Customized zinc alloy die casting processing, professional die casting manufacturer
Mindwell has more than ten years of zinc alloy die casting and customized production experience. after continuous learning and accumulation, the company set up a perfect team of engineers with advanced technology and experience. To provide customers with zinc alloy die casting mold design, mold, die casting products, precision machining, surface treatment of all processes, one-stop service
We provide customers with free zinc alloy mold design drawings, mold flow analysis, and a DFM report. Quick quotation, the fastest 10 days to open the mold sample, precision can be controlled to 0.01.
At Mindwell, we are committed to providing high-quality zinc alloy die-casting services to meet the different parts customization needs of various industries. Among them, we custom-designed zinc alloy parts for a well-known European electronic equipment manufacturer. At that time, they were faced with a challenging task: they needed a housing that was both lightweight and strong to ensure the safety of the electronic components inside their latest products. run. Customer requirements are unique and specific. Our engineers studied the 3D drawings of the parts and gained a deep understanding of the customer’s needs. After detailed communication with the customer, we started product design and engineering analysis. We had to find a solution that would provide both a lightweight design and strong protection in the face of accidental bumps and vibrations. Zinc alloys have an excellent strength-to-weight ratio that perfectly meets the requirements of the part.
We design and manufacture special zinc alloy die-casting molds specifically for customers to ensure product quality and precision. Mold development is a critical step in ensuring final product quality. After the mold was ready and the samples were sent to the customer, who was very satisfied, we started mass production of zinc alloy die-casting. State-of-the-art equipment and processes are used to ensure the specifications and consistency standards of each zinc alloy part. Our QC department follows Mindwell’s quality control process to ensure product reliability.
Finally, we successfully delivered the customized zinc alloy shell to the customer. They are very satisfied with the quality and performance of the product, as it is not only lightweight but also provides excellent performance. Customer satisfaction and trust are the ultimate goals of our work.
Advantages of zinc alloy die casting
Only by combining good zinc alloy raw materials with precision die-casting molds, die-casting machines, and surface treatment processes can high-quality, high-precision zinc alloy die-casting parts be made.
- Lightweight
- High dimensional accuracy, surface accuracy, and thin-walled casting accuracy
- Mass production
- Economical and affordable
- Convenient surface treatment
- High plasticity
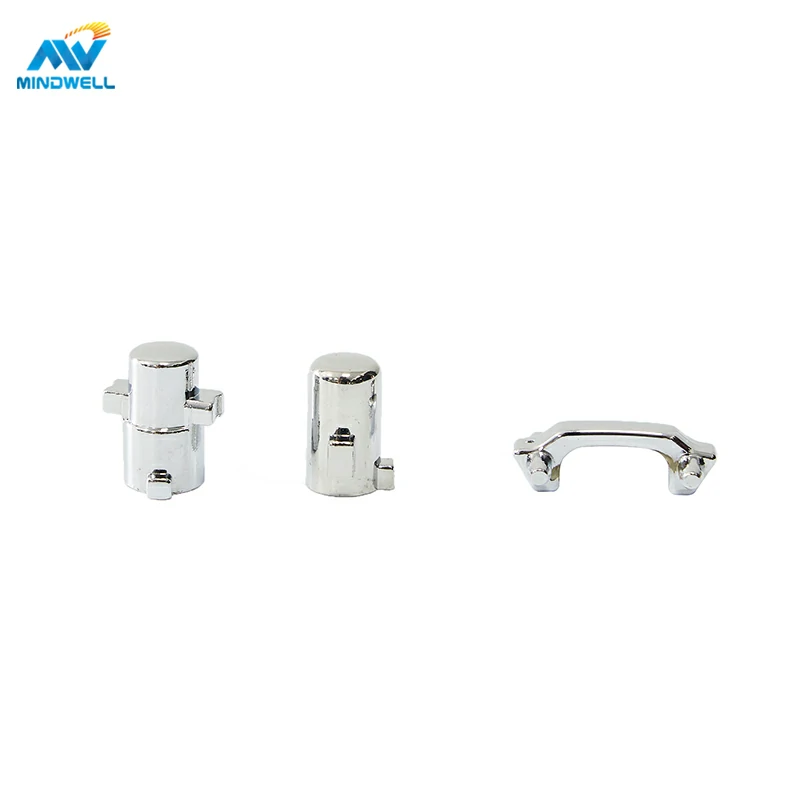
Zinc alloy die-cast process
The zinc die casting process is a common metal processing technique that involves injecting molten zinc into molds at high pressure. Once it cools and solidifies, the desired parts or products are formed. This method offers several advantages, including high efficiency, precision, and cost-effectiveness, making it widely used in industrial production.
One of the key features of the zinc die casting process is its efficiency. In comparison to traditional casting methods, zinc die casting allows for the rapid production of large quantities within a short timeframe, greatly enhancing manufacturing efficiency. Additionally, the process can be automated, reducing labor costs and associated risks.
This manufacturing method has become increasingly popular for its ability to create complex, high-quality metal components quickly and economically. Its versatility and accuracy make it an essential part of many industrial processes.
Get Started Now with Custom Zinc Alloy Die Casting According to Your Needs!
How to choose zinc alloy materials
Zinc alloys are widely used in die casting processes and are classified by numbers, including 2, 3, 4, 5, and 7. Among these, Zamak 3 is a popular choice.
- Zamak 3: Renowned for its excellent fluidity and mechanical properties, Zamak 3 is commonly selected for castings that do not require unusually high mechanical strength. Its applications range from toys and lighting fixtures to decorative items and specific electrical components.
- Zamak 5: Zamak 5 strikes a balance between good fluidity and strong mechanical properties, making it suitable for applications that require modest mechanical strength. This alloy is commonly used in automotive components, electromechanical parts, mechanical components, and electrical elements.
- Zamak 2: Reserved for applications with special requirements for mechanical properties, high hardness, good wear resistance, and standard dimensional accuracy of mechanical components.
- ZA8: Despite its excellent impact strength and dimensional stability, ZA8 has lower fluidity. It is favored for die-casting small components that necessitate high precision and mechanical strength, especially in the field of electrical equipment.
- Superloy: Known for its extraordinary fluidity, Superloy is the ideal choice for die-casting thin-walled, large-sized, highly precise, and complex-shaped components, including electrical elements and their housings.
Each zinc alloy provides distinct physical and mechanical properties, allowing for a wide range of options when designing die-cast components.
Choose Mindwell company for custom processing of zinc alloy
- 15 years of focus on zinc alloy die casting customization, one-stop solution from product mold design to product shipping.
- All customers have one-on-one exclusive sales and direct email service from mold designers, and it only takes 10 days to open the mold.
- Establish a project discussion group to communicate quickly, shorten mold opening time, and help customers reduce production costs.
- With polishing, spraying, grinding and other surface treatment departments and drilling machines, CNC equipment, etc., shipments are 2-5 days faster than peers
- Mindwell implements 5S quality management, production inspection, final inspection, quality control plan incoming material inspection, and production part approval process.

ENGINEER’S ANSWER
Zinc Alloy Die Casting FAQs
Share the issues you want to know about zinc alloy die casting.
Zinc is utilized in die castings for the following reasons:
- Because of its exceptional flexibility and fluidity, zinc alloy may be utilized to die-cast a variety of intricately formed goods.
- Zinc alloy material may be used in place of several non-renewable metals and is a recyclable metal that complies with the nation’s sustainable development strategy.
- Zinc alloy is highly hard, has a modest specific gravity, and is an excellent heat conductor.
Die-cast zinc alloy will not rust. Zinc alloy does not rust because there is a passivation film on its surface, which can prevent air oxidation and protect zinc alloy die castings from corrosion. However, zinc alloy die-casting parts will become moldy and black in a humid environment. This is a normal phenomenon and does not constitute rust.
The disadvantages of zinc alloy die casting are as follows:
- Zinc alloy die-casting parts will become moldy and black in a humid environment. This is normal and does not constitute rust.
- Zinc alloy die castings cannot be heat treated and strengthened, nor can they be welded, and are prone to cracking and large deformation.
- Zinc alloy die castings are more expensive than aluminum alloys and are not suitable for mass production.
Zinc alloy and die-cast zinc are not the same. Die-cast zinc is an alloy of zinc and other elements used to make metal. This alloy is easy to weld, braze, and plastically process, and it has a low melting temperature and good fluidity. It resists corrosion in the environment and is simple to recycle and remelt the waste materials. An alloy that has additional elements added to zinc is called a zinc alloy. This alloy may be used to die-cast zinc alloy goods with a variety of complicated geometries because of its high fluidity and flexibility.s.
The strength of zinc alloy is different from that of steel. Zinc alloys are lower in strength than steel. The hardness of zinc alloys ranges from 65-140, while the hardness of iron depends on its alloy content, but is usually between 260-440. Therefore, the hardness of zinc alloys is significantly lower than iron, and the hardness difference with steel is even greater.
Zinc alloy is better than pure zinc. Because zinc alloy is a material formed by mixing zinc with other metals, the properties of the zinc alloy can be adjusted by controlling the ratio of zinc to other metals. Alloy zinc is more stable than pure zinc and is more suitable for use in various high temperature, high pressure, and corrosive environments. The corrosion resistance, electrical conductivity, and even strength of alloy zinc are also superior to pure zinc.
Zinc alloys turn green. When a zinc alloy is oxidized on the surface, an oxide layer will appear. The thickness and composition of the different oxide layers will cause the zinc alloy to show different colors, ranging from colorless and gray to yellow, blue, green, and other colors. The reason why the zinc alloy turns green may be that the slow oxidation reaction of the zinc alloy with water, oxygen, and other substances produces basic copper carbonate, also called patina, which is the green substance.
Zinc alloy will not rot. Zinc alloy is a metal material mixed with zinc and other metal elements. Because of its good corrosion resistance and low smelting cost, it is often used to form mechanical parts, ships, bridges, aircraft, containers, and other components. The surface of these objects is easily affected by the weather, so they will rust but will not completely rot.