Bu dört alaşım arasında titanyum alaşımı en sert ve en güçlü olanıdır. Sertlik açısından, titanyum alaşımları diğer üç alaşımdan çok daha serttir. Çekme mukavemeti açısından, titanyum alaşımları çinko alaşımlarından daha güçlüdür, ardından magnezyum alaşımları gelir ve alüminyum alaşımları en zayıf olanıdır.
Mukavemet ve Sertlik Karşılaştırması
Ancak ürün yapısı tasarımı açısından ağırlığın da dikkate alınması gerekir. İlerleme açısından özgül ağırlık dikkate alınırsa, çinko alaşımı en yüksek yoğunluğu nedeniyle en küçük özgül mukavemete sahiptir. Titanyum alaşımları ve magnezyum alaşımları yüksek özgül mukavemete sahiptir, ancak titanyum alaşımları pahalıdır ve zayıf işlenebilirliğe sahiptir. Bu nedenle magnezyum alaşımları daha çok ağırlık ve mukavemetin dikkate alındığı yapısal parçalarda kullanılır.
Magnezyum ve magnezyum alaşımı
Magnezyum düşük yoğunluğa sahiptir ve fiziksel ve kimyasal özellikleri nedeniyle kolay yanar. 20°C'de metalik magnezyumun yoğunluğu 1,738g/cm3 ve sıvı metalik magnezyumun yoğunluğu 1,58g/cm3'tür; standart atmosferik basınç altında metalik magnezyumun erime noktası (650±1)°C ve kaynama noktası 1090°C'dir. Havada ısıtıldığında, metalik magnezyum 632°C ila 635°C'de yanmaya başlar. Bu nedenle, magnezyumun hazırlanması ve alaşım eritme işleminin nispeten karmaşık olduğu belirlenmiştir. Endüstriyel kullanım için magnezyumun saflığı 99.9%'ye ulaşabilir, ancak saf magnezyum yapısal bir malzeme olarak kullanılamaz. Saf magnezyuma alüminyum, çinko, lityum, manganez, zirkonyum ve nadir toprak gibi elementlerin eklenmesiyle oluşan magnezyum alaşımları yüksek mukavemete sahiptir. Günümüzde en çok kullanılan Magnezyum-alüminyum alaşımları olup, bunu magnezyum-mangan alaşımları ve magnezyum-çinko-zirkonyum alaşımları takip etmektedir. Ağırlıklı olarak havacılık, uzay, ulaşım, kimya endüstrisi, roket ve diğer endüstriyel sektörlerde kullanılır.
Magnezyum alaşımının özellikleri
- ① hafif
Magnezyumun özgül ağırlığı sadece 1,8G/CM3, alüminyum alaşımının özgül ağırlığı ise 2,7G/CM3'tür. Magnezyum alaşımı alüminyum alaşımından 30%, çelikten ise 80% daha hafiftir. Bu nedenle, otomobillerde ve taşınabilir elektronik ürünlerde magnezyum alaşımları parçalar için ideal malzemeler haline gelmiştir.
- ②Güç
Magnezyum alaşımları, metaller ve plastikler gibi mühendislik malzemeleri arasında mükemmel bir mukavemet/ağırlık oranına sahiptir. Akma dayanımı 160MPa ve çekme dayanımı 240MPa'dır.
- Kalıp dökümü
İyi bir yapının korunması koşulu altında, magnezyum alaşımı dökümün et kalınlığının minimum 0,6 mm'ye ulaşmasını sağlar ki bu aynı mukavemete sahip plastikler için imkansızdır. Alüminyum alaşımlarının kalıp döküm performansı ancak 1,2-1,5 mm'nin üzerinde olduğunda magnezyum alaşımlarıyla karşılaştırılabilir. Magnezyum alaşımlarının kalıp dökümü daha kolaydır ve seri kalıp döküm üretimi için uygundur (üretim hızı alüminyumun 1,5 katı olabilir). Ayrıca magnezyum alaşımlı kalıbın aşınması alüminyumunkinden daha düşüktür. Bunun ana nedeni alüminyumun yüksek viskozitesidir.
- ④Şok emilimi
Magnezyum mükemmel histerezis şok emme performansına sahiptir, titreşimi ve gürültüyü emebilir ve gürültü iletimini azaltmak, şoku önlemek ve göçük hasarını önlemek için ekipman kasası olarak kullanılabilir. LCD veya LED için bir arka panel olarak iyidir.
- ⑤ Sertlik
Magnezyum alüminyumdan iki kat daha serttir ve çoğu plastikten daha serttir. Magnezyum iyi bir gerilim direncine sahiptir.
- ⑥ Yüksek elektromanyetik parazit bariyeri
Magnezyum alaşımı elektromanyetik dalgaları engelleme konusunda iyi bir işleve sahiptir ve elektronik ürünlerin üretimi için uygundur.
- ⑦İyi kesme performansı
Magnezyum, alüminyum ve çinkoya göre daha iyi işlenebilirliğe sahiptir, bu da magnezyumu daha kolay işlenen bir metal haline getirir.
- ⑧ Magnezyum alaşımının özgül ısı kapasitesi küçüktür ve alaşım sıvısının soğuma hızı hızlıdır.
- ⑨Magnezyum alaşımı ile kalıp çeliği arasındaki afinite düşüktür, bu nedenle kalıba yapışması kolay değildir.
Magnezyum alaşımlı malzemelerin avantajları
① hafif
Magnezyum alaşımının özgül ağırlığı tüm yapısal alaşımlar arasında en hafif olanıdır. Özgül ağırlığı alüminyum alaşımında 68%, çinko alaşımında 27% ve çelikte 23%'dir. 3C ürünlerinin kabuk ve iç yapısal parçaları olarak kullanılmasının yanı sıra otomobillerde de kullanılır. uçak ve mükemmel malzemenin diğer parçaları.
②Yüksek özgül mukavemet ve özgül sertlik
Magnezyum alaşımının özgül mukavemeti alüminyum alaşımından ve çelikten önemli ölçüde daha yüksektir ve özgül sertliği alüminyum alaşımına ve çeliğe eşdeğerdir, ancak genel plastiklerin 10 katı olan mühendislik plastiklerinden çok daha yüksektir.
③İyi titreşim direnci
Aynı yük altında, titreşim sönümleme performansı alüminyumun 100 katı ve titanyum alaşımının 300-500 katıdır.
④Mükemmel elektromanyetik ekranlama
3C ürünlerinin (cep telefonları ve bilgisayarlar) kabuğu üstün anti-elektromanyetik koruma sağlayabilmeli ve magnezyum alaşımlı kabuk 100db'yi aşan frekansta elektromanyetik paraziti tamamen emebilmelidir.
⑤ İyi ısı dağılımı
Genel metallerin ısıl iletkenliği plastiklerin yüzlerce katıdır. Magnezyum alaşımlarının ısıl iletkenliği alüminyum alaşımları ve bakır alaşımlarından biraz daha düşük, titanyum alaşımlarından ise çok daha yüksektir. Özgül ısı, yaygın olarak kullanılan alaşımlar arasında en yüksek olan suyunkine yakındır.
⑥ iyi doku
Magnezyum alaşımı mükemmel bir görünüme ve dokunma dokusuna sahiptir, bu da ürünü daha lüks hale getirir.
⑦ İyi geri dönüştürülebilirlik
Maliyet yeni malzeme fiyatının 4%'sine eşit olduğu sürece, magnezyum alaşımlı ürünler ve atıklar geri dönüştürülebilir.
⑧ İstikrarlı kaynak temini
Yerkabuğundaki magnezyum elementi rezervi sekizinci sıradadır ve magnezyum hammaddesinin çoğu deniz suyundan çıkarılır, bu nedenle kaynağı istikrarlı ve yeterlidir.
Magnezyum alaşımlı basınçlı dökümün avantajları
- Yüksek verimlilik
- ②Yüksek hassasiyet
- ③İyi yüzey kalitesi
- ince döküm tanesi
- İnce duvarlı ve karmaşık yapılı ürünler basınçlı dökümle üretilebilir
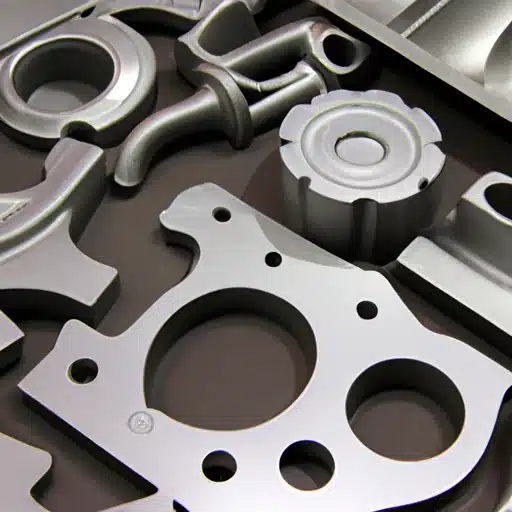
alüminyum alaşım
Alüminyum bazlı alaşımlar için kullanılan genel terim. Ana alaşım elementleri bakır, silikon, magnezyum, çinko, manganez ve ikincil alaşım elementleri nikel, demir, titanyum, krom, lityum ve benzerleridir.
Alüminyum alaşımı düşük yoğunluğa, ancak yüksek kaliteli çeliğe yakın veya onu aşan yüksek özgül mukavemete sahiptir. İyi bir plastikliğe sahiptir ve çeşitli profillere işlenebilir. Mükemmel elektrik iletkenliğine, termal iletkenliğe ve korozyon direncine sahiptir. Endüstride yaygın olarak kullanılır ve kullanımı çelikten sonra ikinci sıradadır.
Alüminyum alaşım sınıflandırması
Aluminum alloys are divided into two categories: cast aluminum alloys, which are used in the as-cast state; deformed aluminum alloys, which can withstand pressure processing, and have higher mechanical properties than the as-cast state. It can be processed into various shapes and specifications of aluminum alloy materials. It is mainly used in the manufacture of aviation equipment, daily necessities, doors and windows for buildings, etc.
Aluminum alloy processing method
According to the processing method, aluminum alloy can be divided into deformed aluminum alloy and cast aluminum alloy. Deformed aluminum alloys are further divided into non-heat-treatable and strengthenable aluminum alloys and heat-treatable and strengthenable aluminum alloys. The non-heat-treatable type cannot improve the mechanical properties by heat treatment, but can only be strengthened by cold deformation. It mainly includes high-purity aluminum, industrial high-purity aluminum, industrial pure aluminum and anti-rust aluminum. Heat-treatable and strengthened aluminum alloys can improve mechanical properties through heat treatment such as quenching and aging. It can be divided into hard aluminum, forged aluminum, super hard aluminum and special aluminum alloys.
Aluminum alloys can be heat treated to obtain good mechanical, physical and corrosion resistance properties.
Cast aluminum alloys can be classified into aluminum-silicon alloys, aluminum-copper alloys, aluminum-magnesium alloys and aluminum-zinc alloys according to their chemical composition.
Comparison of aluminum alloy and magnesium alloy
ADC-12 (ADC-12 has high silicon content, good fluidity and easy die-casting
There is not much difference between aluminum alloy and magnesium alloy, but aluminum alloy is slightly heavier. Processability is relatively sticky. Moreover, since the die-casting aluminum alloy contains a relatively high content of Si, it directly reacts with the chemical solution when performing Anodizing (anodizing). so as to fail. Magnesium alloy is acceptable, and the color is brighter, and Anodizing can be used for post-production appearance technology. However, not everyone can do it.
Zinc alloy
Zinc alloy characteristics
The grade of zinc-based alloy material usually used for electroplating is ZnAl 4-1, composition (%): Al 3.5~4.9, Cu 0.75~1.25, Mg 0.03~0.08, the balance is Zn.
①The proportion is large
② Good casting performance, can die-cast precision parts with complex shapes and thin walls, and the casting surface is smooth
③ Surface treatment available: electroplating, spraying, painting
④ No iron absorption during melting and die-casting, no corrosion of the pressing type, no sticking to the mold
⑤Good mechanical properties and wear resistance at room temperature
⑥ Low melting point, melting at 385°C, easy to die-cast
Problems to be noticed during use
① Poor corrosion resistance.
When the impurity elements lead, cadmium, and tin in the alloy composition exceed the standard, the casting will be aged and deformed, manifested as volume expansion, mechanical properties, especially plasticity, will decrease significantly, and even rupture after a long time. The solubility of lead, tin and cadmium in zinc alloy is very small, so they concentrate on the grain boundary and become the cathode, and the aluminum-rich solid solution becomes the anode, which promotes intergranular electrochemical corrosion under the condition of water vapor (electrolyte). Die castings age due to intergranular corrosion.
② aging effect
The structure of zinc alloy is mainly composed of zinc-rich solid solution containing Al and Cu and Al-rich solid solution containing Zn, and their solubility decreases with decreasing temperature. However, due to the extremely fast solidification rate of die castings, the solubility of the solid solution is greatly saturated at room temperature. After a certain period of time, this supersaturation phenomenon will be gradually relieved, and the shape and size of the casting will change slightly.
③Zinc alloy die castings should not be used in high temperature and low temperature (below 0°C) working environment. Zinc alloys have good mechanical properties at room temperature. But the tensile strength at high temperature and the impact performance at low temperature are significantly decreased.
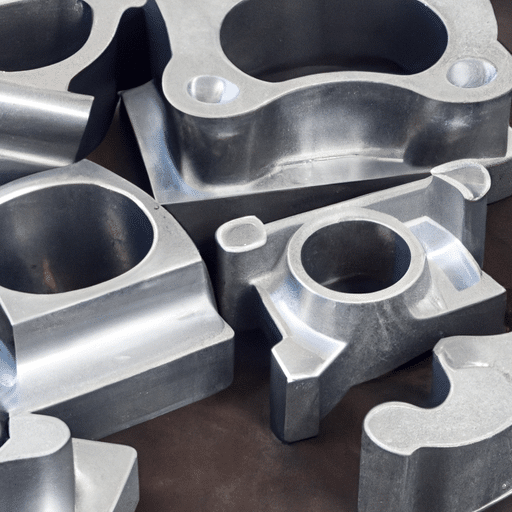
Titanium alloy
Titanium alloy is an alloy composed of titanium as the base and adding other elements. Titanium has two kinds of allotropic crystals: below 882°C is close-packed hexagonal structure α titanium, above 882°C is body-centered cubic β titanium.
Alloying elements can be divided into three categories according to their influence on the phase transition temperature:
① The elements that stabilize the α phase and increase the phase transition temperature are α stable elements, including aluminum, carbon, oxygen, and nitrogen. Among them, aluminum is the main alloying element of titanium alloy, which has obvious effects on improving the strength of the alloy at room temperature and high temperature, reducing the specific gravity, and increasing the elastic modulus.
②The elements that stabilize the β-phase and lower the phase transition temperature are β-stable elements, which can be divided into two types: the isomorph and the eutectoid. The former has molybdenum, niobium, vanadium, etc.; the latter has chromium, manganese, copper, iron, silicon, etc.
③ Elements that have little effect on phase transition temperature are neutral elements, such as zirconium and tin.
Characteristics of titanium alloy
Titanium is a new type of metal. The performance of titanium is related to the content of impurities such as carbon, nitrogen, hydrogen, and oxygen. The purest titanium iodide contains no more than 0.1% of impurities, but its strength is low and its plasticity is high.
- High strength
The density of titanium alloy is generally about 4.51g/cubic centimeter, which is only 60% of that of steel. The density of pure titanium is close to that of ordinary steel. Some high-strength titanium alloys exceed the strength of many alloy structural steels. Therefore, the specific strength (strength/density) of titanium alloy is much higher than other metal structural materials, and parts with high unit strength, good rigidity and light weight can be produced. Titanium alloys are used in engine components, skeletons, skins, fasteners and landing gears of aircraft.
- High heat intensity
The service temperature is several hundred degrees higher than that of aluminum alloys, and it can still maintain the required strength at moderate temperatures, and can work for a long time at a temperature of 450-500°C. These two types of titanium alloys still have high strength in the range of 150°C-500°C Specific strength, while the specific strength of aluminum alloy decreases significantly at 150 °C. The working temperature of titanium alloy can reach 500°C, while the working temperature of aluminum alloy is below 200°C.
- Good corrosion resistance
Titanium alloy works in humid atmosphere and seawater medium, and its corrosion resistance is far superior to that of stainless steel; it is particularly resistant to pitting corrosion, acid corrosion, and stress corrosion; it is resistant to alkali, chloride, chlorine, organic substances, nitric acid, and sulfuric acid. etc. have excellent corrosion resistance. However, titanium has poor corrosion resistance to reducing oxygen and chromium salt media.
- Good low temperature performance
Titanium alloys can maintain their mechanical properties at low and ultra-low temperatures. Titanium alloys with good low-temperature performance and extremely low interstitial elements, such as TA7, can maintain a certain degree of plasticity at -253°C. Therefore, titanium alloy is also an important low-temperature structure material.
- High chemical activity
Titanium has high chemical activity, and has strong chemical reactions with O, N, titanium alloy products, CO, CO2, water vapor, and ammonia in the atmosphere. When the carbon content is greater than 0.2%, hard TiC will be formed in the titanium alloy; when the temperature is high, it will also form a hard TiN surface layer when it interacts with N; when the temperature is above 600°C, titanium absorbs oxygen to form a hardened layer with high hardness ; When the hydrogen content rises, an embrittlement layer will also be formed. The hard and brittle surface produced by absorbing gas can reach a depth of 0.1-0.15 mm, and the hardening degree is 20%-30%. The chemical affinity of titanium is also large, and it is easy to cause adhesion with the friction surface.
- Small thermal conductivity
The thermal conductivity of titanium λ=15.24W/(m.K) is about 1/4 of that of nickel, 1/5 of that of iron, and 1/14 of that of aluminum, and the thermal conductivity of various titanium alloys is about 50% lower than that of titanium. The elastic modulus of titanium alloy is about 1/2 of that of steel, so its rigidity is poor and easy to deform. It is not suitable for making slender rods and thin-walled parts. times, resulting in severe friction, adhesion, and bond wear on the tool flank.
With the progress of industrialization, the standard of living has improved. More and more consumer product accessories and industrial accessories are made of alloy materials, especially in the die-casting process. The materials commonly used in die casting include the above four alloy materials, alüminyum alaşım, magnesium alloy, zinc alloy and titanium alloy. According to the use characteristics of various industries, different alloy materials can be selected for the application position.