Moulage sous pression de l'aluminium
Dans le monde de la fabrication, les pièces moulées en aluminium jouent un rôle important en tant que pierre angulaire de la précision et de la durabilité. Ce guide complet se penche sur les subtilités du moulage sous pression de l'aluminium, en détaillant ses applications, ses avantages et son rôle transformateur dans différentes industries.
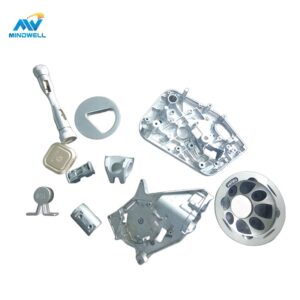
I. L'essence du moulage sous pression de l'aluminium
1.1 Comprendre le processus de moulage sous pression
Le moulage sous pression de l'aluminium est une technologie de fabrication avancée qui consiste à injecter de l'aluminium en fusion dans des moules de précision afin de créer des pièces complexes et précises sur le plan dimensionnel. Ce processus nécessite des compétences hautement spécialisées et un équipement de pointe pour garantir la qualité et la précision du produit final.
Les processus de moulage sous pression de l'aluminium comprend les étapes suivantes :
- Préparation du moule : Il faut d'abord concevoir et fabriquer un moule de précision. Ce moule est généralement fabriqué en acier à haute dureté et peut supporter des températures et des pressions élevées. La conception du moule doit tenir compte des exigences de forme, de taille et de précision du produit.
- Préparation de l'aluminium en fusion : L'aluminium pur ou l'alliage d'aluminium est chauffé jusqu'au point de fusion pour devenir liquide. Ce processus nécessite un contrôle strict de la température afin de garantir la qualité de l'aluminium.
- Injection : L'aluminium en fusion est injecté dans le moule à haute pression. Cette étape nécessite un contrôle précis de la vitesse d'injection et de la pression pour s'assurer que l'aluminium remplit complètement le moule et évite la formation de bulles ou d'autres défauts.
- Refroidissement et solidification : Une fois l'aluminium injecté dans le moule, celui-ci est rapidement refroidi, ce qui permet à l'aluminium de se solidifier rapidement. Cette étape est cruciale pour garantir la résistance et la dureté du produit.
- Démoulage et post-traitement : Lorsque l'aluminium est complètement durci, le moule est ouvert et le produit est retiré. Le produit peut alors nécessiter des étapes de post-traitement, telles que l'ébavurage, le polissage ou le traitement thermique, afin d'obtenir la précision et la qualité de surface finales.
L'avantage du moulage sous pression de l'aluminium est sa capacité à produire des pièces de formes complexes et de dimensions précises, et son efficacité de production est élevée. En outre, en raison de la légèreté de l'aluminium, de sa conductivité électrique et de sa résistance à la corrosion, les pièces moulées sous pression en aluminium sont largement utilisées dans de nombreuses industries, telles que l'automobile, l'aérospatiale, l'électronique et l'éclairage.
1.2 Le rôle de l'aluminium dans le moulage sous pression
L'aluminium moulé sous pression a été choisi pour ses propriétés supérieures, notamment sa conductivité thermique élevée, sa légèreté et sa polyvalence pour les conceptions complexes. Ces propriétés font que l'aluminium moulé sous pression est largement utilisé dans des industries telles que l'automobile, l'aérospatiale, l'électronique et l'éclairage. Ces caractéristiques de performance sont détaillées ci-dessous.
Conductivité thermique élevée
La conductivité thermique élevée de l'aluminium moulé sous pression est l'un de ses principaux avantages. L'aluminium est un bon matériau conducteur de chaleur, avec une conductivité thermique élevée. Au cours du processus de moulage sous pression, l'aluminium en fusion remplit le moule et, après refroidissement et solidification, forme un composant doté d'une bonne conductivité thermique. Cette conductivité thermique élevée fait de l'aluminium moulé sous pression un avantage significatif dans les scénarios où une dissipation efficace de la chaleur est nécessaire. Par exemple, dans les lampes LED, la chaleur générée par la puce LED devant être dissipée rapidement pour maintenir des performances stables et prolonger la durée de vie, la conductivité thermique élevée de l'aluminium moulé sous pression est devenue un choix idéal pour la fabrication des lampes LED.
Légèreté
La légèreté de l'aluminium moulé sous pression est un autre avantage important. L'aluminium est un matériau métallique relativement léger et de faible densité. Au cours du processus de moulage sous pression, l'aluminium remplit le moule et se solidifie, ce qui permet d'obtenir une pièce plus légère. Cette légèreté fait de l'aluminium moulé sous pression un avantage significatif dans les applications où une réduction du poids est nécessaire. Par exemple, dans la construction automobile, le poids total du véhicule doit être réduit afin d'améliorer l'économie de carburant et de réduire les émissions. La légèreté de l'aluminium moulé sous pression lui permet d'être utilisé pour fabriquer des pièces automobiles, telles que des blocs-moteurs, des culasses, etc.
Polyvalence dans les conceptions complexes
La polyvalence des conceptions complexes de l'aluminium moulé sous pression est son troisième avantage important. Grâce à des processus précis de conception et de fabrication de moules, il est possible de fabriquer des pièces métalliques aux formes complexes, aux contours clairs, aux parois minces et aux cavités profondes. Cette capacité de conception sophistiquée permet à l'aluminium moulé sous pression d'être très flexible dans le processus de fabrication et de répondre à une variété de besoins de conception complexes. Par exemple, dans le domaine aérospatial, il est nécessaire de fabriquer des pièces de forme et de structure complexes, telles que des pièces de moteur d'avion, des pièces de structure de vaisseau spatial, etc. Les capacités de conception sophistiquées de l'aluminium moulé sous pression lui permettent de répondre à ces demandes et de produire des pièces de haute qualité et de haute performance.
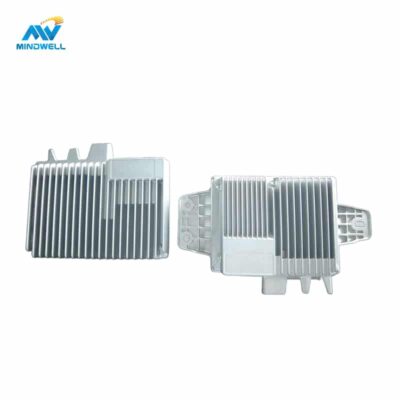
Table des matières
II. Les avantages dévoilés
2.1 Efficacité thermique pour une meilleure performance
L'aluminium possède d'excellentes capacités de dissipation de la chaleur, ce qui lui permet d'évacuer rapidement la chaleur du moule pendant le processus de moulage sous pression. Cette capacité à dissiper la chaleur est importante pour garantir que la pièce moulée sous pression reste à une température optimale, car elle réduit les différences de température à l'intérieur du produit et évite tout problème potentiel dû à une surchauffe.
Dans de nombreuses applications, en particulier celles qui impliquent des équipements électroniques de grande puissance ou des applications nécessitant un fonctionnement à long terme, comme les moteurs automobiles, les luminaires à LED, etc., les capacités de contrôle de la température et de dissipation de la chaleur au sein du produit sont essentielles pour garantir des performances et une fiabilité optimales du produit. . La surchauffe d'un composant peut entraîner une dégradation des performances, un vieillissement accéléré, voire une défaillance.
Cependant, en utilisant la technologie de moulage sous pression de l'aluminium, il est possible de créer des pièces dotées de capacités de dissipation thermique efficaces. En effet, l'aluminium possède une conductivité thermique élevée et est capable de conduire la chaleur rapidement. Au cours du processus de moulage sous pression, l'aluminium en fusion remplit le moule et se refroidit et se solidifie rapidement, formant ainsi des pièces ayant une bonne conductivité thermique. Cette dissipation efficace de la chaleur contribue à prolonger la durée de vie du produit et à améliorer sa fiabilité et ses performances.
2.2 Une construction légère pour plus de polyvalence
La légèreté de l'aluminium le rend non seulement facile à travailler, mais lui confère également de nombreux avantages fonctionnels, notamment en termes d'efficacité énergétique, d'économies de matériaux, d'optimisation de la conception et d'options respectueuses de l'environnement. Ces avantages font de l'aluminium un matériau idéal pour de nombreuses applications, que ce soit dans les secteurs de l'automobile, de l'aérospatiale, de l'électronique ou de l'éclairage, où les pièces moulées sous pression en aluminium sont largement utilisées pour répondre à divers besoins. Voici quelques détails sur la polyvalence des constructions légères en aluminium :
- Efficacité énergétique : La légèreté de l'aluminium permet de réduire la consommation d'énergie pendant le transport. Qu'ils soient transportés par voie terrestre ou aérienne, les produits en aluminium, de par leur légèreté, permettent de réduire les coûts de transport et donc l'impact sur l'environnement.
- Économies de matériaux : En raison de la faible densité de l'aluminium, il est possible d'économiser des matériaux au cours du processus de fabrication. Cela permet non seulement de réduire les coûts de production, mais aussi de limiter le gaspillage des ressources, ce qui est conforme au principe du développement durable.
- Conception optimisée : Les propriétés de légèreté de l'aluminium permettent aux concepteurs de concevoir des produits plus souples. Ils peuvent se concentrer davantage sur la fonctionnalité et les performances du produit sans se soucier d'un poids excessif. Cette flexibilité permet aux produits en aluminium d'exceller dans une grande variété d'applications.
Environnement - Un choix respectueux de l'environnement : L'aluminium est un matériau recyclable, il peut donc être recyclé et réutilisé après usage, ce qui réduit l'impact sur l'environnement. Cette recyclabilité fait de l'aluminium un choix écologique qui répond aux exigences du développement durable.
2.3 Ingénierie de précision pour les conceptions complexes
La technologie du moulage sous pression permet de produire des pièces métalliques aux formes complexes, aux contours clairs, aux parois minces et aux cavités profondes, ce qui est difficile à réaliser avec d'autres méthodes de fabrication. Les capacités d'ingénierie de précision de cette conception complexe donnent à l'aluminium moulé sous pression un avantage significatif pour répondre aux besoins changeants d'une variété d'industries.
Dans certaines industries, telles que l'aérospatiale, la construction automobile et la fabrication d'équipements électroniques, la précision et la complexité des composants sont essentielles. Ces industries doivent fabriquer des pièces de haute précision, résistantes et de formes complexes pour répondre à des exigences de performance et à des normes de sécurité spécifiques.
La technologie du moulage sous pression permet de fabriquer des pièces de haute précision grâce à des processus de conception et de fabrication de moules précis. Au cours du processus de moulage sous pression, l'aluminium en fusion est versé dans un moule et, après refroidissement et solidification, forme des pièces de la forme et de la taille souhaitées. Cette capacité de fabrication de précision permet à l'aluminium moulé sous pression de répondre aux exigences de précision et de complexité de ces industries.
En outre, la technologie du moulage sous pression permet également de produire des pièces à parois minces et à cavités profondes, ce qui est difficile à réaliser avec d'autres méthodes de fabrication. Cette conception à parois minces et à cavités profondes peut offrir une meilleure résistance et une plus grande rigidité tout en réduisant la quantité de matériau utilisé, ce qui permet de réduire encore les coûts et la consommation de ressources.
En résumé, la technologie du moulage sous pression permet de créer des modèles complexes et précis qui répondent aux besoins en constante évolution d'une industrie qui exige la précision de chaque pièce. Les capacités d'ingénierie de précision de cette conception complexe ont conduit à l'utilisation généralisée de l'aluminium moulé sous pression dans l'aérospatiale, la construction automobile, la fabrication d'équipements électroniques et d'autres industries.
Pièces moulées en aluminium sur mesure, Mindwell est votre choix de confiance
III. Applications dans tous les secteurs d'activité
3.1 Secteur automobile
Les pièces moulées sous pression en aluminium sont largement utilisées dans l'industrie automobile, couvrant de nombreux domaines clés tels que les systèmes de moteur, les systèmes de suspension et les châssis, les structures de carrosserie et les systèmes électriques. Elles fournissent des pièces légères, très résistantes et résistantes à la corrosion pour les véhicules, améliorant ainsi leur consommation de carburant, leurs performances et leur fiabilité. Voici la gamme détaillée des applications des pièces moulées sous pression en aluminium dans l'industrie automobile :
- Système de moteur : Les pièces moulées sous pression en aluminium jouent un rôle important dans les systèmes de moteur. Elles peuvent être utilisées pour fabriquer des composants critiques tels que les blocs moteurs, les culasses et les carters. Ces composants doivent résister à des températures et des pressions élevées, ainsi qu'à des mouvements à grande vitesse, et requièrent donc une grande solidité et une bonne résistance à la corrosion. Les pièces moulées sous pression en aluminium sont idéales pour la fabrication de ces pièces en raison de leurs excellentes propriétés mécaniques et de leur résistance à la corrosion.
- Système de suspension et châssis : Les pièces moulées sous pression en aluminium sont également largement utilisées dans les systèmes de suspension et les châssis. Elles peuvent être utilisées pour fabriquer divers composants des systèmes de suspension, tels que les bras de suspension, les bras de commande et les rotules de direction. Ces composants doivent résister à des forces et à des mouvements complexes et nécessitent donc une résistance et une rigidité élevées. Les pièces moulées sous pression en aluminium sont idéales pour la fabrication de ces pièces en raison de leur légèreté et de leurs excellentes propriétés mécaniques.
- Structure de la carrosserie : Les pièces moulées sous pression en aluminium sont également utilisées pour fabriquer divers composants de la structure de la carrosserie, tels que les portes, les capots, les cadres de carrosserie, etc. Ces composants doivent être légers, solides et résistants à la corrosion afin de réduire la consommation de carburant et d'améliorer la sécurité. Les pièces moulées sous pression en aluminium sont idéales pour la fabrication de ces pièces en raison de leur légèreté et de leurs excellentes propriétés mécaniques.
- Système électrique : Les pièces moulées sous pression en aluminium sont également utilisées pour fabriquer divers composants de systèmes électriques, tels que des boîtiers de batterie, des boîtiers de moteur, etc. Ces composants doivent être légers, très solides et résistants à la corrosion pour offrir de meilleures performances électriques et une plus grande fiabilité. Les pièces moulées sous pression en aluminium sont idéales pour la fabrication de ces pièces en raison de leur légèreté et de leurs excellentes propriétés mécaniques.
3.2 Électronique et technologie
Alu die castings are also widely used in electronic equipment, mainly involving casing and chassis manufacturing, radiator manufacturing, and antenna manufacturing. They provide lightweight, high-strength and corrosion-resistant parts for electronic equipment, improving the performance and reliability of the equipment, mainly involving the following aspects:
- Housing and chassis manufacturing: Aluminum die castings are often used to manufacture housings and chassis for electronic equipment. These components need to be lightweight, high-strength and corrosion-resistant to provide better protection and stability. Aluminum die castings are ideal for manufacturing these parts due to their excellent mechanical properties and corrosion resistance.
- Radiator manufacturing: Electronic equipment generates a lot of heat when working, so heat dissipation is an important issue. Aluminum die castings have excellent thermal conductivity and can quickly conduct and dissipate heat, helping to keep the temperature of the equipment within a safe range. Therefore, aluminum die castings are also often used to manufacture heat sinks for electronic equipment.
- Antenna manufacturing: Antennas in electronic devices also need to be lightweight, high-strength and corrosion-resistant. Aluminum die castings are ideal for manufacturing these parts due to their excellent mechanical properties and corrosion resistance.
3.3 Consumer Goods
Aluminum die castings are widely used in consumer products, from kitchen appliances to handheld devices, and their versatility ensures seamless integration of components in a variety of consumer products. Here are some applications of aluminum die castings in consumer products:
- Kitchen utensils: Aluminum die castings are widely used in kitchen utensils, such as pressure cookers, steamers, ovens, etc. These appliances need to withstand high temperatures and pressures, so they need to have high strength and corrosion resistance. Aluminum die castings are ideal for manufacturing these appliances due to their excellent mechanical properties and corrosion resistance. In addition, aluminum die castings are also used to manufacture components such as kitchen faucets and water pipes, which need to have good corrosion resistance and environmental protection.
- Handheld devices: Aluminum die castings are also widely used in handheld devices, such as mobile phones, tablets, digital cameras, etc. These devices require lightweight, high strength and corrosion resistance to provide a better operating experience and reliability. Aluminum die castings are ideal for manufacturing the housings of these devices due to their light weight and excellent mechanical properties. At the same time, aluminum die castings are also used to manufacture internal mechanical components, such as camera brackets, buttons, etc.
- Personal care products: Aluminum die castings are also widely used in personal care products, such as electric toothbrushes, razors, etc. These products require lightweight, high strength and corrosion resistance to provide a better user experience and reliability. Aluminum die castings are ideal for manufacturing the housings of these products due to their light weight and excellent mechanical properties.
- Sports equipment: Aluminum die castings are also widely used in sports equipment, such as bicycles, scooters, etc. These equipment require lightweight, high strength and corrosion resistance to provide better performance and user experience. Aluminum die castings are ideal for manufacturing frames and components for these equipment due to their light weight and excellent mechanical properties.
IV. The Production Journey
4.1 Mold Creation and Injection
The die-casting process begins with the creation of a mold, followed by a precise injection of molten aluminum to form components with unmatched precision. Here is a detailed introduction to mold creation and injection:
Tool creation
- Design stage: First, based on product requirements and design requirements, the designer will create a 3D model. This model will determine the product’s shape, size and all details.
- Mold manufacturing: Next, high-quality mold steel materials are used to manufacture the mold based on the 3D model. Molds usually consist of two main parts: upper mold and lower mold. The upper mold is used to form the external shape of the product, while the lower mold is used to form the internal shape of the product.
- Mold trial stage: Before formal production, a trial mold is usually conducted. At this stage, the mold is checked for accuracy, flowability, and other key parameters. If any problems are discovered, the mold can be adjusted and repaired in time.
injection stage
- Molten Aluminum Preparation: Put the aluminum block into the smelting furnace and heat it to the melting point, then convert it into molten aluminum. This process requires precise control of temperature and time to ensure the quality of the molten aluminum.
- Injection process: When the molten aluminum is ready, it is injected into the mold through the pipe. During this process, the injection speed, pressure and temperature need to be precisely controlled to ensure that the aluminum liquid can evenly fill all parts of the mold.
- Cooling and demolding: After the molten aluminum has cooled and solidified in the mold, the demolding operation can be performed. This process is required to ensure product integrity and avoid any possible damage.
- Post-processing: After demoulding, the product may need some post-processing, such as grinding, polishing, etc., to obtain the desired appearance.
Throughout the process, precision and quality control are crucial. Through precise mold design and manufacturing, along with precise injection processes, die castings can be manufactured with unparalleled precision. These parts often offer high strength, corrosion resistance and good thermal conductivity, making them ideal for a variety of applications.
4.2 Precision Machining and Finishing
Die-cast components often require further processing to ensure they meet precise specifications and to enhance their durability and aesthetics. The following is a detailed introduction to precision machining and finishing:
Usinage de précision
Rough machining: After the die casting is complete, the part may need to be rough machined. This basically involves removing excess material to achieve the desired shape and size. Rough machining can include operations such as cutting, drilling, milling, etc.
Finishing: Compared to roughing, finishing is more detail-oriented and precise. This may include operations such as grinding, polishing, fine milling, etc., to further refine the surface of the part and ensure that its shape and size exactly match the design requirements.
The significance of finishing
Finishing not only increases the accuracy of the part, but also enhances its aesthetics and durability. For example, by polishing or grinding, defects on the surface of a part can be removed, making its surface smoother, thus improving its wear and corrosion resistance. At the same time, finishing can also improve the appearance quality of the parts, making them more beautiful.
Finishing techniques
In order to achieve precision machining, advanced processing equipment and processes are required. For example, CNC machine tools, grinding machines, polishing machines, etc. are all commonly used finishing equipment. In addition, in order to ensure machining accuracy, high-precision tools and fixtures are also required.
Conclusion
Precision machining and finishing are important steps after die casting to ensure the accuracy, aesthetics and durability of the part. Through the use of advanced equipment and processes, high-precision parts manufacturing can be achieved to meet the needs of various applications.
V. Quality Assurance Measures
5.1 Non-Destructive Testing
Non-Destructive Testing (NDT for short) is a method that uses sound, light, magnetism, electricity and other characteristics to detect whether there are defects or unevenness in the object without damaging the performance of the object. , a general term for all technical means that provide information on the size, location, nature and quantity of defects, and then determine the technical status of the inspected object (such as qualified or not, remaining life, etc.).
At Mindwell Company, we use non-destructive testing for every die-cast component. The following is a detailed introduction to non-destructive testing:
Purpose of non-destructive testing: The main purpose of non-destructive testing is to detect internal and surface defects in die-cast components without damaging or changing them. These defects may be cracks, pores, inclusions, etc., which can affect the performance and service life of the component.
Commonly used non-destructive testing methods: In the die-casting industry, common non-destructive testing methods include ultrasonic testing (UT), radiographic testing (RT), magnetic particle testing (MT) and penetrant testing (PT). Each method has its specific application scope and advantages and disadvantages.
Ultrasonic testing (UT): Utilizes the propagation characteristics of ultrasonic waves in materials to detect defects. This method can detect defects such as cracks and pores inside die-cast parts.
Radiographic Inspection (RT): Uses X-rays or gamma rays to penetrate die-cast parts and identify defects by detecting transmitted or scattered rays. This method is suitable for detecting defects such as inclusions and shrinkage cavities inside castings.
Magnetic Particle Inspection (MT): This is done by applying a magnetic field to the surface of a die-cast part and using magnetic particles to reveal defects. This method is suitable for detecting surface or near-surface defects such as cracks.
Penetrant Testing (PT): Using a penetrant to penetrate into defects on the surface of the die-cast part, and then using a developer to draw the penetrant out and reveal the defects. This method is suitable for detecting defects with surface openings.
Advantages of non-destructive testing: Non-destructive testing methods offer the following advantages:
Non-destructive: Testing can be carried out without damaging or changing die-cast parts, avoiding the waste and cost of traditional destructive testing.
High Accuracy: Modern non-destructive testing technology has extremely high accuracy and resolution and can accurately identify minute defects.
Comprehensiveness: Die-cast parts can be fully inspected, including internal and external defects, to ensure the overall quality of the product.
Applications of non-destructive testing: At Mindwell we mainly use it in the following aspects:
- Quality Control: During the production process, die-cast parts are inspected non-destructively to ensure they meet quality standards.
- Product Acceptance: Before product delivery, die-cast parts are subjected to final non-destructive testing to confirm that they meet customer needs and specifications.
- Failure analysis: When a die-cast part fails, non-destructive testing technology can be used to analyze the cause and nature of the failure.
In short, non-destructive testing is one of the important means to ensure the quality of die-cast components. By employing appropriate non-destructive testing methods and techniques, our company can accurately detect defects in die-cast parts, ensuring that each component meets the highest quality standards.
5.2 Dimensional Inspections
Mindwell’s dimensional inspection of die castings is a very important quality control step. Dimensional inspection can verify whether the die casting meets the design requirements and ensure its dimensional accuracy and consistency.
When performing dimensional inspection, measuring tools such as calipers, micrometers, measuring instruments, etc. are usually used to accurately measure various dimensions of die castings. These measurements are compared to the values specified on the design drawing to determine if the die cast meets specifications.
The purpose of dimensional inspection is to ensure the dimensional consistency and accuracy of die castings. If there are dimensional deviations in a die cast part, it can cause assembly issues, performance issues, or quality issues. Therefore, these problems can be discovered and corrected in time through dimensional inspection, ensuring reliable and consistent quality of die castings.
In order to improve the accuracy and efficiency of dimensional inspection, Mindwell may use advanced measuring equipment and measurement technology. These equipment and technologies can provide high-precision measurement results, reduce human errors, and improve detection efficiency.
In short, Mindwell’s dimensional inspection of die castings is one of the important means to ensure product quality. Through strict dimensional inspection, you can ensure that die castings meet design requirements, improve product reliability and consistency, and thus meet customer needs and specifications.
VI. Customization in Alu Die Casting
6.1 Tailoring Solutions for Varied Industries
Mindwell’s ability to tailor solutions for various industries is one of its core competencies. Through an in-depth understanding of industry needs, custom design, manufacturing capabilities and continuous optimization, Mindwell is able to provide customers with high-quality, high-performance custom die-cast parts that meet the specific needs of specific industries. . The ability to customize die-cast parts allows manufacturers to meet the specific needs of specific industries, ensuring a tailor-made solution.
The following is a detailed introduction to Mindwell’s customized solutions for various industries:
- Deep understanding of industry needs: Mindwell works closely with various industries to gain a deep understanding of their needs and challenges. This includes knowledge of industry standards, regulatory requirements, performance requirements and more. By working closely with customers, Mindwell is able to accurately grasp industry needs and trends.
- Customized design: Based on an in-depth understanding of industry needs, Mindwell is able to provide customers with customized design solutions. This includes customization of die-cast parts in terms of shape, size, material selection, surface treatment, and more. By working with the client’s design team, Mindwell is able to ensure that the design meets the client’s specific needs.
- Manufacturing capabilities: Mindwell has advanced die-casting equipment and manufacturing technology to ensure the manufacturing of high-quality custom die-cast parts. During the manufacturing process, Mindwell strictly controls every aspect, including mold design, raw material selection, smelting, die-casting, post-processing, etc., to ensure high precision and high quality of parts.
- Continuous optimization: During the customization process, Mindwell maintains close communication with customers and provides timely feedback and adjustments to the design plan. Through continuous optimization, Mindwell is able to ensure that customized die-cast parts meet customer expectations and requirements, and to continuously improve product performance and reliability.
- Providing a full range of services: In addition to customizing die-cast parts, Mindwell also provides customers with a full range of services, including product testing, quality assurance, technical support, etc. These services ensure customers receive optimal performance, reliability and reduced operating costs when using custom die-cast parts.
6.2 Impact on Design and Functionality
Customization has a positive impact on the design and functionality of die-cast products. It not only meets specific functional requirements, but also improves design aesthetics and personalized touch, bringing higher added value and market competitiveness to die-cast products.
- Meet functional requirements: The primary purpose of customization is to meet specific functional requirements. Different industries and application scenarios have different functional requirements for die castings. Through customization, you can ensure that die castings fully meet specific functional requirements in terms of shape, size, strength, wear resistance, etc. This precise matching ensures that the die cast parts will perform optimally in the actual application.
- Improvement of design aesthetics: Customization not only focuses on functional requirements, but also on design aesthetics. The look and feel of die-cast products is an important part of the user experience. Through customization, designers can get creative with shapes, lines, finishes, and more to create a unique and attractive look. This not only improves the visual beauty of the product, but also increases user recognition and satisfaction.
- Personalized touch: Customization provides a personalized touch to die-cast products. Through different surface treatment processes, such as polishing, sandblasting, electroplating, etc., die castings can be given different textures and touches. This personalized touch not only adds to the uniqueness of the product, but also enhances the user experience.
- Space for innovation: Customization provides designers with greater space for innovation. On the basis of meeting functional requirements, designers can try new design elements and creative concepts to create unique die-cast products. This kind of innovation can not only meet the diverse needs of the market, but also help enhance brand image and product competitiveness.
- Flexible adjustment and optimization: During the customization process, designers can flexibly adjust and optimize based on customer feedback and market demand. This flexibility ensures that the product can closely match actual usage scenarios and user needs, improving product practicality and satisfaction.
VII. Sustainability Initiatives
7.1 Material Efficiency and Waste Reduction
Alu die-casting is a manufacturing process whose sustainability is primarily in terms of material efficiency and waste reduction. Here is a detailed introduction to these two aspects:
Material efficiency:
Optimized design: Through accurate design and engineering analysis, materials can be maximized and waste reduced. For example, optimizing the design of die-casting parts to make them more in line with the characteristics of the die-casting process, thereby reducing material use and energy consumption during the production process.
Recycling and reuse: For die castings that have been used, the consumption of new materials can be reduced through recycling and reuse. For example, scrap aluminum die castings are recycled and reused to produce new die castings after processing.
Use high-strength materials: Using high-strength, lightweight materials can reduce the amount of material used in the manufacturing process while improving the strength and durability of your product.
Waste reduction:
Reduce scrap rate: By optimizing the production process and using advanced mold technology, the scrap rate generated during the production process can be reduced. This not only reduces waste but also reduces production costs.
Environmentally friendly manufacturing processes: The impact on the environment can be reduced by adopting environmentally friendly manufacturing processes, such as using environmentally friendly coatings and additives, and using energy-efficient equipment.
Properly arrange the production plan: By properly arranging the production plan, overproduction and inventory backlog can be avoided, thus reducing waste and storage costs.
Waste recycling: Waste generated during the production process can be processed through recycling. For example, scrap aluminum die castings are recycled, processed and reused to produce new die castings.
Through the above measures, the aluminum die-casting process can reduce the impact on the environment while improving manufacturing efficiency. This sustainable manufacturing process helps drive the development of green manufacturing and a circular economy.
7.2 Recycling Possibilities
The recyclability of aluminum die-casting is an important part of its sustainability and is in line with sustainability goals. Here’s a closer look at the recycling possibilities for aluminum die casting:
Recyclability of Aluminum:
Aluminum is a very recyclable material. It has the characteristics of corrosion resistance, easy processing and wide application, so it is widely used in many fields, including construction, automobile, electronics, etc. Recycling of aluminum can reduce reliance on natural resources, lower production costs, and reduce environmental impact.
Recyclability of die-casting parts:
- Recycling of waste die-casting parts: Wasted aluminum die-casting parts can be disposed of through recycling and reuse. The recycling process involves steps such as crushing, screening, and smelting die castings, which are then reused to make new die castings. Not only does this reduce the need for raw materials, it also reduces production costs.
- Recycling of die-casting molds: In the die-casting process, the mold is an important consumable. Used molds can also be recycled and reused. The recycled molds are repaired and reprocessed and can be reused to produce new die-cast parts.
Opportunities to practice environmentally friendly practices:
- Promote the circular economy: Through the recycling and reuse of aluminum die-casting, we can promote the development of the circular economy. Circular economy emphasizes the effective use of resources and the reduction and recycling of waste. The recycling and reuse of aluminum die-casting is in line with this concept.
- Reduce carbon emissions: The recycling and reuse of aluminum die castings can reduce the need for raw materials, thus reducing carbon emissions during the production process. This has important implications for combating climate change and achieving the Sustainable Development Goals.
- Improve resource efficiency: Through the recycling and reuse of aluminum die-casting, the efficiency of resource utilization can be improved and the consumption of natural resources can be reduced. This plays a positive role in protecting the environment and promoting sustainable development.
In conclusion, the recyclability of alu die-casting provides opportunities for its sustainability. Recycling and reusing used die-casting parts and molds can reduce the need for raw materials, reduce production costs, and reduce environmental impact. This is in line with sustainable development goals and provides opportunities for environmentally friendly practices in the die casting sector.
In conclusion
In conclusion, this guide sheds light on the multifaceted world of aluminum die casting. From precision engineering to multifunctional applications and sustainability initiatives, aluminum die casting continues to shape the industry and pave the way for a future of innovation and efficiency. Mindwell has also been committed to promoting the development of industrial manufacturing along the way. We have more than ten years of experience in the aluminum die-casting industry, and we hope to continue to contribute to the aluminum die-casting industry.
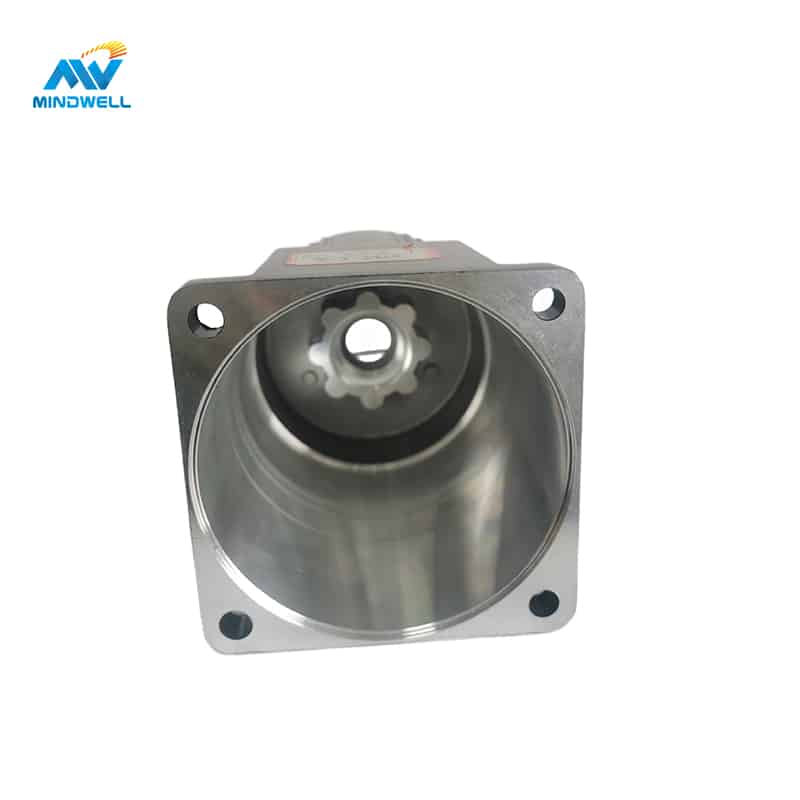
Are alu die castings suitable for all industries?
Aluminum alloy die castings are widely used in many industries due to their lightweight, high strength, corrosion resistance and other properties. For example:
- Automotive industry: Aluminum alloy die castings are used to manufacture automobile engines, chassis, bodies and other components. They have the advantages of lightweight, improved fuel economy, and reduced emissions.
- Electronics industry: Aluminum alloy die castings are used to manufacture housings, radiators, connectors, etc. for electronic equipment and have excellent electrical conductivity and heat dissipation properties.
- Consumer goods industry: Aluminum alloy die-casting parts are used to manufacture shells and structural parts of consumer goods such as household appliances, toys, and fitness equipment. They are beautiful, durable, and environmentally friendly.
Therefore, it can be said that aluminum alloy die castings are suitable for all industries that require lightweight, high strength, corrosion resistance and other properties.
How does aluminum contribute to the sustainability of die casting?
As a recyclable material, aluminum has the following advantages in the die-casting process, helping to achieve sustainable manufacturing:
- Recyclability: Aluminum is a recyclable material that can be used over and over again, reducing the need for raw materials. By recycling and reusing scrap aluminum die castings, production costs can be reduced and the impact on the environment can be reduced.
- Energy saving and emission reduction: Aluminum has a low density and requires relatively little energy during the die-casting process. In addition, aluminum has good thermal conductivity, which helps to quickly cool molds and parts, shorten production cycles, and reduce energy consumption.
- Environmental protection: Waste gas, waste water, waste residue and other waste generated during the aluminum die-casting process can be recycled and reused through effective treatment measures to reduce the impact on the environment.
Aluminum therefore has significant advantages in promoting the sustainability of die casting.
Can die cast parts be customized for specific applications?
Yes, die cast parts can be customized for specific applications. By changing the design and manufacturing process of the mold, die castings of different shapes, sizes and properties can be produced. In addition, the strength, hardness, corrosion resistance and other properties of die castings can be improved by changing the material composition and adding alloy elements to meet the requirements of specific applications.
What measures are taken to ensure the quality of die castings?
In order to ensure the quality of die castings, the following measures can be taken:
- Strict quality control: Establish a complete quality control system to strictly monitor and test all aspects of the die-casting process to ensure that product quality meets standards.
- Non-destructive testing: Use non-destructive testing technology to conduct comprehensive testing of die-casting parts, including appearance, size, internal structure, etc., to ensure that the product is free of defects and defects.
- Mold design and manufacturing: The design and manufacturing quality of the mold directly affect the quality of die castings. Therefore, it is necessary to adopt advanced mold design and manufacturing technology to ensure the accuracy and stability of the mold.
- Raw material control: Strictly control the quality and composition of raw materials to ensure that they meet standard requirements.
- Production process control: Optimize production process parameters to ensure that parameters such as temperature, pressure, and time during the production process meet standard requirements.
- Employee training: Strengthen employees’ quality awareness and skills training, and improve employees’ understanding of product quality and operating skills.
Through the comprehensive application of the above measures, the quality of die castings can be effectively guaranteed.