has a unique combination of benefits and drawbacks.
Why is aluminum material suitable for high-pressure die casting?
The reasons why aluminum materials are suitable for high-pressure die-casting are as follows:
- Low melting point: Aluminum has a relatively low melting point, about 660°C, which makes it easy to melt and inject into molds under high pressure.
- Good fluidity: Aluminum has good fluidity and can be smoothly injected into fine parts of the mold under high pressure to obtain a complete product.
- Good corrosion resistance: Aluminum is a corrosion-resistant material that does not easily react with oxygen, carbon dioxide, water, and other substances in the air, so it can maintain its performance and appearance for a long time.
- Moderate density: The density of aluminum is relatively low, about 2.7 g/cm2, which means aluminum products are lightweight and easy to transport and use.
- Recyclable: Aluminum is a recyclable material that meets the requirements of sustainable development.
- To sum up, the reason why aluminum material is suitable for high-pressure die-casting is mainly due to its low melting point, good fluidity, good corrosion resistance, moderate density and recyclability.
High-Pressure Aluminum Die Casting Applications:
Sector del automóvil:
Automobile structural elements, engine components, and gearbox cases benefit from high-pressure die-cast aluminum’s strength and lightweight qualities.
Electrónica para consumidores:
This method is often used to create housings for complex components such as heat sinks and electrical gadgets.
Airspace:
High-pressure die-cast aluminum is lightweight and strong, making it a great choice for a variety of aviation components, including housings and structural sections.
Engineering in general:
A large variety of components for tools, machinery, and industrial equipment may be produced because to the process’s adaptability.
A popular and effective technique for creating aluminum components that satisfy industrial requirements and high quality standards is high-pressure aluminum die casting. Because of its capacity to create intricate forms and preserve dimensional precision, it is essential to the production of many goods in a variety of industries.
Conclusión:
High-pressure aluminum die casting is a sophisticated and efficient manufacturing process that has revolutionized the production of complex aluminum components. Its ability to achieve high precision, cost-effectiveness, and versatility makes it a preferred choice across diverse industries, driving innovation and advancements in product design and manufacturing. As technology continues to evolve, high-pressure aluminum die casting is likely to play a crucial role in shaping the future of manufacturing.
What are 3 limitations of high pressure die casting?
High-pressure die casting (HPDC) has several drawbacks in addition to its numerous benefits. The following three main restrictions apply to high-pressure die casting:
Costs of tooling:
For high-pressure die casting, the initial tooling costs might be somewhat substantial. It takes a lot of money to create the molds, or die tooling, that are used to shape and form the molten metal. The complexity and expense of their manufacturing are increased by the molds’ need to endure high pressures and temperatures. Tooling expenses may be a big issue, especially when developing prototypes or limited production runs.
Limited Choice of Alloys:
Alloys that exhibit excellent fluidity and castability at elevated temperatures are often suitable candidates for high-pressure die casting. Due to their advantageous qualities, aluminum and zinc are often employed in HPDC; nevertheless, certain alloys that have poor castability or are prone to porosity at high pressures may not be as well suited for the process. Certain specific alloys could require different casting techniques or adjustments to the process parameters.
Limitations on Part Size:
Smaller to medium-sized components are often better suited for high-pressure die casting. The size and weight of the pieces that can be produced efficiently may be restricted by the machinery and equipment employed in the process. It might be difficult to cast larger, heavier components using high-pressure die casting methods. Other casting techniques, including sand casting or low-pressure die casting, can be better suited for bigger pieces.
It’s crucial to remember that high-pressure die casting is still appropriate for many applications despite these drawbacks. The method is still very useful for producing a variety of components, especially those that need to be produced in huge numbers with a high degree of accuracy and complexity. However, while choosing a casting technique for a particular project, designers and manufacturers should carefully analyze these limits and assess if high-pressure die casting fits with their needs and limitations.
What are the pressures for die casting?
Die casting is a process that creates intricate and precise objects by forcing molten metal under great pressure into a mold chamber. One important factor influencing the speed, integrity, and quality of the casting process is the pressure applied during the die casting process. The material being cast, the size and complexity of the component, and the particular die casting technique (e.g., high-pressure die casting or low-pressure die casting) may all affect the required pressure. The following are typical pressure ranges for several die casting types:
High-Pressure Die Casting (HPDC):
The pressure range often used in high-pressure die casting is 10,000 to 30,000 psi (70 to 200 MPa).
During the injection step, considerable pressure is used to guarantee that the molten metal fills the mold cavity fully and quickly.
Low-Pressure Die Casting (LPDC):
In contrast to high-pressure die casting, low-pressure die casting employs lower pressures.
Generally speaking, pressures in LPDC vary from a few hundred to a few thousand psi (or from 0.07 to 3 MPa).
Throughout the casting process, the lower pressure is maintained, enabling a slower, more deliberate fill of the mold.
Gravity Die Casting:
Melted metal is poured into the mold using gravity in gravity die casting, rather than using a lot of external pressure.
The height at which the molten metal is poured determines the pressure in gravity die casting, which is much lower than in high-pressure die casting.
It’s crucial to remember that the precise pressure needs might change depending on the alloy being cast, the part’s design, and the casting apparatus used. In order to achieve full mold filling, reduce errors, and guarantee the manufacture of castings of superior quality, pressure is an essential element.
The pressure numbers shown here are just suggestions; the actual pressures used in die casting may vary according to the particular needs of the project and the equipment’s capacity. In order to achieve the intended outcomes, casting process optimization requires careful consideration of these characteristics by designers and manufacturers.
Why does high pressure die casting?
For the manufacturing of intricate metal components, high-pressure die casting (HPDC) is used for a number of reasons, chief among them being the benefits it provides in terms of effectiveness, accuracy, and affordability. Here are several main justifications for the widespread usage of high-pressure die casting:
Quick Production:
High-pressure die casting makes it possible to produce intricate pieces quickly and precisely in huge numbers.
The method allows for quick cycle times, which makes it appropriate for large-scale production.
intricate geometries:
For casting complicated, detailed forms with precise features, HPDC is a good fit.
High pressure is used throughout the casting process to guarantee that molten metal fills complex mold cavities, resulting in components with fine details and tight tolerances.
Dimensional Precision:
Excellent dimensional precision and reproducibility are the outcome of maintaining a high pressure during the whole solidification process.
High-pressure die-casting components usually don’t need much further machining.
Slender Walled Areas:
Lightweight components and thin-walled sections may be produced using high-pressure die casting without compromising structural integrity.
Because of this, the procedure may be used in situations when losing weight is essential.
Integridad superior de los materiales:
The cast pieces’ material integrity is improved and porosity is reduced thanks to the high pressure.
Better mechanical qualities, such increased strength and enhanced surface polish, are the outcome of this.
Economical for Large Volumes:
Large production runs make high-pressure die casting cost-effective, despite the potentially expensive initial tooling costs.
The low amount of post-casting machining and high production rates add to the overall cost effectiveness.
Versatility of Alloy:
High-pressure die casting is a flexible process that works with a variety of alloys, the most popular ones being zinc and aluminum.
This makes it possible to choose materials with flexibility in accordance with certain performance criteria.
Diminished Waste:
Reduced scrap and material waste are a result of the die casting process’s great accuracy and control.
The need for extra material reduction is reduced when near-net-shape components may be produced.
Even though high-pressure die casting has several benefits, it’s important to take the particular needs of a given application into account. When selecting the best casting technique, consideration should be given to elements including component size, complexity, production volume, and material qualities.
What type of aluminum is used for die casting?
Good mechanical qualities, outstanding castability, and resistance to the high pressures and temperatures needed in the die casting process define aluminum alloys that are often used in die casting. The following aluminum alloys are most often used in die casting:
1. Aluminum Alloy 380 (A380):
One of the most popular alloys of aluminum for die casting is A380.
It has excellent machining and casting qualities.
Because of its exceptional fluidity, the A380 is a good choice for manufacturing intricate components with thin walls.
2. Aluminum Alloy 383 (A383):
A383 and A380 are comparable, while A383 has better resistance to heat cracking.
It is very useful for die casting complex components because of its increased fluidity.
3. Aluminum Alloy 360 (A360):
High strength, superior resistance to corrosion, and exceptional pressure tightness are attributes of A360.
It is often used for items that need to be machined as well as cast.
4. Aluminum Alloy 413 (A413):
Excellent fluidity and pressure tightness are provided by A413.
It is often applied to components that need to be very durable and resistant to corrosion.
5.Aluminum Alloy 390 (A390):
Excellent corrosion resistance and pressure tightness are two of A390’s best qualities.
It is often used in applications needing high-performance qualities, such as automobile components.
6. Aluminum Alloy 356 (A356):
The popular aluminum-silicon alloy A356 is renowned for its excellent casting qualities and thermal treatability.
It provides an excellent balance of corrosion resistance, ductility, and strength.
7. Aluminum Alloy 319 (A319):
When applications call for more fluidity and pressure tightness than some other alloys, A319 is often used.
The requirements of the application, which include elements like mechanical qualities, corrosion resistance, thermal conductivity, and economic considerations, determine which particular aluminum alloy is best for die casting. Depending on how these qualities need to be balanced for a given part or application, several alloys may be used. It’s also important to remember that new aluminum alloys may eventually be used in die casting applications as a result of developments in die casting technology and alloy development.
¿Cuál es la diferencia entre fundición a presión y fundición a alta presión?
Although die casting and high-pressure die casting are similar techniques, they are often used synonymously. There is a little difference between the two, however. Let’s explain the distinction:
Fundición a presión:
Definition: The technique of pumping molten metal into a mold, or die, to create a particular form or component is known as die casting.
Alternatives: Depending on the pressure used during the casting process, die casting may be roughly divided into several categories. These variations include gravity die casting, low-pressure die casting, and high-pressure die casting.
Pressure Range: Generally speaking, die casting may entail a variety of pressures. There are variations for both high and low pressures.
High-Pressure Die Casting (HPDC):
Definition: The method of die casting in which molten metal is pumped into a mold at high pressures is known as high-pressure die casting.
Features: During the injection phase of an HPDC, pressures usually vary from 10,000 to 30,000 psi (70 to 200 MPa).
Benefits: HPDC is renowned for its quick turnaround times on intricate, high-precision products with superior surface polish and dimensional accuracy.
Materials: often used for alloys made of zinc and aluminum.
To sum up, not all die casting is high-pressure die casting; nonetheless, all die casting is die casting. The phrase “die casting” refers to a group of procedures that include the injection of molten metal into a mold, sometimes at different pressures. High-pressure die casting is a subclass of die casting that focuses on using high injection pressures to obtain certain benefits including high material integrity, quick manufacturing, and complex component geometries.