In the dynamic landscape of manufacturing, zinc alloy die-casting has become a game-changer. This guide reveals the intricacies of zinc alloy die castings, illustrating the applications, manufacturing processes, and superior benefits that make them the first choice.
1. Understanding Zinc Alloy Die Casting Parts
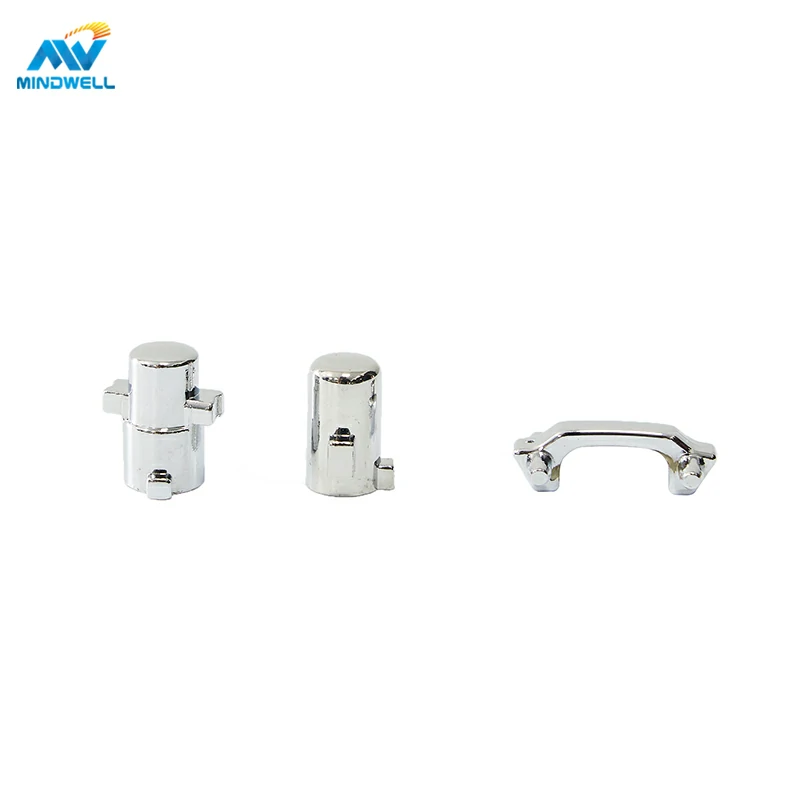
Zinc alloy die castings are a type of part widely used in manufacturing, with unique composition and performance characteristics that allow them to perform well in a variety of applications.
First of all, the main component of zinc alloy die-casting parts is zinc, which usually accounts for as much as 96%. At the same time, in order to enhance its mechanical properties, some other elements will be added, such as aluminum (usually 4%), magnesium (0.04%), and copper (less than 0.25%). In addition, impurity elements such as iron, lead, cadmium and tin are also strictly controlled to ensure the quality and performance of zinc alloys.
The performance features of zinc alloy die castings mainly include the following aspects:
- Good casting performance: Zinc alloy has good fluidity and filling properties, so it can be die-cast into products with complex shapes, thin walls, and high dimensional accuracy.
- High surface quality: The surface of zinc alloy die-casting parts is smooth and can be used directly, or various surface treatments such as polishing, electroplating, spraying, etc. can be performed to obtain better surface quality.
- High strength and wear resistance: Zinc alloy has high tensile strength, yield strength, impact toughness and hardness, as well as good elongation, making zinc alloy die-casting parts have good room-temperature mechanical properties and wear resistance.
- Low melting point: The melting point of zinc alloy is low, about 385°C, and it is easier to die-cast than aluminum alloy and magnesium alloy.
- Non-stick mold: During the melting and die-casting process, the zinc alloy does not absorb iron, does not corrode the die, and does not stick to the mold, thereby protecting the life of the mold.
- Easy to carry out various surface treatments: Zinc alloy die-casting parts can be subjected to surface treatment processes such as electroplating, spraying, and painting to achieve diversified appearance effects and functional requirements.
These features make zinc alloy die castings widely used in manufacturing fields. For example, zinc alloy die castings are used in automobiles, motorcycle parts, lighting accessories, toy accessories, electrical accessories, leather hardware, electronics and other industries.
In general, zinc alloy die casting is a high-quality manufacturing material with unique composition and performance characteristics that can meet a variety of complex and demanding application scenarios.
2.Applications across Industries
Zinc alloy die castings are widely used in many industries. Here are a few main areas:
- Automobile industry: Zinc alloy die-casting parts are widely used in the automobile industry. Zinc alloy die castings may be used in automobile exterior parts, such as wheels, doors, hoods, etc., and internal parts, such as cylinder heads, oil pans, transmission cases, etc. Their high strength, corrosion resistance and lightweight properties make them an ideal material for automotive manufacturing.
- Electronic industry: Zinc alloy die-casting parts also have many applications in the electronic industry, such as TV casings, computer parts, mobile phone casings, etc. Its good thermal conductivity and electromagnetic shielding properties make it suitable for use in housings for these devices.
- Furniture Industry: Zinc alloy die-casting parts also have certain applications in furniture manufacturing. For example, zinc alloy die castings may be used for zinc alloy chair legs and table legs. Its high strength and durability enable the furniture to withstand the wear and tear of everyday use.
- Construction industry: In the construction field, zinc alloy die castings can be used to manufacture various parts, such as roofs, railings, stairs, etc. Its corrosion resistance and aesthetic properties make it ideal for the construction industry.
- Medical industry: Zinc alloy die-casting parts are also used in the medical industry, such as manufacturing surgical instruments and dental appliances. Due to its high strength and corrosion resistance, zinc alloys also have extensive applications in the medical field.
- Consumer Electronics: From digital cameras to laptops, zinc alloy die-casting plays a key role in the manufacturing of the casings of these consumer electronics. Their high strength, light weight and aesthetics add to the appeal of these products.
- Toy Industry: Zinc alloy die-casting parts are also widely used in toy manufacturing, such as toy cars, toy animals, etc. Its safety and durability enable the toys to meet strict safety standards.
To sum up, zinc alloy die castings are widely used in various industries, mainly due to their excellent performance characteristics, including high strength, corrosion resistance, good casting performance, and diverse surface treatment possibilities.
3.Manufacturing Precision: The Die Casting Process
The die casting process is a precision manufacturing method suitable for manufacturing metal parts of various shapes and sizes. In the manufacturing process of zinc alloy die-casting parts, every stage has an important impact on accuracy and efficiency.
- Mold making: Mold is the basis of die casting process. Manufacturing high-precision molds is a key step to ensure part size and shape. Mold design is usually carried out using CAD/CAM technology to achieve high-precision processing. During the mold making process, details such as gates, exhaust ports, and ejection mechanisms need to be taken into consideration to ensure the smooth progress of the die-casting process.
- Die-casting process: Die-casting is the core part of zinc alloy parts manufacturing. During this process, the zinc alloy is heated to a liquid state and then injected into the mold through a gate. The high-speed and high-pressure injection speed can ensure that the alloy fills every corner of the mold and improves the density and mechanical properties of the parts. At the same time, reasonable injection pressure and time settings are also key factors to ensure dimensional stability of parts.
- Cooling and Demolding: The zinc alloy injected into the mold hardens after cooling. During this process, the cooling rate needs to be controlled to prevent defects such as shrinkage holes and cracks in the parts. When the part is completely cooled, it is ejected from the mold by an ejection mechanism. This step needs to ensure a balance between ejection force and ejection speed to avoid deformation or damage of the parts.
- Post-processing: The demoulded zinc alloy parts require some post-processing, such as edge trimming, polishing, spraying, etc., to further improve the quality and appearance of the parts. These steps also have a significant impact on part accuracy and efficiency.
- Quality inspection: Strict quality inspection is required at each stage of the manufacturing process to ensure that the accuracy and quality of parts meet requirements. For example, X-ray flaw detection, ultrasonic testing, metallographic analysis and other methods can be used to inspect internal defects. At the same time, strict control of dimensional accuracy and surface quality is also required.
Overall, the manufacturing accuracy and efficiency of zinc alloy parts depends largely on each stage of the die-casting process. From mold making to final product, each step requires careful operation and maintenance to ensure the production of high-quality, efficient zinc alloy die-casting parts.

4.Quality Assurance in Zinc Alloy Die Casting
The quality assurance of zinc alloy die-casting parts is a complex and critical process involving multiple links and quality control measures. Here are some of the main steps and measures:
- Raw material control: The raw materials for zinc alloy die casting are mainly zinc alloy ingots or granules. First of all, make sure to use zinc alloy materials that meet the specifications, in which the zinc content and the content of other alloying elements must meet the requirements. Substandard raw materials may result in reduced performance or substandard die castings.
- Mold management: Molds are key tools in the die-casting process, and their quality and maintenance have an important impact on the quality of die-casting parts. Mold design, manufacturing and repair require strict standards and procedures. Regular inspection and maintenance of molds to ensure that they are in good working condition are important measures to ensure the quality of die castings.
- Production process control: During the die-casting process, parameters such as injection pressure, injection speed, cooling time, etc. need to be precisely controlled. Fluctuations in these parameters can lead to quality issues in die castings. By implementing standardized operating procedures and monitoring the production process, it is possible to ensure that these parameters are within acceptable ranges, thus ensuring stable quality of die castings.
- Quality testing: Quality testing is another important link to ensure the quality of zinc alloy die castings. This includes inspecting the appearance, dimensions, weight, performance, etc. of the die castings. For example, internal defects can be found through X-ray testing or ultrasonic testing. In addition, tensile, impact, hardness and other mechanical properties tests must be conducted to ensure that the die castings meet the design requirements.
- Certification and industry standards: Many industries and international organizations have established quality standards and certification systems for zinc alloy die castings. These standards usually include regulations on material composition, performance requirements, testing methods, etc. By adhering to these standards and obtaining relevant certifications, we can ensure that the quality of zinc alloy die castings reaches first-class levels and meets the needs of customers and the market.
- Environmental control: Environmental factors such as temperature, humidity, cleanliness, etc. during the manufacturing process also have an impact on the quality of zinc alloy die castings. Therefore, it is necessary to control the manufacturing environment to ensure that it complies with relevant standards and regulations.
- Continuous improvement and training: Continuous improvement of process flow and improvement of employee skills and awareness are also important aspects to ensure the quality of zinc alloy die castings. Through regular training and education activities, employees are informed of the latest quality standards and requirements, and master advanced manufacturing skills and methods.
- Records and traceability: Establishing a good record system is an important measure to ensure the quality of zinc alloy die castings. This includes raw material purchasing, mold usage records, production process parameter records, quality inspection records, etc. Through these records, the problem can be traced back to the point where it occurred, corresponding corrective measures can be taken, and similar problems can be avoided from happening again.
- Supply chain management: Effective management of the supply chain is also an important part of ensuring the quality of zinc alloy die castings. From the procurement of raw materials to the selection of parts suppliers, everything needs to be strictly evaluated and controlled. Establish long-term cooperative relationships with reliable suppliers to ensure supply chain stability and quality consistency.
- Customer feedback and market research: Constantly paying attention to market dynamics and customer feedback is an important means to optimize product quality. By collecting and analyzing customer reviews and suggestions on products, we can promptly adjust production processes and improve product performance to meet changing market demands.
In summary, the quality assurance of zinc alloy die-casting parts is a systematic process involving multiple links and factors. By implementing strict quality control measures, following relevant certifications and industry standards, as well as continuous improvement and training, we can ensure that the production of zinc alloy die-casting parts reaches first-class quality levels and meets customer needs and market requirements.
5.Sustainability and Environmental Impact
Zinc alloy die castings offer numerous advantages in terms of sustainability and environmental impact. The following are some of the main environmental aspects and practices:
- Recyclability: zinc alloy is a recyclable material. When zinc alloy die-casting parts are discarded at the end of their service life, they can be recycled and re-melted back into the production process. This recycling characteristic makes zinc alloy an environmentally friendly manufacturing material.
- Energy-saving production process: Zinc alloy die-casting is a relatively energy-saving production technology. Zinc alloy die casting requires lower energy consumption compared to some other metal casting processes. In addition, due to the low melting point of zinc alloys, injection molding requires relatively less energy. These features make zinc alloy die casting produce lower carbon emissions during the production process.
- Short production cycle: the production cycle of zinc alloy die casting is relatively short. Due to advances in mold design and manufacturing technology, as well as the popularity of automated production equipment, zinc alloy die castings can be manufactured faster, thereby reducing energy consumption and carbon emissions during the production process.
- Reduced scrap and waste: By optimizing the mold design and production process, scrap and waste can be reduced during the zinc alloy die-casting process. For example, using accurate mold matching and a reasonable pouring system can reduce defects such as under pouring or overflow, thereby reducing the generation of waste materials.
- Use environmentally friendly materials: During the zinc alloy die-casting process, choosing environmentally friendly and low-volatility additives, coatings and other auxiliary materials can reduce the impact on the environment and employee health. While meeting product performance requirements, these environmentally friendly materials also comply with national and international environmental regulations and standards.
- Reducing water consumption: By optimizing the production process and adopting water-saving equipment, water consumption during the zinc alloy die-casting process can be reduced. For example, using efficient water cooling systems and circulating water systems can reduce water consumption and sewage emissions.
- Compliance and Regulation: Manufacturers of zinc alloy die castings are required to comply with national and international environmental regulations and standards. These regulations and standards include regulations on air emissions, wastewater treatment, solid waste disposal, etc. Manufacturers need to establish corresponding environmental protection management systems to ensure environmental compliance during the production process.
- Education and training: Improving employee awareness and awareness of environmental protection is an important aspect of promoting sustainable practices. Manufacturers need to provide regular environmental training and education to their employees so that they understand environmental regulations and best practices and apply them in their daily work.
- Research and Development: Encouraging research and development of new environmentally friendly technologies and processes is also an important means of promoting sustainable development. Manufacturers need to pay attention to the latest environmentally friendly technologies and trends in the industry, and invest in the research and development of environmentally friendly processes and equipment that suit their own production characteristics.
- Partnerships: It is also important to work with partners such as suppliers and customers to promote sustainable practices. Manufacturers can develop sustainable partnerships with partners to jointly promote environmentally friendly materials and technologies to achieve broader environmental protection goals.
In summary, zinc alloy die castings offer great advantages in terms of sustainability and environmental impact. Manufacturers can contribute to sustainable manufacturing while meeting market demands and customer expectations by adopting a range of environmental measures and practices.
6.Advantages and Limitations
Zinc alloy die castings offer a number of advantages that make them an ideal choice in many applications. However, any material has its limitations, and zinc alloys are no exception. The following is an analysis of the advantages and limitations of zinc alloy die-casting parts:
voordeel:
- Cost-effectiveness: Zinc alloy die castings are relatively cheap to produce because they can achieve economies of scale through mass production. In addition, the price of zinc alloy is relatively stable, and its purchase cost is also low compared with other metals.
- High Strength and Hardness: Zinc alloy die castings have high strength and hardness, allowing them to withstand impacts and pressure. This makes them a reliable material choice in many applications.
- Good casting performance: Zinc alloy has good fluidity and filling properties, which makes the die-casting process smoother and reduces the scrap rate.
- Aesthetic appearance: Zinc alloy die-cast parts can have smooth surfaces and fine details, which make them very attractive in appearance.
- Corrosion resistance: Zinc alloy has good corrosion resistance and can resist erosion by the atmosphere and certain chemical substances.
- Recyclability: As mentioned before, zinc alloy is a recyclable metal material, which facilitates sustainable manufacturing.
limitation:
- Coefficient of thermal expansion: Zinc alloys have a high coefficient of thermal expansion, which means that during use, parts may undergo dimensional changes due to temperature changes. This may have an impact on applications where accuracy is critical.
- Machinability: Zinc alloys have relatively poor machinability, so they may require more time and effort to process during manufacturing.
- Fatigue Strength: Zinc alloys have relatively low fatigue strengths, which means they may suffer from fatigue fracture in applications where they are subjected to repeated stress or impact.
- Fire resistance: Zinc alloys have poor fire resistance and require additional safety measures when used in environments with a higher risk of fire.
- Impact on human health: Certain elements in zinc alloys may have an impact on human health, so correct operation and handling methods need to be ensured during use.
To summarize, zinc alloy die castings offer many advantages that make them ideal for many applications. However, when considering the use of zinc alloys, its limitations must be weighed and an informed decision made based on the specific needs of the application.
7.Case Studies: Real-world Applications
Case 1: Automotive Industry
Application: Automotive engine mount
Challenge: The automotive industry has stringent requirements for strength, corrosion resistance and lightweight components. Engine mounts need to withstand the weight and vibration of the engine and therefore require high strength and durability.
Solution: Use zinc alloy die castings to manufacture the engine mounts, taking advantage of its high strength, corrosion resistance and lightweight properties. The complex shape and high-precision requirements of the bracket are achieved through precise mold design and manufacturing processes.
Results: The zinc alloy die-cast engine mount was lightweight while meeting the strength and durability requirements, reducing the overall weight of the car and thereby improving fuel efficiency. In addition, the good casting properties of zinc alloy reduce production costs.
Case 2: Electronics industry
Application: mobile phone case
Challenge: The casing of electronic equipment needs to have good electromagnetic shielding properties, thermal conductivity and aesthetics. In addition, as consumers’ demand for thinner and lighter devices increases, the thinner and lighter outer casing is also an important challenge.
Solution: Use zinc alloy die-casting parts to make mobile phone casings, taking advantage of its good thermal conductivity and electromagnetic shielding properties. By optimizing the mold design and die-casting process, the outer shell is made thinner and lighter and requires high precision.
Results: The zinc alloy die-cast mobile phone casing not only meets the requirements of electromagnetic shielding and thermal conductivity, but also achieves thinness, lightness and aesthetics, improving the overall quality and user experience of the mobile phone. In addition, the recyclability of zinc alloy is beneficial to environmental protection and sustainable development.
Case 3: Furniture Industry

Application: Outdoor furniture (e.g. patio chairs)
Challenge: Outdoor furniture needs to withstand a variety of climatic conditions and environmental factors, such as sunlight, rain, wind, etc. Therefore, furniture materials need to have good corrosion resistance and durability.
Solution: Use zinc alloy die-casting parts to make the frame and support structure of the patio chair, taking advantage of its good corrosion resistance and strength. Through reasonable mold design and manufacturing processes, the chair’s complex shape and comfort requirements are achieved.
Results: The zinc alloy die-cast patio chair achieved comfort and beauty while meeting corrosion resistance and strength requirements, improving the quality and service life of outdoor furniture. In addition, the environmental protection of zinc alloy is also conducive to sustainable development.
These case studies demonstrate the widespread use and effectiveness of zinc alloy die castings across a variety of industries. From the automotive industry to the electronics industry to the furniture industry, the versatility, high precision and good casting properties of zinc alloys are fully reflected. These successful cases not only prove the value of zinc alloy die-casting parts, but also provide useful references and inspirations for other industries.
8.Challenges and Solutions
Zinc alloy die casting is widely used in many industries, but there are still some challenges. Here are some common challenges and corresponding solutions:
Challenge 1: Mold life
Problem: During the zinc alloy die-casting process, the life of the mold is often short. Since the solidification temperature range of zinc alloy is narrow, the opening position and structure of the mold have a great impact on the life of the mold.
Solution: Use mold materials with high strength and high wear resistance, such as carbide and powder metallurgy mold steel. Optimize mold design and processing technology to reduce the occurrence of thermal fatigue cracks in molds. The heat treatment process is used to improve the hardness and fatigue resistance of the mold.
Challenge 2: Air holes and cold isolation
Problem: Defects such as pores and cold insulation are prone to occur in zinc alloy die castings, which affects product quality and performance.
Solution: Optimize the die-casting process and control the fluidity of molten metal. Add exhaust ports and overflow ports in the mold design to avoid gas accumulation in the mold. Use appropriate coatings and release agents to reduce adsorption and adhesion on the mold surface and reduce the formation of pores.
Challenge 3: machining performance
Problem: Zinc alloy has poor machining properties and is prone to cracks and burrs during processing.
Solution: Use advanced mechanical processing equipment and processes, such as CNC machine tools and ultra-precision cutting, to improve processing accuracy and surface quality. Optimize processing parameters, control cutting force and cutting temperature, and reduce the occurrence of cracks and burrs. Use surface treatment techniques such as polishing and sandblasting to improve the surface quality and appearance of die castings.
Challenge 4: Dimensional accuracy and stability
Problem: The dimensional accuracy and stability of zinc alloy die castings are sometimes difficult to meet the requirements of high-precision manufacturing.
Solution: Improve the accuracy and stability of the mold by optimizing the mold design and manufacturing process. Use advanced die-casting equipment and technology, such as precision die-casting machines and digital control systems, to improve the stability and accuracy of the die-casting process. Perform post-processing process control, such as polishing, trimming and heat treatment, to improve the dimensional accuracy and stability of the product.
Challenge 5: Environmental protection and sustainability
Problem: Certain materials and processes used in the zinc alloy die-casting process may have impacts on the environment and human health.
Solution: Use environmentally friendly materials and additives, such as biodegradable coatings and low-volatile organic compound (VOC) coatings. Optimize production processes and reduce waste and energy consumption. Implement environmental protection management systems and technological innovation to improve the environmental protection and resource utilization efficiency of the production process.
Challenge 6: Cost-effectiveness
Problem: The production cost of zinc alloy die castings is relatively high, which may affect its application in some fields.
Solution: Reduce unit costs through mass production and optimized production processes. Use advanced die-casting equipment and technology to improve production efficiency and yield rate. Reasonably control raw material procurement, energy consumption and labor costs to reduce overall production costs. At the same time, new alloy materials and alternative materials can be considered to further reduce costs.
By adopting appropriate solutions and innovative technologies for these challenges, the zinc alloy die-casting industry can continuously achieve process improvements and product upgrades, ensuring continuous improvement and meeting changing market demands.
9.Frequently Asked Questions
- What are the unique features of zinc alloy die castings?
Zinc alloy die castings stand out for their versatility, precision and cost-effectiveness. - Are zinc alloy parts environmentally friendly?
Yes, zinc alloy die casting is environmentally friendly, thanks to zinc’s recyclability and energy-saving production. - How accurate is the manufacturing process?
The die-casting process ensures exceptional precision, enabling complex part designs. - Which industries benefit the most from zinc alloy die casting?
The automotive, electronics and consumer goods industries benefit significantly from zinc alloy die castings. - How to carry out quality control of zinc alloy die castings?
Strict quality control measures, certifications and compliance with industry standards ensure a high-quality end product. - Can zinc alloy die castings be mass-produced?
Yes, zinc alloy die casting is suitable for both small and large scale production, providing efficiency and cost-effectiveness.
10.Conclusion
Through this guide, we have an in-depth understanding of the characteristics, application fields, manufacturing processes, challenges and solutions of zinc alloy die castings. As a metal material with high strength, good casting properties and aesthetics, zinc alloy has been widely used in furniture, automobiles, electronics and many other industries.
This guide details the production process, advantages and limitations of zinc alloy die castings, and how to deal with common challenges. Through case studies and practical experience, we see the successful applications of zinc alloy die castings in the real world and how they create value for manufacturing companies and end users.
With the continuous advancement of technology and changing market demands, the zinc alloy die-casting industry will continue to develop and innovate. This guide aims to provide readers with comprehensive knowledge and understanding of zinc alloy die casting, helping readers better apply and use this valuable material, while contributing to the sustainable development of the industry.