LED 전구용 알루미늄 다이캐스팅
LED 전구의 알루미늄 다이캐스팅 부분은 압력 주조 알루미늄 합금으로 만든 액세서리입니다. 램프의 보호 성능과 외관을 향상시킬 수 있습니다. 동시에 다양한 사양과 모양을 사용자 지정하여 다양한 유형과 모델의 LED 램프의 요구 사항을 충족할 수 있습니다.
알루미늄 액세서리는 열을 발산하고 LED 부품을 지지하고 보호하는 데 도움이 될 수 있습니다. 마인드웰은 맞춤형 LED 전구를 제공합니다. 알루미늄 다이캐스팅 서비스를 포함합니다:
- LED 조명 하우징
- 방열판
- LED 전등갓
- LED 드라이버 하우징
- LED 브래킷
- 렌즈 후드
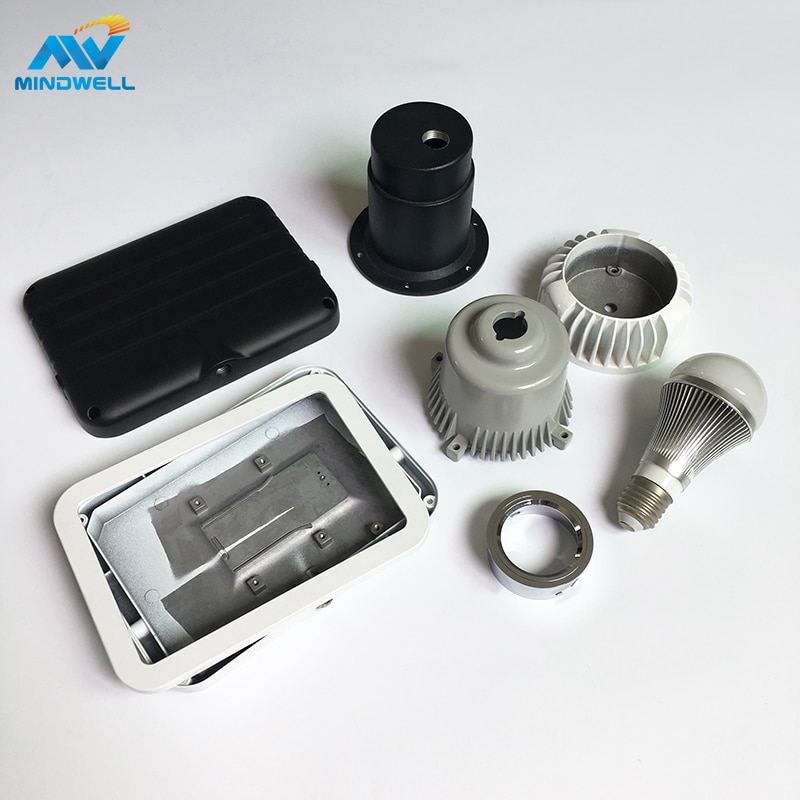
LED 조명 제조에서 알루미늄 다이캐스팅의 역할
알루미늄 다이캐스팅은 LED 전구 제조에 중요한 역할을 하며 주로 램프 홀더, 쉘, 라디에이터 및 기타 LED 램프의 구성 요소를 만드는 데 사용됩니다. 알루미늄 다이캐스팅의 장점은 소재가 강하고 가볍고 단단하다는 것입니다. 램프의 품질 요구 사항을 충족하는 동시에 무게를 최대한 줄여 램프를 더 안전하고 안정적으로 만듭니다. 또한 알루미늄은 방열 측면에서 열전도율이 뛰어나며 LED 전구는 일반적으로 장기적인 안정성과 신뢰성을 유지하기 위해 열 방출이 우수해야합니다. 따라서 전구에서 발생하는 열을 멀리 전도하기 위해 LED 전구의 하우징으로 사용됩니다.
간단히 말해, 당사는 알루미늄 합금 다이캐스팅을 사용하여 알루미늄 케이스를 제작합니다. 제조 공정이 비교적 간단하고 빠르고 효율적으로 생산할 수 있어 생산 비용을 절감할 수 있습니다. 일반적으로 내부 회로 기판 뒤에 알루미늄 라디에이터를 설치하여 방열 기능을 높이고 외부에 브래킷을 추가하여 고정 설치를 용이하게합니다. 다이캐스팅 쉘의 표면 처리는 일반적으로 실외에서 일부는 폴리 에스테르 스프레이로, 일부는 불소로 뿌립니다. 카본 스프레이, 특수 보호 요구 사항이 있는 실외용 분말.
요컨대, 알루미늄 다이캐스팅은 주로 LED 전구 제조에서 방열, 열 전도, 경량 및 부식 방지 역할을 합니다.

조명 산업에서 알루미늄 합금 다이캐스팅 액세서리 적용의 장점
가벼운 무게
알루미늄 합금의 밀도는 강철 및 기타 소재보다 작습니다. 알루미늄 합금 다이캐스트 액세서리를 사용하면 램프의 무게를 줄이고 운송 및 설치를 용이하게 할 수 있습니다.
높은 열 전도성
알루미늄 합금은 열전도율이 높아 LED 램프 비드에서 발생하는 열을 빠르게 발산하고 LED 램프의 수명을 연장하는 데 도움이 됩니다.
간편한 처리
알루미늄 합금은 가소성이 좋고 다양한 모양으로 쉽게 가공할 수 있어 다양한 형태의 LED 램프를 쉽게 제작할 수 있습니다.
저렴한 비용
알루미늄 합금은 비교적 저렴하고 일반 사용자가 사용할 수 있어 LED 램프의 비용을 절감하는 데 도움이 됩니다.
산화 방지
알루미늄 표면에는 산화 알루미늄 층이 조밀하게 형성되어 있어 산화 및 부식 방지에 좋은 효과가 있어 생산된 LED 램프의 내구성을 보장합니다.
요약하면 알루미늄 합금 다이캐스팅 액세서리는 장비의 방열 성능을 개선하고 장비의 무게를 줄이며 장비의 미학을 개선하는 등 조명 산업에서 광범위한 응용 전망을 가지고 있습니다. 마인드웰 컴퍼니는 고품질 다이캐스팅 금형 및 알루미늄 합금 제품을 전문적으로 제공하는 제조업체입니다. 고품질 제품, 첨단 기술 및 우수한 서비스로 업계의 찬사를 받았습니다.
LED 전구 방열판
LED 칩이 작동할 때 일정량의 열이 발생하기 때문에 방열 성능은 LED 전구 설계에서 매우 중요합니다. 열 방출이 좋지 않으면 LED 칩의 온도가 너무 높아져 LED 전구의 수명과 성능에 영향을 미칩니다.
알루미늄 다이캐스팅이 LED 전구의 방열 성능을 향상시키는 방법
- 알루미늄 다이캐스팅은 열전도율과 방열 기능이 뛰어나기 때문에 LED 전구에서 중요한 역할을 합니다. 다음은 알루미늄 다이캐스팅이 LED 전구의 열 성능을 향상시키는 몇 가지 주요 측면입니다:
- 열 방출 방법: 일반적으로 자연 방열과 강제 공기 냉각의 두 가지 유형이 있으며, 특정 작업 환경과 요구 사항에 따라 선택해야 합니다.
- 방열 구조 최적화: 알루미늄 다이캐스팅을 통해 복잡한 방열판과 핀이 있는 라디에이터 구조를 설계하여 방열 표면적을 넓혀 방열 효율을 향상시킬 수 있습니다. 이를 통해 LED 전구의 온도를 제어할 수 있습니다.
- 소재 안정성: 알루미늄 합금은 열전도율이 뛰어나 LED에서 발생하는 열을 빠르게 전달할 수 있습니다. 이는 전구의 외부 표면으로 열을 분산시켜 LED 소자 주변에 열이 쌓이는 것을 방지합니다. 또한 알루미늄 합금 소재는 다양한 온도에서도 안정성을 유지할 수 있으며 변형이나 팽창이 잘 일어나지 않습니다. 따라서 온도 변화로 인한 성능 문제 없이 장기간 작동하는 동안 LED 전구의 구조적 안정성을 유지할 수 있습니다.
요약: LED 전구의 설계 과정에서 알루미늄 다이캐스팅은 LED 전구의 방열 성능에 중요한 역할을 하여 LED 전구의 열 관리 문제를 해결하고 LED의 수명을 연장하며 성능과 신뢰성을 개선하는 데 도움을 줍니다. 마인드웰에서는 시뮬레이션 실험 등을 통해 조정 및 최적화를 수행하여 LED 전구의 방열 성능이 우수하도록 합니다.

LED 전구 알루미늄 하우징
LED 전구 알루미늄 하우징은 LED 전구 구조의 중요한 부분입니다. LED 전구 알루미늄 하우징은 경량, 고강도 및 높은 안정성의 특성을 가지고 있습니다. LED 부품을 보호하고 전구의 안정성을 보장 할 수 있습니다. LED 전구 알루미늄 하우징은 LED 조명 솔루션의 수명, 성능 및 미학을 개선하는 데 도움이됩니다.
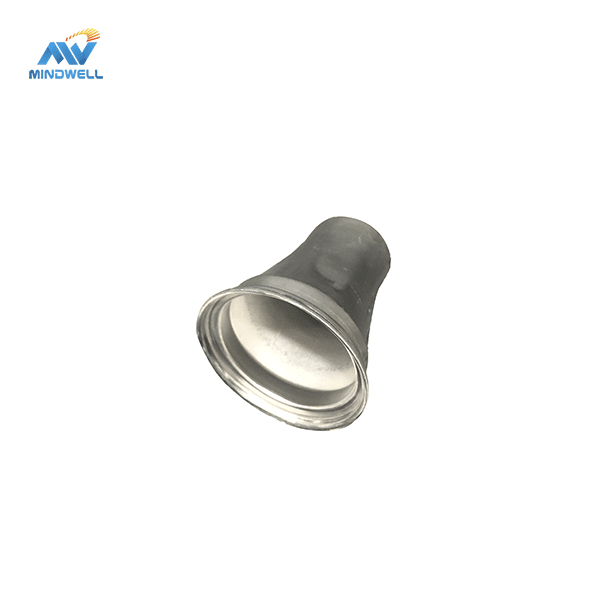
LED 전구 설치 수정
알루미늄 다이캐스팅은 LED 전구의 강력한 구조적 지지력을 제공하며, 이는 LED 부품의 올바른 설치와 장기적인 안정성을 보장하는 데 필수적입니다. 알루미늄 다이캐스팅이 구조적 지지력을 제공하는 역할을 하는 방법은 다음과 같습니다:
- 견고하고 안정적인
- 진동 및 내충격성
- 강도와 가벼움
- 내식성
요약하면, 알루미늄 다이캐스팅은 구조적 지지력을 제공하는 동시에 알루미늄의 강도와 안정성은 LED 부품을 장기간 안정적으로 설치하여 다양한 환경에서 LED 전구의 성능과 안정성을 유지할 수 있도록 합니다. 이는 고객의 요구와 기대를 충족하는 데 필수적인 요소입니다.

알루미늄 다이캐스팅은 지속 가능성과 환경적 이점이 있습니다.
재활용 가능성
알루미늄은 재활용성이 높은 금속으로, 폐 알루미늄 다이캐스팅을 녹여 모양을 바꿔 새로운 다이캐스팅 제품에 다시 사용할 수 있습니다. 이러한 재활용 프로세스는 원자재를 절약할 뿐만 아니라 폐기물로 인한 환경 오염도 줄일 수 있습니다.
재료 낭비 줄이기
알루미늄 다이캐스팅 공정은 다이캐스팅 공정의 특성상 사용되는 재료의 양을 정밀하게 제어할 수 있어 생산 공정 중 낭비를 줄일 수 있습니다. 알루미늄 다이캐스팅은 다른 금속 가공 방법보다 재료를 더 효율적으로 활용하기 때문에 재료 낭비가 적습니다.
에너지 절약 및 탄소 발자국 감소의 이점
알루미늄 다이캐스팅은 다른 금속 가공 방법보다 효율적이며 에너지 소비를 줄일 수 있습니다. 동시에 알루미늄의 가벼운 특성으로 인해 알루미늄 다이캐스팅을 사용하면 제품의 무게를 줄일 수 있어 운송 및 사용 중 에너지 소비를 줄여 탄소 발자국을 줄일 수 있습니다.
알루미늄 다이캐스팅은 알루미늄 재활용성, 재료 낭비 감소, 에너지 소비 및 탄소 발자국 감소 등 다양한 지속 가능성 및 환경적 이점을 제공합니다. 따라서 환경 보호와 지속 가능한 개발 원칙에 부합하는 환경 친화적인 제조 방식입니다.
LED 전구용 알루미늄 다이캐스팅: 조명 혁신
LED 전구용 알루미늄 다이캐스팅의 혁신적인 역할에 대해 알아보세요. 정확도 엔지니어링, 내구성 및 사용자 지정 옵션에 대해 자세히 알아보세요. 이 포괄적인 내용을 통해 이해의 폭을 넓혀보세요. 알루미늄 다이캐스팅 가이드 LED 전구용.
1. 알루미늄 다이캐스팅의 기원
알루미늄 다이캐스팅의 역사는 19세기로 거슬러 올라갑니다. 중요한 제조 방법인 알루미늄 다이캐스팅은 LED 전구 및 기타 분야에서 중요한 역할을 합니다. 정밀 엔지니어링의 설계 및 생산을 통해 알루미늄 다이캐스팅 공정은 복잡한 모양과 미세한 구조를 가진 부품을 만들어 빛의 방향과 분포를 정밀하게 제어하여 LED 전구의 최상의 성능을 달성 할 수 있습니다. 앞으로 기술의 지속적인 발전과 응용 요구 사항이 증가함에 따라 알루미늄 다이캐스팅 공정은 지속적으로 발전하고 혁신하여 제조 산업 발전에 더 큰 기여를 할 것입니다. 자세한 개발 프로세스와 관련하여 다음과 같은 측면에서 살펴볼 수 있습니다:
- 알루미늄 다이캐스팅 기술의 기원: 19세기 후반, 산업 혁명의 발전과 제조 기술의 지속적인 발전으로 다이캐스팅 기술은 점차 사람들의 관심을 끌기 시작했습니다. 초기 다이캐스팅 기술은 주로 납형과 같은 작고 단순한 금속 부품을 생산하는 데 사용되었습니다. 이 시기의 다이캐스팅 기계는 주로 수동 피스톤식 핫 챔버 다이캐스팅 기계로, 생산 효율과 정밀도가 상대적으로 낮았습니다.
- 20세기에 접어든 후 다이캐스팅 기술은 더욱 발전하여 사용되었습니다. 1905년 H.H. Doehler는 산업 생산용 다이캐스팅 기계를 성공적으로 개발했습니다. 이 발명은 다이캐스팅 기술이 대규모 고효율 생산이 가능하다는 것을 보여주었습니다. 제조 기술의 지속적인 발전과 함께 다이캐스팅 공정의 생산 효율성과 품질도 지속적으로 향상되었습니다.
- 알루미늄 다이캐스팅 기술의 발전: 20세기 전반기에 알루미늄 다이캐스팅 기술이 점차 개발되고 적용되었습니다. 알루미늄의 가벼움과 우수한 전기 전도성으로 인해 알루미늄 다이캐스팅은 전자, 전기 및 기타 분야에서 널리 사용됩니다. 기술의 지속적인 발전과 적용으로 알루미늄 다이캐스팅 공정은 더욱 개선되고 혁신되었습니다. 최신 알루미늄 다이캐스팅 공정은 복잡한 모양과 미세한 구조를 가진 알루미늄 다이캐스팅 부품을 생산할 수 있으며 생산 효율성과 제품 품질이 크게 향상되었습니다.
- LED 전구에 알루미늄 다이캐스팅 기술 적용: LED 전구 생산에서 알루미늄 다이캐스팅 기술은 내부 고정밀 부품을 제조하는 데 널리 사용됩니다. 이러한 구성 요소는 LED 전구의 발광 효율과 수명을 개선하는 데 중요한 역할을 합니다. 정밀 엔지니어링의 설계 및 생산을 통해 알루미늄 다이캐스팅 공정은 복잡한 모양과 미세한 구조를 가진 부품을 만들어 빛의 방향과 분포를 정밀하게 제어하여 LED 전구의 최상의 성능을 달성할 수 있습니다.
2. LED 전구에서 알루미늄 다이캐스팅의 장점은 다음과 같습니다.
LED 전구에서 알루미늄 다이캐스팅의 장점은 주로 높은 열효율, 긴 서비스 수명, 경량 및 내구성, 설계 유연성에 반영됩니다. 이러한 장점으로 인해 알루미늄 다이캐스팅 공정은 LED 조명 분야에서 광범위한 응용 전망과 시장 잠재력을 가지고 있습니다. 아래에서는 LED 전구에서 알루미늄 다이캐스팅 부품의 장점을 자세히 소개합니다:
1. 높은 열 효율
알루미늄은 열전도율이 뛰어나 알루미늄 다이캐스팅이 LED 전구의 열을 효과적으로 전도하고 발산할 수 있습니다. LED 전구는 작동할 때 많은 양의 열을 발생시킵니다. 열을 효과적으로 방출하지 못하면 LED 칩의 온도가 상승하여 발광 효율과 수명에 영향을 미칩니다. 알루미늄 다이캐스팅의 높은 열전도율은 LED 전구가 작동 중에 적절한 온도를 유지하고 과열로 인한 성능 저하 및 수명 단축을 방지할 수 있습니다.
2. 긴 서비스 수명
알루미늄 다이캐스팅 부품은 방열 성능이 우수 할뿐만 아니라 내식성과 내마모성이 높기 때문에 알루미늄 다이캐스팅 부품은 LED 전구의 안정적인 작업 조건을 오랫동안 유지하고 LED 전구의 수명을 연장 할 수 있습니다. 동시에 알루미늄 다이캐스팅 부품의 고정밀 제조 및 안정적인 치수 정확도는 장기간 사용시 LED 전구의 안정성과 신뢰성을 보장합니다.
3. 가볍고 내구성
알루미늄은 밀도가 낮고 무게가 가벼워 LED 전구에서 알루미늄 다이캐스팅을 경량화합니다. 동시에 알루미늄 다이캐스팅 부품은 강도가 높고 인성이 우수하며 외력에 의한 충격과 진동에 견딜 수 있어 열악한 환경에서도 LED 전구의 정상적인 작동을 보장합니다. 가볍고 내구성이 뛰어난 알루미늄 다이캐스팅은 LED 조명 솔루션의 전반적인 효율을 개선하고 에너지 소비를 줄이는 데 도움이 됩니다.
4. 설계 유연성
알루미늄 다이캐스팅 공정은 복잡한 모양과 미세한 구조의 제조를 실현할 수 있어 LED 전구 디자인에 더 많은 가능성을 제공합니다. 디자이너는 상상력을 마음껏 발휘하여 다양한 고객의 요구를 충족하는 독특하고 아름다운 LED 전구 모양을 다양하게 만들 수 있습니다. 동시에 알루미늄 다이캐스팅의 고정밀 제조는 LED 전구의 광학 성능과 사용 효과도 보장합니다.

3. LED 조명 애플리케이션
알루미늄 다이캐스팅은 하우징부터 LED 어셈블리의 복잡한 부품에 이르기까지 폭넓게 적용되어 LED 조명 애플리케이션에서 핵심적인 역할을 합니다. 이러한 다양성과 적응성은 다양한 환경에서 LED 전구의 효율적이고 안정적인 성능을 보장합니다. 다음은 LED 조명에서 알루미늄 다이캐스팅의 주요 응용 분야 중 일부입니다:
하우징 및 방열판
방열 효과: 알루미늄 다이캐스트 하우징과 라디에이터는 높은 열전도율을 사용하여 LED 칩에서 발생하는 열을 주변 환경으로 효과적으로 전도 및 방출하여 과열을 방지하고 LED 전구의 안정성과 긴 수명을 보장합니다.
가볍고 튼튼합니다: 알루미늄의 가벼운 특성 덕분에 LED 조명기구는 충분한 강도와 내구성을 유지하면서 더 가볍고 설치 및 휴대가 간편합니다.
반사경 및 광학 장치
정밀한 조명 제어: 알루미늄 다이캐스팅은 복잡한 반사판과 렌즈를 제조하여 빛의 방향과 분포를 정밀하게 제어하여 광 효율과 조명 품질을 개선할 수 있습니다.
내식성: 알루미늄 다이캐스팅은 내식성이 우수하여 습하거나 부식성이 있는 환경에서도 안정적인 광학 성능을 유지할 수 있습니다.
회로 기판 및 전자 부품 홀더
전기적 특성: 알루미늄은 전기 전도성이 뛰어나 회로 기판과 전자 부품 지지대에 이상적인 소재로, 전기의 원활한 흐름을 보장합니다.
정밀한 위치 지정: 알루미늄 다이캐스팅 공정의 높은 정밀도는 전자 부품의 정확한 위치 지정과 설치를 보장하여 LED 전구의 전반적인 성능을 향상시킵니다.
커넥터 및 고정 장치
안정성: 알루미늄 다이캐스트 커넥터와 고정 장치는 강력한 지지력과 안정성을 제공하여 진동이나 충격 환경에서도 LED 전구가 정상적으로 작동할 수 있도록 합니다.
가공의 용이성: 알루미늄은 가공이 쉬워 커넥터와 픽스처를 다른 부품과 쉽게 조립할 수 있어 생산 효율성이 향상됩니다.
창의적인 디자인 및 사용자 지정
디자인 유연성: 알루미늄 다이캐스팅 공정의 높은 유연성 덕분에 디자이너는 시장과 소비자의 다양한 요구를 충족하는 독특하고 맞춤형 LED 전구를 다양하게 제작할 수 있습니다.
비용 관리: 알루미늄 다이캐스팅 공정은 저렴한 비용을 유지하면서 대량 생산이 가능하여 고품질의 LED 조명 제품을 더 많은 사람들이 이용할 수 있게 해줍니다.
전반적으로 LED 조명 애플리케이션에서 알루미늄 다이캐스팅의 다양성과 적응성은 다양한 환경에서 LED 전구의 고효율과 안정적인 성능을 보장합니다. 기술의 지속적인 발전과 시장 수요의 성장에 따라 LED 조명 분야에서 알루미늄 다이캐스팅 부품의 적용은 더욱 광범위하고 심층적으로 이루어질 것입니다.
4. 생산 프로세스
LED 전구의 알루미늄 다이캐스트 부품을 생산하는 것은 여러 단계의 매우 섬세한 공정으로, 각 단계는 최종 제품의 품질과 성능에 매우 중요합니다. 다음은 제조 공정의 주요 단계입니다:
금형 설계 및 제조:
디자인: LED 전구의 사양 및 요구 사항에 따라 CAD 소프트웨어를 사용하여 금형을 설계합니다.
재료 선택: 금형의 내구성과 정밀도를 보장하기 위해 알루미늄 다이캐스팅에 적합한 금형 재료(일반적으로 고경도 강철)를 선택합니다.
가공: CNC 공작 기계 및 기타 고정밀 장비를 사용하여 금형을 가공하여 금형의 정확성과 표면 품질을 보장합니다.
알루미늄 다이캐스팅 생산:
제련: 알루미늄 잉곳을 녹는점까지 가열하고 제련 과정에서 불순물을 제거합니다.
주입: 예열된 금형에 용융 알루미늄을 고압으로 주입하여 액체 알루미늄이 금형 캐비티를 완전히 채우도록 합니다.
냉각 및 응고: 용융된 알루미늄을 금형에서 식히고 응고시켜 원하는 부품 모양을 형성합니다.
탈형: 금형을 열고 굳은 알루미늄 다이 캐스팅을 꺼냅니다.
포스트 프로세싱 및 마무리:
트리밍: 다이캐스트 부품의 가장자리에서 버와 여분의 재료를 제거합니다.
열처리: 알루미늄 다이캐스팅의 기계적 특성은 열처리 공정을 통해 더욱 향상됩니다.
표면 처리: 스프레이 및 전기 도금과 같은 표면 처리를 수행하여 부품의 내식성과 미관을 개선합니다.
검사 및 QC:
치수 검사: 측정 도구를 사용하여 알루미늄 다이캐스팅의 치수 검사를 수행하여 설계 요구 사항을 충족하는지 확인합니다.
성능 테스트: 압력 테스트, 인장 테스트 등을 수행하여 알루미늄 다이캐스팅의 성능 지표를 검증합니다.
외관 검사: 제품의 표면 품질을 점검하여 결함이나 결함이 없는지 확인합니다.
5. 사용자 지정 옵션
알루미늄 다이캐스팅 공정의 높은 유연성은 LED 전구 제조업체에게 다양한 맞춤형 옵션을 제공합니다. 이러한 옵션은 독특한 디자인과 기능에 대한 시장과 소비자의 요구를 충족시킬 뿐만 아니라 경쟁이 치열한 LED 시장에서 제조업체가 돋보일 수 있도록 도와줍니다. 다음은 사용자 지정 옵션 중 몇 가지 주요 사항입니다:
- 모양 및 크기 사용자 지정: 제조업체는 고객의 요구 또는 특정 애플리케이션 시나리오에 따라 LED 전구의 모양과 크기를 맞춤화할 수 있습니다. 전통적인 구형, 튜브 모양 또는 보다 창의적인 특수 모양 디자인 등 알루미늄 다이캐스팅 공정을 통해 모두 구현할 수 있습니다.
- 방열 구조 최적화: LED 전구의 방열 요구 사항에 따라 제조업체는 라디에이터의 구조와 크기를 맞춤화하여 LED 칩이 다양한 작업 환경에서 효과적으로 열을 방출할 수 있도록 하여 제품 수명을 연장할 수 있습니다.
- 광학 성능 조정: 제조업체는 반사판 및 렌즈와 같은 광학 부품의 모양과 표면 처리를 조정하여 다양한 조명 요구 사항을 충족하도록 LED 전구의 배광 및 효율을 맞춤화할 수 있습니다.
- 맞춤형 표면 처리: 알루미늄 다이캐스팅 부품의 표면 처리도 색상, 질감, 코팅 등을 포함하여 맞춤화할 수 있습니다. 이를 통해 LED 전구 제조업체는 보다 매력적인 제품 외관을 만들 수 있는 디자인 자유도를 높일 수 있습니다.
6. 품질 보증: 신뢰성 입증
LED 전구의 생산 공정에서 품질 보증 조치는 제품의 신뢰성과 안정적인 성능을 보장하는 핵심 연결고리입니다. 다음은 몇 가지 중요한 품질 보증 조치입니다:
- 비파괴 검사: X-레이 및 초음파 등의 비파괴 검사 기술을 사용하여 알루미늄 다이캐스팅 부품의 내부 결함을 감지하여 제품 내부에 기공, 균열 및 기타 문제가 없는지 확인합니다.
- 치수 정확도 관리: 첨단 측정 장비와 엄격한 검사 프로세스를 통해 알루미늄 다이캐스팅의 치수 정확도를 제어하여 각 부품이 설계 요구 사항을 충족하도록 보장합니다.
- 환경 적응성 테스트: LED 전구에 대해 고온, 저온, 습도-열 및 기타 환경 적응성 테스트를 수행하여 다양한 환경에서 제품의 작동 안정성과 신뢰성을 검증합니다.
7. LED 제조의 지속 가능성
환경 보호에 대한 인식이 높아지면서 LED 제조 업계도 지속 가능한 개발에 점점 더 많은 관심을 기울이고 있습니다. 알루미늄 다이캐스팅 공정은 이와 관련하여 적극적인 역할을 합니다:
- 자원 재활용: 알루미늄은 재활용성이 높은 소재입니다. 사용한 알루미늄 다이캐스팅 부품은 재활용 및 재사용이 가능하므로 1차 자원의 수요와 착취를 줄일 수 있습니다.
- 에너지 소비를 줄입니다: 생산 공정을 최적화하고 장비를 업그레이드함으로써 알루미늄 다이캐스팅 공정에서 에너지 소비를 줄이고 에너지 활용 효율을 개선할 수 있습니다.
- 폐기물 배출을 줄입니다: 생산 과정에서 고형 폐기물 배출을 줄이기 위해 엄격한 폐기물 관리 시스템을 구현하고, 폐기물을 합리적으로 분류 및 처리합니다.
- 환경 친화적인 소재 사용: 알루미늄 다이캐스팅 공정에서 환경 친화적인 코팅, 용제 및 기타 보조 재료를 사용하여 환경에 유해한 배출을 줄입니다.
알루미늄 다이캐스팅이 LED 전구의 성능을 어떻게 향상시킬까요?
LED 전구는 높은 에너지 효율과 긴 수명으로 인해 점점 더 인기를 얻고 있습니다. LED 전구의 전반적인 성능에 영향을 미치는 핵심 요소는 전구 제작에 사용되는 소재입니다. 특히 다이캐스트 알루미늄은 LED 전구 제조업체들 사이에서 가장 먼저 선택되는 소재입니다. 이 글에서는 다이캐스트 알루미늄을 사용하는 이유와 LED 전구의 성능을 향상시킬 수 있는 방법을 살펴봅니다.
1. 열 방출
LED 전구에 다이캐스트 알루미늄을 사용할 때의 주요 장점 중 하나는 뛰어난 방열 특성입니다. LED 전구는 작동 중에 열을 발생시킵니다. 열을 효과적으로 방출하지 못하면 성능이 저하되고 수명이 단축됩니다. 다이캐스트 알루미늄은 열전도율이 높아 LED 부품에서 발생하는 열을 효과적으로 전달할 수 있습니다. 따라서 LED가 차가운 상태를 유지하여 과열을 방지하고 최적의 성능을 유지할 수 있습니다.
2. 내구성 및 보호
다이캐스트 알루미늄은 정밀 LED 부품에 탁월한 내구성과 보호 기능을 제공합니다. 견고한 특성 덕분에 충격, 진동 및 외부 환경 요인에 대한 저항력이 뛰어납니다. 이는 열악한 환경에 노출될 수 있는 실외 또는 산업 환경에서 사용되는 LED 전구의 경우 특히 중요합니다. 다이캐스트 알루미늄 하우징은 보호막 역할을 하여 내부 구성품이 손상되지 않도록 보호하고 LED 전구의 수명을 연장합니다.
3. 가볍고 컴팩트한 디자인
다이캐스트 알루미늄은 가볍고 튼튼한 특성으로 잘 알려져 있어 LED 전구 제작에 이상적인 소재입니다. 무게가 가볍기 때문에 설치가 간편하고 조명 기구에 가해지는 스트레스를 줄여줍니다. 또한 다이캐스팅을 통한 컴팩트한 디자인 덕분에 매입형 조명, 트랙 조명, 장식용 조명 등 다양한 조명기구에 LED 전구를 설치할 수 있습니다. 이러한 다용도성 덕분에 LED 전구는 성능 저하 없이 다양한 환경에 원활하게 통합될 수 있습니다.
4. 내식성
LED 전구는 특히 실외나 습한 지역에서 습기 및 기타 부식성 요소에 노출될 수 있습니다. 다이캐스트 알루미늄은 부식에 매우 강하기 때문에 이러한 유형의 애플리케이션에 탁월한 선택입니다. 다이캐스트 알루미늄의 부식 방지 특성 덕분에 열악한 환경에서도 LED 전구를 보호하고 성능을 유지할 수 있습니다.
5. 설계 유연성
다이캐스팅 알루미늄은 복잡한 디자인이 가능하여 제조업체가 혁신적인 기능을 갖춘 LED 전구를 제작할 때 더 큰 유연성을 제공합니다. 다이캐스팅의 다용도성 덕분에 방열판과 광학 장치 등 다양한 부품을 전구 구조에 통합할 수 있습니다. 그 결과 배광이 개선되고 연색성이 향상되며 LED 전구의 전반적인 성능이 향상됩니다.
결론적으로
다이캐스트 알루미늄은 LED 전구의 성능을 향상시키는 데 중요한 역할을 합니다. 뛰어난 열 성능, 내구성, 경량 디자인, 내식성 및 디자인 유연성 덕분에 LED 전구 제작에 이상적인 소재입니다. 제조업체는 다이캐스트 알루미늄을 사용하여 최적의 성능과 LED 전구의 긴 수명을 보장하고 다양한 애플리케이션에 효율적인 조명 솔루션을 제공할 수 있습니다.
알루미늄 다이캐스팅을 다양한 유형의 LED 전구 디자인에 적용할 수 있나요?
예, 알루미늄 다이캐스팅은 다양한 유형의 LED 전구 디자인에 적용할 수 있습니다.
알루미늄 다이캐스팅은 알루미늄 금속을 원료로 사용하는 제조 공정입니다. 알루미늄을 녹여 다이캐스팅 기계를 통해 금형에 주입한 다음 냉각하여 필요한 모양으로 굳힙니다. 이 공정을 통해 다양하고 복잡한 모양과 구조를 만들 수 있어 다양한 유형의 LED 전구 디자인에 적용할 수 있습니다.
예를 들어 LED 전구의 쉘, 라디에이터, 브래킷 등은 알루미늄 다이캐스팅을 사용하여 제조할 수 있습니다. 합리적인 금형 설계 및 가공 기술을 통해 우수한 방열 성능, 고강도, 고정밀 및 아름다운 외관을 갖춘 LED 전구 케이스를 생산할 수 있습니다.
또한 알루미늄 다이캐스팅 공정은 사출 성형, 스프레이 등과 같은 다른 제조 공정과 결합하여 더욱 복잡하고 다양한 LED 전구 제품을 만들 수 있습니다.
요약하면, 알루미늄 다이캐스팅은 다양한 유형의 LED 전구 디자인에 적용하기에 적합한 제조 공정입니다.
LED 전구용 알루미늄 다이캐스팅에서 열 효율은 어떤 역할을 하나요?
열 효율은 LED 전구용 알루미늄 다이캐스팅에서 중요한 역할을 합니다.
첫째, 열 효율은 LED 전구의 성능과 수명에 직접적인 영향을 미칩니다. LED 칩은 작동할 때 열을 발생시킵니다. 열을 제대로 제어하지 않으면 LED 칩의 성능이 저하되거나 손상 될 수도 있습니다. 따라서 알루미늄 다이캐스팅의 열효율을 개선하면 LED 칩에서 발생하는 열을 효과적으로 발산하고 LED 전구의 안정성과 수명을 유지할 수 있습니다.
둘째, 열 효율은 LED 전구의 에너지 절약 효과에도 영향을 미칩니다. 알루미늄 다이캐스팅의 열효율이 낮으면 LED 전구는 작업시 더 많은 열을 발생시키고 작업을 유지하는 데 더 많은 에너지가 필요하므로 에너지 소비와 운영 비용이 증가합니다. 따라서 알루미늄 다이캐스팅 부품의 열효율을 개선하면 LED 전구의 에너지 소비를 줄이고 에너지 절약 효과를 향상시킬 수 있습니다.
요약하면 열 효율은 LED 전구 알루미늄 다이캐스팅에서 중요한 역할을하며 LED 전구의 성능, 수명 및 에너지 절약 효과에 직접적인 영향을 미칩니다. 따라서 LED 전구 알루미늄 다이캐스팅을 설계하고 제조 할 때 제품 성능을 개선하고 에너지 소비를 줄이기 위해 열효율 요소를 충분히 고려해야합니다.
알루미늄의 가벼운 특성이 LED 전구 제조에 도움이 될까요?
LED 전구 제조에 있어 소재 선택은 최종 제품의 성능, 효율성 및 전반적인 품질을 결정하는 데 중요한 역할을 합니다. 최근 몇 년 동안 많은 관심을 받고 있는 소재 중 하나는 알루미늄으로, 주로 가벼운 특성과 제조 과정에서 알루미늄이 제공하는 다양한 장점으로 인해 주목받고 있습니다. 이 글에서는 알루미늄의 가벼운 특성이 LED 전구 제조에 유리한 이유를 살펴봅니다.
1. 에너지 효율
LED 전구는 에너지 효율이 뛰어난 것으로 잘 알려져 있으며, 알루미늄의 가벼운 특성도 에너지 효율을 높이는 데 기여합니다. 알루미늄은 열을 더 잘 방출할 수 있는 가벼운 금속으로, 과열의 위험을 줄이고 LED 전구의 전반적인 에너지 효율을 높여줍니다. 알루미늄은 열을 효율적으로 방출함으로써 LED 칩의 수명을 연장하여 전구의 밝기와 성능을 더 오래 유지할 수 있도록 도와줍니다.
2. 설계 유연성
알루미늄의 가벼운 특성 덕분에 제조업체는 LED 전구 생산 시 디자인 유연성을 높일 수 있습니다. 알루미늄의 가단성 덕분에 복잡한 모양으로 쉽게 성형할 수 있어 혁신적이고 아름다운 LED 전구 디자인을 만들 수 있습니다. 이러한 유연성은 최적의 작동 온도를 유지하는 데 필수적인 방열판과 같은 추가 기능을 통합하는 데에도 적용됩니다.
3. 간편한 설치
알루미늄이 가볍다는 또 다른 장점은 설치가 쉽다는 점입니다. 알루미늄으로 만든 LED 전구는 다른 소재로 만든 전구보다 훨씬 가볍기 때문에 취급과 설치가 쉽습니다. 이러한 경량 기능은 상업용 또는 산업용 환경과 같이 많은 수의 LED 전구를 설치해야 하는 경우에 특히 유용합니다.
4. 내구성
알루미늄은 가벼운 무게에도 불구하고 내구성이 뛰어난 소재입니다. 알루미늄으로 제작된 LED 전구는 부식에 강해 열악한 환경에서도 수명을 보장합니다. 이러한 내구성은 습기, 먼지 또는 성능에 영향을 줄 수 있는 기타 요인에 노출될 수 있는 LED 전구에 매우 중요합니다. 제조업체는 알루미늄을 사용하여 가벼울 뿐만 아니라 강하고 내구성이 뛰어난 LED 전구를 만들 수 있습니다.
5. 환경 친화적
알루미늄은 재활용성이 뛰어나 LED 전구 제조에 친환경적인 소재로 잘 알려져 있습니다. 알루미늄은 가볍기 때문에 전반적인 재료 소비를 줄여 보다 지속 가능한 제조 공정을 구현할 수 있습니다. 또한 알루미늄은 고유의 특성을 잃지 않고 쉽게 재활용할 수 있어 LED 전구 생산과 관련된 환경 영향을 더욱 줄일 수 있습니다.
결론적으로
알루미늄의 가벼운 특성은 LED 전구 제조에 많은 이점을 제공합니다. 향상된 에너지 효율과 설계 유연성부터 설치 용이성, 내구성, 친환경성까지 알루미늄은 고품질 LED 전구를 생산하고자 하는 제조업체에게 탁월한 선택임이 입증되고 있습니다. 에너지 효율적인 조명 솔루션에 대한 수요가 계속 증가함에 따라 LED 전구 제조에 알루미늄의 경량 특성을 활용하는 것은 의심할 여지 없이 이러한 요구를 충족하는 데 중요한 역할을 할 것입니다.
알루미늄 다이캐스팅의 커스터마이징이 LED 전구 혁신에 어떻게 기여하나요?
과학과 기술의 급속한 발전으로 LED 전구는 현대 조명의 주류가 되었습니다. 이 분야에서 알루미늄 다이캐스팅 기술의 맞춤형 적용은 LED 전구 혁신의 새로운 세계를 열어가고 있습니다. 알루미늄 다이캐스팅은 LED 전구에 뛰어난 방열 성능과 경량 설계를 제공할 뿐만 아니라 고도로 맞춤화된 특성으로 LED 전구 설계의 다양성과 유연성을 촉진합니다.
1. 알루미늄 다이캐스팅 기술이 선사하는 디자인의 자유로움
알루미늄 다이캐스팅 기술을 통해 제조업체는 특정 요구 사항과 적용 시나리오에 따라 LED 전구의 모양, 크기 및 구조를 맞춤화할 수 있습니다. 복잡한 방열 구조든 독특한 외관이든 알루미늄 다이캐스팅은 고정밀 제조를 실현할 수 있습니다. 이를 통해 디자이너는 더 큰 창의적 공간을 확보하여 LED 전구의 디자인을 더욱 다채롭게 만들고 다양한 시장 수요를 충족할 수 있습니다.
2. 방열 성능을 최적화하고 LED 효율을 개선합니다.
LED 전구의 효율과 수명은 방열 성능에 따라 크게 영향을 받습니다. 알루미늄 다이캐스팅 기술은 방열 구조가 우수한 LED 전구 하우징을 생산할 수 있어 작동 중 LED 칩에서 발생하는 열을 빠르고 효과적으로 방출할 수 있습니다. 맞춤형 방열 설계를 통해 LED 전구의 열 효율을 더욱 향상시켜 수명을 연장하는 동시에 에너지 소비를 줄이고 더욱 에너지 절약적이고 친환경적인 조명 솔루션을 실현할 수 있습니다.
3. 가벼운 디자인, 간편한 설치 및 적용
알루미늄의 가벼운 특성 덕분에 LED 전구는 고성능을 유지하면서 가벼운 디자인을 구현할 수 있습니다. 이는 전구의 설치와 교체를 용이하게 할 뿐만 아니라 샹들리에나 벽 램프와 같이 매달거나 고정해야 하는 상황에서 LED 램프가 더욱 유리하게 작용합니다. 맞춤형 알루미늄 다이캐스팅 기술은 다양한 설치 요구 사항에 따라 정확하게 조정된 LED 전구 구조를 생산할 수 있어 설치 프로세스를 간소화하고 사용 편의성을 향상시킵니다.
4. 열악한 환경에 적응하고 내구성 향상
알루미늄은 내식성과 강도가 우수합니다. 알루미늄 다이캐스팅 기술로 제조된 LED 전구 하우징은 열악한 환경의 부식을 견디고 다양한 기후와 환경에서도 안정적인 작업 성능을 보장할 수 있습니다. 지역 및 환경 조건에 따라 맞춤형 디자인을 조정하여 특정 환경에 더 적합한 LED 전구 제품을 만들 수 있습니다.
5. 결론
알루미늄 다이캐스팅 기술의 맞춤형 적용은 LED 전구의 혁신에 강력한 추진력을 불어넣었습니다. 물리적 성능 측면에서 LED 전구의 품질과 수명을 향상시킬뿐만 아니라 디자인 측면에서 더 큰 유연성과 다양성을 제공합니다. 기술의 지속적인 발전과 시장 수요의 다양화에 따라 알루미늄 다이캐스팅 맞춤화의 잠재력이 더욱 탐구되어 LED 조명 산업이 더 나은 미래로 나아갈 수 있도록 도울 것입니다.
LED 전구 생산에 알루미늄을 사용하면 어떤 주요 이점이 있나요?
LED 전구 생산에 알루미늄을 사용할 때의 주요 이점은 다음과 같습니다:
- 방열 성능: 알루미늄은 열전도율이 뛰어나 열을 빠르게 전도할 수 있습니다. LED 전구는 작동할 때 열을 발생시킵니다. 열이 제때 방출되지 않으면 LED의 수명에 영향을 미칩니다. 알루미늄 케이스는 LED 칩의 작동 온도를 낮추고 LED의 수명을 연장하는 데 도움이 됩니다.
- 내식성: 알루미늄은 습기, 산화 및 화학적 공격에 매우 강합니다. 따라서 알루미늄 하우징은 혹독한 기후 조건을 장시간 견딜 수 있어 실외 환경에 이상적입니다.
- 환경 친화적: 알루미늄은 재활용 및 재사용이 용이한 재생 가능한 소재입니다. 따라서 LED 가로등의 알루미늄 하우징은 자원 낭비와 환경 영향을 줄이는 데 도움이 되며 지속 가능한 개발 원칙에 부합합니다.
- 외관과 내구성: 알루미늄 하우징은 아노다이징, 스프레이 코팅, 전기 코팅 등 다양한 표면 처리를 통해 다양한 외관과 색상을 구현하고 내구성을 높일 수 있습니다.
- 비용 효율성: 알루미늄은 상대적으로 경제적 인 소재이므로 LED 가로등의 알루미늄 하우징 제조 비용이 상대적으로 낮아 전체 비용을 제어하는 데 도움이됩니다.
- 경량: 알루미늄은 가벼운 소재이므로 알루미늄으로 만든 LED 전구는 상대적으로 가볍기 때문에 설치 및 운송 시 더 편리합니다.
요약하자면, 알루미늄을 LED 전구의 주요 소재로 사용하면 방열 성능, 내식성, 환경 보호, 아름다움과 내구성, 높은 가성비, 휴대성 등 여러 가지 장점이 있습니다.
알루미늄 다이캐스팅의 품질 보증은 어떻게 신뢰할 수 있는 LED 전구 성능을 보장합니까?
LED 조명 장비에서 알루미늄 다이캐스팅의 품질은 전구의 신뢰성과 성능에 중요한 역할을 합니다. 알루미늄 다이캐스트 쉘은 전구의 장식일 뿐만 아니라 방열, 기계적 강도, 내식성 및 기타 측면에서도 중요한 역할을 하여 LED 전구의 성능과 수명을 보장합니다.
1. 소재 품질
첫째, 알루미늄 다이캐스트 하우징의 소재 품질이 중요합니다. 순도가 낮거나 불순물이 포함된 알루미늄은 열전도율 및 기계적 강도와 같은 주요 특성이 저하될 수 있습니다. 따라서 고순도 알루미늄 또는 알루미늄 합금을 선택하는 것이 다이캐스팅 품질을 보장하기 위한 첫 번째 단계입니다.
2. 금형 설계
금형의 디자인은 알루미늄 다이캐스트 하우징의 모양과 정확도에 결정적인 영향을 미칩니다. 금형의 결함이나 오류는 최종 제품으로 직접 전달될 수 있습니다. 따라서 정확한 금형 설계는 다이캐스팅 품질을 보장하기 위한 두 번째 단계입니다.
3. 생산 공정 제어
생산 과정에서 용융 알루미늄 주입부터 냉각 및 탈형에 이르기까지 모든 단계는 정밀한 제어가 필요합니다. 예를 들어 용융 알루미늄의 주입 속도와 온도, 금형의 냉각 속도 등이 모두 제품의 품질에 영향을 미칩니다. 따라서 엄격한 공정 제어는 다이캐스팅 품질을 보장하기 위한 세 번째 단계입니다.
4. 제품 테스트
알루미늄 다이캐스트 하우징의 각 배치에는 외관, 크기, 기계적 특성, 열전도율 등을 포함한 엄격한 품질 검사가 필요합니다. 이러한 테스트를 통해 제품의 품질이 기대치와 표준을 충족하는지 확인할 수 있습니다. 이것이 다이캐스팅 품질을 보장하는 네 번째 단계입니다.
5. 환경적 요인
또한 보관 및 작업 환경도 알루미늄 다이캐스트 하우징의 품질에 영향을 미칩니다. 예를 들어 습한 환경에서는 알루미늄 케이스가 부식되고 녹이 슬어 열전도율과 외관에 영향을 미칠 수 있습니다. 따라서 적절한 보관 환경과 사용 조건을 유지하는 것이 다이캐스팅 품질을 보장하기 위한 다섯 번째 단계입니다.
요약하자면, 알루미늄 다이캐스팅의 품질 보증은 LED 전구의 안정적인 성능을 보장하는 핵심 링크입니다. 재료 선택, 금형 설계, 생산 공정 제어, 제품 테스트에 이르기까지 모든 링크에는 엄격한 제어와 관리가 필요합니다. 그래야만 LED 전구의 안정적인 성능을 보장하고 사용자에게 고품질의 제품과 서비스를 제공할 수 있습니다.
알루미늄 다이캐스트 부품을 LED 전구 제조에 재활용할 수 있나요?
LED 전구 제조 공정에서 알루미늄 다이캐스팅은 재활용할 수 있습니다.
알루미늄은 재활용이 가능한 소재이므로 알루미늄 다이캐스팅은 폐기 후 재활용, 재용해 새로운 알루미늄 제품이나 알루미늄 다이캐스팅으로 만들 수 있습니다. 이러한 재활용 및 재사용 방법은 자원 낭비를 줄일 뿐만 아니라 환경에 미치는 영향을 줄일 수 있으며 지속 가능한 발전의 원칙에 부합합니다.
LED 전구 제조 공정에서 알루미늄 다이캐스팅의 재활용을 실현하기 위해서는 몇 가지 조치를 취해야 합니다:
- 알루미늄 다이캐스팅은 사용 중에 손상되거나 오염되지 않도록 하여 재활용 시 우수한 물성을 유지할 수 있도록 해야 합니다.
- A complete recycling system needs to be established, including recycling sites, transportation and processing facilities, etc., to ensure that the recycling and processing process of aluminum die castings proceeds smoothly.
It should be noted that the recycling of aluminum die castings may be affected by some factors, such as the purity of the aluminum, impurity content, recycling process, etc. Therefore, during the recycling process, aluminum die castings need to be strictly inspected and processed to ensure that their quality and performance meet the requirements.
What sustainability initiatives are associated with Aluminum Die Casting for LED bulbs?
Sustainable Development Measures for Aluminum Die Castings for LED Bulbs
As the world pays increasing attention to sustainable development, the LED lighting industry is also actively seeking environmentally friendly and energy-saving solutions. Aluminum die-casting is an important material in the manufacturing of LED bulbs, and its sustainable development measures are of great significance in promoting the green development of the entire industry. This article will discuss sustainable development measures for aluminum die castings used in LED light bulbs.
1. Optimize design and improve material utilization
In the design stage of LED light bulbs, through optimized design, the use of aluminum die castings can be reduced and material utilization improved. For example, lightweight design is adopted to reduce unnecessary structural parts, thereby reducing the use of aluminum. At the same time, rationally plan the layout of parts to reduce waste in the mold manufacturing process, further reducing costs and resource consumption.
2. Use environmentally friendly materials
Choosing environmentally friendly aluminum materials and coatings is an important measure for the sustainable development of aluminum die castings for LED light bulbs. For example, recyclable aluminum alloy materials are used to reduce the burden on the environment. At the same time, low-volatile organic compound (VOC) coatings are used to reduce environmental pollution during the production process.
3. Promote circular economy
Circular economy is an important way to achieve sustainable development. In the manufacturing process of LED light bulbs, the recycling of aluminum die-casting parts should be promoted. By establishing a complete recycling system, we can recycle, classify, and reuse scrap aluminum die-casting parts to achieve effective utilization of resources and reduce dependence on natural resources.
4. Improve production efficiency
Improving production efficiency is an important means to reduce energy consumption and resource consumption. By introducing advanced production equipment and technology, optimizing the production process and improving production efficiency, energy consumption and raw material waste can be reduced and contribute to sustainable development.
5. Strengthen R&D and innovation
Innovation is an important driving force for sustainable development. In the field of aluminum die castings for LED bulbs, R&D innovation should be strengthened to develop more environmentally friendly and efficient manufacturing technologies and materials. Through technological breakthroughs, we can reduce energy and resource consumption in the manufacturing process and provide strong support for the sustainable development of the industry.
6. Strengthen policy guidance and supervision
The government should strengthen policy guidance and supervision of the LED lighting industry to promote the sustainable development of the industry. Formulate relevant policies and regulations to encourage companies to adopt environmentally friendly materials and manufacturing technologies, while increasing penalties for violations to ensure the green development of the industry.
In short, the sustainable development of aluminum die-casting parts for LED bulbs needs to start from multiple aspects such as design, materials, production, recycling, etc., through optimizing design, using environmentally friendly materials, promoting circular economy, improving production efficiency, strengthening R&D innovation, and strengthening policy guidance and regulatory measures to jointly promote the green development of the industry.
What emerging trends and innovations can be expected in Aluminum Die Casting for future LED bulbs?
In the future, aluminum die-casting technology for LED bulbs may have the following new trends and innovations:
- Lightweight design: As LED light bulbs increase in power and efficiency, aluminum die castings need to withstand higher thermal loads and mechanical stresses. Therefore,lightweight design will become an important trend in future aluminum die-casting technology. By optimizing materials and structures, the quality of aluminum die-casting parts can be reduced and their strength and durability improved.
- High-precision manufacturing: As the LED lighting market continues to expand and consumers have higher requirements for product quality, high-precision manufacturing will become an important development direction of aluminum die-casting technology. By introducing advanced manufacturing equipment and processes, the accuracy and consistency of aluminum die-casting parts can be improved to meet the needs of different application scenarios.
Intelligent manufacturing: With the rapid development of - Industry 4.0 and intelligent manufacturing, intelligent manufacturing will become an important innovation direction for aluminum die casting technology. By introducing advanced sensors, Internet of Things technology and big data analysis, we can achieve automated, flexible and intelligent manufacturing of aluminum die castings, improving production efficiency and product quality.
- Environmentally friendly materials: With the improvement of environmental awareness and the requirements of sustainable development, environmentally friendly materials will become an important innovation direction in aluminum die-casting technology. By introducing environmentally friendly materials such as recyclable aluminum alloy materials and low-VOC coatings, we can reduce the environmental impact of aluminum die castings and improve the environmental performance of products.
- Personalized customization: As consumers’ demand for personalization increases, personalization will become an important innovation direction in aluminum die-casting technology. By introducing advanced 3D printing technology and personalized customization platform, we can achieve rapid and personalized customization of aluminum die-casting parts to meet the personalized needs of consumers.
In short, in the future, the aluminum die-casting technology of LED bulbs will develop in the direction of lightweight, high precision, intelligence, environmental protection and personalization to meet market demand and promote the sustainable development of the industry.