The die-casting process is divided into cold chamber die-casting and hot chamber die-casting according to different die-casting machine process modes and suitable materials. Cold chamber die casting is a kind of die casting process, which is mainly suitable for high melting point metal materials such as aluminum alloy and copper alloy.
Cold Chamber Die Casting Process
Sequence of Operations in the Cold Chamber Die Casting Process The mold is closed and the molten metal is scooped into the cold chamber sleeve. The plunger pushes the molten metal into the cavity, where it maintains pressure until it solidifies. The mold opens and the plunger advances to ensure that the casting remains in the ejected mold. The core, if any, is retracted. The ejection pin pushes the casting out of the ejection half of the mold and the plunger returns to its original position.
In cold chamber die casting, the aluminum alloy enters cooling tubes and then flows to the nozzle of the die casting machine. Through high pressure, the molten metal is hydraulically injected into the mold, which is rapidly cooled and solidified to form the desired metal part. The advantage of cold chamber die casting is that parts with more complex structures can be produced, and the material is stronger, with higher strength and wear resistance. In addition, due to the existence of the cooling system, the temperature at which the aluminum alloy contacts the mold during the flow process is reduced, which greatly reduces the wear and failure of the die casting machine equipment.
Metal materials suitable for cold chamber die casting process
- aluminum alloy
- copper alloy
- magnesium alloy
- Zinc alloy
- brass
These alloys yield high-quality castings in the cold chamber die casting process, which provides precise control and uniform cooling, helping to ensure end product performance and quality. Selecting the right material depends on the specific application needs and performance requirements.
Cold Chamber Die Casting Mold
Main features of cold chamber die casting molds:
- High-temperature-resistant materials: Since the cold chamber die-casting process needs to deal with high-temperature metal alloys, the molds are made of high-temperature resistant materials to ensure the stability and life of the molds. Materials commonly used include alloy steel, heat-resistant steel and special ceramics.
- Precision Machining: The manufacture of molds involves high-precision machining to ensure the precision and quality of the final casting. The inner surface of the mold is usually precision ground and polished to have a smooth surface and reduce casting surface defects.
- Complex structures: Cold chamber die casting is used to manufacture castings with complex shapes and structures, so the molds are designed and manufactured to meet these complex requirements. Molds may include multi-chamber designs to make multiple castings in one go.
- Wear resistance: The mold has good wear resistance, because the inside of the mold needs to withstand the impact of metal liquid under high pressure and high temperature to prolong the service life of the mold. This is usually achieved through surface coating or selection of wear-resistant materials.
- Cooling system: In order to ensure uniform cooling of castings, molds are usually equipped with cooling systems, including water channels or air channels, to control temperature distribution during casting. This helps to reduce thermal stress and shrinkage differences in castings.
- Easy to disassemble and replace: The mold may be worn or damaged after long time use, the cold chamber die casting mold can be easily disassembled and replaced parts of the mold. This helps in reducing downtime in production.
- Automation Compatibility: Cold chamber die casting is often used with automated production lines, so the molds are automation compatible to integrate with robots or automated systems for efficient production.
The design and manufacture of cold chamber die casting molds is a complex process that requires consideration of multiple factors to ensure high quality castings. The quality and performance of molds directly affect the quality and production efficiency of final products.
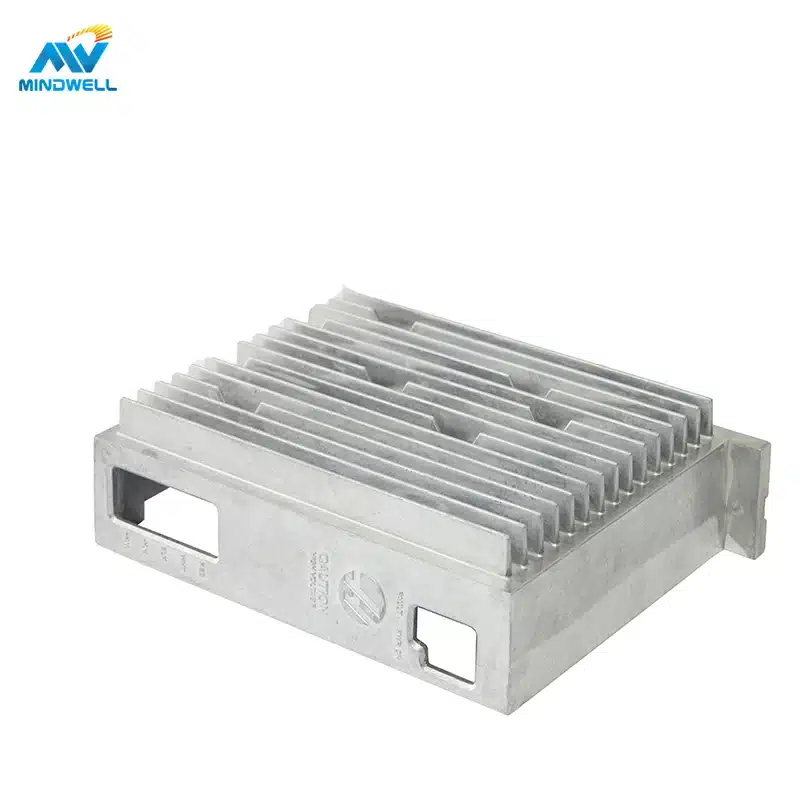
Cold chamber die casting advantages and disadvantages
Advantage:
- Stable and accurate casting: During the casting process, the cold chamber die-casting machine ensures the uniform cooling of the castings, thus ensuring the physical properties of the castings and reducing the generation of bubbles and defects. Adopting advanced die-casting technology, the product has high precision and meets the high-precision production requirements.
- Compact structure: The cold chamber die-casting machine has a compact structure, occupies a small amount of space, and is convenient for layout and adjustment of the production line. Its design is user-friendly, easy to operate, and improves production efficiency.
- Saving of materials and energy: the cold chamber die-casting machine can complete the casting process in a short time, which reduces the waste of materials and energy, and reduces the production cost.
Disadvantages:
- Heat loss of the metal liquid: During the injection process, the metal liquid is easy to lose heat, and the contact with the air may cause oxidation and inclusions.
- Special process requirements: for products that require high density or heat treatment, special processes are required.

Cold chamber die casting applications
- Manufacturing of auto parts: Cold chamber die casting machines are widely used to manufacture auto parts of various sizes, shapes and complexities, including engine cylinder heads, crankcases, transmission frames, etc.
- Manufacturing of electronic product shells: cold chamber die-casting machines are suitable for forming metal alloys such as aluminum, copper, and magnesium, and are especially suitable for the manufacturing of various electronic product shells, such as mobile phones, tablet computers, TVs, computers, etc.
- Shell manufacturing of home appliances: Cold chamber die-casting machines are also widely used in the field of home appliances, including washing machines, air conditioners, refrigerators, microwave ovens, gas stoves, etc.
Cold Chamber Die Casting Equipment
The choice of vertical cold chamber die-casting machine and horizontal cold chamber die-casting machine depends on the actual production needs, and the following factors are mainly considered:
- Casting size and weight, and yield requirements.
- Difficulty of installation, commissioning and processing of die-casting molds.
- The position and size of the parting surface of the die casting in the die casting mold.
- The clamping force of the die-casting machine can meet the requirements of die-casting parts.
- The relative position of pressure chamber diameter and pouring system overflow port.
- The injection pressure in the injection chamber and the fluidity of the molten metal after injection filling.
- The location of the sprue on the parting surface facilitates the removal of the casting from the die-casting mold.
How to choose the vertical cold chamber die casting machine and the horizontal cold chamber die casting machine?
For example, aluminum alloy products require high precision, and you can choose a horizontal cold chamber die-casting machine. Advantages of Horizontal Cold Chamber Die Casting Machine:
- The structure of the pressure chamber is relatively simple, with few faults, easy maintenance, and easy automation.
- The flow of molten metal is short, the loss of pressure and heat is small, and the casting is compact.
- There are many types of alloys that can be die-casted, and the adaptability is strong, especially the die-casting aluminum alloys are widely used.
The difference between cold chamber die casting and hot chamber die casting
The difference between cold chamber die casting and hot chamber die casting is as follows:
- Applicable alloys are different: cold chamber die casting is suitable for high melting point metals, which generally have stronger strength and wear resistance, and are suitable for producing large or complex metal components. The hot chamber die casting is suitable for low melting point and special metals, capable of producing high-quality and high-precision parts, suitable for the production of small and fine metal products.
- Different temperature range: The temperature range of hot chamber die casting is different from cold chamber die casting. The highest temperature for alloys that can be safely die cast in a hot chamber machine is around 450°C, including alloys such as zinc, magnesium, and lead. Cold room equipment processes high-temperature non-ferrous alloys, usually metal alloys with a temperature of 600°C or above, including aluminum, copper, brass and other alloys.
- The location of the furnace is different: the hot chamber equipment has a built-in furnace to melt the metal, so the metal is directly sent to the mold cavity through the gooseneck. In cold-chamber die-casting installations, the melting furnace is located outside and the molten metal must be fed into the machine using automatically or manually operated ladles.
In Mindwell, we have the ability of cold chamber die casting and hot chamber die casting. We can provide different customized die casting services according to different needs of customers. Our company has advanced die casting equipment and constantly updated die casting technology. We are proficient in a variety of die casting Craftsmanship skills, and the experience we’ve gained from our 15 years in town, please contact us if you have cold chamber die casting needs.