Aluminum alloy die-casting is an efficient, economical, and precise casting method. It has the advantages of high production efficiency, low processing cost, easy mechanical automation in the production process, high dimensional accuracy of castings, good surface quality, and good overall mechanical properties. It is widely used in production and life. However, defects such as pores, flow marks, scratches, dents, cracks, undercasting, etc. are likely to occur during the casting and molding processes. These defects reduce the appearance and mechanical properties of die castings. In order to avoid the above problems during the die-casting molding process, structural designers need to evaluate the scheme in advance during the structural design of the die-casting part, make a reasonable layout in the structural design of the parts, and reduce defects to a minimum through optimized structures.

Key points in the design of aluminum alloy die castings
The rationality of die-casting design is related to the entire die-casting molding process. When designing die-casting parts, the structural characteristics of the die-casting parts and the die-casting process requirements should be fully considered to minimize the possibility of defects in the designed die-casting parts during the die-casting molding process. happens, and the quality of die castings is improved to the greatest extent with the optimal design solution.
Reasonable design of die casting wall thickness
The wall thickness issue must be fully considered when designing the structure of aluminum alloy die-casting parts. Wall thickness is a factor of special significance in the die-casting process. Wall thickness is closely related to the entire process specifications, such as the calculation of filling time and the selection of the inner gate speed; the calculation of solidification time, analysis of mold temperature gradient, role of pressure (final specific pressure), length of mold retention time; the casting ejection temperature; and operating efficiency. if the design wall thickness is too thick, shrinkage holes, blisters, and pores will appear , external surface defects such as coarse internal grains will reduce mechanical properties and increase part quality, leading to higher costs; Too thin a wall thickness will cause poor filling of aluminum liquid, difficulty in molding, poor dissolution of aluminum alloy, and proneness to difficulty filling the surface of castings , shortage of materials, and other defects, and bring difficulties to the die-casting process. As the pores increase, the internal defects of die-casting parts such as pores and shrinkage holes increase. Therefore, on the premise of ensuring that the casting has sufficient strength and stiffness, the casting wall should be minimized as much as possible. Thick and keep the thickness of the section uniform.
Reasonable design of die-cast stiffeners
For die-casting parts with large planes or thin walls, their strength and rigidity are poor, and they are easy to deform. At this time, the use of reinforcing ribs can effectively prevent shrinkage and fracture of the die-casting parts, eliminate deformation, enhance the strength and rigidity of the die-casting parts, and improve the performance of columns that are too tall. On platforms and other structures, the reinforcing ribs can be used to improve the stress distribution and prevent root fractures. At the same time, the reinforcing ribs can assist the flow of molten metal and improve the filling performance of the casting. The thickness of the root of the reinforcing rib is not greater than the thickness of the wall here, and the general thickness is designed to be 0.8 to 2.0 mm; the draft angle of the stiffener is generally designed to be 1° to 3°, and the higher the height, the smaller the draft angle is designed; reinforcement Fillets need to be added to the rib roots to avoid sharp changes in the cross-section of the part and, at the same time, assist the flow of molten metal, reduce stress concentration on the part, and improve the strength of the part. The fillets are generally close to the wall thickness here; the height of the reinforcing ribs generally does not exceed 5 times its thickness. In modern times, the thickness of the reinforcing ribs is generally required to be uniform. If the design is too thin, the reinforcing ribs themselves are easy to break. If they are too thick, defects such as dents and pores are likely to occur.
Reasonable design of die casting angle
The role of the mold ejection angle of the die casting is to reduce the friction between the casting and the mold cavity, making it easier to remove the casting; ensuring that the die casting surface is not strained, and at the same time extending the life of the mold. The mold draft is related to the height of the die casting. The greater the height, the smaller the mold draft. Under normal circumstances, the draft angle of the outer surface of the die-casting part is about 1/2 of the draft angle of the inner cavity, but in actual design, the draft angle of the inner and outer surfaces of the die-casting part can be designed to be consistent to maintain the wall thickness. Uniform, simplified structure design.
Reasonable design of machining allowance
When designing die-casting parts, machining should be avoided as much as possible. Machining will destroy the dense layer on the surface of the part and affect the mechanical properties of the part. It will also expose the pores inside the die-casting part, affecting the surface quality and increasing the cost of the part. When machining is unavoidable for die-casting parts, designs with large cutting volumes should be avoided as much as possible. The structural design should be as convenient as possible for machining, or reduce the machining area to reduce machining costs.
The upper part of the die-casting parts requires high dimensional accuracy, or the surface roughness of some planes is high, and the die-casting process is difficult to meet the requirements. At this time, subsequent processing is required. For this part of the structure, try to leave a machining allowance when designing. The surface strength and hardness of the die-casting parts are higher than the inside. When machining, attention should be paid to retaining the surface density, so the machining allowance should not be excessive. Excessive machining is likely to produce pores and outer surface defects.
Spray coating design of aluminum alloy die castings
The surface spraying design of die-casting parts generally adopts the powder spraying process. The principle is electrostatic powder spraying: the paint is mainly polarized through electrodes, and then the object to be sprayed is charged with the opposite charge. Under the action of the electric field force, the powder adheres uniformly to the surface of the object. . Characteristics of the powder spraying process: Powder electrostatic spraying will not cause air pollution, the powder can be recycled to reduce material consumption costs, and the coating film has good acid, alkali and corrosion resistance.
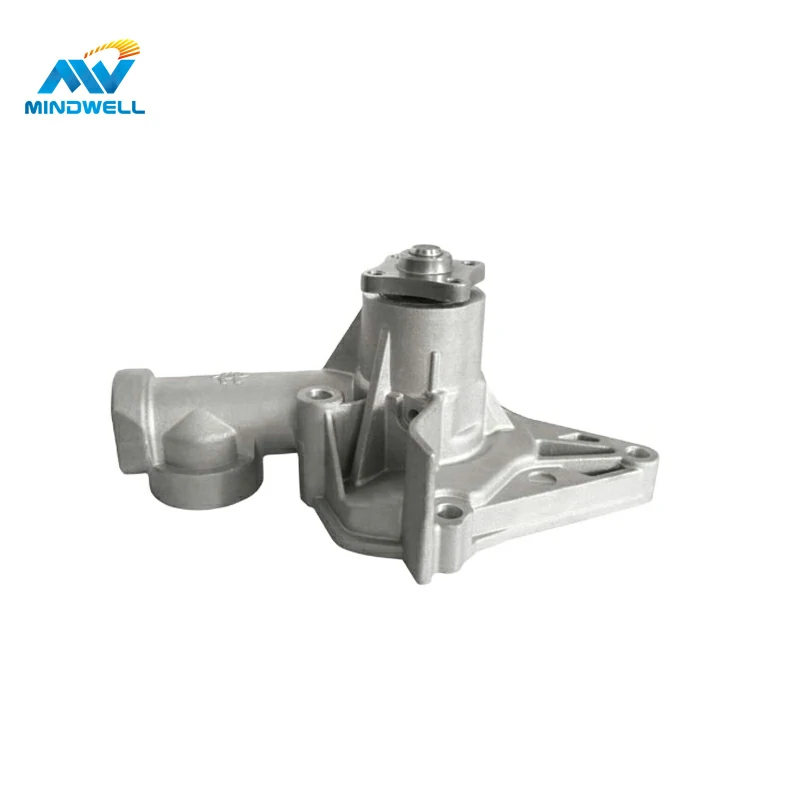
Issues to note when designing aluminum alloy die castings
- Aluminum alloy selection issues: Aluminum alloys have good processing properties and corrosion resistance, and different alloy materials are suitable for different working conditions. Therefore, when designing aluminum alloy die-casting parts, appropriate aluminum alloy materials should be selected according to actual working conditions.
- Die casting mold issues: The structure and shape of the die casting mold are critical to the quality of aluminum alloy die castings, and the accuracy and stability of the blank must be ensured. In the design stage, factors such as blank size, wall thickness, and wall-to-thin ratio need to be taken into consideration to avoid problems such as blank shrinkage, cracking, and pores.
- Gating system issues: The design of the gating system should avoid the generation of gases and inclusions, while allowing the molten metal to flow evenly during the die casting process. It is necessary to consider the location, size, quantity, shape, and other factors of the gate to ensure that the aluminum alloy liquid can fully fill the mold cavity and avoid defects such as shrinkage cavities and pores in the aluminum alloy during the pouring process.
- Temperature control issues: The melting point of aluminum alloy materials is low, so the temperature of the molten metal and the mold need to be accurately controlled to ensure good fluidity and molding quality. Temperature control can be achieved through heating or cooling measures, such as mold surface heating or the use of water coolers, etc.
- Machining issues: Aluminum alloy die castings usually require machining, so this should be considered during the design stage and specified into corresponding manufacturing requirements. For example, the blank surface’s flatness, tensile strength, hardness, dimensional tolerance, etc. are required to ensure the accuracy of subsequent machining and assembly.
- Demoulding problem: When demoulding, it is necessary to ensure the surface quality of the die-casting part and prevent defects such as metal flow or breakage. Therefore, a reasonable demolishing angle and demolishing force are necessary. In the design stage, manufacturing factors such as demoulding angle, wedge-shaped notch position, and demoulding force need to be taken into consideration.
- Surface treatment issues: The surface quality and processing methods of aluminum alloy die castings directly affect the appearance and mechanical properties of the product. Appropriate surface treatment methods should be selected, such as spraying, anodizing, etc., to achieve multiple effects such as beauty, corrosion resistance, explosion-proofness, and enhanced mechanical properties.
- Fatigue resistance and life issues: Fatigue life is very important for important components. The stress distribution and fatigue life of the components should be taken into consideration during the design stage to improve the durability of die castings. Reasonably designing the blank size and wall thickness to ensure a safe and reliable connection between the metal and the blank is also crucial to improving the fatigue life of aluminum alloy die castings.
- Cost issue: The cost of aluminum alloy materials is usually relatively high. The design of die-casting parts must not only meet technical requirements, but also reasonably control costs to improve competitiveness. Costs can be controlled by optimizing mold design, adjusting the gating system, and reducing the scrap rate.
As an established aluminum alloy die-casting company with decades of experience in die-casting, Mindwell has extensive experience in the дизайн, production, and processing of aluminum alloy die-casting parts. This experience can help customers avoid detours, save on capital costs, and shorten products. Improve production time, improve product service life, and maximize value creation for customers. When actually designing products, careful analysis and discussion must be conducted based on the actual situation to ensure the high quality and cost-effective production of aluminum alloy die castings.