Introduction
In the complex world of manufacturing, die-cast aluminum parts are among the most widely used, combining strength, precision, and versatility. This article delves into the intricate details of die-cast aluminum parts, exploring their manufacturing processes, applications across industries, and the undeniable advantages they bring to modern production.
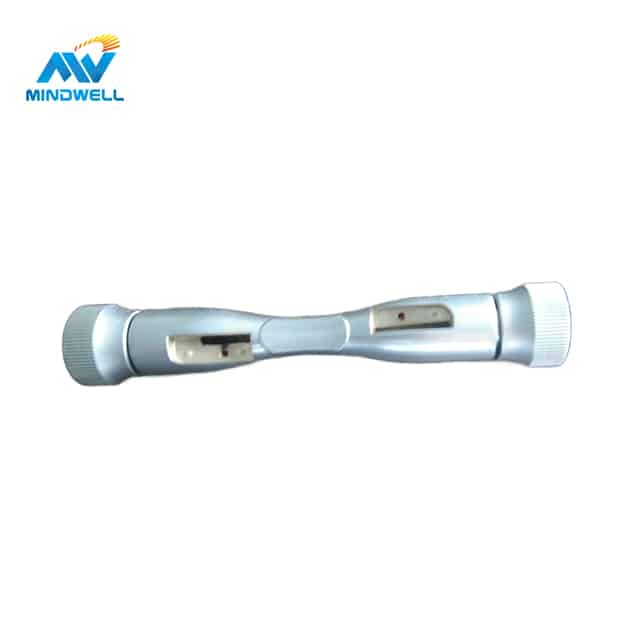
1.Create miracles
Die-cast aluminum parts production
The artistry behind die-cast aluminum parts involves a careful production process. From material selection to advanced molding techniques, every step helps create parts of unmatched quality.
- The selection of materials is key. Aluminum is a lightweight, high-strength metal with good electrical conductivity and corrosion resistance. During the die-casting process, selecting high-quality aluminum alloys can ensure the mechanical properties and durability of the parts. At the same time, appropriate aluminum alloys can also provide good casting properties, including fluidity, shrinkage, and air tightness.
- Mold design and manufacture. Mold is a key tool for forming die-cast aluminum parts. Its quality and design have a decisive impact on the shape, size and surface quality of the part. During the mold manufacturing process, factors such as the geometry, dimensional accuracy, surface finish, and draft of the part need to be taken into consideration. At the same time, in order to ensure production efficiency and reduce costs, mold design also needs to consider the replacement and repair of wearing parts.
- During the die-casting process, the molten aluminum alloy is injected into the mold under high pressure, and then cooled and demoulded to obtain die-cast aluminum parts. In this process, the control of pressure, temperature and time is vital. Too much pressure may cause damage to the mold, while too little pressure may cause defects such as blow holes in the part. At the same time, the control of temperature and time also directly affects the cooling rate, shrinkage rate and internal stress distribution of the part.
- Finally, the subsequent processing of die-cast aluminum parts is also critical. This includes steps such as deburring, polishing, and spray painting. These treatments can not only improve the appearance quality of the parts, but also enhance their corrosion resistance and wear resistance.
In short, the production process of die-cast aluminum parts is a detailed and complex process, and every link has an important impact on the quality of the parts. By selecting the right materials, designing and manufacturing high-quality molds, precisely controlling the die-casting process and post-processing, we can create die-cast aluminum parts of unparalleled quality.
State of the art CAD
Advanced computer-aided design (CAD) technology plays a crucial role in ensuring the precision of the molding process. This technology plays a key role in transforming complex designs into tangible, high-quality aluminum parts by utilizing specialized software for product design, simulation and analysis.
First, CAD technology can carry out prototyping and simulation during the design stage to test the feasibility and performance of the design. By testing designs in a computer environment, possible manufacturing issues can be predicted and resolved, such as mold flow, pore formation, and part assembly fit. This predictive design greatly improves production efficiency and reduces production costs, while also ensuring product accuracy and quality.
Second, CAD technology can precisely control the mold manufacturing process. Using the precise data of the CAD model, molds with finer details and more accurate dimensions can be manufactured. At the same time, CAD technology can also conduct stress analysis on the mold to prevent potential problems such as cracks during the die-casting process. This precise mold making process ensures part dimensional accuracy and shape accuracy, allowing the aluminum parts produced to meet strict quality requirements.
In addition, CAD technology can also perform simulation and optimization during the die-casting process. By simulating the die casting process in a computer environment, die casting parameters such as metal flow, mold cooling rate, and pressure distribution can be accurately predicted and optimized. This simulation optimization maximizes production efficiency while maintaining part quality and performance.
Finally, CAD technology can also be used for monitoring and optimizing the production process. Using sensors and monitoring equipment, data from the production process can be obtained in real time and compared and analyzed with CAD models. This kind of monitoring can promptly detect and solve potential problems, and at the same time, the design can be adjusted and optimized based on actual production conditions to meet market demand.
In conclusion, advanced computer-aided design (CAD) technology plays a key role in ensuring the precision of the molding process. By performing prototyping and simulation during the design phase, precisely controlling the mold manufacturing process, simulating and optimizing the die-casting process, and monitoring and optimizing the production process, CAD technology enables complex aluminum component designs to be realized and produced with high quality and precision. Aluminum parts. The application of this technology not only improves production efficiency and reduces production costs, but also brings more possibilities for the production of aluminum components.
Temperature and Pressure Control
In the die-casting process, precise temperature and pressure control are of extremely important importance. They are not only crucial to ensure the structural integrity of the part, but also play a decisive role in improving the strength and surface finish of the part.
- Temperature control. During the aluminum alloy die-casting process, appropriate temperature control can ensure the fluidity of molten aluminum and reduce the occurrence of internal defects in the casting. Dihui Die Casting relies on advanced temperature control equipment to control and monitor the casting temperature in real time. Typically, the melting temperature of aluminum alloy is 650℃-710℃, while the temperature of the mold is usually between 150℃-250℃. In actual operation, the mold and furnace temperatures can be precisely controlled to ensure that the temperature of each casting meets the standard requirements.
- Pressure control is also a critical factor in the die casting process. Appropriate pressure can ensure that the metal fully fills every detail of the mold and avoids problems such as pores and defects. By precisely adjusting the pressure, the consistency and integrity of the parts can be achieved, and the accuracy and stability of the molding can be improved. During the die-casting process, the size and action time of pressure have a significant impact on the quality and performance of the casting.
- Through precise temperature and pressure control, the structural integrity of the castings is ensured. This means each casting will have the intended shape, size and internal details. In addition, these controls improve the strength of the casting. Since the metal flows more evenly under high pressure and internal defects are reduced, the overall strength of the casting will be improved.
- Finally, precise temperature and pressure control can also improve the surface finish of your castings. During the die-casting process, appropriate temperature and pressure conditions help reduce the roughness of the mold surface, making the casting surface smoother. In addition, by controlling the flow rate and filling pattern of metal, surface defects such as pores and cold shut-offs can be reduced, further improving the surface quality of the casting.
To sum up, accurate temperature and pressure control play an extremely important role in the die casting process. Not only do they ensure the structural integrity and strength of the casting, but they also improve the surface finish of the casting. High-quality aluminum alloy castings can be produced by using advanced temperature control equipment and precise pressure regulation.

2.Cross-industry Application
Driving automotive innovation
In the automotive sector, die-cast aluminum parts play a vital role in driving lightweight design, fuel efficiency and structural integrity in modern vehicles.
- Let’s think about lightweight design. Modern automakers are working to reduce the weight of their vehicles through the use of lightweight materials and optimized designs to improve fuel efficiency and performance. Die-cast aluminum parts are a key factor in achieving this goal due to their high strength and light weight. For example, the use of aluminum hoods, fenders, doors, door frames and other components significantly reduces the vehicle’s weight while maintaining the required strength and stiffness. In addition, the lightweight design also provides the car with better controllability and response speed, improving the driving experience.
- Die-cast aluminum parts also play a major role in improving fuel efficiency. Because aluminum is less dense, using aluminum parts can reduce the overall weight of the vehicle, thereby reducing the burden on the engine and improving fuel efficiency. One study showed that for every 100 kilograms of vehicle weight reduced, fuel consumption can be reduced by about 7%. Therefore, die-cast aluminum parts are of great importance in promoting green environmental protection.
- Die-cast aluminum parts are also critical to maintaining and improving the structural integrity of your vehicle. Aluminum is a high-strength, high-rigidity material that can resist external impact and corrosion. In automobile structures, die-cast aluminum parts such as chassis components, engine components, braking system components, etc. can enhance the structural strength and durability of the car body. In addition, due to the high thermal conductivity of aluminum, components such as aluminum radiators help to quickly conduct heat to the vehicle surface, improve heat dissipation efficiency, and ensure the stable operation of the engine and braking system.
Die-cast aluminum parts play an increasingly important role in the automotive industry. Not only do they help enable lightweight designs and improve fuel efficiency, but they also enhance the structural integrity of the car. At the same time, the manufacturing process of aluminum die castings is relatively environmentally friendly and complies with the requirements of sustainable development. With the advancement of technology and the increasing demand for environmental protection, the application prospects of die-cast aluminum parts in the future automotive industry will be broader.
Illuminating possibilities in the electronics world
In the electronics world, die-cast aluminum components have a broad and far-reaching impact on efficient heat dissipation applications. Whether it is smartphones, tablets, laptops, or various industrial electronic products, die-cast aluminum components play a key role.
First, let’s start with the smartphone. The performance and stability of a smartphone depend largely on the design of its internal electronic components and cooling system. Die-cast aluminum components play a vital role in this. Aluminum’s high thermal conductivity and lightweight properties make it an ideal material for mobile phone cooling systems. Precision-designed die-cast aluminum parts, such as radiators, casings, etc., can effectively conduct heat from inside the phone to the outside, ensuring the stability and reliability of the phone during high-load operation.
In addition to smartphones, die-cast aluminum components are also equally important in heat dissipation applications in other electronic products such as tablets and laptops. The internal structures of these devices are more complex, and efficient cooling systems are critical to maintaining high performance and stability. Die-cast aluminum components can meet the needs of lightweight, high strength and efficient heat dissipation of these devices, and therefore are widely used in the design of these devices.
Additionally, die-cast aluminum components are increasingly used in industrial electronic equipment. Industrial electronic equipment generally has higher power and more complex circuit designs, so the requirements for cooling systems are also more stringent. Die-cast aluminum parts provide high strength, high thermal conductivity and lightweight solutions, allowing these devices to maintain stable performance in harsh operating environments.
Overall, die-cast aluminum components play a key role in efficient cooling of electronic devices. From smartphones to industrial electronics, die-cast aluminum components have a wide range of applications and far-reaching impacts. As electronic technology continues to advance and heat dissipation requirements continue to increase, die-cast aluminum components will continue to play an important role in the design and manufacturing of future electronic devices.
3. Advantages and Innovation
Strength to weight ratio
The excellent strength-to-weight ratio of die-cast aluminum parts is due to some of the unique physical and mechanical properties of the aluminum itself, as well as the advantages of the die-casting process. This property makes die-cast aluminum components the first choice for many industries that require lightweight yet strong components.
- Aluminum is a light metal with a relatively low density. This allows the aluminum parts to be relatively light in weight yet retain adequate strength. Aluminum’s strength to weight ratio is superior to that of many other metals, such as steel and copper. This means that for the same weight, aluminum offers greater strength, allowing aluminum parts to perform exceptionally well when withstanding loads and stresses.
- The die casting process plays a key role in achieving a high strength to weight ratio. Die casting is a high-pressure molding process that applies high pressure in a mold to inject molten aluminum alloy into the mold cavity and form the part after cooling. Due to the high pressure and rapid cooling during die casting, aluminum alloys are able to form a dense microstructure that increases the strength and hardness of the part. Additionally, the die-casting process enables the design of complex shapes and thin-walled structures, further reducing component weight while maintaining the required strength and stiffness.
- The composition and heat treatment process of the aluminum alloy also have a significant impact on the strength-to-weight ratio. By adding alloying elements and carrying out appropriate heat treatment, the mechanical properties and microstructure of aluminum alloys can be adjusted to further improve their strength and hardness. This enables die-cast aluminum components to perform exceptionally well in a variety of application conditions.
- Combined with the above factors, the strength-to-weight ratio of die-cast aluminum components makes them the preferred choice for many industries. In the aerospace sector, for example, weight reduction is critical to improving fuel efficiency and flight performance. Die-cast aluminum components play an important role in the manufacture of structural parts and casings in spacecraft such as aircraft, satellites and rockets. In the automotive industry, die-cast aluminum components are used to make vehicle bodies, engine parts, and suspension systems to reduce vehicle weight and improve fuel efficiency. In addition, die-cast aluminum components are also widely used in areas such as electronics, power tools, and sporting goods.
The excellent strength-to-weight ratio of die-cast aluminum components is the result of a combination of the lightweight properties of aluminum, the advantages of the die-casting process, and the control of the alloy composition and heat treatment process. This characteristic makes die-cast aluminum parts the first choice for critical industries that require lightweight yet strong components.
Unleash complex designs
Die casting is an advanced manufacturing process capable of producing aluminum parts with complex geometries, thin-walled structures and high quality. Here are just a few of the ways die-casting technology offers design freedom and meets modern, evolving design requirements:
- Complex geometries: Die casting technology can produce aluminum parts with complex geometries, such as parts with fine features, projections and grooves. This degree of design freedom allows designers to innovate in the structure and appearance of parts and realize more complex design concepts.
- Thin-wall structure: Die-casting technology can realize the design of thin-wall structure, and the wall thickness of parts can be very thin, reaching the millimeter level. This thin-walled design can significantly reduce the weight of the part while maintaining adequate strength and stiffness. This degree of design freedom is very important for modern products, especially for applications such as automotive, electronics and aerospace that require lightweighting and energy conservation.
- High-quality surface: Die-casting technology can produce high-quality aluminum parts with smooth, flat surfaces and no obvious flaws and defects. This high-quality surface enhances the look and feel of your product, while also improving its longevity and reliability.
- Good Mechanical Properties: Die-cast aluminum parts have mechanical properties such as high strength, high hardness and good wear resistance. These properties can meet the requirements for high strength, lightweight and durability of modern products.
- Diverse material selection: Die-casting technology can use different types of aluminum alloys as raw materials. These aluminum alloys have different mechanical properties and chemical compositions and can be selected according to design requirements. This diversity of material options allows designers to use suitable aluminum alloy materials in different application areas.
In summary, the design freedom and ability to meet modern and evolving design requirements that die-casting technology offers make it an important manufacturing process in modern manufacturing. By leveraging die-casting technology, designers can innovate and design more freely to achieve more complex, lightweight and high-quality product designs.
time and cost efficient
In the competitive landscape of the manufacturing industry, time is indeed money. Production cycles for die-cast aluminum parts surpass traditional methods, providing companies with a competitive advantage and faster time to market. Let’s delve deeper into this issue:
- Optimization of production cycle: Die-casting technology has efficient production capacity and can complete the production of a large number of parts in a short time. The die-casting process allows more products to be manufactured in less time than traditional machining or forging processes. This optimization of the production cycle saves valuable manufacturing time for companies and speeds up product launch.
- Reduce manufacturing links: Die-casting technology can achieve integrated manufacturing, that is, the entire manufacturing process from raw materials to final parts can be completed in one device. This kind of integrated manufacturing reduces links and transportation time in the production process, reducing the manufacturing cycle.
- Rapid prototyping: Die-casting technology allows rapid production of prototype parts, allowing designers and engineers to test and validate products at an early stage. This rapid prototyping capability greatly shortens the product development cycle and accelerates the speed of products to market.
- Customized production: Die-casting technology can realize customized production, producing parts of different specifications and shapes according to customer needs. This customized production capability provides companies with more market opportunities, meets the special needs of customers, and further improves the speed of products to market.
- Efficient supply chain management: Die-casting technology can make supply chains more efficient and flexible. Because die-cast aluminum parts are consistent and standardized, companies can more easily conduct inventory management and logistics distribution, reducing supply chain management costs.
Taken together, the production cycle of die-cast aluminum parts exceeds traditional methods, providing companies with a competitive advantage and faster time to market. By optimizing production cycles, reducing manufacturing links, rapid prototyping, customized production and efficient supply chain management, die-casting technology brings higher production efficiency and faster response speed to companies, meeting the needs of modern manufacturing.
4.FAQ
Are die-cast aluminum parts suitable for high-stress applications?
Yes, die-cast aluminum parts perform well in high-stress applications due to their superior strength-to-weight ratio and structural integrity.
Can these components be recycled?
Absolutely. Die-cast aluminum parts are highly recyclable, contributing to sustainable and eco-friendly manufacturing practices.
How does temperature and pressure control affect the quality of die castings?
Precise temperature and pressure control ensures thorough mold filling, minimizing defects and improving part structural integrity and surface finish.
Which industries benefit most from die-cast aluminum parts?
The aerospace, automotive, electronics, and renewable energy industries are major beneficiaries, leveraging the versatility and strength of these parts.
What finishing options are available for die cast aluminum parts?
Common surface treatment options include anodizing and powder coating, which not only provide aesthetics but also provide additional protection against corrosion.
How do die-cast aluminum parts contribute to sustainability?
Their recyclability, light weight and energy efficiency of production contribute to the overall sustainability of die-cast aluminum parts.
Conclusion: Shaping the Future
In conclusion, die-cast aluminum parts are the backbone of modern manufacturing innovation. Its diverse applications and unrivaled advantages make it a cornerstone of various industries. As technology advances, so does the influence of die-cast aluminum parts, shaping the future of manufacturing with strength, precision and sustainability.