Low-pressure die-casting is one of the commonly used die-casting processes in aluminum alloy die-casting. Compared with high-pressure die-casting, it has the characteristics of low cost and can manufacture large parts. In low-pressure die casting, if you do not master the low-pressure die-casting technology, there will be some defects. Let’s take a look at the 9 major defects that will occur in low-pressure die-casting and how to prevent them
Stomata
1.feature
(1) stomata
Pore-type defects formed by gas inside the casting. Its surface is generally smooth, mainly pear-shaped, round or oval. Generally not exposed on the surface of the casting, the large holes often exist in isolation, and the small holes appear in groups.
(2) Subcutaneous stomata
Dispersed porosity located under the casting skin. Reactive pores produced by the chemical reaction between molten metal and sand molds (molds, wet cores, coatings, chilled iron with dirty surfaces). The shapes are needle-like, tadpole-like, spherical, pear-like, etc. Varying in size and depth. Usually found after machining or heat treatment.
(3) Air pockets (air pit surface pores)
A smoother air hole is recessed in the surface of the casting.
(4) air shrinkage cavity
Cavity casting defects formed by the combination of dispersed pores, shrinkage cavities and shrinkage porosity.
(5) pinhole
Generally, it is the precipitated pores with the size of needles distributed on the cross section of the casting. Such pores often appear in aluminum alloy castings, which are very harmful to the performance of castings.
- ① Point-shaped pinholes: This kind of pinholes are dot-shaped in low-magnification microstructure, with clear outlines and unconnected. The number of pinholes per square centimeter can be counted and the diameter of the pinholes can be measured. This type of pinhole is easy to distinguish from shrinkage cavity and shrinkage porosity. Point pinholes are formed by bubbles precipitated during solidification of castings, and mostly occur in castings with a small crystallization temperature range and good feeding capacity, such as ZL102 alloy castings. When the solidification rate is fast, point-like pinholes will also appear in the ZL105 alloy castings that are far away from the eutectic composition.
- ② Reticular pinholes: This kind of pinholes are densely connected into a network in the low-magnification microstructure, accompanied by a small number of larger holes, it is difficult to count the number of pinholes, it is difficult to measure the diameter of the pinholes, and often have ends , commonly known as “fly feet”. For alloys with a wide crystallization temperature, the gas precipitated during slow solidification of the casting is distributed on the grain boundaries and in the developed dendrite gaps. Mesh pinholes.
- ③ Mixed pinholes: This kind of pinholes are mixed with dot pinholes and mesh pinholes, which are often found in castings with complex structures and uneven wall thickness. Pinholes can be graded according to national standards. The worse the grade, the lower the mechanical properties of the casting, and the worse its corrosion resistance and surface quality. When the pinhole level allowed by the technical conditions of the casting is not reached, the casting will be scrapped, and the mesh pinhole splits the alloy matrix, which is more harmful than the point pinhole.
(6) Surface pinholes
Scattered pores distributed in groups on the surface of the casting. Its characteristics and causes are the same as those of subcutaneous pores, which are usually exposed on the surface of castings and can be removed after machining 1 to 2 mm.
(7) Choke fire (choke hole)
A large amount of gas generated during the pouring process cannot be discharged smoothly, and boiling occurs in the molten metal, resulting in a large number of pores in the casting, and even incomplete casting defects.
2.Classification of stomata
(1) Precipitation pores
This kind of pores are evenly distributed in the areas with high temperature near the gate, riser, hot joint, etc. The pores are small and scattered, and often coexist with shrinkage cavities. Precipitation: That is, the aluminum water contains gas, which is not completely removed and precipitates during the solidification process.
(2) Reactive pores
Such pores are evenly distributed on the contact surface between the mold wall and the casting. The surface of the pores is smooth, silvery white (cast steel), metallic bright or dark. Reaction: Molds, cores, cold irons, paints, etc. contain substances that react with aluminum water to generate gas.
(3) Invasive stomata
These pores are distributed in the upper part of the casting, and the pores are large and smooth. Intrusion: The gas in the cavity is not discharged out of the mold in time and invades into the casting.
3.Pore formation mechanism
The mold of low-pressure casting is basically sealed, and the molten metal fills the mold faster, and the gas has no time to discharge, and the bag forms pores or pinholes in the casting.
- Precipitation of dissolved gas in the molten metal—precipitation pores (pinholes), the gas contained in the melting of the metal, when the liquid metal cools and solidifies, the gas is precipitated due to the decrease in the solubility of the gas, and it is too late to remove it, resulting in pores in the casting . Gas in molten aluminum has high inclusion content, poor refining effect, and low solidification speed of castings. the
- Wet core, paint, cold iron with unclean surface, gas generated after pouring and heating – reactive pores (subcutaneous pores), pores produced by chemical reaction between mold wall material and liquid metal or inside liquid metal .
- The gas in the cavity is not discharged out of the mold in time – intrusive pores (single large pores), due to unreasonable casting process design, such as poor exhaust of the mold or core, or due to careless operation, If the gas hole is blocked during pouring (pouring speed is too fast), the gas in the cavity is caused by being trapped in the casting.
4.Prevention measures
Strictly implement the smelting operation rules, avoid metal liquid inhalation, and carefully degas. Prevent exudative pores
- Metal raw materials and recycled materials should be dry, free from rust, oil, etc., and should be preheated before use.
- The melting temperature should not be too high. The higher the melting temperature of molten metal, the more gas (mainly hydrogen) dissolved in it. Therefore, the melting temperature should be strictly controlled, especially for non-ferrous alloys.
- The smelting time of any kind of metal should be shortened as much as possible, in case the smelting time is too long to increase the gas absorption of the liquid metal. A factory produces aluminum-iron-manganese brass castings, which are melted and released in 2.5 hours. The airtightness is all qualified; but the castings poured after 6 hours of melting and clearing out of the furnace, under the premise of the same process, all the castings are scrapped due to unqualified airtightness. When the melting time is restored, the airtightness of the castings is all qualified, which fully shows the influence of the length of melting time on the airtightness of the castings.
- Alloys containing aluminum should not be smelted in a power frequency furnace as much as possible, because the stirring ability of this furnace is extremely strong, and aluminum is easily oxidized into Al2O3 when it contacts with air, and enters the liquid metal to become slag, which also provides a source for the precipitation of gas. Chance. At the same time, it is also easy to react with H2O, so that the liquid metal can absorb hydrogen H2. If you use a resistance reverberatory furnace, a far-infrared heating furnace, or even a reverberatory furnace with oil or gas, it can be smelted. Practice has proved that the aluminum alloys smelted by these furnaces have less gas content and less impurities. the
- When feeding materials, the materials with low melting point should be put in first, followed by the materials with high melting point. This will cause the metal to absorb less gas, and the reason is that the contact area and time between the charge and the air are reduced.
- After degassing the liquid metal, the slag should be removed immediately, and then poured, and it should not stay for too long to prevent re-breathing.
- Refining degassing or vacuum degassing with hexachloroethane or argon.
(2) Minimize the gas generation of coatings, sand cores, metal molds (cores), etc. Choose good-quality coatings with low gas generation, and fully dry the mold and core coatings. Prevent reactive pores
- ① The type of coating should be selected properly, and the gas generation of the coating should not be high. The paint also has a certain amount of outgassing.
- ③ Do not wipe off the paint after spraying. Where the paint falls off, it should be sprayed immediately.
- ② The mold and core should be preheated first, and then the paint should be sprayed, and it must be fully baked before use. the
- ④ Sand cores must be thoroughly dried before use.
- ⑤ The surface of the metal type and cold iron should be smooth and clean, and should be dried before use.
(3) Improve the exhaust conditions of the mold and core.
According to the characteristics of the casting, the filling situation of the casting can be considered comprehensively, and a reasonable exhaust position and different exhaust measures can be selected: exhaust grooves, exhaust sheets, exhaust needles, exhaust plugs, exhaust holes, etc. for exhaust .
Shrinkage and porosity
Shrinkage defect: When the metal solidifies and shrinks, the defect occurs because the molten metal does not effectively feed the casting. Including shrinkage cavity, shrinkage porosity, shrinkage, sinking and so on.
1.feature
- Shrinkage cavity: There are extremely irregular holes in the casting, the hole wall is rough and has dendrites, which is called shrinkage cavity defect. Mostly appear in the final solidification part of the casting.
- Shrinkage porosity: There are scattered and small shrinkage cavities on the casting section, sometimes called shrinkage porosity defects with the aid of a magnifying glass. For example, when aluminum pistons are produced by low-pressure casting, shrinkage sometimes appears on the top of the pistons. the
- Porosity: Very small holes appearing in the slow solidification zone of the casting. Distributed in dendrites and between dendrites, it is a mixed defect of diffuse pores, micro-shrinkage, and coarse structure, which reduces the compactness of the casting and easily causes leakage.
- Shrinkage: The thick end face of the casting or the collapse of the upper plane at the cross-section junction. Sometimes there are shrinkage cavities below the shrinkage, and sometimes the shrinkage also appears near the inner shrinkage cavity.
- Shrinkage: A casting defect that occurs when using sodium silicate limestone sand molds to produce castings, which is characterized by the expansion of the cross-sectional size of the casting.
- Shrinkage cracks: Cracks caused by improper casting, shrinkage resistance or uneven shrinkage. May appear immediately after solidification or at lower temperatures.
2.cause
The reason for the formation of shrinkage cavity and shrinkage porosity is: during the solidification process of the molten metal, due to the liquid shrinkage and solidification shrinkage of the alloy, that is, the volume loss caused by the volume shrinkage cannot be compensated, that is, it cannot be fed, and often solidifies at the end of the casting Holes appear in the parts. the
Different from general gravity casting, low-pressure casting is filled from bottom to top, and the gate is at the bottom. In order for the casting to get enough shrinkage, it is necessary to form a sequential solidification from top to bottom, that is, the place far away from the runner is solidified first, and the place away from the runner is solidified last, otherwise shrinkage cavity and shrinkage defects will occur. the
3.Preventive measures (simultaneous or sequential solidification)
Since low-pressure casting and differential pressure casting are all anti-gravity castings, gravity is always hindering feeding, so whether it is for sand casting or metal casting, or for castings that solidify simultaneously or sequentially, the quality of the liquid level pressure control system is good. Bad, is the key link to determine the compactness of castings. Especially for metal mold casting of thin-walled parts, the solidification time is not long. When the mold is filled to the top of the mold, the solid phase fraction in the liquid metal has already occupied a considerable proportion. At this time, the pressure should be increased rapidly in order to overcome the negative effect of gravity and carry out feeding. At this time, the compactness of the casting is an extremely critical moment. At present, some liquid level pressurization control systems still pressurize slowly according to the filling speed at critical moments, and some control systems are even worse. They can still boost normally when the pressure is low, but the higher the pressure, the slower the boosting speed. That is, the so-called downward parabolic filling.
When the solidification of the liquid metal is basically over, the control system will increase the pressure of the pressurization and feeding. Obviously it is too late, and this will not have a good effect on the density of the casting. Sometimes the feeding pressure is already very high (up to 0.2MPa) in production, but the casting still has shrinkage porosity defects, resulting in too high pressure leakage rate. When the feeding channel is reasonable, it is mainly because the timing of the pressurization of the control system is not well controlled, rather than the so-called “feeding pressure has little effect on the compactness of the casting”. For large thin-walled parts, no qualified castings were cast after more than two years of trial production. The faults were that the castings had a lot of shrinkage, poor compactness, and serious pressure leakage.
When the old-fashioned liquid level pressurization control system was replaced by the closed-loop feedback “CLP-3” low-pressure casting liquid level pressurization control system, the situation changed drastically. The original process did not change much, and qualified castings were produced. A factory in Shenyang used a manual control system to produce thin-walled shell castings on a differential pressure casting machine, and the reject rate was almost as high as 80% to 90%, and then replaced it with the “CLP” type differential pressure casting designed by Harbin Institute of Technology to pressurize the liquid surface After controlling the system, the scrap rate dropped sharply immediately, and qualified castings with clear edges and corners and plump printing were cast. It can be seen from this that the position of the liquid level pressurization control system in differential pressure and low pressure casting is extremely important.
4.specific preventive measures
For the shrinkage cavity that occurs in the sequential solidification of metal molds, the elimination methods are as follows.
- Make the temperature distribution of the mold reasonable, that is, the temperature of the upper part is low and the temperature of the lower part is high. It is better to use the CLP-5 type liquid surface suspension pressurization control system, which can increase the temperature of the lower part and increase the feeding capacity.
- Make the heat capacity distribution of the mold itself reasonable, that is, the heat capacity of the lower part is small, and the heat capacity of the upper part is large (that is, the wall of the lower part is thin and the wall of the upper part is thick).
- Forced cooling should be used at the local hot joints to adjust a temperature field distribution that conforms to feeding.
- For the “cold joint” that locally affects feeding, drill and mill grooves around the back, and then fill with insulating materials to increase thermal resistance and give a reasonable temperature field.
- Reduce the filling speed and mold temperature, but it should be appropriate to prevent cold shut and insufficient pouring
- Appropriately lowering the pouring temperature has a significant effect on reducing shrinkage porosity. : Make the temperature distribution of the mold reasonable, the upper part temperature is higher and the lower part temperature is lower; The “cold festival” treatment method is the same as above.
5.The processing methods of mold temperature, filling speed and pouring temperature are opposite to those of sequential solidification.
It is more convenient to change the casting process of sand molds, so whether it is simultaneous solidification or sequential solidification, there are many ways to eliminate shrinkage cavities.
The specific preventive measures are as follows:
- For large and medium-sized non-ferrous alloy and ferrous metal castings, where the wall thickness varies greatly, set up risers, and pressurize from the risers to strengthen feeding and prevent shrinkage cavities and porosity.
- Properly reduce the pouring temperature or pouring speed.
- Reasonably design the casting process and establish sequential (simultaneous) solidification conditions.

Inclusion
1.feature
- Inclusion defects The general term for various metal and non-metal inclusions in castings. Usually, impurity particles such as oxides, sulfides, silicates, etc. are mechanically retained in the solid metal, or formed in the metal during solidification, or formed in the metal during the reaction after solidification. Including inclusions, cold beans, infiltrated beans, slag inclusions, trachoma, etc.
- Inclusions The particles that are different from the matrix metal composition in the casting or on the surface. Including: slag, sand, paint layer, oxide, sulfide, silicate, etc.
- Endogenous inclusions In the process of smelting, pouring and solidification, the inclusions generated due to the chemical reaction between the molten metal and the furnace gas (can also include the mold), and the solubility decreases due to the temperature drop of the molten metal and precipitated inclusions.
- Exogenous inclusions Inclusions caused by slag and foreign impurities.
- Slag inclusions: inclusion defects in castings caused by slag, low melting point compounds and oxides wrapped in molten metal due to impure pouring molten metal, or improper pouring method and pouring system design. Because its melting point and density are usually lower than that of molten metal, it is generally distributed on the top or upper part of the casting, as well as the lower surface of the core and the dead corner of the casting, and the fracture is dull and dark gray.
- Paint slag holes: irregular pits containing residual paint accumulation substances caused by the powdering and falling off of the layer and remaining on the surface of the casting. The paint on the pouring tools, molds, riser pipes, sand cores, etc. will fall off, especially if the sand core is brushed with paint and then baked with fire, it will peel (explode). Therefore, when the production is not tight, try to use a constant temperature oven to bake. Baked sand core.
- Cold beans The metal particles (beads) existing on the surface of the casting below the pouring position have the same chemical composition as the casting, and there is oxidation on the surface. Generally, it is formed due to the splashing of molten metal, a small amount of molten metal contacting with the mold, rapid solidification and subsequent molten metal not being combined.
- Trachoma Holes with sand grains inside or on the surface of the casting.
- Hard spots Scattered or relatively large hard inclusions appear on the cross section of the casting, which are mostly found during machining or surface treatment.
- Slag pores Non-metallic inclusions on the upper surface of the casting position are usually found to coexist with pores after processing, and the pores are of different sizes and clustered together.
2.cause
Oxidized slag inclusions often appear in low-pressure casting castings. The source of oxidation slag is analyzed:
- (1) When aluminum liquid is added to the crucible during continuous production, the oxide slag on the liquid surface is rushed into the riser and brought into the mold during pouring; so in After adding aluminum liquid, a tool should be inserted into the upper end of the riser pipe to scoop out the slag in the riser pipe.
- (2) The oxide skin caused by the repeated rise and fall of the liquid level of the riser pipe.
- (3) The pressurization speed is too fast, resulting in splashing and producing scale.
- In addition, non-metallic slag inclusions may be caused by the loss of casting materials and coatings.
3.Prevention
- Strictly control the filling speed to ensure that the molten metal rises steadily without impact or splashing.
- Thoroughly remove the oxidation slag in the alloy liquid.
- Use a filter screen at the mouth of the riser or the sprue of the mold. However, not all filters can be used, some are large and complex, and the wall thickness is thinner, and the weight of the product will not be filled after using the filter, only some are small and simple, and the wall thickness is thicker , lighter weight product, easy to use. the
- Check whether the paint layer has fallen off, and the dust, sand and sundries in the cavity should be thoroughly cleaned.
Cold insulation and insufficient watering
1.Feature
- (1) Cold shut: There are penetrating or impenetrable gaps with rounded edges on the casting, and the middle of the gap is often separated by oxide scales, which cannot be completely integrated into one defect. It mostly appears in the wide upper surface or thin wall far away from the gate, the confluence of molten metal, cold iron core support and other chilling parts.
- (2) The casting is incomplete or the outline is incomplete or may be complete but the corners are round and bright, which is called insufficient pouring. It often appears in parts far away from the gate and in thin-walled places. Its pouring system is the best.
2.Causes of formation (fluidity, exhaust)
- The mold temperature or molten metal temperature is low;
- Low metal filling pressure and slow filling speed;
- The exhaust of the cavity is not smooth, and the gas counterpressure in the cavity is too large.
3.Preventive measures (fluidity, exhaust)
- (1) Use reasonable mold temperature and molten metal pouring temperature (two important process parameters); general thin-walled and complex metal cores for castings, metal molds 200-300, 250-320, 250-350 for low-pressure casting The temperature is 10 to 20 degrees lower than the pouring temperature of gravity pouring under the same conditions.
- (2) Use reasonable pressurization specifications.
- (3) Improve the exhaust conditions and exhaust methods of the mold and core.
- (4) If very shallow convection groove marks are found on the casting, just spray some paint on the convection part of the mold to eliminate them.
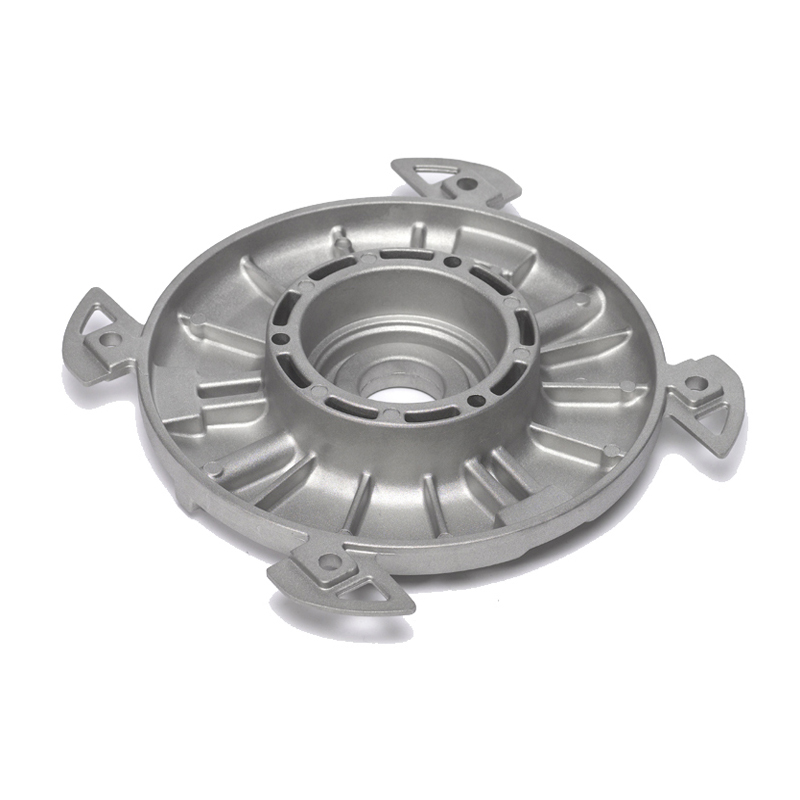
Cracks
1.Cause of formation
Cracks can be divided into hot and cold cracks. During the cooling and solidification process of liquid metal, if the stress caused by various reasons occurs shortly after the solid phase skeleton is formed, the cracks formed are called hot cracks; otherwise, they are called cold cracks.
2.Prevention method
- Increase the retreat of the part that hinders shrinkage in the mold and core, and increase the thickness of the coating.
- Increase the feeding of the hot cracked part. Because most of the hot cracking part is the final solidification part, strengthening the feeding of this part will naturally reduce hot cracking.
- Increase the heat dissipation capacity of the mold in the hot part, which may transfer the hot crack part or prevent the hot crack.
- On both sides of the metal mold (core) corresponding to the crack, a shallow channel parallel to the crack direction is opened to disperse the shrinkage stress during solidification, so as to overcome the hot crack.
- Opening the mold and taking out the casting as early as possible can effectively reduce hot cracking.
- Increasing the mold temperature and pouring temperature is conducive to simultaneous solidification and has a good effect on reducing thermal cracking. The cold cracking can be considered from the structural design, and the produced castings can be slowly cooled or annealed immediately, which is beneficial to reduce the residual thermal stress, can effectively reduce the cold cracking, and can also add tension bars to the parts to remove Crackproof.
sticky sand
1.Cause of formation
Sticky sand can be divided into chemical sticky sand and mechanical sticky sand, but for low-pressure casting or differential pressure casting, it is mainly mechanical sticky sand. The reason for this is that the pressure of the liquid metal increases greatly when it is under pressure, and the pressure forces the liquid metal to overcome the surface tension and penetrate into the sand core or sand mold, resulting in mechanical sand sticking.
2.Prevention method
- Brush the high refractoriness and dense coating layer on the surface of the sand mold or sand core, which can effectively overcome the defects of sand sticking.
- Properly reduce the pouring temperature.
- Appropriately reduce the pressure jump value during pressure holding.
deformation
1.Cause of formation
The causes of casting deformation are the same as those of cold cracks
2.Prevention method
The treatment of this problem is basically the same as that of cold cracking. In addition, there are some special methods:
- (1) According to the deformation of the casting, a correction amount for anti-deformation is reserved on the mold.
- (2) The mold reserves the stretch bars, which will be removed after heat treatment and annealing.
- (3) After deformation, it can be corrected on the press.
flash, burr
1.Causes of flash burr formation
Due to thermal stress deformation or other mechanical reasons (insufficient pressure of the hydraulic cylinder), the mold is not closed tightly, resulting in gaps, leaving flashes and burrs after filling.
2.Prevention method
- (1) Increase the rigidity of the mold and change the structure of the mold to reduce the thermal deformation of the mold.
- (2) It may also be due to operational reasons that the corners of the mold may be deformed (bumped) and one side of the parting surface may be raised. It should be carefully checked or tested on a platform, and then filed flat.
- (3) Properly reduce the pouring temperature, pouring speed (filling speed, pressurization speed) or pressurized crust delay
leak
Air leakage, water seepage or oil seepage occurs during the air tightness test or use of castings. Some aluminum castings with high density requirements often have quality problems of pressure leakage, mostly due to defects such as pores, shrinkage, looseness, coarse structure or cracks in the castings, and there are a lot of Al2O3 in these parts. The reason is that when the aluminum liquid contacts the air during pouring, an oxide film is formed on its surface immediately, and the mixed flow that occurs due to the unsteady flow of the liquid when filling the mold will often suppress these oxide films and some cast aluminum parts that require high density. The quality problem of leakage, the main cause of leakage is micropores, microshrinkage and cracks, and there are a lot of Al2O3 in these parts. The reason is that when the aluminum liquid contacts the air during pouring, an oxide film is formed on its surface immediately, and the turbulence that occurs due to the unsteady flow of the liquid when filling the mold will mix these oxide films together with the adsorbed gas into the interior of the aluminum liquid. The relative density of these inclusions is similar to that of the aluminum liquid, and because the viscosity of the aluminum liquid increases as the temperature drops, the impurities will not have time to float out and remain inside the casting. The two adjacent oxide films provide positions and opportunities for the formation of initial cracks, and the gas precipitated during solidification and insufficient feeding will also form micro-pores and micro-shrinkage porosity in these areas. This will significantly reduce the mechanical properties of the material and become the source of pressure leakage, so the speed of liquid metal entering the cavity and the stability of liquid flow are crucial issues. It has been studied abroad that when a thin plate with a thickness of 5mm is filled at different speeds, the strength and plasticity of the resulting castings are different. Even if the filling speed is the same, the severity of the turbulence caused by the structure of the cavity is different, and the strength and plasticity of the corresponding parts are also different. Therefore, the hydraulic pressure control system has a very serious impact on the quality of complex thin-walled parts with high internal quality requirements.