Of these four alloys, titanium alloy is the hardest and the strongest. In terms of hardness, titanium alloys are far harder than the other three alloys. In terms of tensile strength, titanium alloys are stronger than zinc alloys, followed by magnesium alloys, and aluminum alloys are the weakest.
Comparison of Strength and Hardness
However, in terms of product structure design, weight also needs to be considered. If the specific gravity is considered in terms of progress, zinc alloy has the smallest specific strength because of its highest density. Titanium alloys and magnesium alloys have high specific strength, but titanium alloys are expensive and have poor processability. Therefore, magnesium alloys are mostly used in structural parts that take weight and strength into account.
Magnesium and magnesium alloy
Magnesium has low density and is easy to burn due to its physical and chemical properties. At 20°C, the density of metallic magnesium is 1.738g/cm3, and the density of liquid metallic magnesium is 1.58g/cm3; under standard atmospheric pressure, the melting point of metallic magnesium is (650±1)°C, and the boiling point is 1090°C. When heated in air, metallic magnesium begins to burn at 632°C to 635°C. Therefore, it is determined that the preparation and alloy smelting process of magnesium are relatively complicated. The purity of magnesium for industrial use can reach 99.9%, but pure magnesium cannot be used as a structural material. Magnesium alloys formed by adding elements such as aluminum, zinc, lithium, manganese, zirconium and rare earth to pure magnesium have high strength. Currently, the most used Magnesium-aluminum alloys are the most widely used, followed by magnesium-manganese alloys and magnesium-zinc-zirconium alloys. Mainly used in aviation, aerospace, transportation, chemical industry, rocket and other industrial sectors.
Characteristics of magnesium alloy
- ① light weight
The specific gravity of magnesium is only 1.8G/CM3, and the specific gravity of aluminum alloy is 2.7G/CM3. Magnesium alloy is 30% lighter than aluminum alloy, and 80% lighter than steel. Therefore, magnesium alloys in automobiles and portable electronic products have become ideal materials for parts.
- ②Strength
Magnesium alloys have an excellent strength/weight ratio among engineering materials such as metals and plastics. The yield strength is 160MPa and the tensile strength is 240MPa.
- ③Die casting
Under the condition of maintaining a good structure, the magnesium alloy allows the wall thickness of the casting to reach a minimum of 0.6mm, which is impossible for plastics with the same strength. The die-casting performance of aluminum alloys can only be compared with magnesium alloys when they are above 1.2-1.5 mm. Magnesium alloys are easier to die-cast and are suitable for mass die-casting production (production speed can be 1.5 times that of aluminum). In addition, the wear of magnesium alloy die is lower than that of aluminum. The main reason is the high viscosity of aluminum.
- ④Shock absorption
Magnesium has excellent hysteresis shock absorption performance, can absorb vibration and noise, and can be used as equipment casing to reduce noise transmission, prevent shock and prevent dent damage. It is good as a backplane for LCD or LED.
- ⑤ Rigidity
Magnesium is twice as rigid as aluminum and more rigid than most plastics. Magnesium has good stress resistance.
- ⑥ High electromagnetic interference barrier
Magnesium alloy has a good function of blocking electromagnetic waves and is suitable for the production of electronic products.
- ⑦Good cutting performance
Magnesium has better machinability than aluminum and zinc, making magnesium an easier machining metal.
- ⑧The specific heat capacity of magnesium alloy is small, and the cooling speed of the alloy liquid is fast.
- ⑨The affinity between magnesium alloy and mold steel is low, so it is not easy to adhere to the mold.
Advantages of magnesium alloy materials
① light weight
The specific gravity of magnesium alloy is the lightest among all structural alloys. Its specific gravity is 68% of aluminum alloy, 27% of zinc alloy, and 23% of steel. In addition to being used as the shell and internal structural parts of 3C products, it is also used in automobiles. , aircraft and other parts of the excellent material.
②High specific strength and specific stiffness
The specific strength of magnesium alloy is significantly higher than that of aluminum alloy and steel, and its specific stiffness is equivalent to that of aluminum alloy and steel, but far higher than that of engineering plastics, which is 10 times that of general plastics.
③Good vibration resistance
Under the same load, the vibration damping performance is 100 times that of aluminum, and 300-500 times that of titanium alloy.
④Excellent electromagnetic shielding
The shell of 3C products (mobile phones and computers) should be able to provide superior anti-electromagnetic protection, and the magnesium alloy shell can completely absorb electromagnetic interference with a frequency exceeding 100db.
⑤ Good heat dissipation
The thermal conductivity of general metals is hundreds of times that of plastics. The thermal conductivity of magnesium alloys is slightly lower than that of aluminum alloys and copper alloys, and much higher than that of titanium alloys. The specific heat is close to that of water, which is the highest among commonly used alloys.
⑥ good texture
Magnesium alloy has an excellent appearance and touch texture, which makes the product more luxurious.
⑦ Good recyclability
As long as the cost is equivalent to 4% of the new material price, magnesium alloy products and waste can be recycled.
⑧Stable resource provision
The reserve of magnesium element in the earth’s crust ranks eighth, and most of the magnesium raw material is extracted from seawater, so its resource is stable and sufficient.
Advantages of magnesium alloy die casting
- High productivity
- ②High precision
- ③Good surface quality
- fine casting grain
- Products with thin walls and complex structures can be die-casted
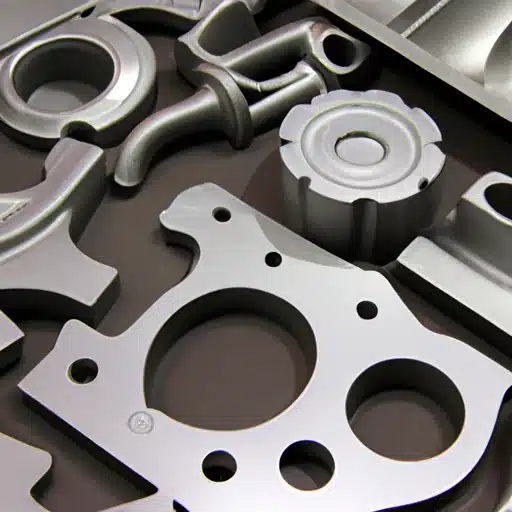
aluminum alloy
The general term for alloys based on aluminum. The main alloying elements are copper, silicon, magnesium, zinc, manganese, and the secondary alloying elements are nickel, iron, titanium, chromium, lithium and so on.
Aluminum alloy has low density, but high specific strength, which is close to or surpasses high-quality steel. It has good plasticity and can be processed into various profiles. It has excellent electrical conductivity, thermal conductivity and corrosion resistance. It is widely used in industry, and its usage is second only to steel. .
Aluminum alloy classification
Aluminum alloys are divided into two categories: cast aluminum alloys, which are used in the as-cast state; deformed aluminum alloys, which can withstand pressure processing, and have higher mechanical properties than the as-cast state. It can be processed into various shapes and specifications of aluminum alloy materials. It is mainly used in the manufacture of aviation equipment, daily necessities, doors and windows for buildings, etc.
Aluminum alloy processing method
According to the processing method, aluminum alloy can be divided into deformed aluminum alloy and cast aluminum alloy. Deformed aluminum alloys are further divided into non-heat-treatable and strengthenable aluminum alloys and heat-treatable and strengthenable aluminum alloys. The non-heat-treatable type cannot improve the mechanical properties by heat treatment, but can only be strengthened by cold deformation. It mainly includes high-purity aluminum, industrial high-purity aluminum, industrial pure aluminum and anti-rust aluminum. Heat-treatable and strengthened aluminum alloys can improve mechanical properties through heat treatment such as quenching and aging. It can be divided into hard aluminum, forged aluminum, super hard aluminum and special aluminum alloys.
Aluminum alloys can be heat treated to obtain good mechanical, physical and corrosion resistance properties.
Cast aluminum alloys can be classified into aluminum-silicon alloys, aluminum-copper alloys, aluminum-magnesium alloys and aluminum-zinc alloys according to their chemical composition.
Comparison of aluminum alloy and magnesium alloy
ADC-12 (ADC-12 has high silicon content, good fluidity and easy die-casting
There is not much difference between aluminum alloy and magnesium alloy, but aluminum alloy is slightly heavier. Processability is relatively sticky. Moreover, since the die-casting aluminum alloy contains a relatively high content of Si, it directly reacts with the chemical solution when performing Anodizing (anodizing). so as to fail. Magnesium alloy is acceptable, and the color is brighter, and Anodizing can be used for post-production appearance technology. However, not everyone can do it.
Zinc alloy
Zinc alloy characteristics
The grade of zinc-based alloy material usually used for electroplating is ZnAl 4-1, composition (%): Al 3.5~4.9, Cu 0.75~1.25, Mg 0.03~0.08, the balance is Zn.
①The proportion is large
② Good casting performance, can die-cast precision parts with complex shapes and thin walls, and the casting surface is smooth
③ Surface treatment available: electroplating, spraying, painting
④ No iron absorption during melting and die-casting, no corrosion of the pressing type, no sticking to the mold
⑤Good mechanical properties and wear resistance at room temperature
⑥ Low melting point, melting at 385°C, easy to die-cast
Problems to be noticed during use
① Poor corrosion resistance.
When the impurity elements lead, cadmium, and tin in the alloy composition exceed the standard, the casting will be aged and deformed, manifested as volume expansion, mechanical properties, especially plasticity, will decrease significantly, and even rupture after a long time. The solubility of lead, tin and cadmium in zinc alloy is very small, so they concentrate on the grain boundary and become the cathode, and the aluminum-rich solid solution becomes the anode, which promotes intergranular electrochemical corrosion under the condition of water vapor (electrolyte). Die castings age due to intergranular corrosion.
② aging effect
The structure of zinc alloy is mainly composed of zinc-rich solid solution containing Al and Cu and Al-rich solid solution containing Zn, and their solubility decreases with decreasing temperature. However, due to the extremely fast solidification rate of die castings, the solubility of the solid solution is greatly saturated at room temperature. After a certain period of time, this supersaturation phenomenon will be gradually relieved, and the shape and size of the casting will change slightly.
③Zinc alloy die castings should not be used in high temperature and low temperature (below 0°C) working environment. Zinc alloys have good mechanical properties at room temperature. But the tensile strength at high temperature and the impact performance at low temperature are significantly decreased.
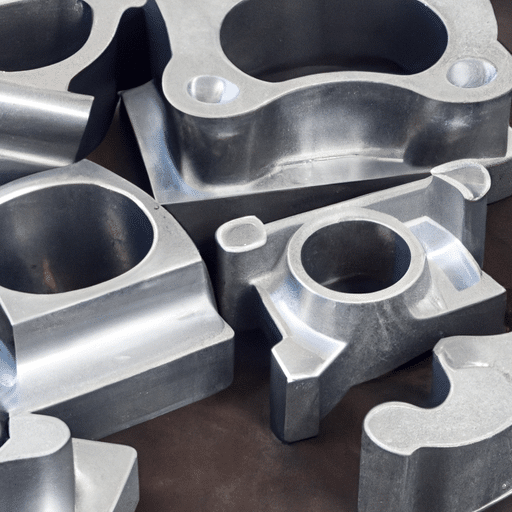
Titanium alloy
Titanium alloy is an alloy composed of titanium as the base and adding other elements. Titanium has two kinds of allotropic crystals: below 882°C is close-packed hexagonal structure α titanium, above 882°C is body-centered cubic β titanium.
Alloying elements can be divided into three categories according to their influence on the phase transition temperature:
① The elements that stabilize the α phase and increase the phase transition temperature are α stable elements, including aluminum, carbon, oxygen, and nitrogen. Among them, aluminum is the main alloying element of titanium alloy, which has obvious effects on improving the strength of the alloy at room temperature and high temperature, reducing the specific gravity, and increasing the elastic modulus.
②The elements that stabilize the β-phase and lower the phase transition temperature are β-stable elements, which can be divided into two types: the isomorph and the eutectoid. The former has molybdenum, niobium, vanadium, etc.; the latter has chromium, manganese, copper, iron, silicon, etc.
③ Elements that have little effect on phase transition temperature are neutral elements, such as zirconium and tin.
Characteristics of titanium alloy
Titanium is a new type of metal. The performance of titanium is related to the content of impurities such as carbon, nitrogen, hydrogen, and oxygen. The purest titanium iodide contains no more than 0.1% of impurities, but its strength is low and its plasticity is high.
- High strength
The density of titanium alloy is generally about 4.51g/cubic centimeter, which is only 60% of that of steel. The density of pure titanium is close to that of ordinary steel. Some high-strength titanium alloys exceed the strength of many alloy structural steels. Therefore, the specific strength (strength/density) of titanium alloy is much higher than other metal structural materials, and parts with high unit strength, good rigidity and light weight can be produced. Titanium alloys are used in engine components, skeletons, skins, fasteners and landing gears of aircraft.
- High heat intensity
The service temperature is several hundred degrees higher than that of aluminum alloys, and it can still maintain the required strength at moderate temperatures, and can work for a long time at a temperature of 450-500°C. These two types of titanium alloys still have high strength in the range of 150°C-500°C Specific strength, while the specific strength of aluminum alloy decreases significantly at 150 °C. The working temperature of titanium alloy can reach 500°C, while the working temperature of aluminum alloy is below 200°C.
- Good corrosion resistance
Titanium alloy works in humid atmosphere and seawater medium, and its corrosion resistance is far superior to that of stainless steel; it is particularly resistant to pitting corrosion, acid corrosion, and stress corrosion; it is resistant to alkali, chloride, chlorine, organic substances, nitric acid, and sulfuric acid. etc. have excellent corrosion resistance. However, titanium has poor corrosion resistance to reducing oxygen and chromium salt media.
- Good low temperature performance
Titanium alloys can maintain their mechanical properties at low and ultra-low temperatures. Titanium alloys with good low-temperature performance and extremely low interstitial elements, such as TA7, can maintain a certain degree of plasticity at -253°C. Therefore, titanium alloy is also an important low-temperature structure material.
- High chemical activity
Titanium has high chemical activity, and has strong chemical reactions with O, N, titanium alloy products, CO, CO2, water vapor, and ammonia in the atmosphere. When the carbon content is greater than 0.2%, hard TiC will be formed in the titanium alloy; when the temperature is high, it will also form a hard TiN surface layer when it interacts with N; when the temperature is above 600°C, titanium absorbs oxygen to form a hardened layer with high hardness ; When the hydrogen content rises, an embrittlement layer will also be formed. The hard and brittle surface produced by absorbing gas can reach a depth of 0.1-0.15 mm, and the hardening degree is 20%-30%. The chemical affinity of titanium is also large, and it is easy to cause adhesion with the friction surface.
- Small thermal conductivity
The thermal conductivity of titanium λ=15.24W/(m.K) is about 1/4 of that of nickel, 1/5 of that of iron, and 1/14 of that of aluminum, and the thermal conductivity of various titanium alloys is about 50% lower than that of titanium. The elastic modulus of titanium alloy is about 1/2 of that of steel, so its rigidity is poor and easy to deform. It is not suitable for making slender rods and thin-walled parts. times, resulting in severe friction, adhesion, and bond wear on the tool flank.
With the progress of industrialization, the standard of living has improved. More and more consumer product accessories and industrial accessories are made of alloy materials, especially in the die-casting process. The materials commonly used in die casting include the above four alloy materials, aluminum alloy, magnesium alloy, zinc alloy and titanium alloy. According to the use characteristics of various industries, different alloy materials can be selected for the application position.