Alüminyum dökümler, alüminyum malzeme kullanılarak kalıp döküm işlemi ile üretilen bileşenlerdir Çalışma prensibi, alüminyum malzemenin sıvı hale dönüştürülmesi için ısıtılmasını içerir. Sıvı alüminyum malzeme, bir enjeksiyon yöntemi kullanılarak bir kum veya metal kalıbın kalıp boşluğuna enjekte edilir. Kalıp boşluğu çeşitli şekil ve boyutlarda tasarlanabilir. Sıvı alüminyum malzeme boşluğu doldurduğunda, istenen şekli alır ve alüminyum dökümlerin üretilmesine neden olur.
Alüminyum malzemeler, erime noktaları ve sertliklerine göre farklı derecelerde saf alüminyum ve alüminyum alaşımlı malzemeler olarak sınıflandırılabilir. Kalıp döküm, bileşenler için bir üretim sürecidir ve ayrıca yüksek basınçlı kalıp döküm, düşük basınçlı kalıp döküm, yerçekimi kalıp döküm ve diğerleri olarak kategorize edilebilir. Alüminyum dökümler otomotiv, elektronik, makine, mobilya ve motorlar gibi çeşitli sektörlerde geniş uygulama alanı bulmaktadır. İlerleyen bölümlerde, alüminyum dökümlere kapsamlı bir giriş yapacağız.
Alüminyum dökümün gelişim tarihi
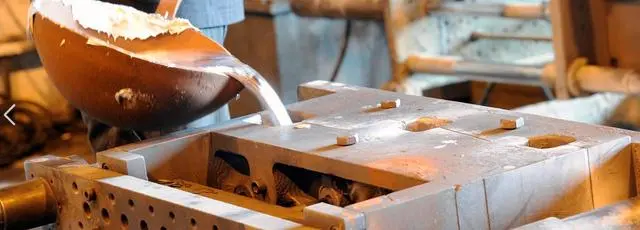
Kalıp döküm işlemi, kurşun-kalay ve alüminyum alaşımlı kalıp dökümlerin ilk kez baskı ekipmanları, ambalaj ve baskı türleri için kullanıldığı 19. yüzyılın başlarına kadar izlenebilir. Bu işlemin 150 yılı aşkın bir geçmişi vardır. 20. yüzyılın başlarında, alüminyum alaşımlı kalıp döküm teknolojisi ortaya çıkmaya başladı. 1905 yılında, endüstriyel üretime uygun kalıp döküm makineleri tanıtıldı ve alüminyum alaşımlı bileşenlerin kalıp dökümü popülerlik kazanmaya başladı. Ancak, o dönemde alaşım malzemelerindeki ve yapısal tasarımdaki sınırlamalar nedeniyle, alüminyum alaşımlı basınçlı döküm yalnızca sınırlı sayıda basit parça üretebiliyordu.
1927 yılında Çek mühendis Josef Polak sütun tipi bir soğuk oda teknolojisinde önemli bir gelişmeye işaret eden alüminyum kalıp döküm makinesi. Bu yenilik, yüksek derecede esneklik, maliyet etkinliği ve geliştirilmiş ürün performansı getirdi. Tasarım ve alüminyum kalıp döküm üretimi. 1952 yılında, eski Sovyetler Birliği'nde ilk sütun tipi soğuk hazneli alüminyum döküm makinesi üretildi ve alüminyum alaşımlı kalıp dökümlerin üretimi daha da yaygınlaştırıldı.
1966 yılına gelindiğinde, alüminyum dökümde hassasiyet, hız ve yoğunluk ilkeleri oluşturuldu ve 1969 yılında İngilizler oksijen enjeksiyonlu gaz gözeneksiz alüminyum döküm yöntemini tanıttı. 150 yıl boyunca, alüminyum döküm alanı ilk aşamalarından olgun bir endüstriye dönüşmüştür. Hem malzemeler hem de üretim teknikleri sürekli olarak gelişti ve pazar talebi genişledi. Üretim süreci boyunca, ürün kusurlarını azaltmak için alüminyum alaşımlarının bileşiminin iyileştirilmesi ve kalıpların uygun şekilde ayarlanması da dahil olmak üzere çeşitli optimizasyonlar uygulanmıştır.
Çeşitli bilimsel ve teknolojik gelişmelerin sürekli ilerlemesiyle birlikte alüminyum döküm, modern imalat endüstrilerinin tasarım, imalat ve montajında giderek daha hayati bir rol oynamaktadır. Üretim verimliliğini artırırken bileşen performansını da geliştirir. Pazar talebi artmaya devam ettikçe, alüminyum döküm yaygın olarak kullanılacak ve modern endüstriyel üretim teknolojisinin vazgeçilmez bir parçası haline gelecektir.
Alüminyum basınçlı döküm nedir?
Alüminyum basınçlı döküm olarak da bilinen alüminyum kalıp döküm, alüminyum alaşımlı bileşenler için üretim süreçlerinden biridir. Erimiş alüminyum alaşımının yüksek basınçta bir kalıba enjekte edilmesini ve ardından alüminyum alaşımlı kalıp parçaları elde etmek için katılaştırılmasını ve soğutulmasını içerir. Alüminyum kalıp döküm işlemi, malzeme hazırlama, kalıp tasarımı, kalıp imalatı, eritme ve döküm, titreşim tabanlı cüruf giderme ve ısıl işlem dahil olmak üzere birkaç adıma ayrılabilir. Alüminyum kalıp döküm aşağıdaki özellikleri sergiler:
- Ürünlerin şekillerinde yüksek karmaşıklık, hem iç hem de dış şekillerin yüksek hassasiyetle işlenmesini sağlar.
- Büyük boyutlu, yüksek mukavemetli ve hafif döküm bileşenler üretebilir.
- Seri üretime uygun kısa üretim döngüleri ile uygun maliyetli.
Bu süreçle üretilen alüminyum kalıp döküm bileşenleri otomotiv, havacılık, telekomünikasyon, elektronik, makine ve inşaat gibi sektörlerde geniş uygulama alanı bulmaktadır.
Basınçlı dökümler için alüminyum alaşımlı malzemeler
Alüminyum alaşımlı kalıp döküm malzemeleri öncelikle üç ana kategoriye ayrılır: alüminyum-silikon alaşımları, alüminyum-silikon-bakır alaşımları ve alüminyum-magnezyum alaşımları. İşte bu malzemelerin Çince isimleri ve karşılık gelen İngilizce çevirileri:
Alüminyum-Silikon Alaşımları:
- YL102 (ADC1, A413.0, vb.)
- YL104 (ADC3, A360, vb.)
Alüminyum-Silikon-Bakır Alaşımları:
- YL112 (A380, ADC10, vb.)
- YL113 (3830)
- YL117 (B390, ADC14, ADC12, vb.)
Alüminyum-Magnezyum Alaşımları:
- 302 (5180, ADC5, ADC6, vb.)
Alüminyum-silisyum alaşımlarında ve alüminyum-silisyum-bakır alaşımlarında, isimlerinden de anlaşılacağı gibi, alüminyum dışındaki ana bileşenler silisyum ve bakırdır. Silisyum içeriği tipik olarak 6-12% arasında değişir ve öncelikle alaşımın akışkanlığını artırır. Bakır içeriği ikincildir ve esas olarak mukavemet ve gerilme özelliklerini geliştirir. Demir içeriği tipik olarak 0.7-1.2% arasındadır ve bu aralıkta en iyi kalıp ayırma etkisini sağlar. Bileşimleri nedeniyle bu alaşımlar oksitlenmeye ve renklenmeye eğilimli değildir. Desilikonizasyon işlemleriyle bile istenen renklendirme etkisini elde etmek zordur. Öte yandan, alüminyum-magnezyum alaşımları oksitlenebilir ve renklendirilebilir, bu da önemli bir ayırt edici özelliktir.
Spesifik alüminyum alaşımlı kalıp döküm malzemeleri söz konusu olduğunda, yaygın olarak kullanılan bazı malzemeler ve uygulamaları şunlardır:
- 6061 Alüminyum Alaşım: Yüksek mukavemet, korozyon direnci ve iyi kaynaklanabilirlik sunar. Yüksek korozif ortamlardaki uygulamalar, yüksek yoğunluklu yapısal bileşenler, alet kutuları, aksesuarlar ve daha fazlası için uygundur.
- 7075 Alüminyum Alaşım: Yüksek mukavemeti, hafif özellikleri ve işleme kolaylığı ile bilinen bu alaşım, uçak yapısal bileşenlerinin, roket gövdelerinin ve süspansiyon sistemi parçalarının yapımında kullanılır.
- 383 Alüminyum Alaşım: Esas olarak otomotiv bileşenleri için kullanılır.
- 413 Alüminyum Alaşım: Mükemmel döküm performansı ve çatlak bastırma özellikleri sergiler, bu da onu aşağıdakiler de dahil olmak üzere çeşitli bileşenlerin üretimi için uygun hale getirir otomotiv ve havacılık endüstrisi parçaları.
- ADC12 Alüminyum Alaşımı: Bu alaşım iyi döküm performansı ve mekanik özellikler sunar ve otomotiv ve motosiklet parçalarının yanı sıra elektronik ürünler için tutamaklar gibi uygulamalarda yaygın olarak kullanılır.
Alüminyum döküm süreci nedir?
Alüminyum döküm süreci, dökümlerin kalitesini ve genel kalıplama etkisini sağlamada çok önemli olan bir dizi iyi tanımlanmış adımı içerir. Bu adımları ayrıntılı olarak inceleyelim:
- Kalıp Tasarımı ve İmalatı: Kalıp, alüminyum dökümde kritik bir araçtır ve tasarımı ve imalatı dökümlerin kalitesini önemli ölçüde etkiler. Kalıp tasarımı, alüminyum parçaların şekil ve boyut gereksinimlerinin dikkate alınmasını, uygun kalıp malzemelerinin seçilmesini ve yapısal tasarımı içerir. Yaygın kalıp üretim yöntemleri arasında manuel kalıp yapımı, CNC işleme ve 3D baskı yer alır.
- Alüminyum Alaşımının Eritilmesi: Dökümü kolaylaştırmak için alüminyum alaşımının veya saf alüminyumun eritilerek sıvı metal haline getirilmesi gerekir. Bu genellikle elektrikli veya gazlı fırınlar kullanılarak gerçekleştirilir. Alüminyum malzeme sıvı metale dönüşene kadar fırın içinde ısıtılır. Daha sonra, alüminyum parçaların mukavemetini ve sertliğini artırmak için temperleme işlemleri gerçekleştirilir.
- Dökme: Dökme adımı, erimiş alüminyumun kalıp içine enjekte edilmesini içerir. döküm kalıbı. Dökme sıcaklığı ve hızının hassas kontrolü, gözeneklilik, inklüzyonlar ve soğuk ayrışma gibi kusurları önlemek için çok önemlidir. Alüminyum sıvısının saflığının korunması da kirlilik kontaminasyonunu önlemek için gereklidir.
- Soğutma: Alüminyum sıvı döküm kalıbına enjekte edildikten sonra hızla soğur ve katılaşarak alüminyum parçanın ilk şeklini alır. Soğutma işlemi, alüminyum parçaların iç yapısının ve boyutunun stabilitesini sağlamak için soğutma hızlarının ve sıcaklık dağılımının dikkatli bir şekilde kontrol edilmesini gerektirir. Soğutma tipik olarak su veya soğutma gazı kullanılarak gerçekleştirilir.
- Kalıptan çıkarma: Soğutulmuş alüminyum parçalar, kalıptan çıkarma olarak bilinen bir işlemle döküm kalıbından dikkatlice çıkarılmalıdır. Kalıp titreşim cihazları ve kalıp boşaltma makineleri gibi özel alet ve ekipmanlar genellikle bu amaçla kullanılır. Kalıptan çıkarma, herhangi bir hasarı önlerken alüminyum parçaların bütünlüğünü ve yüzey kalitesini korumayı amaçlar.
- Çapak Alma: Kalıptan çıkarma işleminden sonra, alüminyum parçalar genellikle yüzey çapakları veya delinme izleri sergiler. Yüzey kalitesini artırmak için çapak alma işlemi gereklidir. Çapak alma yöntemleri arasında mekanik parlatma, kimyasal korozyon veya kumlama yer alabilir ve bunların tümü yüzey kusurlarını ortadan kaldırmaya yarar.
- Takip İşlemleri: Alüminyum döküm sürecinin son adımı, ısıl işlem, yüzey işlemi, işleme ve muayene dahil olmak üzere takip işlemlerini içerir. Isıl işlem alüminyum parçaların düzenini ve performansını artırırken, yüzey işlemi korozyon direncini ve estetiği geliştirir. İşleme, alüminyum parçaların hassas boyut ve şekil gereksinimlerini karşılamasını sağlar ve denetim, kalite ve güvenliği garanti eder.
Alüminyum döküm süreci karmaşık ve titizdir, her adım dikkatli bir tasarım ve uygulama gerektirir. Alüminyum parçaların kalitesini sağlamak ve istenen kalıplama etkisini elde etmek için her aşamada proses gerekliliklerine sıkı sıkıya bağlı kalmak şarttır. Alüminyum döküm süreçlerindeki sürekli yenilik ve iyileştirme, alüminyum imalat endüstrisinin ilerlemesi için değerli teknik destek sağlar.
Alüminyum Basınçlı Dökümün Avantajları
- Olgun Teknoloji: Alüminyum alaşımlı kalıp döküm teknolojisi köklüdür, çeşitli endüstrilerde yaygın olarak uygulanır ve kapsamlı üretim deneyimi ile desteklenir, istikrarlı ve güvenilir ürün kalitesi sağlar.
- Yüksek Hassasiyet ve Karmaşıklık: Alüminyum alaşımlı kalıp döküm, karmaşık bileşen tasarımlarının hızlı bir şekilde üretilmesini sağlarken, kullanım kolaylığını korur ve kapalı döngü proses kontrolü sağlar.
- Mükemmel Fiziksel Özellikler: Alüminyum alaşımları ideal mukavemet, korozyon direnci, termal iletkenlik ve mükemmel işlenebilirlik gibi olağanüstü fiziksel özellikler sunarak pazar taleplerini karşılar.
- İyi Mekanik Performans: Alüminyum döküm parçalar tek tip bileşim, düzenli tane yapısı, nispeten düşük yoğunluk, yüksek mukavemet, iyi süneklik ve mükemmel gerilme ve basınç mukavemeti sergiler.
- Yüksek Üretim Verimliliği: Alüminyum alaşımlı kalıp döküm teknolojisi, üretim verimliliğini önemli ölçüde artırır, iş gücü yoğunluğunu azaltır ve kısa bir zaman dilimi içinde büyük ölçekli üretim sağlar.
- İnce Duvarlı Hafif: Diğer döküm malzemeleriyle karşılaştırıldığında, alüminyum alaşımlı döküm parçalar daha ince üretim kalınlığına, daha düşük yoğunluğa sahip olabilir, ağırlık azaltmayı, ince duvar tasarımını kolaylaştırır ve bileşen hafifletme ve enerji tasarrufu sağlar.
- Uygun Maliyetli: Alüminyum alaşımlı kalıp döküm teknolojisi, diğer üretim süreçlerine göre maliyet avantajlarına sahiptir, kullanımı ve işletimi kolaydır, böylece rekabetçi bir fiyat avantajı sağlar.
- Geri dönüştürülebilirlik: Alüminyum alaşımlı malzemeler geri dönüştürülebilir ve çevrenin korunmasına katkıda bulunur.
- Pürüzsüz Yüzey: Döküm sonrası mekanik veya kimyasal işlemler, yüksek yüzey pürüzsüzlüğü sağlayarak kendi kendine satılan ürünlerin ve karmaşık montaj öğelerinin yüzey gereksinimlerini karşılar.
- Özelleştirme: Alüminyum alaşımlı döküm parçaların üretimi müşteri ihtiyaçlarına göre uyarlanabilir ve tasarım ve üretim süreçlerini maksimum ölçüde optimize etmek için sürekli olarak iyileştirilebilir.
- İyi Termal İletkenlik: Alüminyum alaşımlı kalıp döküm malzemeleri mükemmel termal iletkenlik sergileyerek elektrikli bileşenler veya makineler tarafından üretilen ısının hızlı bir şekilde dağıtılmasını sağlar.
- Hassas İşleme: Alüminyum alaşımlı kalıp döküm teknolojisi, geleneksel işleme süreçlerine kıyasla parça doğruluğunu ve iş verimliliğini önemli ölçüde artırarak yüksek hassasiyetli parça işleme olanağı sağlar.
- Yüksek Süneklik: Alüminyum alaşımlı malzemeler yüksek mukavemete, iyi sünekliğe, deformasyona karşı dirence ve çeşitli şekillerde işleme kolaylığına sahiptir ve karmaşık yapıların üretimi için gereksinimleri karşılar.
Alüminyum Basınçlı Döküm için Yüzey İşlem Prosesleri
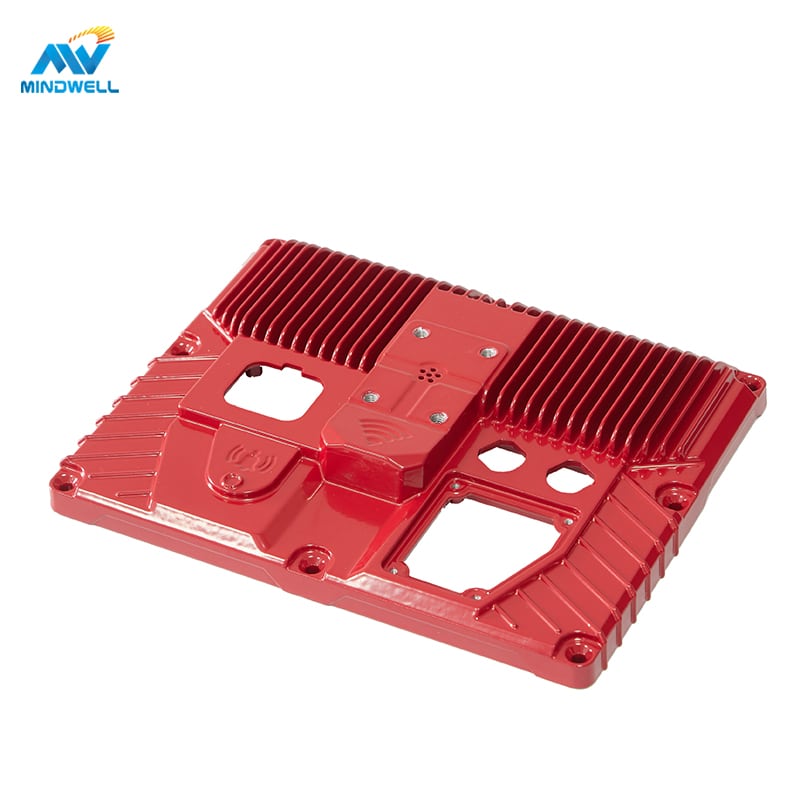
Alüminyum kalıp döküm çeşitli alüminyum alaşımlı bileşenlerin işlenmesinde kullanılan yaygın bir üretim yöntemidir. Bununla birlikte, alüminyum alaşımlı yüzeyler genellikle korozyona, aşınma ve yıpranmaya karşı dirençlerini ve görsel çekiciliklerini artırmak için işlem gerektirir. Bu makale, çeşitli geleneksel yüzey işlemlerini özetleyecektir alümi̇nyum alaşimli döküm i̇çi̇n prosesler.
Elektrokaplama Tekniği
Elektrokaplama, yüzeylerine bir metal veya alaşım tabakası biriktirerek alüminyum alaşımlarının özelliklerini geliştiren yaygın olarak kullanılan bir yüzey işleme yöntemidir. Yaygın elektrokaplama prosedürleri krom kaplama, nikel kaplama ve çinko kaplamayı kapsar. Krom kaplama alüminyum alaşımlarının hem korozyon direncini hem de estetik çekiciliğini artırabilirken, nikel kaplama dayanıklılıklarını artırır ve çinko kaplama korozyon direncini güçlendirir.
Kaplama Prosedürü
Kaplama basit ve etkili bir yüzey kaplamasıdır tedavi süreci alüminyum alaşımlarının yüzeylerine bir kat boya veya cila uygulayarak performanslarını artıran bir üründür. Kaplama hem hoş bir estetik etki hem de koruyucu özellikler sunar. Yaygın kaplama teknikleri arasında sprey kaplamalar, lak uygulamaları ve toz kaplamalar yer alır. Sprey kaplamalar alüminyum alaşımlarının çeşitli renk ve dokular sergilemesini sağlar, lak uygulamaları hava koşullarına karşı dayanıklılıklarını artırır ve toz kaplamalar sertliklerini ve aşınmaya karşı dirençlerini artırır.
Oksidasyon Yöntemi
Oksidasyon, alüminyum alaşımları için yüzeyde bir oksit film tabakası oluşturarak özelliklerini geliştiren geleneksel bir yüzey işleme sürecidir. Oksidasyon, alüminyum alaşımlarının korozyon direncini, aşınma direncini ve yalıtım özelliklerini yükseltir. Yaygın oksidasyon yöntemleri arasında eloksal ve kimyasal oksidasyon yer alır. Eloksal tek tip ve yoğun bir oksit filmi üretirken, kimyasal oksidasyon farklı renk ve dokulara sahip bir oksit filmi oluşturur.
Kumlama Tekniği
Kumlama, yüzey boyunca yüksek hızlı kumlanmış parçacık akışlarını iterek alüminyum alaşımlarının yüzey kalitesini artıran rutin bir yüzey işleme işlemidir. Kumlama, oksit tabakalarını ve kirleticileri ortadan kaldırarak pürüzsüz ve eşit bir alüminyum alaşım yüzeyi elde edilmesini sağlar. Ayrıca yüzeyin pürüzlülüğünü artırarak kayganlığı ve yapışmayı geliştirir.
Parlatma İşlemi
Parlatma, alüminyum alaşımının yüzeyini mekanik olarak parlatarak yüzeyin finisajını ve düzlüğünü artıran, sıklıkla kullanılan bir yüzey işleme tekniğidir. Parlatma, yüzeye ayna benzeri bir etki kazandırarak estetiğini ve optik özelliklerini geliştirir. Yaygın parlatma yöntemleri arasında mekanik parlatma, elektrolitik parlatma ve kimyasal parlatma yer alır.
Sonuç olarak, alüminyum alaşımlı döküm için yüzey işleme süreçleri elektrokaplama, kaplama, oksidasyon, kumlama ve parlatmayı kapsar. Bu prosedürler alüminyum alaşımlarının genel kalitesini ve hizmet ömrünü artırırken korozyon direncini, aşınma direncini ve görsel çekiciliği geliştirmeye hizmet eder. Bu yöntemleri pratik uygulamalarda kullanırken, özel gereksinimlere göre uygun yüzey işleme prosesinin seçilmesi ve proses parametrelerinin titizlikle kontrol edilmesi, işlem sonuçlarının kararlılığını ve tutarlılığını sağlamak için gereklidir.
Alüminyum Basınçlı Döküm, Kum Döküm ve Vakumlu Basınçlı Döküm Arasındaki Farklar

Alüminyum Basınçlı Döküm
Alüminyum döküm, kalıp boşlukları içinde soğutmak ve katılaştırmak için yüksek basınçlı erimiş metal kullanımını içerir ve istenen alüminyum alaşımlı bileşenleri oluşturur. Bu süreç, yüksek üretim verimliliği ve düşük maliyet gibi avantajlar sunar.
Alüminyum dökümün avantajları arasında yüksek üretim verimliliği, düşük maliyet ve büyük ölçekli üretime uygunluk yer almaktadır. Bununla birlikte, nispeten yüksek hurda oranı, işlem sonrası gereksinim potansiyeli ve çeşitli faktörlerin basınçlı döküm parçaların kalitesi üzerindeki etkisi gibi dezavantajları vardır.
Alüminyum basınçlı döküm, büyük ölçekli üretim ve genel makine, mobilya ve elektronik ürün endüstrileri gibi yüksek üretim verimliliğinin gerekli olduğu senaryolar için uygundur.
Kum Döküm
Kum dökümGenellikle en eski ve en çok yönlü döküm yöntemi olarak anılan bu yöntem, tek bir kalıbı paylaşarak ve küçük seri üretim için aynı kum kalıbı yeniden kullanarak aynı anda birçok özdeş parçayı dökebilir. Bununla birlikte, bu yöntem tipik olarak nihai üründe daha az ayrıntı veya pürüzlü bir yüzeyle sonuçlanır ve bu da genellikle kullanımdan önce işleme, parlatma ve son işlem gerektirir.
Kum dökümün avantajları:
- Düşük üretim maliyeti: Kum döküm, daha düşük hammadde giderleri ve nispeten basit bir üretim süreci nedeniyle genellikle diğer döküm yöntemlerine kıyasla daha düşük üretim maliyetlerine neden olur.
- Yüksek çok yönlülük: Kum döküm, çok çeşitli karmaşık şekilli dökümler üretebilir ve döküm yüzeylerinde çeşitli desenler ve yazılar oluşturabilir.
- Yüksek işleme hassasiyeti: Kum döküm, döküm boyutlarında ve yüzey pürüzlülüğünde yüksek hassasiyet elde edebilir.
- Kısa üretim döngüsü: Kum dökümün üretim döngüsü, prosesin basitliği ve kısa kuruma ve sertleşme süreleri nedeniyle diğer döküm yöntemlerine kıyasla daha kısadır.
Kum döküm, düşük üretim maliyetleri, yüksek çok yönlülük, yüksek işleme hassasiyeti ve kısa üretim döngüleri gibi avantajlara sahip yaygın bir döküm yöntemi olsa da, ortalama yüzey kalitesi, kum çekirdeği çökmesine yatkınlık ve uzun serbest bırakma süreleri gibi dezavantajlarının pratik koşullara göre değerlendirilmesi gerekir.
Vakumlu Basınçlı Döküm
Vakumlu basınçlı döküm, basınçlı döküm sırasında kalıp boşluğundan havayı uzaklaştırarak erimiş metalin vakum altında boşluğu doldurmasını sağlayan ve hassas basınçlı döküm parçalar elde edilmesini sağlayan bir işlemdir. Bu yöntem gaz sıkışmasını etkili bir şekilde azaltır, basınçlı döküm parçaların yoğunluğunu ve mekanik özelliklerini geliştirir.
Vakumlu basınçlı dökümün avantajları arasında basınçlı döküm parçaların yoğunluğunu ve mekanik özelliklerini iyileştirmek, gaz sıkışmasını azaltmak, hurda oranlarını düşürmek ve ürün kalitesini artırmak yer alır. Bununla birlikte, yüksek ekipman maliyetleri ve nispeten daha düşük üretim verimliliği gibi dezavantajları vardır.
Vakumlu basınçlı döküm, otomotiv, havacılık ve üst düzey alet endüstrileri gibi basınçlı döküm parçalarda yüksek yoğunluk ve üstün mekanik özellikler gerektiren uygulamalar için uygundur.
Pratik üretimde, uygun bir üretim sürecinin seçimi belirli gereksinimlerle uyumlu olmalıdır ve tutarlı ve istikrarlı tedavi sonuçları sağlamak için süreç parametrelerine dikkat edilmesi hayati önem taşır. Teknoloji ilerledikçe, bu üretim süreçleri gelişmeye ve optimize edilmeye devam edecek, üretim endüstrisindeki ilerlemelere katkıda bulunarak çeşitli alanlarda daha yüksek verimlilik ve kalite vaat edecektir.
Alüminyum Basınçlı Döküm Uygulamaları
- Otomotiv Endüstrisi: Alüminyum döküm, otomotiv endüstrisinde motor silindir kafaları, şanzıman muhafazaları, debriyaj muhafazaları, su pompası muhafazaları, karbüratör muhafazaları ve direksiyon dişlisi muhafazaları gibi bileşenlerin üretiminde yaygın olarak kullanılmaktadır.
- Elektronik ve Elektrikli Aletler: Elektronik ve elektrikli ev aletleri alanında, alüminyum döküm çeşitli muhafazalar, ısı alıcıları ve diğer bileşenleri üretmek için kullanılır.
- Mekanik Aletler: Alüminyum döküm, tutamaklar, muhafazalar, braketler ve daha fazlası dahil olmak üzere mekanik aletler için çeşitli bileşenlerin üretiminde kullanılır.
- Diğer Alanlar: Alüminyum döküm ayrıca havacılık, telekomünikasyon, mobilya dökümü, bahçecilik, aydınlatma armatürleri, ev aletleri, abajurlar, mutfak eşyaları, mobilya aksesuarları, dijital kasalar, işçilik, güvenlik ürünleri kasaları, LED aydınlatma (abajurlar) ve bazı yeni enerji endüstrileri gibi sektörlerde de uygulama alanı bulmaktadır.
Sonuç
İmalat endüstrisinde alüminyum döküm, bileşenleri oluşturmak için erimiş alüminyumun kalıplara enjekte edilmesini ve ardından yüksek kaliteli parçalar üretmek için soğutulmasını içeren çok yönlü bir süreçtir. Bu yöntem otomotiv, elektronik ve makine gibi sektörlerde yaygın uygulama alanı bulmaktadır. Basınçlı döküm süreci kalıp tasarımı, alüminyum eritme, döküm, soğutma, kalıptan çıkarma, çapak alma ve sonraki işlemler gibi kritik adımları kapsar. Başarıya ulaşmak için hassasiyet ve süreç gerekliliklerine bağlılık büyük önem taşır.
Alüminyum dökümün avantajları arasında köklü teknoloji, yüksek hassasiyet, hafif ancak sağlam bileşenler ve maliyet etkinliği bulunmaktadır. Ayrıca, elektrokaplama ve kaplama gibi yüzey işlemleri korozyon direncini ve estetiği artırabilir. Alüminyum basınçlı döküm, verimliliği ve maliyet etkinliği ile bilinir ve hassasiyeti, çok yönlülüğü ve ürün kalitesi nedeniyle döküm yöntemleri arasında öne çıkmasını sağlar. Teknoloji ilerledikçe, bu yöntem çeşitli sektörlerde ilerleme sağlamaya devam etmektedir.