The metal casting process is vital to the manufacture of metal components used in various industries. The process involves pouring molten metal into a mold to create the shape of the desired part. The molten metal cools and solidifies in the mold, forming the desired part shape. There are different types of metal casting processes, each with its own unique advantages and disadvantages.
Sand casting
Sand casting is one of the most popular types of metal casting processes in manufacturing. The process involves making molds from a mixture of sand, clay, and water. The model is pressed into the sand and molten metal is poured into the cavity. After the metal solidifies, the sand mold is broken to reveal the finished product. This method is cost-effective and suitable for the production of medium to large components.

Advantages of sand casting:
- Wide range of application: Sand casting is suitable for various metals, including iron, steel, aluminum, copper, magnesium, etc.
- Low manufacturing cost: Compared with other casting methods, the cost of equipment and tools for sand casting is low.
- High flexibility: sand casting can produce castings of various shapes and sizes, suitable for the production of small to large pieces.
- Prototyping: Sand casting is a common method for making prototypes, and samples can be quickly produced by making wooden molds.
Sand casting disadvantages:
- Low dimensional accuracy: The dimensional accuracy of sand casting is relatively low, making it difficult to achieve high precision and tight tolerance requirements. Sand casting molds and sand molds may be subject to certain shrinkage and deformation, resulting in uncertainty in the size of the casting.
- Low production efficiency: The production cycle of sand casting is relatively long, because the process of preparing sand molds and sand molds is cumbersome. In addition, sand casting is usually suitable for small batch or single piece production, and it is not efficient for mass production.
- Sand core limitations: Sand cores are often required in parts that require internal cavities or pipes. However, core preparation and positioning can be difficult and there may be limitations to more complex internal structures.
Sand casting is widely used in the automotive, aerospace, machinery manufacturing, agricultural equipment and other fields to manufacture large parts, complex shaped components and small batch production.
Investment casting
Investment casting, also known as lost wax casting, is a process that involves making a wax pattern of a component. The wax pattern is then encapsulated in a ceramic shell. When the shell is baked, the wax melts and molten metal is poured into the cavity. After the metal solidifies, the ceramic shell cracks to reveal the finished product. This method is ideal for producing complex and detailed components.

Advantages of Investment Casting:
- High precision and complexity: Ability to produce metal parts of high precision and complex shapes, including internal structures, thin walls and details, etc.
- Excellent surface quality: Investment casting can provide smooth, fine-grained surfaces, reducing the need for subsequent machining and surface preparation.
- Wide range of materials: suitable for a variety of metals and alloys, including steel, stainless steel, copper, aluminum, nickel alloys, etc.
- Dimensional Consistency: Capable of highly consistent size and shape replication to meet stringent engineering requirements.
Investment Casting Disadvantages:
- Long manufacturing cycle: The manufacturing cycle of investment casting is relatively long. Involving multiple steps such as wax pattern preparation, coating, baking, investment, cooling and mold breaking, it takes patience and time to complete the whole process.
- Investment loss: Wax patterns in investment casting are melted and lost, so new wax patterns need to be made for each production run. This increases production cost and cycle time, especially for high-volume production.
- Design Limitations: Investment casting imposes certain limitations on certain design features and shapes. Complex internal structures, fine details or thin-walled parts may be constrained and require additional process adjustments and optimizations.
Investment casting is widely used in aerospace, automotive, medical devices, industrial equipment and other fields to manufacture complex components, precision parts, artwork and jewelry.
Die casting
Die casting is the process of injecting molten metal into a mold cavity under high pressure. The mold is made from two hardened steel dies designed to create complex shapes with high precision. The process is suitable for high-volume production of small and medium-sized components with excellent dimensional accuracy and surface finish.

Advantages of die casting include:
- High precision and complexity: Ability to manufacture parts with high precision, complex shapes and details.
- Rapid production: The production cycle is relatively short, suitable for mass production.
- Excellent surface quality: Die casting can provide smooth and delicate surface quality, reducing the need for subsequent processing.
- High Strength and Durability: Die cast parts typically have excellent mechanical properties and durability.
- Diversity of materials: It can be used to cast a variety of non-ferrous metal alloys, such as aluminum alloys, zinc alloys, magnesium alloys, etc.
Disadvantages of die casting:
- Complexity limitations: While die casting can produce parts with complex shapes and details, for some special geometries and internal structures, the design and manufacture of molds may be limited. Certain shapes may require additional mold parts or special handling.
- Surface defects: Due to high pressure injection and rapid cooling, die casting castings may be prone to some surface defects such as blow holes, shrinkage holes, cold shuts, etc. These defects may require additional machining or handling steps to repair or hide.
- Challenges of Design Changes: Once a die casting mold is fabricated, design changes and revisions to the mold are difficult and expensive.
Die casting is widely used in automotive, aerospace, electronics, home appliances, etc. to produce various metal parts such as engine parts, gears, electronic housings, connectors, etc.
Permanent mold casting
Permanent mold casting involves casting a part using a reusable mold, usually made of metal. The process is suitable for producing complex shapes with high dimensional accuracy and smooth surface finish. The metal is poured into the mold, and when it solidifies, the part pops out of the mold.
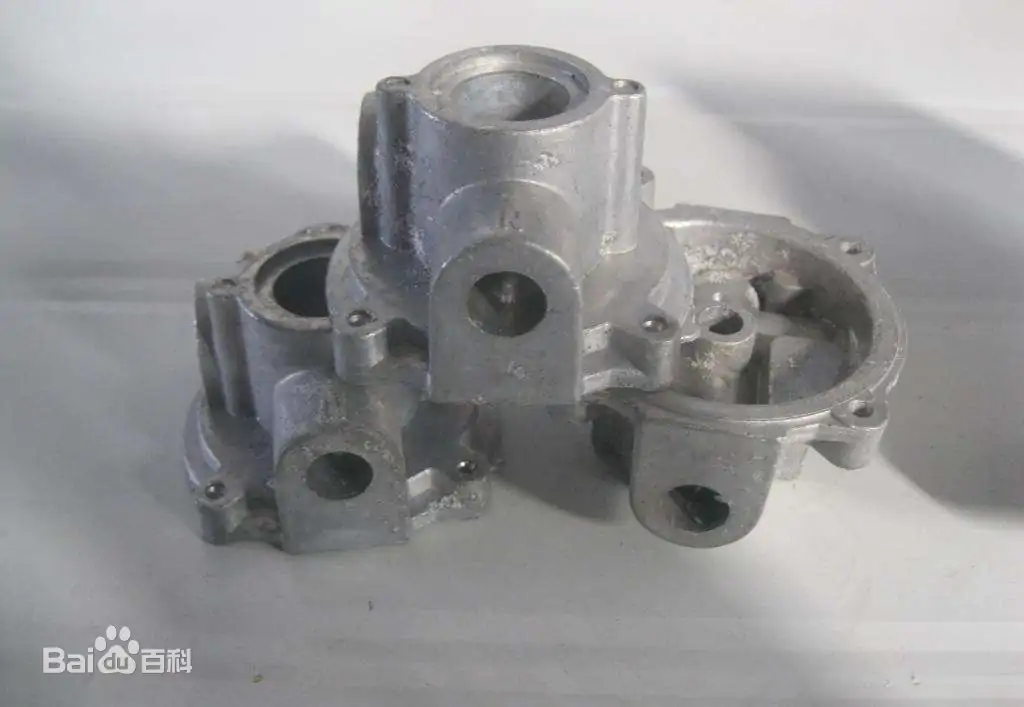
Advantages of permanent mold casting:
- High production efficiency: Compared with sand casting, permanent mold casting has a faster production speed and is suitable for mass production.
- Higher surface quality: Permanent mold casting can provide better surface finish and precision, reducing the need for subsequent processing.
- Excellent dimensional consistency: The stability and reusability of the mold can ensure the dimensional consistency of the casting.
- High Density and Strength: Castings cast from permanent molds generally have high density and strength.
- Diversity of materials: permanent mold casting is suitable for a variety of metal alloys, including aluminum alloys, copper alloys, zinc alloys, etc.
Disadvantages of permanent mold casting:
- High initial cost: Permanent mold casting has a high initial cost compared to some other casting methods.
- Restricted shapes and designs: Due to the limitations of the permanent mold, the casting process may have limitations for certain shapes and designs.
- Limited production speed: Compared to high-pressure casting methods such as die casting, permanent mold casting has a slow production speed.
Permanent mold casting is widely used in the automotive, aerospace, electronics, home appliances and other industries to produce various metal parts such as auto parts, motor housings, pipe joints, etc.
In conclusion, the metal casting process is necessary for the production of various metal components used in different industries. Each process has its own unique advantages and disadvantages, and choosing the right method depends on the complexity of the part, required precision, surface finish and throughput. By choosing the right process for your application, you can ensure the best possible results. Whether you need parts for machinery, automotive, or any other industry, Metal Casting is sure to meet your needs.