Aluminum die-castings are components produced using the aluminum material through the die-casting process.The working principle involves heating the aluminum material to transform it into a liquid state. The liquid aluminum material is injected into the mold cavity of a sand or metal mold using an injection method. The mold cavity can be designed in various shapes and sizes. When the liquid aluminum material fills the cavity, it takes on the intended shape, resulting in the production of aluminum die-castings.
Aluminum materials can be classified into pure aluminum and aluminum alloy materials, with different grades based on melting points and hardness. Die-casting is a manufacturing process for components and can be further categorized into high-pressure die-casting, low-pressure die-casting, gravity die-casting, and others. Aluminum die-castings find wide applications in various industries, including automotive, electronics, machinery, furniture, and motors, among others. In the following sections, we will provide a comprehensive introduction to aluminum die-castings.
The development history of aluminum die casting
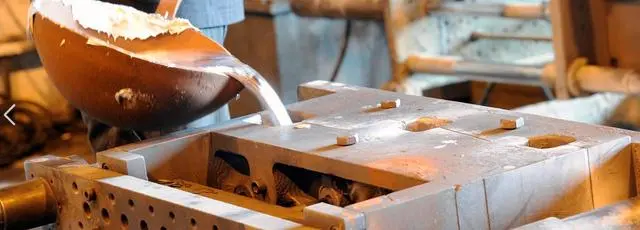
The die-casting process can be traced back to the early 19th century, when lead-tin and aluminum alloy die-castings were first used for printing equipment, packaging, and printing types. It has a history of over 150 years. In the early 20th century, the technology for aluminum alloy die-casting began to emerge. In 1905, die-casting machines suitable for industrial production were introduced, and the die-casting of aluminum alloy components started to gain popularity. However, due to limitations in alloy materials and structural design at the time, aluminum alloy die-casting could only produce a limited number of simple parts.
In 1927, Czech engineer Josef Polak designed a column-type cold chamber aluminum die-casting machine, which marked a significant development in the technology. This innovation brought a high degree of flexibility, cost-effectiveness, and improved product performance to the design and production of aluminum die-castings. In 1952, the first column-type cold chamber aluminum die-casting machine was produced in the former Soviet Union, further popularizing the production of aluminum alloy die-castings.
By 1966, the principles of precision, speed, and density in aluminum die-casting were established, and in 1969, the British introduced the gas porosity-free aluminum die-casting method with oxygen injection. Over the course of 150 years, the field of aluminum die-casting has evolved from its early stages to a mature industry. Both the materials and production techniques have continually improved, and market demand has expanded. Throughout the production process, various optimizations, including refining the composition of aluminum alloys and setting up molds properly, have been implemented to reduce product defects.
With the continuous advancement of various scientific and technological developments, aluminum die-casting plays an increasingly vital role in the design, manufacturing, and assembly of modern manufacturing industries. It enhances manufacturing efficiency while also improving component performance. As market demand continues to grow, aluminum die-casting will be widely utilized and become an indispensable part of modern industrial manufacturing technology.
What is aluminum die casting?
Aluminum die-casting, also known as aluminum pressure die-casting, is one of the production processes for aluminum alloy components. It involves injecting molten aluminum alloy at high pressure into a mold and then solidifying and cooling it to obtain aluminum alloy mold parts. The process of aluminum die-casting can be divided into several steps, including material preparation, mold design, mold manufacturing, melting and casting, vibration-based slag removal, and heat treatment. Aluminum die-casting exhibits the following characteristics:
- High complexity in the shapes of the products, enabling high-precision processing of both internal and external shapes.
- Capable of producing large-sized, high-strength, and lightweight die-cast components.
- Cost-effective, with short production cycles suitable for mass production.
Aluminum die-casting components produced through this process find wide applications in industries such as automotive, aerospace, telecommunications, electronics, machinery, and construction.
Aluminum alloy materials for die castings
Aluminum alloy die-casting materials are primarily divided into three main categories: aluminum-silicon alloys, aluminum-silicon-copper alloys, and aluminum-magnesium alloys. Here are the Chinese names and corresponding English translations for these materials:
Aluminum-Silicon Alloys:
- YL102 (ADC1, A413.0, etc.)
- YL104 (ADC3, A360, etc.)
Aluminum-Silicon-Copper Alloys:
- YL112 (A380, ADC10, etc.)
- YL113 (3830)
- YL117 (B390, ADC14, ADC12, etc.)
Aluminum-Magnesium Alloys:
- 302 (5180, ADC5, ADC6, etc.)
In aluminum-silicon alloys and aluminum-silicon-copper alloys, as the names suggest, the main components, apart from aluminum, are silicon and copper. Silicon content typically ranges between 6-12% and primarily improves the alloy’s fluidity. Copper content is secondary and mainly enhances strength and tensile properties. Iron content typically falls between 0.7-1.2%, providing the best mold release effect within this range. Due to their composition, these alloys are not prone to oxidizing and coloring. Even with desiliconization processes, achieving the desired coloring effect is difficult. On the other hand, aluminum-magnesium alloys can be oxidized and colored, which is a significant distinguishing feature.
When it comes to specific aluminum alloy die-casting materials, some commonly used materials and their applications include:
- 6061 Aluminum Alloy: It offers high strength, corrosion resistance, and good weldability. It is suitable for applications in highly corrosive environments, high-density structural components, toolboxes, accessories, and more.
- 7075 Aluminum Alloy: Known for its high strength, lightweight properties, and ease of machining, it is used in the construction of aircraft structural components, rocket bodies, and suspension system parts.
- 383 Aluminum Alloy: Mainly used for automotive components.
- 413 Aluminum Alloy: It exhibits excellent casting performance and crack suppression characteristics, making it suitable for manufacturing various components, including automotive and aerospace industry parts.
- ADC12 Aluminum Alloy: This alloy offers good casting performance and mechanical properties and is widely used in applications like automotive and motorcycle parts, as well as handles for electronic products.
What is the process of aluminum casting?
The process of aluminum casting involves a series of well-defined steps that are crucial in ensuring the quality of castings and the overall molding effect. Let’s explore these steps in detail:
- Mold Design and Manufacturing: The mold is a critical tool in aluminum casting, and its design and fabrication significantly impact the quality of castings. Mold design involves considering the shape and size requirements of the aluminum parts, selecting appropriate mold materials, and structural design. Common mold manufacturing methods include manual mold making, CNC machining, and 3D printing.
- Melting Aluminum Alloy: To facilitate casting, aluminum alloy or pure aluminum needs to be melted into liquid metal. This is typically achieved using electric or gas furnaces. The aluminum material is heated in the furnace until it transforms into liquid metal. Afterward, tempering operations are carried out to enhance the strength and hardness of the aluminum parts.
- Pouring:The pouring step involves injecting the molten aluminum into the casting mold. Precise control of pouring temperature and speed is crucial to preventing defects such as porosity, inclusions, and cold segregation. Maintaining the purity of the aluminum liquid is also essential to avoid impurity contamination.
- Cooling: Once the aluminum liquid is injected into the casting mold, it rapidly cools and solidifies, taking on the initial shape of the aluminum part. The cooling process requires careful control of cooling rates and temperature distribution to ensure the stability of the internal structure and size of the aluminum parts. Cooling is typically achieved using water or cooling gas.
- Demolding:Cooled aluminum parts must be carefully removed from the casting mold in a process known as demolding. Special tools and equipment such as mold vibration devices and mold unloading machines are often used for this purpose. Demolding aims to preserve the integrity and surface quality of the aluminum parts while avoiding any damage.
- Deburring:After demolding, aluminum parts often exhibit surface burrs or puncture marks. To enhance the surface quality, deburring is necessary. Deburring methods may include mechanical polishing, chemical corrosion, or sandblasting, all of which serve to eliminate surface imperfections.
- Follow-up Treatment:The final step in the aluminum casting process involves follow-up treatments, including heat treatment, surface treatment, machining, and inspection. Heat treatment enhances the organization and performance of aluminum parts, while surface treatment improves corrosion resistance and aesthetics. Machining ensures that aluminum parts meet precise size and shape requirements, and inspection guarantees quality and safety.
The aluminum casting process is intricate and rigorous, with each step demanding careful design and execution. Strict adherence to process requirements in every stage is essential to ensure the quality of aluminum parts and achieve the desired molding effect. Continuous innovation and refinement in aluminum casting processes provide valuable technical support for the advancement of the aluminum manufacturing industry.
Advantages of Aluminum Die Casting
- Mature Technology: Aluminum alloy die-casting technology is well-established, widely applied across various industries, and backed by extensive manufacturing experience, ensuring stable and reliable product quality.
- High Precision and Complexity: Aluminum alloy die-casting enables the rapid production of intricate component designs while maintaining ease of operation and achieving closed-loop process control.
- Excellent Physical Properties: Aluminum alloys offer outstanding physical properties such as ideal strength, corrosion resistance, thermal conductivity, and excellent processability, meeting market demands.
- Good Mechanical Performance: Aluminum die-cast parts exhibit uniform composition, regular grain structure, relatively low density, high strength, good ductility, and excellent tensile and compressive strength.
- High Production Efficiency: Aluminum alloy die-casting technology significantly enhances production efficiency, reduces labor intensity, and enables large-scale production within a short timeframe.
- Thin-Wall Lightweight: Compared to other casting materials, aluminum alloy die-cast parts can have thinner production thickness, lower density, facilitating weight reduction, thin-wall design, and achieving component lightweighting and energy savings.
- Cost-Effective: Aluminum alloy die-casting technology boasts cost advantages over other manufacturing processes, being easy to use and operate, thus maintaining a competitive price advantage.
- Recyclability: Aluminum alloy materials are recyclable, contributing to environmental protection.
- Smooth Surface: Post-casting mechanical or chemical treatments yield high surface smoothness, meeting the surface requirements of self-selling products and complex assembly items.
- Customization: The manufacturing of aluminum alloy die-cast parts can be tailored to customer needs and continually refined to optimize design and production processes to the maximum extent.
- Good Thermal Conductivity: Aluminum alloy die-casting materials exhibit excellent thermal conductivity, allowing for the rapid dissipation of heat generated by electrical components or machinery.
- Precision Machining: Aluminum alloy die-casting technology enables high-precision part processing, significantly improving part accuracy and work efficiency compared to traditional machining processes.
- High Ductility: Aluminum alloy materials possess high strength, good ductility, resistance to deformation, and ease of processing into various shapes, meeting the requirements for manufacturing complex structures.
Surface Treatment Processes for Aluminum Die Casting
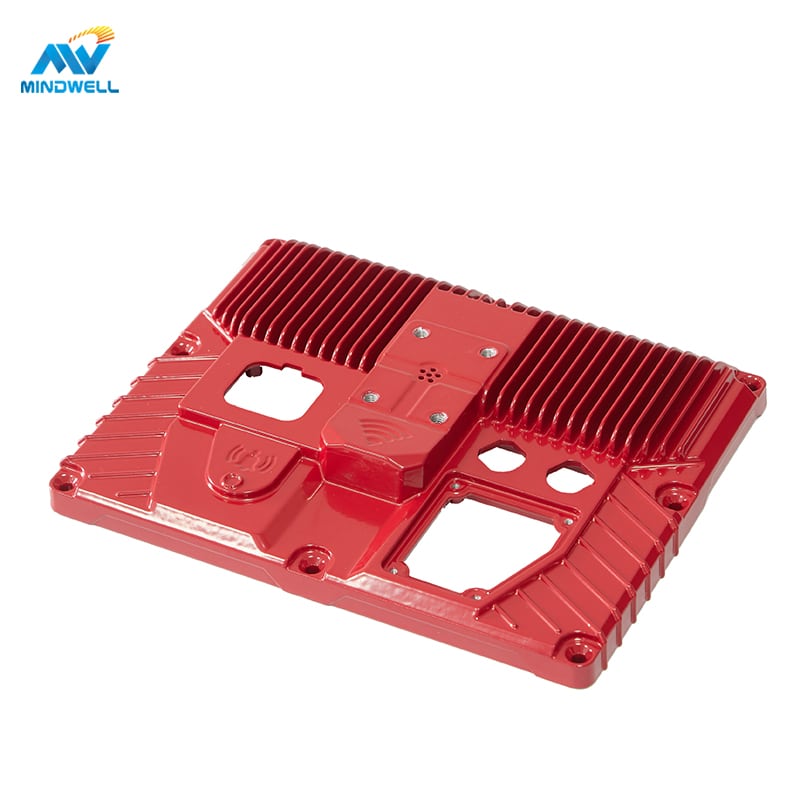
Aluminum die casting is a prevalent manufacturing method employed for crafting diverse aluminum alloy components. Nevertheless, aluminum alloy surfaces often necessitate treatment to enhance their resistance to corrosion, wear and tear, and their visual appeal. This article will outline several customary surface treatment processes for aluminum alloy die casting.
Electroplating Technique
Electroplating is a widely used surface treatment method that enhances the attributes of aluminum alloys by depositing a layer of metal or alloy onto their surfaces. Common electroplating procedures encompass chromium plating, nickel plating, and zinc plating. Chromium plating can augment both the corrosion resistance and the aesthetic appeal of aluminum alloys, while nickel plating enhances their durability, and zinc plating bolsters their corrosion resistance.
Coating Procedure
Coating is a straightforward and effective surface treatment process that enhances the performance of aluminum alloys by applying a coat of paint or lacquer to their surfaces. Coating offers both a pleasing aesthetic effect and protective capabilities. Common coating techniques involve spray coatings, lacquer applications, and powder coatings. Spray coatings enable aluminum alloys to exhibit various colors and textures, lacquer applications enhance their resilience against weathering, and powder coatings increase their hardness and resistance to abrasion.
Oxidation Method
Oxidation is a conventional surface treatment process for aluminum alloys, which enhances their properties by forming a layer of oxide film on the surface. Oxidation elevates corrosion resistance, wear resistance, and insulating characteristics of aluminum alloys. Common oxidation methods include anodizing and chemical oxidation. Anodizing produces a uniform and dense oxide film, whereas chemical oxidation creates an oxide film with distinct colors and textures.
Sandblasting Technique
Sandblasting is a routine surface treatment process that heightens the surface quality of aluminum alloys by propelling high-speed streams of sandblasted particles across the surface. Sandblasting eliminates oxide layers and contaminants, resulting in a smooth and even aluminum alloy surface. It also increases the surface’s roughness, enhancing lubricity and adhesion.
Polishing Process
Polishing is a frequently employed surface treatment technique that enhances the surface’s finish and flatness by mechanically polishing the aluminum alloy’s surface. Polishing imparts a mirror-like effect to the surface, enhancing its aesthetics and optical properties. Common polishing methods include mechanical polishing, electrolytic polishing, and chemical polishing.
To conclude, surface treatment processes for aluminum alloy die casting encompass electroplating, coating, oxidation, sandblasting, and polishing. These procedures serve to improve corrosion resistance, wear resistance, and visual appeal while enhancing the overall quality and service life of aluminum alloys. When applying these methods in practical applications, it is essential to select the appropriate surface treatment process based on specific requirements, and meticulous control of process parameters is essential to ensure the stability and consistency of the treatment outcomes.
Differences Between Aluminum Die Casting, Sand Casting, and Vacuum Die Casting

Aluminum Die Casting
Aluminum die casting involves the use of high-pressure molten metal to cool and solidify within mold cavities, creating the desired aluminum alloy components. This process offers advantages such as high production efficiency and low cost.
The advantages of aluminum die casting include high production efficiency, low cost, and suitability for large-scale production. However, it has disadvantages, including a relatively high scrap rate, potential for post-processing requirements, and the impact of various factors on the quality of die-cast parts.
Aluminum die casting is suitable for large-scale production and scenarios where high production efficiency is required, such as in general machinery, furniture, and the electronic product industries.
Sand Casting
Sand casting, often referred to as the oldest and most versatile casting method, is capable of casting many identical parts simultaneously by sharing a single mold and reusing the same sand mold for small batch production. However, this method typically results in fewer details in the final product or a rough surface, which often necessitates post-machining, polishing, and finishing before use.
Advantages of sand casting:
- Low manufacturing cost: Sand casting generally incurs lower manufacturing costs compared to other casting methods due to lower raw material expenses and a relatively simple manufacturing process.
- High versatility: Sand casting can produce a wide range of complex-shaped castings and create various patterns and inscriptions on casting surfaces.
- High machining accuracy: Sand casting can achieve high precision in casting dimensions and surface roughness.
- Short production cycle: The production cycle for sand casting is shorter compared to other casting methods because of the simplicity of the process and short drying and hardening times.
While sand casting is a common casting method with advantages such as low manufacturing costs, high versatility, high machining accuracy, and short production cycles, its drawbacks, including average surface quality, susceptibility to sand core collapse, and extended release times, need to be considered based on practical circumstances.
Vacuum Die Casting
Vacuum die casting is a process that removes air from the mold cavity during die casting, allowing the molten metal to fill the cavity under a vacuum state, resulting in precision die-cast parts. This method effectively reduces gas entrapment, enhances the density and mechanical properties of die-cast parts.
Advantages of vacuum die casting include improving the density and mechanical properties of die-cast parts, reducing gas entrapment, lowering scrap rates, and enhancing product quality. However, it has drawbacks such as high equipment costs and relatively lower production efficiency.
Vacuum die casting is suitable for applications demanding high density and superior mechanical properties in die-cast parts, such as the automotive, aerospace, and high-end instrument industries.
In practical manufacturing, the choice of an appropriate manufacturing process should align with specific requirements, and careful attention to process parameters is vital to ensure consistent and stable treatment outcomes. As technology advances, these manufacturing processes will continue to evolve and optimize, contributing to advancements in the manufacturing industry, promising higher efficiency and quality across various fields.
Applications of Aluminum Die Casting
- Automotive Industry: Aluminum die casting is extensively used in the automotive industry for manufacturing components such as engine cylinder heads, transmission casings, clutch housings, water pump housings, carburetor housings, and steering gear housings, among others.
- Electronics and Electrical Appliances: In the field of electronics and electrical appliances, aluminum die casting is employed to produce various casings, heat sinks, and other components.
- Mechanical Tools: Aluminum die casting is used in the production of various components for mechanical tools, including handles, casings, brackets, and more.
- Other Fields: Aluminum die casting also finds applications in industries such as aerospace, telecommunications, furniture casting, gardening, lighting fixtures, household appliances, lampshades, kitchenware, furniture accessories, digital casings, craftsmanship, security product casings, LED lighting (lampshades), and some new energy industries, among others.
Conclusion
In the manufacturing industry, aluminum die casting is a versatile process that involves injecting molten aluminum into molds to create components, followed by cooling to produce high-quality parts. This method finds widespread applications in industries such as automotive, electronics, and machinery. The die-casting process encompasses critical steps, including mold design, aluminum melting, casting, cooling, demolding, deburring, and subsequent treatments. Precision and adherence to process requirements are of paramount importance for achieving success.
Advantages of aluminum die casting include well-established technology, high precision, lightweight yet robust components, and cost-effectiveness. Furthermore, surface treatments like electroplating and coating can enhance corrosion resistance and aesthetics. Aluminum die casting is known for its efficiency and cost-effectiveness, making it stand out among casting methods due to its precision, versatility, and product quality. As technology advances, this method continues to drive progress across various industries.