In order to prolong the service life of the machine and make the product more ornamental, people use surface treatment techniques to achieve this effect, so what is surface treatment? Surface treatment is to form a surface layer with one or more special properties on the surface of materials by physical or chemical methods. Surface treatment can improve product appearance, texture, function and other aspects of performance.
what is surface treatment
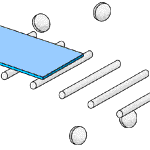
Surface treatment is carried out during the manufacturing process and is a mechanical process. The process of changing the condition and properties of the surface of parts to achieve predetermined performance requirements is called surface treatment. For example, the physical and chemical properties of parts can be improved by applying "plating" or "spraying" to the surface of the material. Through the surface treatment process, the wear resistance, lubricity, strength, impact resistance, electrical conductivity, thermal conductivity, corrosion resistance, chemical resistance, heat resistance and adhesion of the parts can be improved, as well as the decorative performance can be improved.
surface treatment process
Sandblasting
Sand blasting is a process of cleaning and roughening the surface of the substrate by using the impact of high-speed sand flow, that is, using compressed air as the power to form a high-speed jet beam to spray materials (copper ore, quartz sand, corundum, iron sand, Hainan sand) at high speed To the surface of the workpiece that needs to be treated, the appearance or shape of the outer surface of the workpiece surface is changed.
Due to the impact and cutting effect of the abrasive on the surface of the workpiece, the surface of the workpiece can obtain a certain degree of cleanliness and different roughness, and the mechanical properties of the surface of the workpiece are improved, thus improving the fatigue resistance.
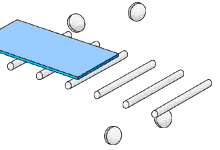
Technical Features:
- Realize different reflective or matte.
- It can clean the tiny burrs on the surface of the workpiece and make the surface of the workpiece more smooth, eliminating the harm of burrs and improving the grade of the workpiece.
- Clear the residual dirt left in the pre-treatment, improve the smoothness of the workpiece, and make the workpiece reveal a uniform and consistent metal color, making the appearance of the workpiece more beautiful and attractive.
In the surface treatment of the fixture, the size change after sandblasting is a normal phenomenon. According to the surface sandblasting according to the process, the size does not become larger, but because the spray material is sprayed on the surface of the workpiece to be treated at a high speed, the roughness of the surface of the workpiece is intensified. Creates an uneven surface.
Anodizing
Electrochemical oxidation of metals or alloys. Aluminum and its alloys form an oxide film on the aluminum product (anode) under the corresponding electrolyte and specific process conditions under the action of an applied current.

Process flow:
Single color, gradient color: polishing/sandblasting/drawing→degreasing→anodizing→neutralization→dyeing→sealing→drying
Two-color:
①Polishing/sandblasting/drawing→degreasing→masking→anodizing 1→anodizing 2→sealing→drying
②Polishing/sandblasting/drawing→oil removal→anodizing 1→radium engraving→anodizing 2→sealing→drying
Technical Features:
- Increase strength
- Realize any color except white
- Realize nickel-free sealing and meet the nickel-free requirements of Europe, the United States and other countries
Technical difficulties and key points for improvement: The yield level of anodic oxidation is related to the cost of the final product. The key to improving the oxidation yield is the appropriate amount of oxidant, appropriate temperature and current density, which requires structural parts manufacturers to continuously explore during the production process , to seek a breakthrough.
Phosphating treatment
The phosphating process is a process in which chemical and electrochemical reactions form a phosphate chemical conversion film, and the formed phosphate conversion film is called a phosphating film. Phosphating can prevent metals from being corroded to a certain extent, and it is used for anti-friction lubrication in metal cold working process.
The phosphating film will not adhere to the molten metal, so it is usually used to protect the alloy casting of the non-cast part when the friction of cylinders, bushings and other parts is reduced. The difference between phosphating and blackening is as follows:
Plating treatment
The process of attaching a layer of metal film to the surface of metal or other material parts by electrolysis, so as to prevent metal oxidation (such as rust), improve wear resistance, conductivity, reflectiveness, and corrosion resistance (copper sulfate, etc.) and enhance aesthetics.
Electroplating has the forms of copper plating, nickel plating, gold plating, titanium plating, etc. Titanium plating is generally used to improve the wear resistance of the surface of objects. For example, taps and drill bits used in high-speed machining centers can be plated with titanium to improve the wear resistance of tools. There is also titanium plating on the surface of the piston ring, which is also to improve wear resistance. The fixture can be used in the processing of positioning pads and positioning pins.
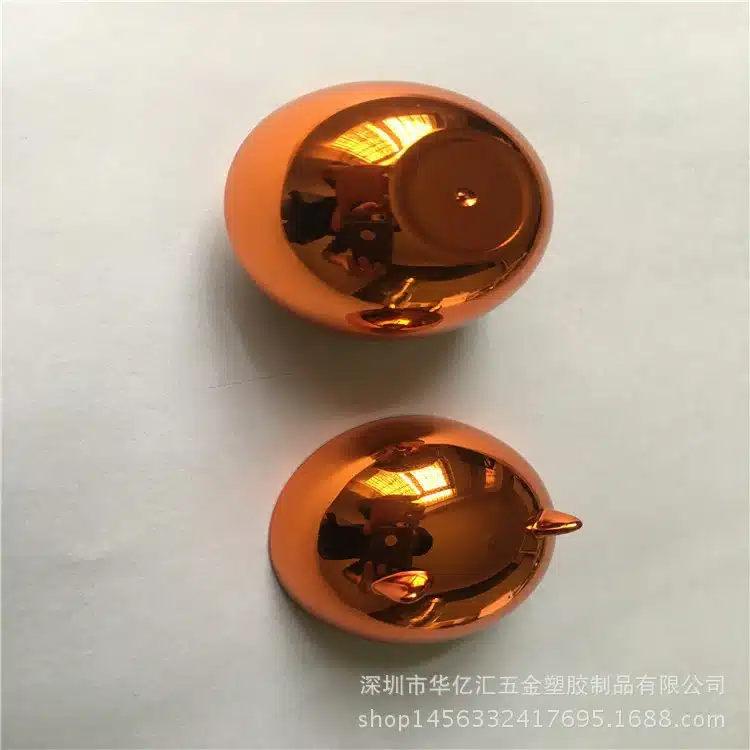
Process flow: pretreatment → cyanide-free alkali copper → cyanide-free cupronickel tin → chrome plating
advantage:
- The coating has high gloss and high-quality metal appearance;
- The base material is SUS, Al, Zn, Mg, etc.; the cost is lower than PVD.
Disadvantages: poor environmental protection, high risk of environmental pollution.
Electrophoresis treatment
Used in stainless steel, aluminum alloy, etc., can make the product present various colors, and maintain the metallic luster, while enhancing the surface performance, with good anti-corrosion performance. Products that require high corrosion resistance, such as auto parts, generally have a thickness of more than 20µm; ordinary metal processing generally have a paint film thickness of about 15µm. Some products with stamping deformation requirements, such as guide rails, often only require 10µm.
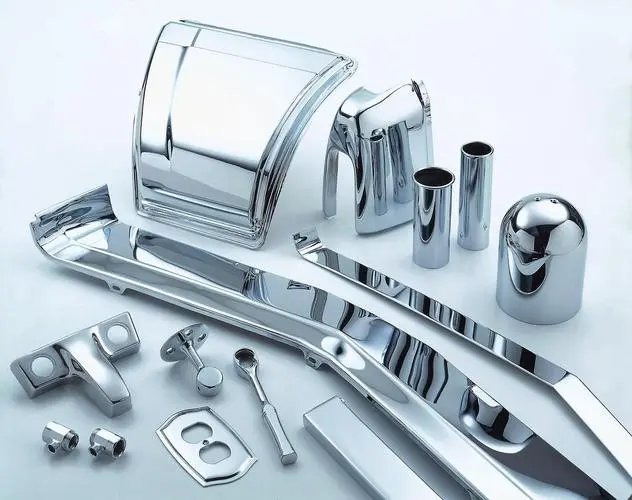
Process flow: pretreatment→electrophoresis→drying
advantage:
- Rich colors;
- No metal texture, can be used with sandblasting, polishing, wire drawing, etc.;
- Processing in a liquid environment can realize surface treatment of complex structures;
- The technology is mature and can be mass-produced.
Disadvantages: The ability to cover up defects is average, and the electrophoresis of die-casting parts requires high pre-treatment.
The essential difference from electroplating: electroplating is accompanied by electrochemical reaction, metal ions are reduced to metal through electrochemical reaction at the cathode, and then crystallized on the treated surface to form an electroplating film layer, while electrophoresis is not accompanied by electrochemical reaction.
Micro-arc oxidation
Micro-arc oxidation, also known as micro-plasma oxidation, is a combination of electrolyte and corresponding electrical parameters, on the surface of aluminum, magnesium, titanium and their alloys, relying on the instantaneous high temperature and high pressure generated by arc discharge, to grow matrix metal oxides. ceramic membrane layer.
Process flow: pretreatment → hot water washing → MAO → drying
advantage:
- Ceramic texture, dull appearance, no high-gloss products, delicate hand feeling, anti-fingerprint;
- Wide range of substrates: Al, Ti, Zn, Zr, Mg, Nb, and their alloys;
- The pre-treatment is simple, the product has excellent corrosion resistance, weather resistance, and good heat dissipation performance.
Disadvantages: At present, the colors are limited, only black and gray are relatively mature, and bright colors are currently difficult to achieve; the cost is mainly affected by high power consumption, which is one of the highest costs in surface treatment.
Metal wire drawing
Metal wire drawing is a surface treatment method that forms lines on the surface of the workpiece by grinding products to achieve a decorative effect.
Technical features: The brushed treatment can make the metal surface obtain a non-mirror-like metallic luster, and the brushed treatment can also eliminate the slight flaws on the metal surface.
shot peening
Shot peening is a cold working process that bombards the surface of the workpiece with pellets and implants residual compressive stress to improve the fatigue strength of the workpiece.
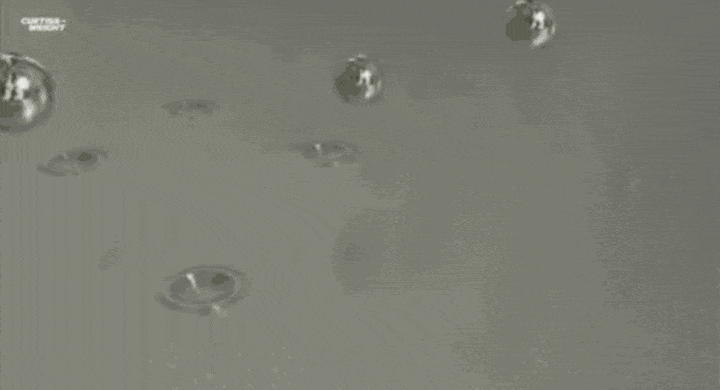
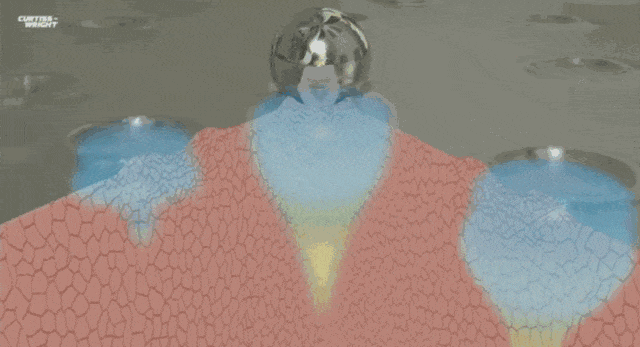
etching
Etching is the technique of removing material using chemical reaction or physical impact. Usually refers to etching, also known as photochemical etching, which refers to removing the protective film of the area to be etched after exposure plate making and development, and contacting chemical solution during etching to achieve the effect of dissolution and corrosion, forming the effect of concave-convex or hollow molding.
Process flow:
Exposure method: The project prepares the material size according to the graphics-material preparation-material cleaning-drying→film or coating→drying→exposure→development→drying-etching→release→OK
Screen printing method: cutting → cleaning plate (stainless steel and other metal materials) → screen printing → etching → stripping → OK
advantage:
- Can carry out micro-processing of metal surface;
- Give the metal surface a special effect;
Disadvantages: Most of the corrosive liquids (acid, alkali, etc.) used in etching are harmful to the environment.
IMD
IMD is In-Mold Decoration (in-mold decoration technology), also known as coating-free technology. It is a popular surface decoration technology. The surface is hardened and transparent film, the middle printing pattern layer, the back injection molding layer, and the middle of the ink can make the product resistant to friction. Prevents the surface from being scratched, and keeps the color bright and not easy to fade for a long time.
Laser carving
Laser engraving, also called laser engraving or laser marking, is a process of surface treatment using optical principles. Use laser beams to carve permanent marks on the surface of a material or inside a transparent material.
laser bite
Laser embossing uses a high-energy-density laser to react with the surface of the steel to form snake skin/etch/pear ground or other forms of texture.
The above are the 11 commonly used surface treatment methods listed above. If you want to know more surface treatment methods, or if you have customized needs for surface treatment, you can contact us directly. We will give you professional advice and quick quotation.